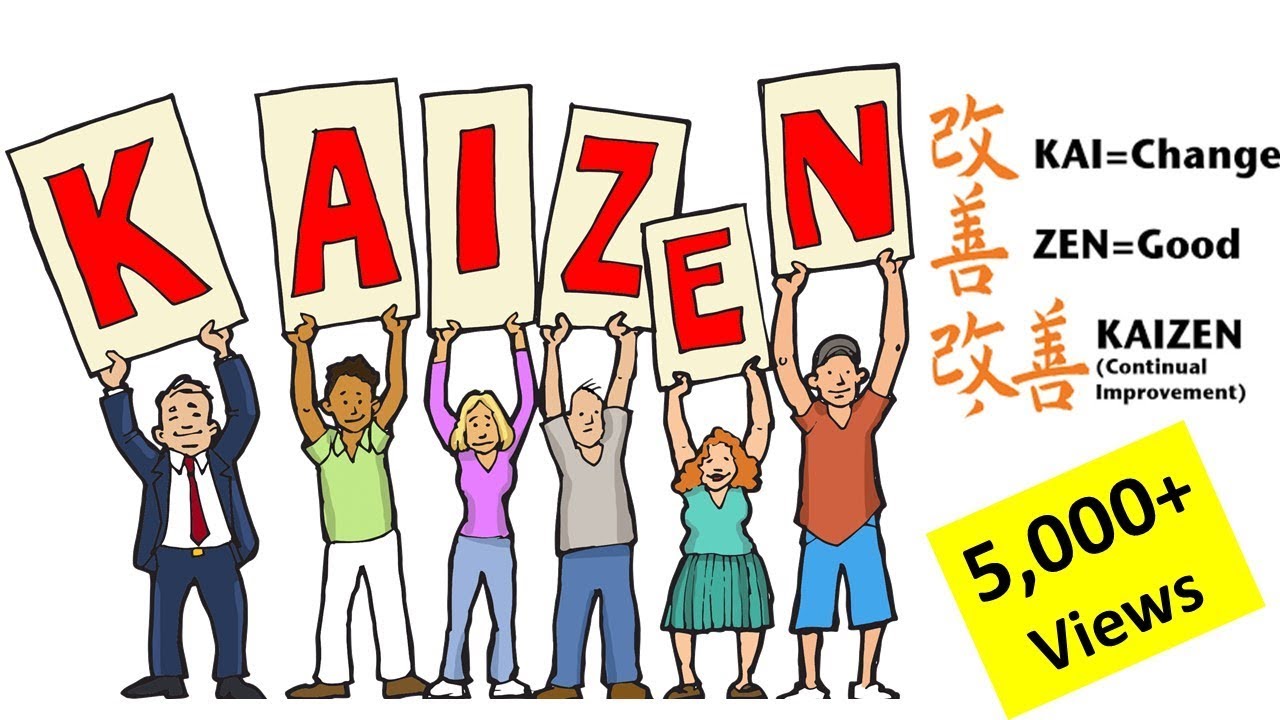
Growing interest in sustainable design has encouraged manufacturing process industries incorporate environmental management system into their processes. These systems usually include formal monitoring of facility waste streams, as well as collaborative problem solving and opportunities for continuous improvement. These systems are based upon the ISO 14001 standard which requires that organizations have an environment management system in order to reduce waste and pollution and improve their environmental performance.
It has been shown that Lean Production practices can improve the environment by reducing waste. All activities that use resources are considered waste. But, waste doesn't create value. Instead, it reduces the amount of materials needed for the production process. It has a negative effect upon the environment. Companies must develop environmental management strategies that align with their goals in order to reduce waste. These strategies can be implemented using lean manufacturing methods. These techniques include 5S - Just in Time, Kaizen Circle, Total Productive maintenance and Continuous improvement.
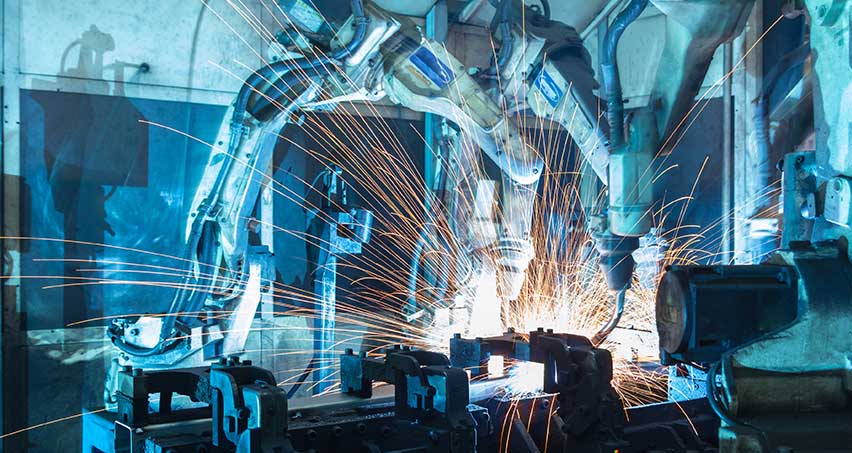
This study examines how Lean Production practices are related to Environmental Management practices. The positive relationship between these concepts was found using multiple case studies. We also identified areas where LM/Green practices can be of benefit. These areas are supply, logistics, production and quality management. We investigated the level of implementation of these practices in companies in the North of Portugal. We also investigated the factors that affect the level of implementation of these practices. Particularly, we looked at whether implementation of lean practices can have a positive influence on the application green practices.
An assessment questionnaire was used in order to determine the level of implementation and effectiveness of LM and Green practices within these companies. It consisted of two parts. The first contained questions about the company. A second part asked about environmental management. SEM was applied to the first part of the questionnaire. The results were good matches with the data sample. The SEM approach revealed that 76% (or 76%) of the variance in environmental practices could be explained by the model.
The results of the test agree with the literature. We should rethink the role of pressure and employee participation in green practices implementation. Passive attitudes can result in poor results. Recognize the importance of practice bundles. Also, we found that green practices and LM have a positive influence on environmental performance.
Employee involvement was also a significant influence on the link between lean management implementation and green practices. This is because LM requires employee participation and engagement in the production process. This leads to greater efficiency. This may impact the relationship between Lean practices and environmental performance. Therefore, it is important to examine the relationship between environmental practices and lean tools.
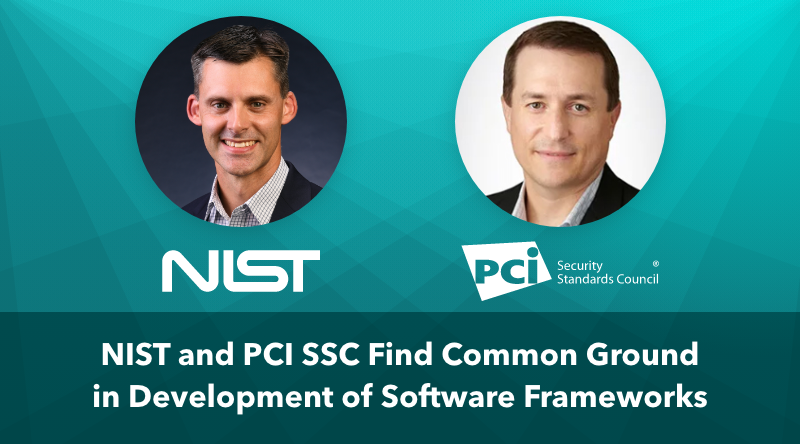
A majority of respondents claimed that Lean Production technologies reduce environmental impact. They also stated that they don't recognize the contributions of Lean Production technologies to their strategic planning.
FAQ
What is the distinction between Production Planning or Scheduling?
Production Planning (PP), is the process of deciding what production needs to take place at any given time. Forecasting demand is one way to do this.
Scheduling involves the assignment of dates and times to tasks in order to complete them within the timeframe.
What are the differences between these four types?
Manufacturing is the process by which raw materials are transformed into useful products through machines and processes. It can involve many activities like designing, manufacturing, testing packaging, shipping, selling and servicing.
How important is automation in manufacturing?
Automating is not just important for manufacturers, but also for service providers. They can provide services more quickly and efficiently thanks to automation. It reduces human errors and improves productivity, which in turn helps them lower their costs.
What are the jobs in logistics?
There are many kinds of jobs available within logistics. These are some of the jobs available in logistics:
-
Warehouse workers – They load and unload pallets and trucks.
-
Transportation drivers: They drive trucks and trailers and deliver goods and make pick-ups.
-
Freight handlers - They sort and pack freight in warehouses.
-
Inventory managers – They manage the inventory in warehouses.
-
Sales reps are people who sell products to customers.
-
Logistics coordinators: They plan and manage logistics operations.
-
Purchasing agents - They purchase goods and services needed for company operations.
-
Customer service representatives - They answer calls and emails from customers.
-
Shipping clerks – They process shipping orders, and issue bills.
-
Order fillers: They fill orders based off what has been ordered and shipped.
-
Quality control inspectors (QCI) - They inspect all incoming and departing products for potential defects.
-
Other - Logistics has many other job opportunities, including transportation supervisors, logistics specialists, and cargo specialists.
What is meant by manufacturing industries?
Manufacturing Industries are businesses that produce products for sale. The people who buy these products are called consumers. These companies use a variety processes such as distribution, retailing and management to accomplish their purpose. They create goods from raw materials, using machines and various other equipment. This includes all types and varieties of manufactured goods, such as food items, clothings, building supplies, furnitures, toys, electronics tools, machinery vehicles, pharmaceuticals medical devices, chemicals, among others.
What are the main products of logistics?
Logistics are the activities involved in moving goods from point A to point B.
They encompass all aspects transport, including packaging and loading, transporting, storage, unloading.
Logisticians ensure that the right product reaches the right place at the right time and under safe conditions. Logisticians help companies improve their supply chain efficiency by providing information about demand forecasts and stock levels, production schedules, as well as availability of raw materials.
They can also track shipments in transit and monitor quality standards.
Statistics
- [54][55] These are the top 50 countries by the total value of manufacturing output in US dollars for its noted year according to World Bank.[56] (en.wikipedia.org)
- Many factories witnessed a 30% increase in output due to the shift to electric motors. (en.wikipedia.org)
- In 2021, an estimated 12.1 million Americans work in the manufacturing sector.6 (investopedia.com)
- You can multiply the result by 100 to get the total percent of monthly overhead. (investopedia.com)
- According to a Statista study, U.S. businesses spent $1.63 trillion on logistics in 2019, moving goods from origin to end user through various supply chain network segments. (netsuite.com)
External Links
How To
Six Sigma and Manufacturing
Six Sigma can be described as "the use of statistical process control (SPC), techniques to achieve continuous improvement." It was developed by Motorola's Quality Improvement Department at their plant in Tokyo, Japan, in 1986. The basic idea behind Six Sigma is to improve quality by improving processes through standardization and eliminating defects. Many companies have adopted this method in recent years. They believe there is no such thing a perfect product or service. Six Sigma aims to reduce variation in the production's mean value. If you take a sample and compare it with the average, you will be able to determine how much of the production process is different from the norm. If the deviation is excessive, it's likely that something needs to be fixed.
Understanding the dynamics of variability within your business is the first step in Six Sigma. Once you understand this, you can then identify the causes of variation. It is important to identify whether the variations are random or systemic. Random variations are caused by human errors. Systematic variations can be caused by outside factors. These are, for instance, random variations that occur when widgets are made and some fall off the production line. However, if you notice that every time you assemble a widget, it always falls apart at exactly the same place, then that would be a systematic problem.
Once you have identified the problem, you can design solutions. It might mean changing the way you do business or redesigning it entirely. Test them again once you've implemented the changes. If they don't work you need to rework them and come up a better plan.