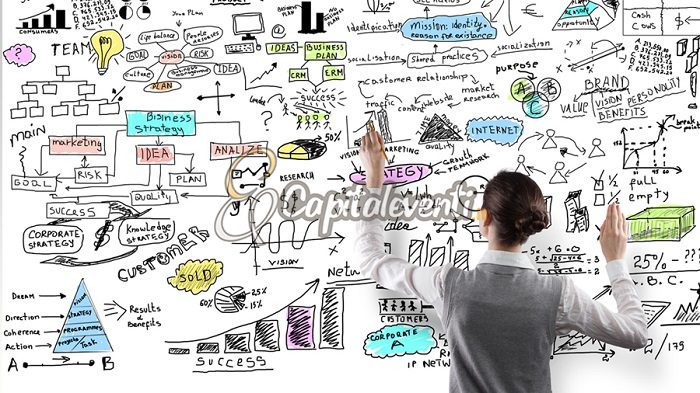
Visual management is the process by which information is conveyed using visual signals. This process helps to increase efficiency and clarity, as information is instantly recognized. There are several kinds of visual control. Here are some examples. Also, you can read more about visual control in Lean manufacturing. Keep reading to find out more. This method can help you get your company on the right path to lean manufacturing.
Lean manufacturing
Andon, which refers to status-display visualization in Japanese, is one of the many methods that can be used for visual management. This helps supervisors and workers to see the status of their work, process flow, and any other relevant information. Visual management allows for easy labeling of workspaces and materials as well as parts, finished goods, or waste. It allows for the identification of inefficiencies and simplifies processes. Below are some of the many benefits of visual control in lean manufacturing.
Lean methodology is incomplete without visible tools that allow for visual management. Clear visual signals help supervisors and operators identify waste, improve process flow, and avoid errors. Additionally, it can reduce safety concerns. Floor markings and other visual indicators can help forklift drivers stay in the right places. Workers can be more productive by using visual management in lean production. Safety risks can be minimized by visual management.
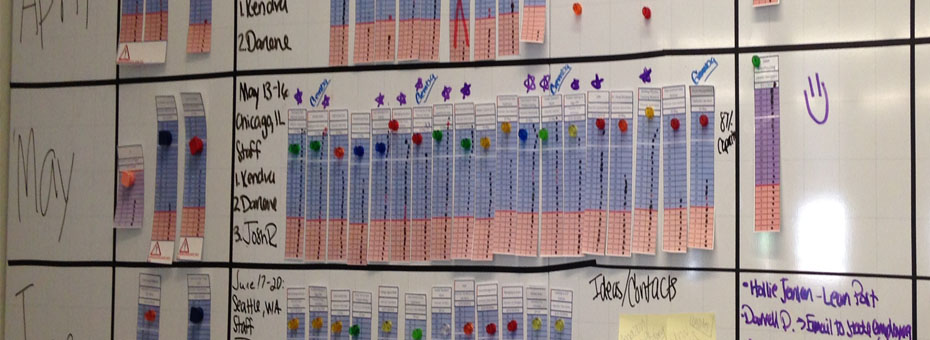
Process control charts
Process control charts can be an effective tool to visualize performance metrics, set a baseline for future improvements, and improve output. They enable operators, management, and other stakeholders communicate clearly by identifying common causes of variability and recommending the correct course of action. These charts are particularly helpful for processes that exhibit unusual patterns or variation. These charts can be useful for visual management as they are easy to create and can be used in order to visualize any system or process.
A control chart's primary purpose is to monitor the process' performance over time. These charts are used to show how many samples were taken and what the results were. This allows managers to assess whether the process is stable. These charts can be used to identify problems and suggest solutions. The control chart's centerline is typically a line segment. It allows the operator to compare the process with its baseline. The control limits usually have three standard deviations from the centerline.
FIFO Lane
FIFO lanes can increase throughput and utilization of a system. Think about an assembly line or fast food counter. It is likely that you have felt the frustration of having to wait in long lines for something. FiFo helps you manage your work flow by setting priority in the queues through visual management. You can define these lanes by placing painted lines on the floor, markings on roller conveyors, and clearly marked shelf spaces. The first job from Process A would move into the first FIFO lane. The next job would then be transferred to the next position.
Time registration is one solution for improving FIFO lane visual management. Employees can track the date and time that carts are placed in a FIFO lane by recording the time and date. Some employees use digital counters to count how many products are in each FIFO lane. Whiteboard stickers can be used to record times on carts. This way, downstream employees can refer to these times to determine which order to take next.
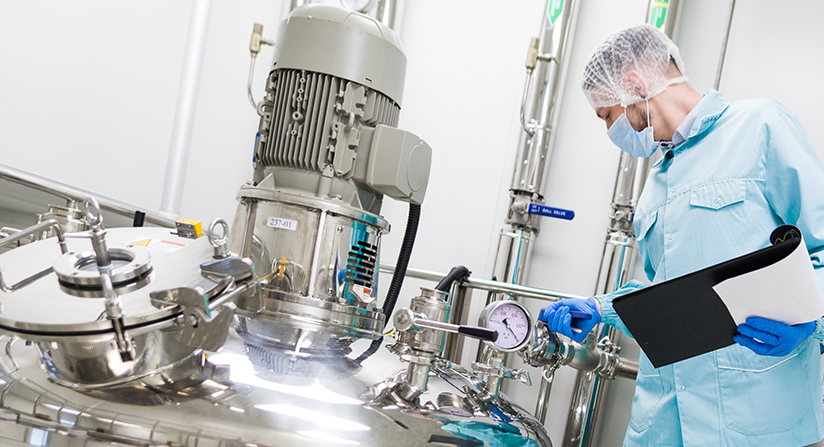
Lean daily management board
A multidisciplinary team created the Lean Daily Management Board based on five predetermined metrics. These were patient outcomes, documentation compliance, employee engagement and productivity. This team met every day to review progress in each area. To check each day's activity, including medication adherence and falls, the team used checklists. To deal with any falls, the team used a problem-solving instrument. The initial data collected in January 2014 noted a medication scan rate of 75% and a fall rate of 1.32/1000 patient days. These data are not applicable to patient care and continuing education.
Instead of simply looking at a company's performance over time, daily managing makes it visible. Managers can then respond to problems as soon as they happen. Poor performers are able to stretch their work in order to not be asked to do more. Poor performers should make stretching work visible so they can account for extra time and effort. Daily management is not meant to be harsh, but it can highlight inefficient or ineffective processes. People issues should be considered for those who are unable to point out a failure in a process.
FAQ
How can we improve manufacturing efficiency?
First, identify the factors that affect production time. We must then find ways that we can improve these factors. You can start by identifying the most important factors that impact production time. Once you've identified them, try to find solutions for each of those factors.
What is the job of a logistics manger?
A logistics manager makes sure that all goods are delivered on-time and in good condition. This is done through his/her expertise and knowledge about the company's product range. He/she should also ensure enough stock is available to meet demand.
What are the responsibilities for a manufacturing manager
A manufacturing manager has to ensure that all manufacturing processes work efficiently and effectively. They should also be aware of any problems within the company and act accordingly.
They should also learn how to communicate effectively with other departments, including sales and marketing.
They must also keep up-to-date with the latest trends in their field and be able use this information to improve productivity and efficiency.
How can overproduction in manufacturing be reduced?
The key to reducing overproduction lies in developing better ways to manage inventory. This would reduce the time needed to manage inventory. This could help us free up our time for other productive tasks.
A Kanban system is one way to achieve this. A Kanban board, a visual display to show the progress of work, is called a Kanban board. Kanban systems are where work items travel through a series of states until reaching their final destination. Each state is assigned a different priority.
When work is completed, it can be transferred to the next stage. However, if a task is still at the beginning stages, it will remain so until it reaches the end of the process.
This allows work to move forward and ensures that no work is missed. A Kanban board allows managers to monitor how much work is being completed at any given moment. This data allows them adjust their workflow based upon real-time data.
Lean manufacturing can also be used to reduce inventory levels. Lean manufacturing emphasizes eliminating waste in all phases of production. Anything that does not contribute to the product's value is considered waste. These are some of the most common types.
-
Overproduction
-
Inventory
-
Packaging not required
-
Materials in excess
Manufacturers can increase efficiency and decrease costs by implementing these ideas.
What are the 4 types manufacturing?
Manufacturing is the process that transforms raw materials into useful products. It can involve many activities like designing, manufacturing, testing packaging, shipping, selling and servicing.
What are the 7 Rs of logistics.
The acronym 7Rs of Logistics refers to the seven core principles of logistics management. It was created by the International Association of Business Logisticians and published in 2004 under its "Seven Principles of Logistics Management".
The acronym is composed of the following letters.
-
Responsible - to ensure that all actions are within the legal requirements and are not detrimental to others.
-
Reliable - have confidence in the ability to deliver on commitments made.
-
It is reasonable to use resources efficiently and not waste them.
-
Realistic - Consider all aspects of operations, including environmental impact and cost effectiveness.
-
Respectful – Treat others fairly and equitably.
-
Reliable - Find ways to save money and increase your productivity.
-
Recognizable - Provide value-added services to customers
Statistics
- Job #1 is delivering the ordered product according to specifications: color, size, brand, and quantity. (netsuite.com)
- According to the United Nations Industrial Development Organization (UNIDO), China is the top manufacturer worldwide by 2019 output, producing 28.7% of the total global manufacturing output, followed by the United States, Japan, Germany, and India.[52][53] (en.wikipedia.org)
- In the United States, for example, manufacturing makes up 15% of the economic output. (twi-global.com)
- [54][55] These are the top 50 countries by the total value of manufacturing output in US dollars for its noted year according to World Bank.[56] (en.wikipedia.org)
- (2:04) MTO is a production technique wherein products are customized according to customer specifications, and production only starts after an order is received. (oracle.com)
External Links
How To
Six Sigma: How to Use it in Manufacturing
Six Sigma refers to "the application and control of statistical processes (SPC) techniques in order to achieve continuous improvement." Motorola's Quality Improvement Department, Tokyo, Japan, developed it in 1986. Six Sigma's basic concept is to improve quality and eliminate defects through standardization. Since there are no perfect products, or services, this approach has been adopted by many companies over the years. Six Sigma seeks to reduce variation between the mean production value. If you take a sample and compare it with the average, you will be able to determine how much of the production process is different from the norm. If the deviation is excessive, it's likely that something needs to be fixed.
Understanding how variability works in your company is the first step to Six Sigma. Once you have a good understanding of the basics, you can identify potential sources of variation. You'll also want to determine whether these variations are random or systematic. Random variations are caused when people make mistakes. While systematic variations are caused outside of the process, they can occur. Random variations would include, for example, the failure of some widgets to fall from the assembly line. It would be considered a systematic problem if every widget that you build falls apart at the same location each time.
Once you identify the problem areas, it is time to create solutions. The solution could involve changing how you do things, or redesigning your entire process. Once you have implemented the changes, it is important to test them again to ensure they work. If they don't work you need to rework them and come up a better plan.