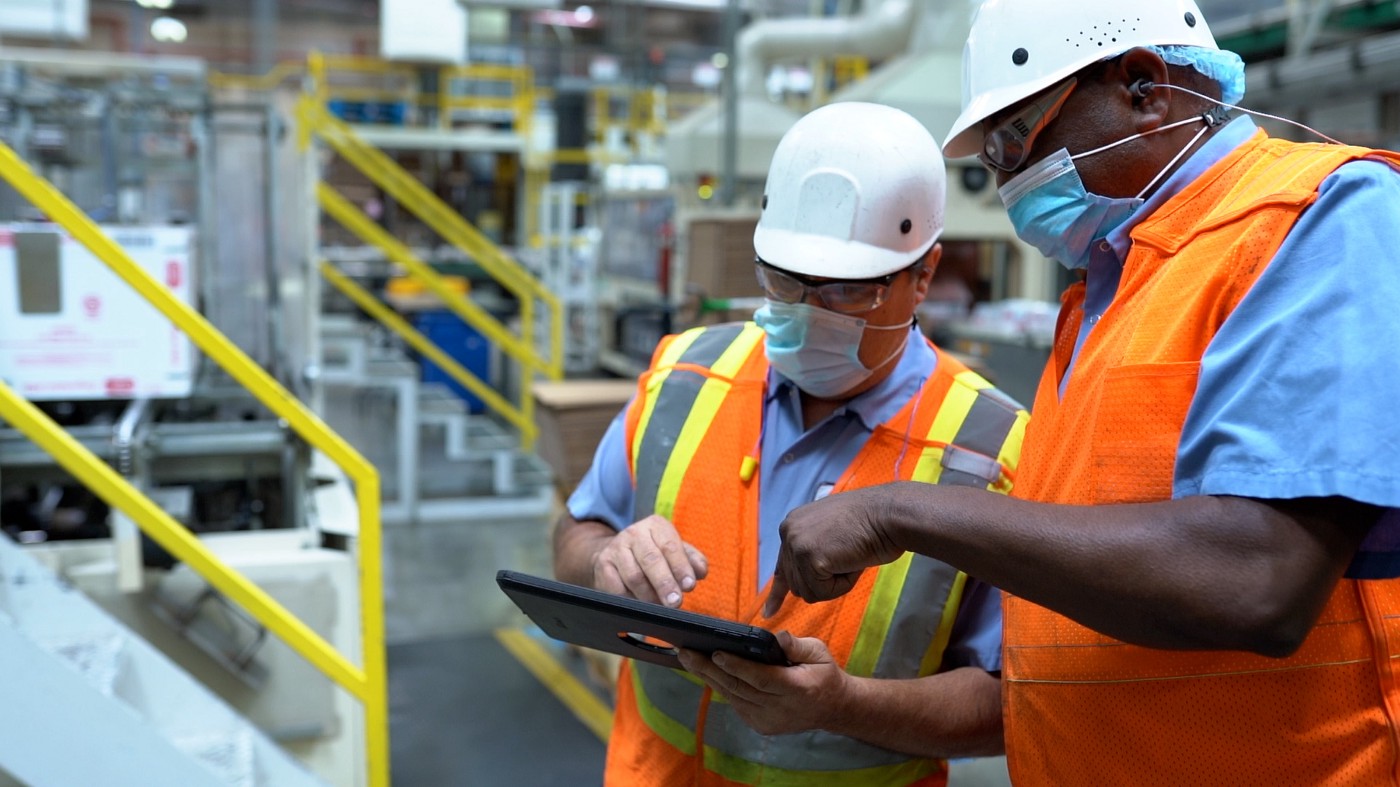
Train engineers can look forward to many perks, in addition to a decent salary. In fact, the average train engineer salary is more than what many people make in their entire lifetime. It is expected that the demand for railroad transportation jobs will rise by approximately one percent. Train engineer salaries vary depending on the location and experience. Train engineers who have worked in the industry for many years can make well over $100,000 annually.
Train engineers have a difficult job. First, you have to complete federal licensing. After you get your license, you'll need to get some experience before you can go on to work on your own. For your certification, you will need to pass a test. This typically includes a vision test and an eye test. If you pass the exam, you will be eligible for employment with federal railroads or other transportation agencies.
Working as a train engineer can mean long hours away. Many train engineers work weekends and nights. There may be times when your schedule is irregular. For example, working in the morning or on holidays. You may also be exposed for different weather types. Some cases may require you to drive electric trains. This can be challenging.
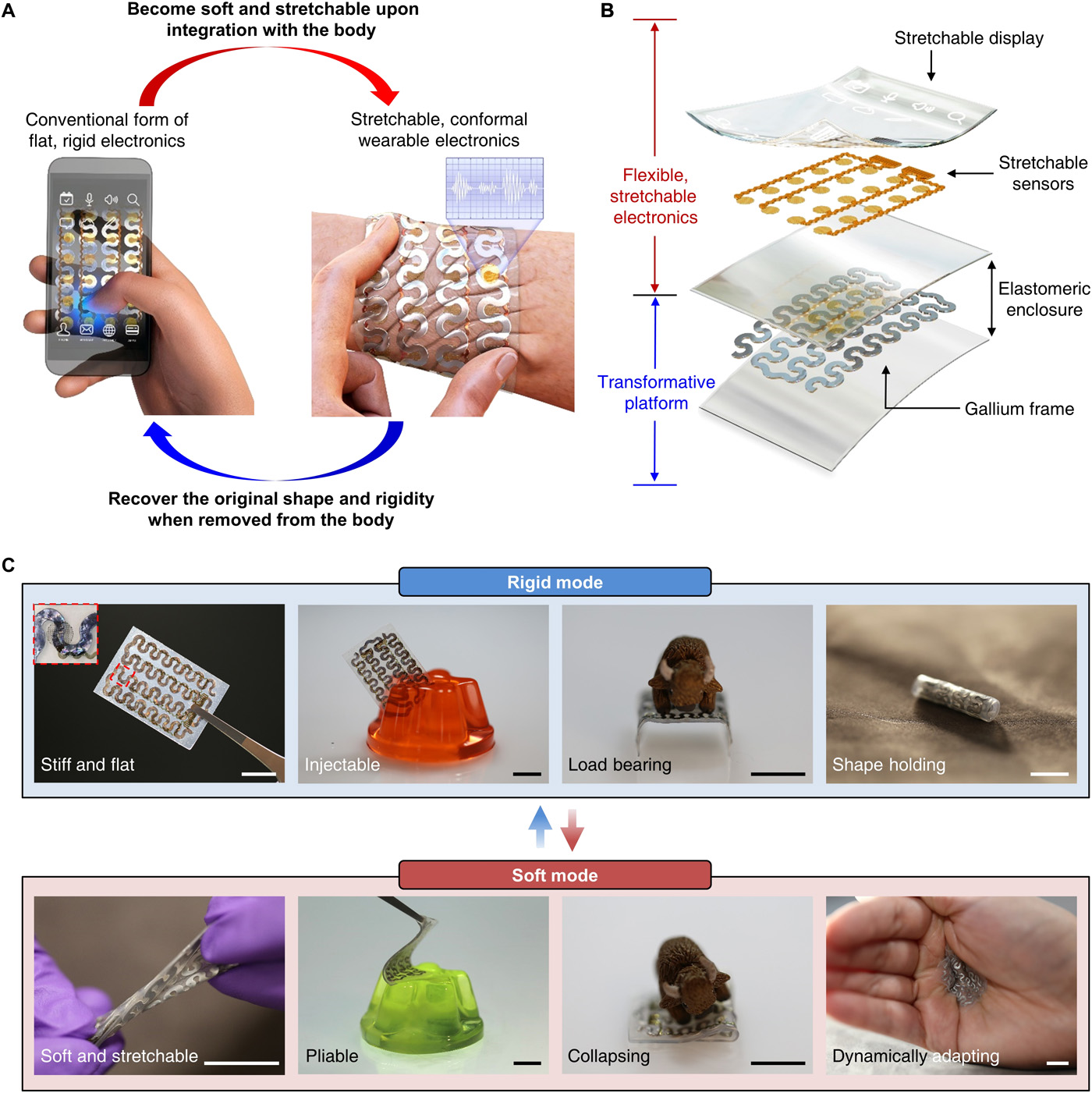
You'll also need to pass a test that tests your mechanical aptitude. You will need to be able see clearly and have good hand-eye coordination. Sometimes you may have to drive freight trains.
Depending on where you are located, you may be required to work in the dark or be available for 24 hours per day. However, as long your job is not too difficult it can be a lucrative way to make a living. The large railroad companies offer the highest pay for train engineers. They have their own training programs, but if you want to work for a smaller railroad, you can get certified through a trade school.
Additionally, you'll need to have a solid high school diploma as well as a clean criminal record. Although it's not required, having a degree in train engineering can help you get noticed by employers. You can also earn certification through a community college or trade school that will enable you to get a job as train engineer.
The average monthly salary of a train engineer is approximately $5,254 However, the salary can vary depending on your location, your experience, and your employer. The average salary for train engineers is $75,000 per annum. The highest earners can make $186,000 annually. If you're willing to search, you might be able to earn a higher average salary. It's also a good idea to look out for job opportunities.
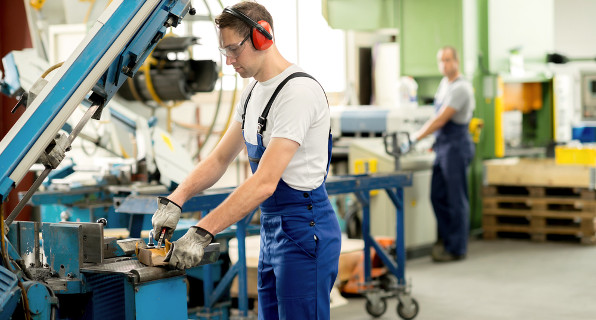
An advanced degree might also be beneficial for your pay. Some locomotive engineers even go on to become train trainers or railroad schedulers. Many train engineers also find that they enjoy their jobs and will keep doing it for a long period of time.
FAQ
What type of jobs is there in logistics
There are many kinds of jobs available within logistics. These are some of the jobs available in logistics:
-
Warehouse workers - They load and unload trucks and pallets.
-
Transport drivers - These are people who drive trucks and trailers to transport goods or perform pick-ups.
-
Freight handlers, - They sort out and pack freight in warehouses.
-
Inventory managers - These are responsible for overseeing the stock of goods in warehouses.
-
Sales representatives - They sell products.
-
Logistics coordinators are responsible for organizing and planning logistics operations.
-
Purchasing agents – They buy goods or services necessary to run a company.
-
Customer service representatives - They answer calls and emails from customers.
-
Shipping clerks – They process shipping orders, and issue bills.
-
Order fillers – They fill orders based upon what was ordered and shipped.
-
Quality control inspectors: They inspect outgoing and incoming products for any defects.
-
Others - There are many other types of jobs available in logistics, such as transportation supervisors, cargo specialists, etc.
What are manufacturing and logistics?
Manufacturing is the production of goods using raw materials. Logistics encompasses the management of all aspects associated with supply chain activities such as procurement, production planning, distribution and inventory control. It also includes customer service. Manufacturing and logistics can often be grouped together to describe a larger term that covers both the creation of products, and the delivery of them to customers.
What are the four types in manufacturing?
Manufacturing is the process by which raw materials are transformed into useful products through machines and processes. It can involve many activities like designing, manufacturing, testing packaging, shipping, selling and servicing.
How can excess manufacturing production be reduced?
It is essential to find better ways to manage inventory to reduce overproduction. This would reduce the amount of time spent on unnecessary activities such as purchasing, storing, and maintaining excess stock. This could help us free up our time for other productive tasks.
A Kanban system is one way to achieve this. A Kanban board, a visual display to show the progress of work, is called a Kanban board. A Kanban system allows work items to move through several states before reaching their final destination. Each state represents a different priority.
As an example, if work is progressing from one stage of the process to another, then the current task is complete and can be transferred to the next. However, if a task is still at the beginning stages, it will remain so until it reaches the end of the process.
This helps to keep work moving forward while ensuring that no work is left behind. Managers can see how much work has been done and the status of each task at any time with a Kanban Board. This allows them to adjust their workflows based on real-time information.
Another way to control inventory levels is to implement lean manufacturing. Lean manufacturing works to eliminate waste throughout every stage of the production chain. Any product that isn't adding value can be considered waste. The following are examples of common waste types:
-
Overproduction
-
Inventory
-
Packaging that is not necessary
-
Excess materials
These ideas can help manufacturers improve efficiency and reduce costs.
What are the 7 Rs of logistics?
The acronym "7R's" of Logistics stands for seven principles that underpin logistics management. It was developed and published by the International Association of Business Logisticians in 2004 as part of the "Seven Principles of Logistics Management".
The following letters make up the acronym:
-
Responsible – ensure that all actions are legal and don't cause harm to anyone else.
-
Reliable - Have confidence in your ability to fulfill all of your commitments.
-
Be responsible - Use resources efficiently and avoid wasting them.
-
Realistic – consider all aspects of operations, from cost-effectiveness to environmental impact.
-
Respectful - treat people fairly and equitably.
-
Reliable - Find ways to save money and increase your productivity.
-
Recognizable provides value-added products and services to customers
Statistics
- Many factories witnessed a 30% increase in output due to the shift to electric motors. (en.wikipedia.org)
- In 2021, an estimated 12.1 million Americans work in the manufacturing sector.6 (investopedia.com)
- According to the United Nations Industrial Development Organization (UNIDO), China is the top manufacturer worldwide by 2019 output, producing 28.7% of the total global manufacturing output, followed by the United States, Japan, Germany, and India.[52][53] (en.wikipedia.org)
- (2:04) MTO is a production technique wherein products are customized according to customer specifications, and production only starts after an order is received. (oracle.com)
- You can multiply the result by 100 to get the total percent of monthly overhead. (investopedia.com)
External Links
How To
How to Use Six Sigma in Manufacturing
Six Sigma is defined by "the application SPC (statistical process control) techniques to achieve continuous improvements." Motorola's Quality Improvement Department developed it at their Tokyo plant in Japan in 1986. Six Sigma's main goal is to improve process quality by standardizing processes and eliminating defects. Many companies have adopted Six Sigma in recent years because they believe that there are no perfect products and services. Six Sigma's primary goal is to reduce variation from the average value of production. If you take a sample and compare it with the average, you will be able to determine how much of the production process is different from the norm. If this deviation is too big, you know something needs fixing.
Understanding the dynamics of variability within your business is the first step in Six Sigma. Once you've understood that, you'll want to identify sources of variation. Also, you will need to identify the sources of variation. Random variations are caused when people make mistakes. While systematic variations are caused outside of the process, they can occur. You could consider random variations if some widgets fall off the assembly lines. However, if you notice that every time you assemble a widget, it always falls apart at exactly the same place, then that would be a systematic problem.
Once you've identified where the problems lie, you'll want to design solutions to eliminate those problems. This could mean changing your approach or redesigning the entire process. After implementing the new changes, you should test them again to see if they worked. If they don't work you need to rework them and come up a better plan.