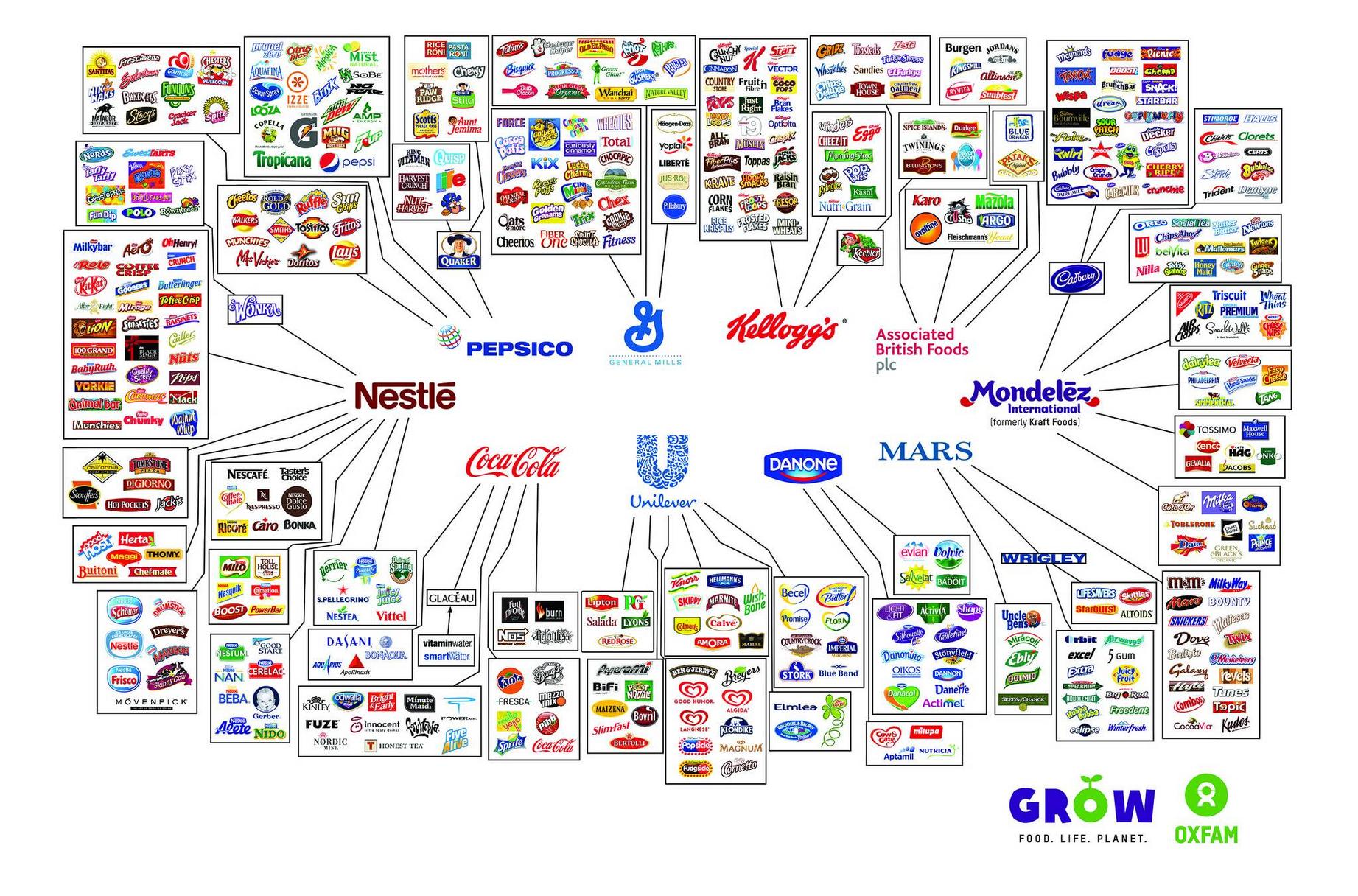
Journal impact factors
Journal impact factors in supply management can be used to evaluate the relative influence and importance of supply chain management journal publications. These factors are calculated using data from ten top academic supply chain management journals as well as the ISI Web of Science Database. These results allow us compare and contrast the relative impact of journals and authors on the field.
Journal impact factors are a key factor in evaluating the quality of a journal. A journal that has a high ranking will likely be high-quality because it attracts high quality research. Journal impact factors consider the number and importance of other journals as well as how many citations a journal gets. Emerald Group Publishing Ltd. is the Journal's publisher. This publishing company is based in the United Kingdom.
Scope of the journal
The scope of journal supply-chain management includes many topics, such as transportation management and logistics. Its purpose is to offer a forum for research-based knowledge in these areas. Articles on these topics are welcomed by the journal. The journal does not require that all submissions be published.

SCMij is an international publication that publishes research to advance the field of supply-chain management. It provides a forum for discussion of empirical and theoretical research. Submissions are welcome from scholars, practitioners, students, and others.
Editorial board
An editorial board is an independent body that assesses the quality and relevance of scientific publications. The Board's members are renowned scientists representing different areas of knowledge. The Board ensures confidentiality of manuscript information and is bound by the editorial code of conduct. The journal can be searched through major search engines. It is also registered in many international scientific databases.
The Journal of Supply Chain Management's Editorial Board is composed of experts in supply chain management, procurement and logistics. Every article submitted for publication goes through peer review to ensure that it's both relevant and useful.
Authors of articles published in the journal
The Journal of Supply Chain Management is open to submissions from professionals in supply chain management, logistics and procurement. The journal publishes original research articles and review articles that relate to supply chain management. The articles should not exceed three thousand words and must discuss new techniques or solutions to problems.
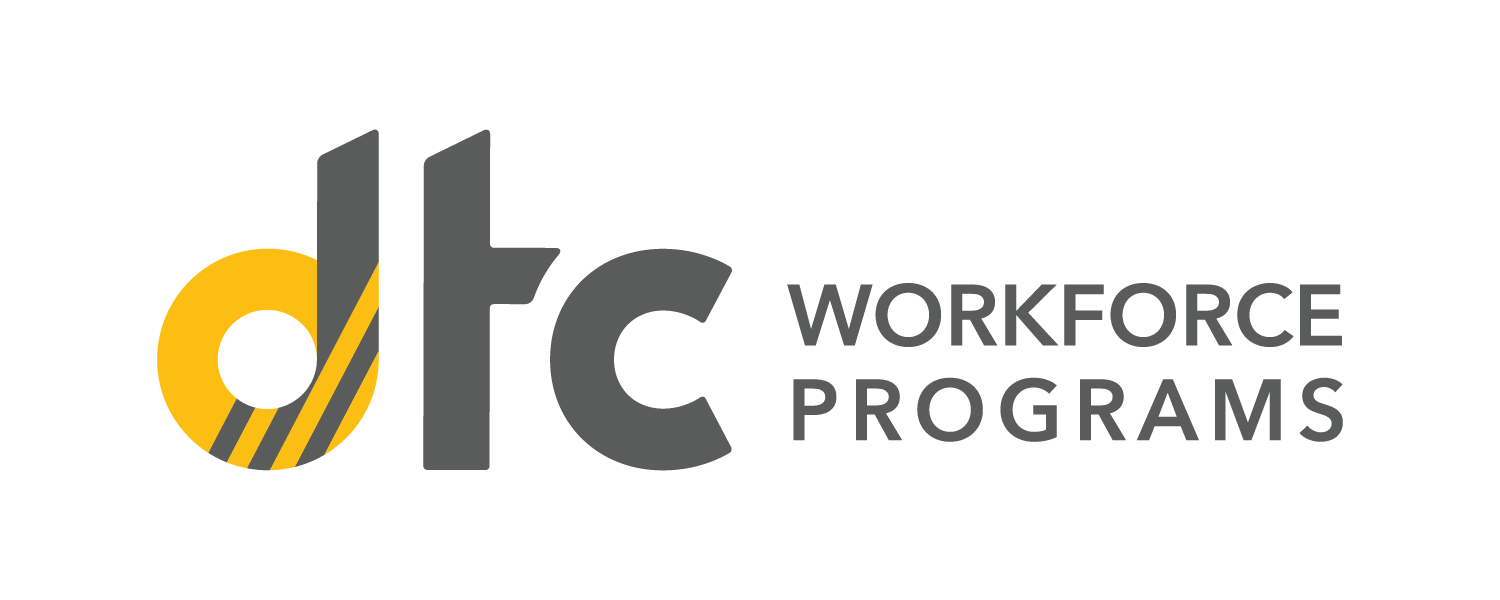
Articles can be submitted online. You can submit them in either text format or separately as files with illustrations. Authors should make sure that their contact details are accurate, and the article should include the most recent address and e-mail. The journal does not charge for publication or submission.
Number of articles published in the journal each year
The Journal of Supply Chain Management publishes articles from several journals. It has a high index (h-index), which means it is highly productive and has high citation impact. The International Standard Serial Number of the journal is 15232409 (total ISSN).
This journal publishes articles written by academics and practitioners in the field. The journal's articles are thought-provoking on supply chain operations. It also publishes features and columns from supply chain practitioners and industry analysts. It also publishes many case reports on companies and supply chains.
FAQ
What are the essential elements of running a logistics firm?
To be a successful businessman in logistics, you will need many skills and knowledge. Effective communication skills are necessary to work with suppliers and clients. You need to understand how to analyze data and draw conclusions from it. You will need to be able handle pressure well and work in stressful situations. To improve efficiency, you must be innovative and creative. You must be a strong leader to motivate others and direct them to achieve organizational goals.
You should also be organized and efficient to meet tight deadlines.
How can manufacturing prevent production bottlenecks?
The key to avoiding bottlenecks in production is to keep all processes running smoothly throughout the entire production cycle, from the time you receive an order until the time when the product ships.
This includes planning for capacity requirements as well as quality control measures.
Continuous improvement techniques like Six Sigma are the best way to achieve this.
Six Sigma is a management system used to improve quality and reduce waste in every aspect of your organization.
It focuses on eliminating variation and creating consistency in your work.
What does it mean to warehouse?
Warehouses and storage facilities are where goods are kept before being sold. It can be indoors or out. It may also be an indoor space or an outdoor area.
What are my options for learning more about manufacturing
Hands-on experience is the best way to learn more about manufacturing. But if that is not possible you can always read books and watch educational videos.
Statistics
- You can multiply the result by 100 to get the total percent of monthly overhead. (investopedia.com)
- According to a Statista study, U.S. businesses spent $1.63 trillion on logistics in 2019, moving goods from origin to end user through various supply chain network segments. (netsuite.com)
- It's estimated that 10.8% of the U.S. GDP in 2020 was contributed to manufacturing. (investopedia.com)
- Many factories witnessed a 30% increase in output due to the shift to electric motors. (en.wikipedia.org)
- Job #1 is delivering the ordered product according to specifications: color, size, brand, and quantity. (netsuite.com)
External Links
How To
Six Sigma: How to Use it in Manufacturing
Six Sigma is defined by "the application SPC (statistical process control) techniques to achieve continuous improvements." Motorola's Quality Improvement Department, Tokyo, Japan, developed it in 1986. The basic idea behind Six Sigma is to improve quality by improving processes through standardization and eliminating defects. This method has been adopted by many companies in recent years as they believe there are no perfect products or services. The main goal of Six Sigma is to reduce variation from the mean value of production. If you take a sample and compare it with the average, you will be able to determine how much of the production process is different from the norm. If this deviation is too big, you know something needs fixing.
Understanding how variability works in your company is the first step to Six Sigma. Once you've understood that, you'll want to identify sources of variation. This will allow you to decide if these variations are random and systematic. Random variations are caused by human errors. Systematic variations can be caused by outside factors. If you make widgets and some of them end up on the assembly line, then those are considered random variations. If however, you notice that each time you assemble a widget it falls apart in exactly the same spot, that is a problem.
Once you've identified where the problems lie, you'll want to design solutions to eliminate those problems. It might mean changing the way you do business or redesigning it entirely. After implementing the new changes, you should test them again to see if they worked. If they didn't work, then you'll need to go back to the drawing board and come up with another plan.