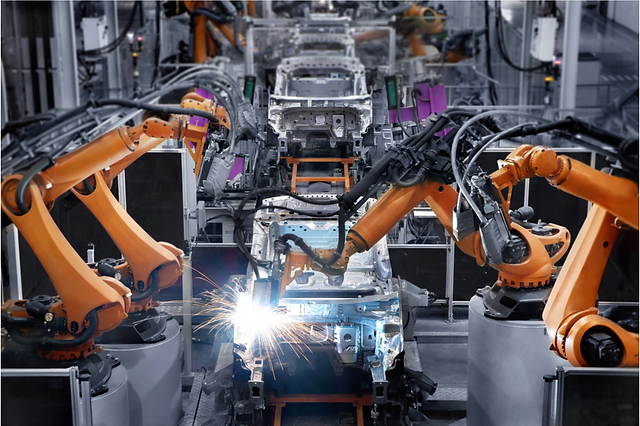
Finding a job in Dallas' logistics industry is possible if you know how to search. You can find employment in a variety of industries such as shipping, trucking, logistics. From entry-level to executive level positions, you can find them all. Get free advice from human resource professionals.
Dallas is home to a growing logistics industry. You can expect a good pay and benefits package from the get go. You may be eligible for perks like gym memberships and free medical insurance, which are some of the best-paid jobs. A courier job is a great option for a new graduate looking for their first job. You may also be interested in a job as a driver. You can expect to work five shifts per semaine.
If you have a driver’s license, good credit scores, and a track record of accomplishments, you will be able to get a logistics job in Dallas. A local community college may offer a driver's education program that is free to you. A military preferred hiring program may be available.
The logistics industry offers many rewarding jobs that require a broad range of skills. You could be a truck driver or a transportation service specialist, as well as a courier or logistics manager. A warehouse manager, supply chain analyst or executive assistant are possible positions. The job holder has a broad range of responsibilities, but the most important task is to coordinate key activities within your organization. You will be able to execute the best strategies possible to ensure smooth goods flow. The logistics industry is a burgeoning sector in the Dallas area, and you can find jobs to suit your talents. There are many positions available at local companies, including those for truck drivers, couriers, and executive assistants. An entry-level job in the trucking industry is a great way get noticed. Apply online if there is a position that interests you. You can search for and apply to jobs in Dallas through a variety of job portals. To see the job openings, you can also look online at free job listings.
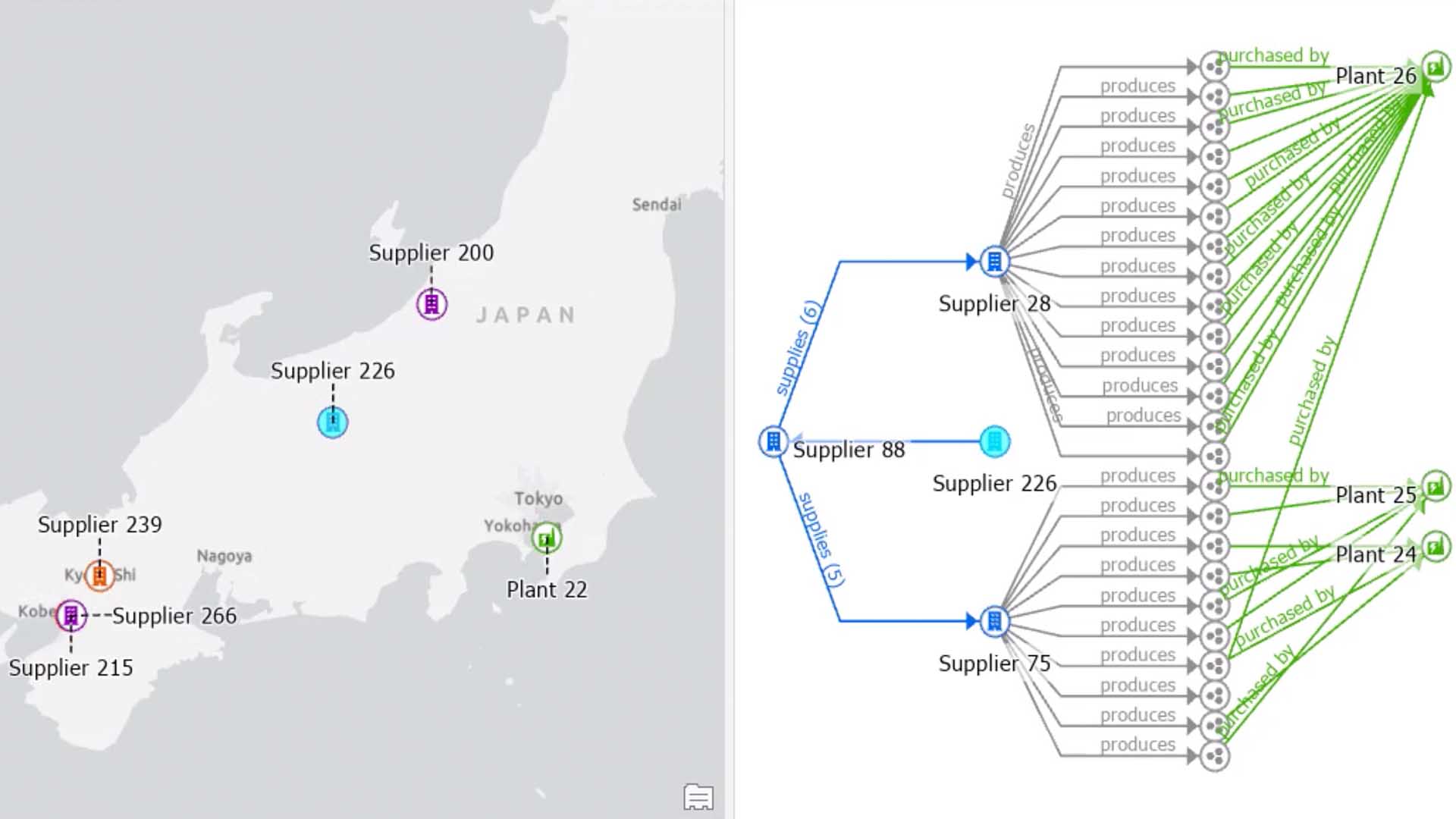
The logistics industry has many exciting possibilities, from truck driver to logistics manager and executive assistant. Browse through several job sites to find the best jobs for Dallas. You may also want to check out CareerOneStop's free online job site to see what companies are looking for in your area. The best part is that you can get free advice from human resources professionals.
FAQ
What is the distinction between Production Planning or Scheduling?
Production Planning (PP), is the process of deciding what production needs to take place at any given time. This can be done by forecasting demand and identifying production capabilities.
Scheduling is the process that assigns dates to tasks so they can get completed within a given timeframe.
What is the importance of logistics in manufacturing?
Logistics are an essential part of any business. They enable you to achieve outstanding results by helping manage product flow from raw materials through to finished goods.
Logistics plays a significant role in reducing cost and increasing efficiency.
What does manufacturing industry mean?
Manufacturing Industries are businesses that produce products for sale. The people who buy these products are called consumers. These companies use a variety processes such as distribution, retailing and management to accomplish their purpose. They make goods from raw materials with machines and other equipment. This covers all types of manufactured goods including clothing, food, building supplies and furniture, as well as electronics, tools, machinery, vehicles and pharmaceuticals.
What does it take for a logistics enterprise to succeed?
To run a successful logistics company, you need a lot knowledge and skills. Effective communication skills are necessary to work with suppliers and clients. You must be able analyze data and draw out conclusions. You need to be able work under pressure and manage stressful situations. You need to be innovative and creative to come up with new ways to increase efficiency. Strong leadership qualities are essential to motivate your team and help them achieve their organizational goals.
It is also important to be efficient and well organized in order meet deadlines.
What are manufacturing & logistics?
Manufacturing is the process of creating goods from raw materials by using machines and processes. Logistics covers all aspects involved in managing supply chains, including procurement and production planning. Manufacturing and logistics can often be grouped together to describe a larger term that covers both the creation of products, and the delivery of them to customers.
Statistics
- In the United States, for example, manufacturing makes up 15% of the economic output. (twi-global.com)
- You can multiply the result by 100 to get the total percent of monthly overhead. (investopedia.com)
- Job #1 is delivering the ordered product according to specifications: color, size, brand, and quantity. (netsuite.com)
- In 2021, an estimated 12.1 million Americans work in the manufacturing sector.6 (investopedia.com)
- [54][55] These are the top 50 countries by the total value of manufacturing output in US dollars for its noted year according to World Bank.[56] (en.wikipedia.org)
External Links
How To
How to Use 5S for Increasing Productivity in Manufacturing
5S stands for "Sort", 'Set In Order", 'Standardize', & Separate>. Toyota Motor Corporation invented the 5S strategy in 1954. It assists companies in improving their work environments and achieving higher efficiency.
This approach aims to standardize production procedures, making them predictable, repeatable, and easily measurable. It means tasks like cleaning, sorting or packing, labeling, and storing are done every day. Through these actions, workers can perform their jobs more efficiently because they know what to expect from them.
Implementing 5S involves five steps: Sort, Set in Order, Standardize Separate, Store, and Each step is a different action that leads to greater efficiency. By sorting, for example, you make it easy to find the items later. You arrange items by placing them in an order. Then, after you separate your inventory into groups, you store those groups in containers that are easy to access. Finally, when you label your containers, you ensure everything is labeled correctly.
This process requires employees to think critically about how they do their job. Employees must understand why they do certain tasks and decide if there's another way to accomplish them without relying on the old ways of doing things. They must learn new skills and techniques in order to implement the 5S system.
In addition to increasing efficiency, the 5S method also improves morale and teamwork among employees. They will feel motivated to strive for higher levels of efficiency once they start to see results.