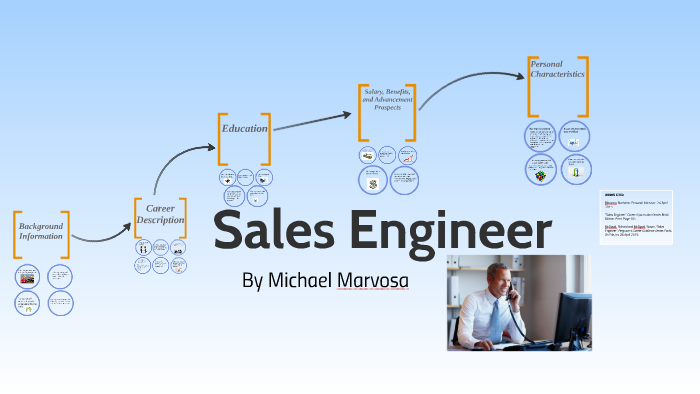
It is essential to get the best price for your investment when choosing a course. This course will educate you about the importance of procurement and the role that procurement management plays in business. These are just a few factors to consider in your decision-making process. Learn more about Cost-based prices, Contracting and Negotiating in order to get the best deal for you business. Here are some of the key points to consider when selecting a course provider:
Cost-based pricing
The Future Procurement course is a Cost-Based Pricing course intended for production and purchasing professionals. It is structured to help both beginners and experienced Procurement Professionals understand and use Cost-Based Pricing in their everyday work. It's available online and can be downloaded free of charge. The course teaches you about CBP and how it works with different types and courses. CBP is an important factor to be aware of when planning your course procurement strategy.

Negotiating
You can learn negotiation skills by taking a course. There are many courses available in negotiation, both online and in-classroom. This course helps you learn the basics of communicating effectively and establishing mutually beneficial relations. This course will help you find a job in negotiation. This course is more detailed than you might think. Below are some tips for getting the most out this course.
Contracting
This workshop is beneficial for students interested in contracting careers. It will provide information about the different activities involved during the sourcing phase. This workshop is useful for all those involved in the procurement cycle, whether you are a newbie or an experienced professional. These are the various purposes of this workshop:
Cooperating with external Partners
In a facilitated classroom setting, this course focuses on six sessions, each using case studies, workbooks, and real-world course procurement experiences. Participants will take part in role-play exercises at the end of each session, which will allow them to gather their learning and assess their comprehension of the training. Participants will gain an awareness of the various sales techniques and behavior. We'll be discussing the benefits and what you can expect in this article.
Certificates
You will learn all about supply chain management and the different processes involved with a Certificate in Course Procurement. In addition, you'll be informed about current trends and other issues. You will be able to improve your negotiation and result skills which will help you stand out from your competitors. A 2.5 grade point average is recommended and the program must be completed within three years. You will learn about the legal and regulatory issues that impact the procurement process.
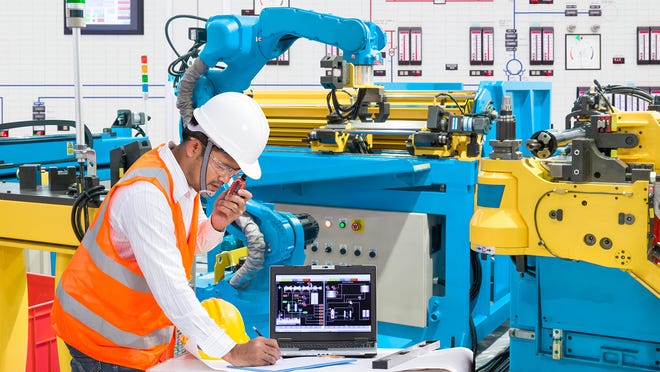
Course platforms
There are many platforms for course purchase. Each has its strengths as well as weaknesses. Some platforms are more premium and offer social learning tools and high levels of interactivity. Some are simpler, with a simpler interface and less features. Teachable was an early online course platform and remains one of its strongest options. However, if you're looking to build a course that can be marketed to the public, you may want to look elsewhere.
FAQ
What is the job of a manufacturer manager?
A manufacturing manager has to ensure that all manufacturing processes work efficiently and effectively. They must also be alert to any potential problems and take appropriate action.
They must also be able to communicate with sales and marketing departments.
They must also keep up-to-date with the latest trends in their field and be able use this information to improve productivity and efficiency.
Why automate your warehouse?
Modern warehouses are increasingly dependent on automation. The rise of e-commerce has led to increased demand for faster delivery times and more efficient processes.
Warehouses must be able to quickly adapt to changing demands. In order to do this, they need to invest in technology. Automation warehouses can bring many benefits. These are just a few reasons to invest in automation.
-
Increases throughput/productivity
-
Reduces errors
-
Improves accuracy
-
Safety is boosted
-
Eliminates bottlenecks
-
Allows companies to scale more easily
-
It makes workers more efficient
-
It gives visibility to everything that happens inside the warehouse
-
Enhances customer experience
-
Improves employee satisfaction
-
Reduces downtime and improves uptime
-
Quality products delivered on time
-
Human error can be eliminated
-
Helps ensure compliance with regulations
What are the products and services of logistics?
Logistics are the activities involved in moving goods from point A to point B.
They include all aspects of transport, including packaging, loading, transporting, unloading, storing, warehousing, inventory management, customer service, distribution, returns, and recycling.
Logisticians make sure that the right product arrives at the right place at the correct time and in safe conditions. They help companies manage their supply chain efficiency by providing information on demand forecasts, stock levels, production schedules, and availability of raw materials.
They monitor shipments in transit, ensure quality standards, manage inventories, replenish orders, coordinate with suppliers and other vendors, and offer support services for sales, marketing, and customer service.
Is it possible to automate certain parts of manufacturing
Yes! Yes! Automation has existed since ancient times. The Egyptians discovered the wheel thousands and years ago. Nowadays, we use robots for assembly lines.
There are many applications for robotics in manufacturing today. These include:
-
Assembly line robots
-
Robot welding
-
Robot painting
-
Robotics inspection
-
Robots that make products
Manufacturing can also be automated in many other ways. For example, 3D printing allows us to make custom products without having to wait for weeks or months to get them manufactured.
What are the four types in manufacturing?
Manufacturing is the process by which raw materials are transformed into useful products through machines and processes. Manufacturing involves many activities, including designing, building, testing and packaging, shipping, selling, service, and so on.
Statistics
- Job #1 is delivering the ordered product according to specifications: color, size, brand, and quantity. (netsuite.com)
- Many factories witnessed a 30% increase in output due to the shift to electric motors. (en.wikipedia.org)
- According to a Statista study, U.S. businesses spent $1.63 trillion on logistics in 2019, moving goods from origin to end user through various supply chain network segments. (netsuite.com)
- In the United States, for example, manufacturing makes up 15% of the economic output. (twi-global.com)
- (2:04) MTO is a production technique wherein products are customized according to customer specifications, and production only starts after an order is received. (oracle.com)
External Links
How To
How to Use Just-In-Time Production
Just-intime (JIT), a method used to lower costs and improve efficiency in business processes, is called just-in-time. It's a way to ensure that you get the right resources at just the right time. This means that only what you use is charged to your account. Frederick Taylor developed the concept while working as foreman in early 1900s. He noticed that workers were often paid overtime when they had to work late. He then concluded that if he could ensure that workers had enough time to do their job before starting to work, this would improve productivity.
JIT is an acronym that means you need to plan ahead so you don’t waste your money. The entire project should be looked at from start to finish. You need to ensure you have enough resources to tackle any issues that might arise. You'll be prepared to handle any potential problems if you know in advance. You won't have to pay more for unnecessary items.
There are different types of JIT methods:
-
Demand-driven JIT: This is a JIT that allows you to regularly order the parts/materials necessary for your project. This will enable you to keep track of how much material is left after you use it. This will let you know how long it will be to produce more.
-
Inventory-based: This allows you to store the materials necessary for your projects in advance. This allows you to predict how much you can expect to sell.
-
Project-driven : This is a method where you make sure that enough money is set aside to pay the project's cost. Knowing how much money you have available will help you purchase the correct amount of materials.
-
Resource-based JIT : This is probably the most popular type of JIT. Here, you allocate certain resources based on demand. You will, for example, assign more staff to deal with large orders. You'll have fewer orders if you have fewer.
-
Cost-based : This is similar in concept to resource-based. But here, you aren't concerned about how many people your company has but how much each individual costs.
-
Price-based: This is a variant of cost-based. However, instead of focusing on the individual workers' costs, this looks at the total price of the company.
-
Material-based is an alternative to cost-based. Instead of looking at the total cost in the company, this method focuses on the average amount of raw materials that you consume.
-
Time-based: This is another variation of resource-based JIT. Instead of focusing only on how much each employee is costing, you should focus on how long it takes to complete your project.
-
Quality-based JIT - This is another form of resource-based JIT. Instead of looking at the labor costs and time it takes to make a product, think about its quality.
-
Value-based: This is one of the newest forms of JIT. In this case, you're not concerned with how well the products perform or whether they meet customer expectations. Instead, you're focused on how much value you add to the market.
-
Stock-based: This inventory-based approach focuses on how many items are being produced at any one time. It's used when you want to maximize production while minimizing inventory.
-
Just-intime planning (JIT), is a combination JIT/sales chain management. It's the process of scheduling delivery of components immediately after they are ordered. It reduces lead times and improves throughput.