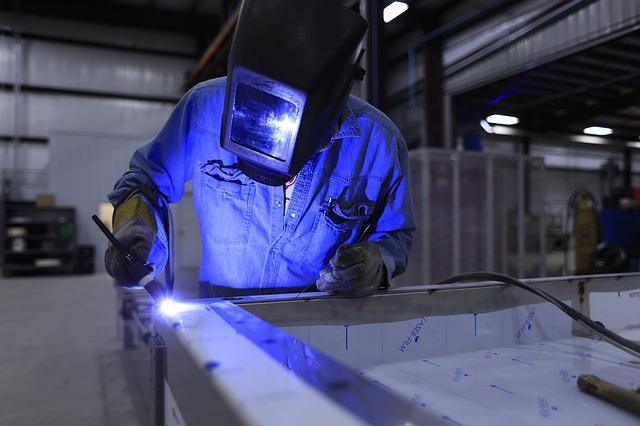
During his tenure as CEO of Wiremold, Art Byrne introduced a series of innovations that helped the company achieve its goal of reducing costs while increasing productivity. Byrne's lean manufacturing case study demonstrated his keen understanding of how to involve the whole team. While implementing the improvements, Byrne encouraged his team to learn by doing and enlisted everyone in the kaizen process.
He established a lean program to track the flow of parts throughout the manufacturing process. He also introduced a variety of tools to reduce waste and increase productivity. He created a laser cutter machine that could produce small batches, which helped to save money on tooling. His success was due a lean strategy, which included just a few simple steps.
He also implemented a JIT manufacturing method. This method of manufacturing allowed the company to deliver finished vehicles at a fast pace. Harmony was also possible during the manufacturing process. This was key to reducing the amount of waste.
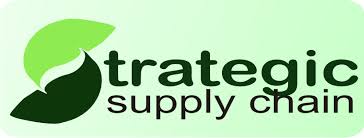
He was a problem-solver during the recession and created a tool maintenance strategy which helped the company save $2,000,000 He implemented an early retirement strategy for unionized workers. These moves enabled him to transform Wiremold, which was a chaotic and inefficient business, into a Lean company.
He created a system that monitors the flow and quality of raw materials in the manufacturing process. He also implemented an ERP system. He also made sure his team understood the value of respect for employees. His lean methods were simple and efficient, which allowed him to make sure everyone understood the concept kaizen. His management style promoted respect for people and an active approach.
His knowledge of the kaizen process was his greatest asset. Danaher Corporation had been his employer for a while, and he was familiar with the three Ps of a good kaizen: process, product, and people. He also made small layoffs for salaried employees. His kaizen strategy was a way for him to ensure that his team did the right thing.
He also introduced value streaming mapping. This diagram shows the effect of manufacturing resources on overall efficiency. He also introduced the concept of a Kaizen event worksheet, which can be used to track key improvement activities. A chart that shows overall achievements displays the results.
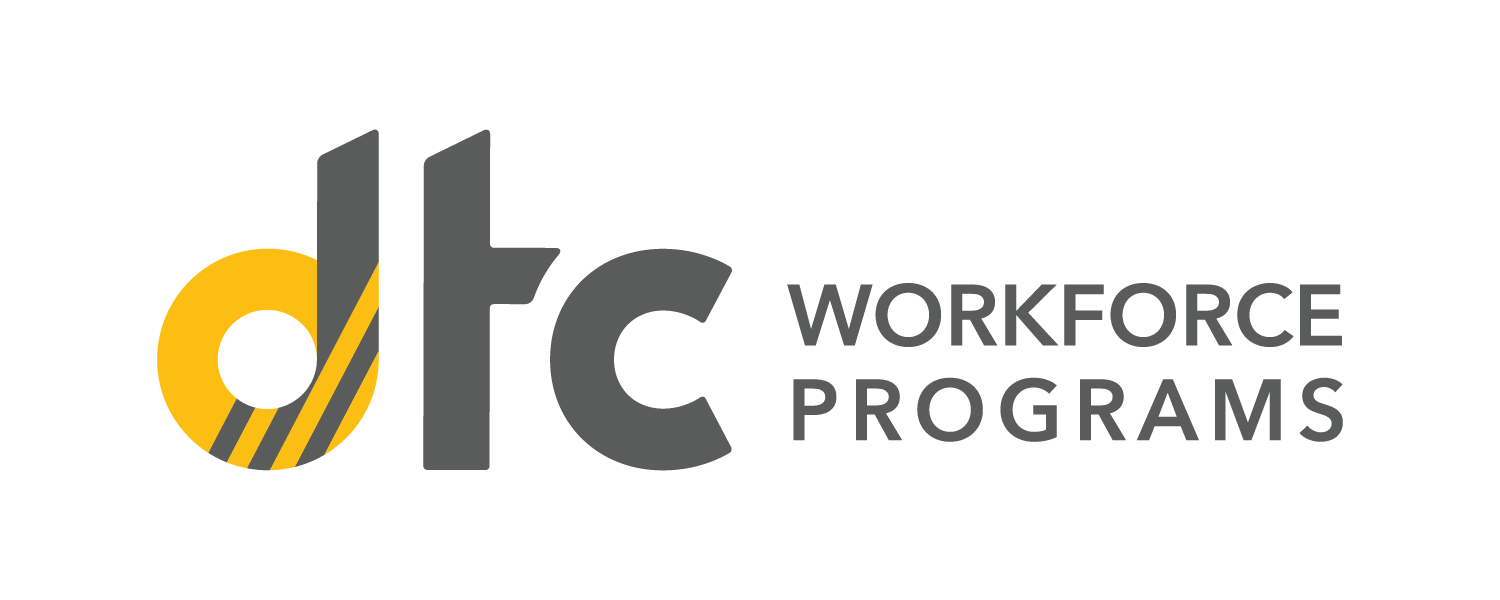
He also developed a system that reduces lead time. This is important in the manufacturing industry. The fine blanking machine produced 600 to 800-blades per hour. It eliminated the need of a lot manual labor. The kanban card is another tool that was used for reducing lead time.
Wiremold was a leader in conduit casing manufacturing. In just ten year, sales rose from 100 million dollars up to 450 millions. French competitor Legrand bought the company in 2001. Wiremold didn't always succeed in its journey. Its greatest problem was queue processing. This meant that designated stations had to do too much or too few work.
FAQ
What are the responsibilities for a manufacturing manager
A manufacturing manager has to ensure that all manufacturing processes work efficiently and effectively. They should be alert for any potential problems in the company and react accordingly.
They should also know how to communicate with other departments such as sales and marketing.
They should also be aware of the latest trends in their industry and be able to use this information to help improve productivity and efficiency.
What is the responsibility for a logistics manager
A logistics manager ensures that all goods are delivered on time and without damage. This is done using his/her knowledge of the company's products. He/she should make sure that enough stock is on hand to meet the demands.
What is the difference between a production planner and a project manager?
The main difference between a production planner and a project manager is that a project manager is usually the person who plans and organizes the entire project, whereas a production planner is mainly involved in the planning stage of the project.
What type of jobs is there in logistics
There are many types of jobs in logistics. Here are some:
-
Warehouse workers – They load, unload and transport pallets and trucks.
-
Transportation drivers: They drive trucks and trailers and deliver goods and make pick-ups.
-
Freight handlers - They sort and pack freight in warehouses.
-
Inventory managers - These are responsible for overseeing the stock of goods in warehouses.
-
Sales reps are people who sell products to customers.
-
Logistics coordinators – They plan and coordinate logistics operations.
-
Purchasing agents: They are responsible for purchasing goods and services to support company operations.
-
Customer service representatives – They answer emails and phone calls from customers.
-
Ship clerks - They issue bills and process shipping orders.
-
Order fillers - These people fill orders based on what has been ordered.
-
Quality control inspectors (QCI) - They inspect all incoming and departing products for potential defects.
-
Others - There are many types of jobs in logistics such as transport supervisors and cargo specialists.
What does manufacturing industry mean?
Manufacturing Industries are businesses that produce products for sale. These products are sold to consumers. These companies use a variety processes such as distribution, retailing and management to accomplish their purpose. They produce goods from raw materials by using machines and other machinery. This covers all types of manufactured goods including clothing, food, building supplies and furniture, as well as electronics, tools, machinery, vehicles and pharmaceuticals.
What is it like to manage a logistics company?
A successful logistics business requires a lot more than just knowledge. Effective communication skills are necessary to work with suppliers and clients. You must be able analyze data and draw out conclusions. You must be able manage stress and pressure under pressure. To increase efficiency and creativity, you need to be creative. To motivate and guide your team towards reaching organizational goals, you must have strong leadership skills.
To meet tight deadlines, you must also be efficient and organized.
Statistics
- Job #1 is delivering the ordered product according to specifications: color, size, brand, and quantity. (netsuite.com)
- [54][55] These are the top 50 countries by the total value of manufacturing output in US dollars for its noted year according to World Bank.[56] (en.wikipedia.org)
- It's estimated that 10.8% of the U.S. GDP in 2020 was contributed to manufacturing. (investopedia.com)
- In 2021, an estimated 12.1 million Americans work in the manufacturing sector.6 (investopedia.com)
- Many factories witnessed a 30% increase in output due to the shift to electric motors. (en.wikipedia.org)
External Links
How To
How to Use Just-In-Time Production
Just-in-time is a way to cut costs and increase efficiency in business processes. It's the process of obtaining the right amount and timing of resources when you need them. This means that you only pay the amount you actually use. Frederick Taylor was the first to coin this term. He developed it while working as a foreman during the early 1900s. He observed how workers were paid overtime if there were delays in their work. He then concluded that if he could ensure that workers had enough time to do their job before starting to work, this would improve productivity.
JIT teaches you to plan ahead and prepare everything so you don’t waste time. Also, you should look at the whole project from start-to-finish and make sure you have the resources necessary to address any issues. You can anticipate problems and have enough equipment and people available to fix them. This will prevent you from spending extra money on unnecessary things.
There are many JIT methods.
-
Demand-driven: This type of JIT allows you to order the parts/materials required for your project on a regular basis. This will allow to track how much material has been used up. This will let you know how long it will be to produce more.
-
Inventory-based: This is a type where you stock the materials required for your projects in advance. This allows for you to anticipate how much you can sell.
-
Project-driven: This method allows you to set aside enough funds for your project. If you know the amount you require, you can buy the materials you need.
-
Resource-based JIT is the most widespread form. Here, you allocate certain resources based on demand. You will, for example, assign more staff to deal with large orders. If you don't receive many orders, then you'll assign fewer employees to handle the load.
-
Cost-based: This approach is very similar to resource-based. However, you don't just care about the number of people you have; you also need to consider how much each person will cost.
-
Price-based: This approach is very similar to the cost-based method except that you don't look at individual workers costs but the total cost of the company.
-
Material-based is an alternative to cost-based. Instead of looking at the total cost in the company, this method focuses on the average amount of raw materials that you consume.
-
Time-based: Another variation of resource-based JIT. Instead of worrying about how much each worker costs, you can focus on how long the project takes.
-
Quality-based: This is yet another variation of resource-based JIT. Instead of thinking about how much each employee costs or how long it takes to manufacture something, you think about how good the quality of your product is.
-
Value-based JIT: One of the most recent forms of JIT. In this scenario, you're not concerned about how products perform or whether customers expect them to meet their expectations. Instead, your focus is on the value you bring to the market.
-
Stock-based. This method is inventory-based and focuses only on the actual production at any given point. This is used to increase production and minimize inventory.
-
Just-in time (JIT), planning: This is a combination JIT/supply chain management. It refers to the process of scheduling the delivery of components as soon as they are ordered. It's important as it reduces leadtimes and increases throughput.