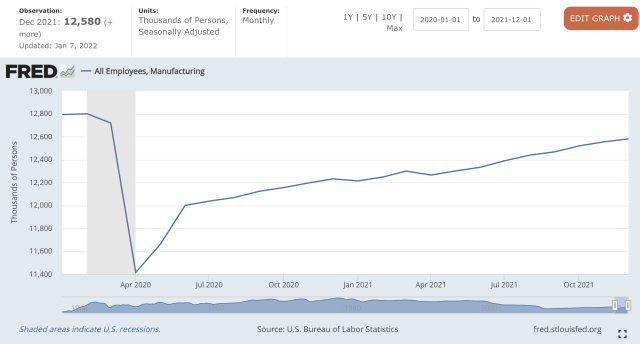
Flow refers to the state where all steps of a production cycle follow each other without interruption. Every step adds value to the product, and goods meander through the production process without being impeded. Production of a specified quantity of stock is planned in many companies to make sure that production orders are met as efficiently as possible. This is Lean Manufacturing's term for "push" production. Here are the essential elements of flow.
Manufacturing just-in-time
The dominant paradigm of "just in time" manufacturing was prevalent when lean manufacturing was introduced to the U.S. late 1970s. This concept is not practical, and it does not have the greatest benefits. It takes many skills and new mindsets to reduce costs and increase efficiency. You will reap the full benefits if it is something you enjoy.
Standardizing processes and working with smaller quantities are two of the most important aspects in just-in-time production. In order to encourage a just in time mindset, it is important to plan your facility layout. Cellular manufacturing, for example, can support production flow. Cellular manufacturing can organize parts bins and workstations in a way that facilitates the flow of materials. And just-in-time manufacturers should avoid long changeover times.
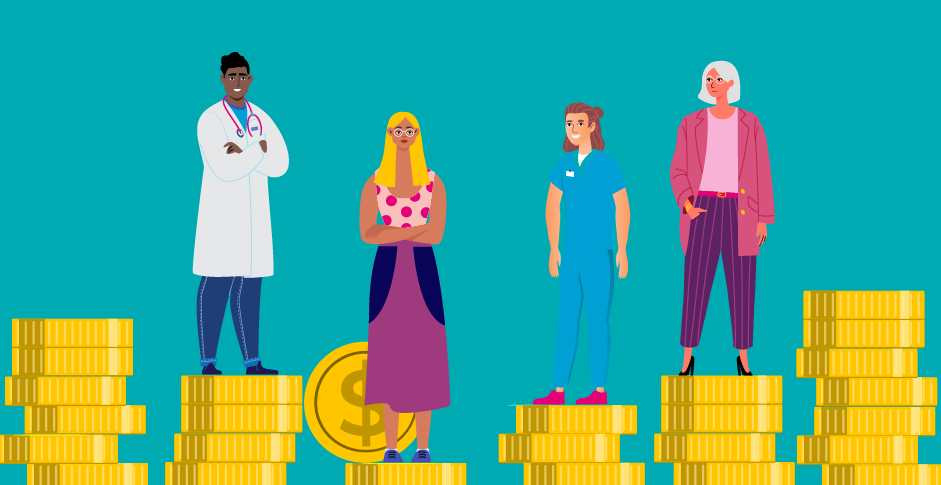
Standardized work
First, you have to create standardized work before applying lean manufacturing in manufacturing processes. This system of work focuses on the workers and what they must do to create a product or service. This refers to the ongoing improvement of the system through kaizen. The cell leader is responsible for standardizing work documents and they are automatically updated as takt times change. Standardized work documentation provides a base for improvement activities, including kaizen and improvement activities.
Having standardized work processes helps an organization improve productivity and service quality. They help to reduce product development and human error. The organization can also fix problems faster because employees are better equipped to understand the process. This allows an organization to continuously improve and increase customer satisfaction. Once standardized, it is not difficult to implement these processes in a company. A mission statement is a great idea.
Continuous improvement
Lean principles encourage continuous improvement and provide a variety of benefits. These benefits are often additive but there is one thread that ties them all together: greater productivity, lower cost, and shorter lead time. Lean continuous improvements are aimed at increasing value creation. But how is continuous improvement possible? This article will give you an overview of some common benefits of continuous improvement. It's simple: it helps companies save money.
A company that is committed to continuous improvement will focus more on incremental changes than on large-scale ones. Individual improvements can seem small or insignificant but the sum of all these improvements is huge. Improvement is a slow process that requires small measured steps, rather than big leaps. Continuous improvement, which focuses on alignment of objectives, is key to lean manufacturing environments. It allows businesses to maximize productivity, profitability, and efficiency. Continuous improvement methods can streamline production and make it easier for all involved to reach a common goal.
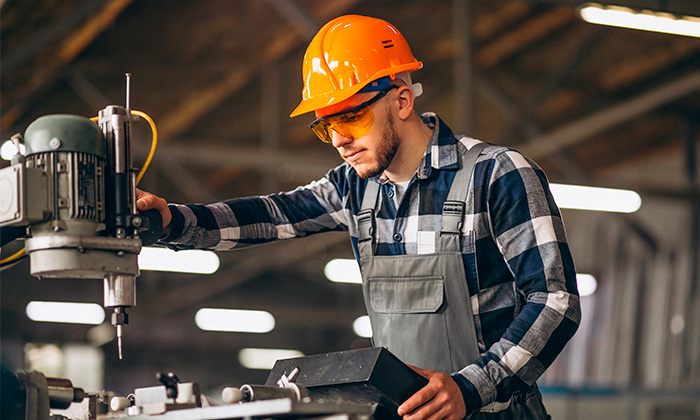
Kaizen
Kaizen, or lean manufacturing, focuses on reducing waste. Sometimes it can improve production yield, decrease lead times, and improve quality. Employees are given specific roles that allow them to investigate the problem and find possible solutions. A kaizen event typically begins with the creation of a value stream map of the process. Next, the team conducts time analyses of all relevant operations. This process is repeated until each step has been improved and the overall process is leaner and more efficient.
A manufacturing plant might purchase a new forklift after identifying inefficiencies. The operator might move inventory around to speed up loading and unloading. The value stream is also a map of the processes that create products or services. Five S's are used in the mapping process to increase employee productivity, workplace practices, and workplace efficiency. There are seven types of muda. Each type focuses upon a different aspect in a manufacturing process.
FAQ
What is the job of a manufacturer manager?
Manufacturing managers must ensure that manufacturing processes are efficient, effective, and cost-effective. They must also be alert to any potential problems and take appropriate action.
They should also be able communicate with other departments, such as sales or marketing.
They should also be knowledgeable about the latest trends in the industry so they can use this information for productivity and efficiency improvements.
What makes a production planner different from a project manger?
The primary difference between a producer planner and a manager of a project is that the manager usually plans and organizes the whole project, while a production planner is only involved in the planning stage.
What does "warehouse" mean?
A warehouse is an area where goods are stored before being sold. It can be an outdoor or indoor area. It could be one or both.
Statistics
- Many factories witnessed a 30% increase in output due to the shift to electric motors. (en.wikipedia.org)
- In 2021, an estimated 12.1 million Americans work in the manufacturing sector.6 (investopedia.com)
- According to the United Nations Industrial Development Organization (UNIDO), China is the top manufacturer worldwide by 2019 output, producing 28.7% of the total global manufacturing output, followed by the United States, Japan, Germany, and India.[52][53] (en.wikipedia.org)
- Job #1 is delivering the ordered product according to specifications: color, size, brand, and quantity. (netsuite.com)
- According to a Statista study, U.S. businesses spent $1.63 trillion on logistics in 2019, moving goods from origin to end user through various supply chain network segments. (netsuite.com)
External Links
How To
Six Sigma and Manufacturing
Six Sigma is defined as "the application of statistical process control (SPC) techniques to achieve continuous improvement." Motorola's Quality Improvement Department in Tokyo, Japan developed Six Sigma in 1986. Six Sigma's core idea is to improve the quality of processes by standardizing and eliminating defects. This method has been adopted by many companies in recent years as they believe there are no perfect products or services. Six Sigma aims to reduce variation in the production's mean value. This means that you can take a sample from your product and then compare its performance to the average to find out how often the process differs from the norm. If there is a significant deviation from the norm, you will know that something needs to change.
The first step toward implementing Six Sigma is understanding how variability works in your business. Once you understand this, you can then identify the causes of variation. You'll also want to determine whether these variations are random or systematic. Random variations happen when people make errors; systematic variations are caused externally. Random variations would include, for example, the failure of some widgets to fall from the assembly line. But if you notice that every widget you make falls apart at the exact same place each time, this would indicate that there is a problem.
Once you've identified the problem areas you need to find solutions. That solution might involve changing the way you do things or redesigning the process altogether. You should then test the changes again after they have been implemented. If they don't work, you will need to go back to the drawing boards and create a new plan.