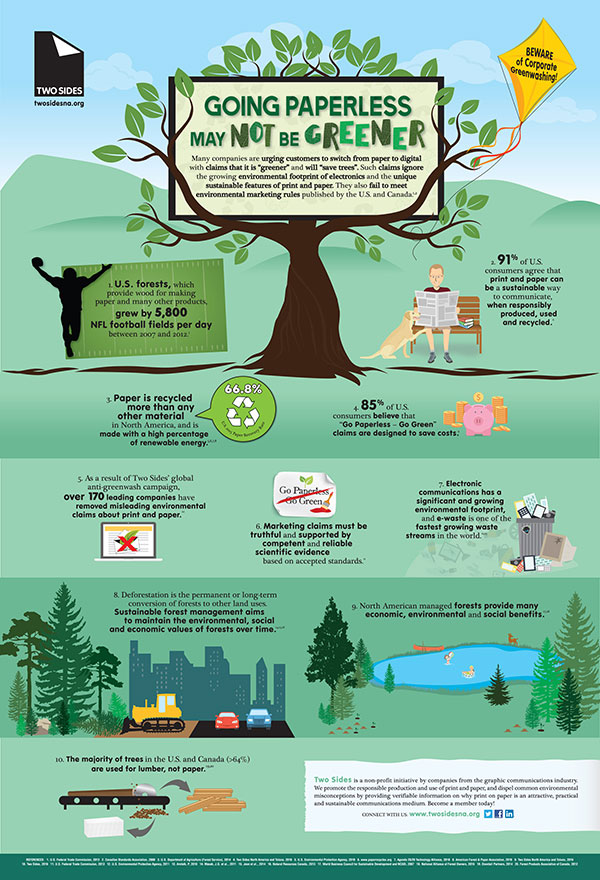
The Production Development Engineer will optimize manufacturing processes. Your responsibilities include setting up a team to ensure product quality and delivery on time. You should be adaptable, innovative and a good communicator. A development-oriented mindset is essential as well as strong analytical skills.
As part of the Advanced Manufacturing Engineering Team the Production Development Engineer works with cross-functional teams. He or she will analyze existing product and process development problems and use process technology in order to increase productivity, reduce costs, and improve quality. A Production Development Engineer will also be able to work with vendors outside of the company to solve technical issues.
This position requires a bachelor of engineering degree. Candidates must have at minimum three years of manufacturing experience. It is desirable to have a strong understanding of Lean Manufacturing. Understanding of technical communication programs and report writing is essential. Production Development Team is looking for someone who has a passion to invent and find cost-effective solutions.
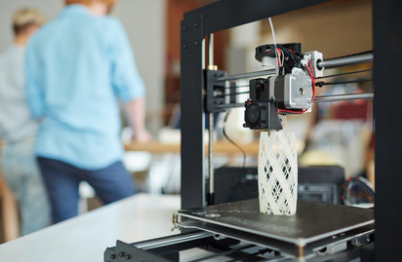
Product engineers are the ones who develop new product ideas. Their duties include identifying consumer needs and preferences, analyzing data, and developing product prototypes. They provide production specifications and quality control. To determine design tolerances or problems, they also test and analyze the proposed product. These tasks require excellent mathematical and analytical skills.
A Production Development Engineer with a high level of success will be creative, efficient, and resourceful. He or she must not only be creative in designing new products but also be able meet the budgetary expectations and satisfy stakeholder needs. To be able to do this you will need extensive industry-specific product knowledge and a solid understanding of manufacturing processes.
Product engineers typically work in fields of expertise such as electrical, materials, and software. Optics, mechanics and testing may also be areas of expertise. The production development engineer is involved in all stages of a project. Producing a new product requires that the production development engineer ensures that the equipment and methods used meet the quality, cost and time goals.
During the product's design phase, the Product Development Engineer will investigate and test the product to identify any potential problems or design tolerances. Then, he or she will create a new prototype with built-in control features that saves money during the manufacturing process.
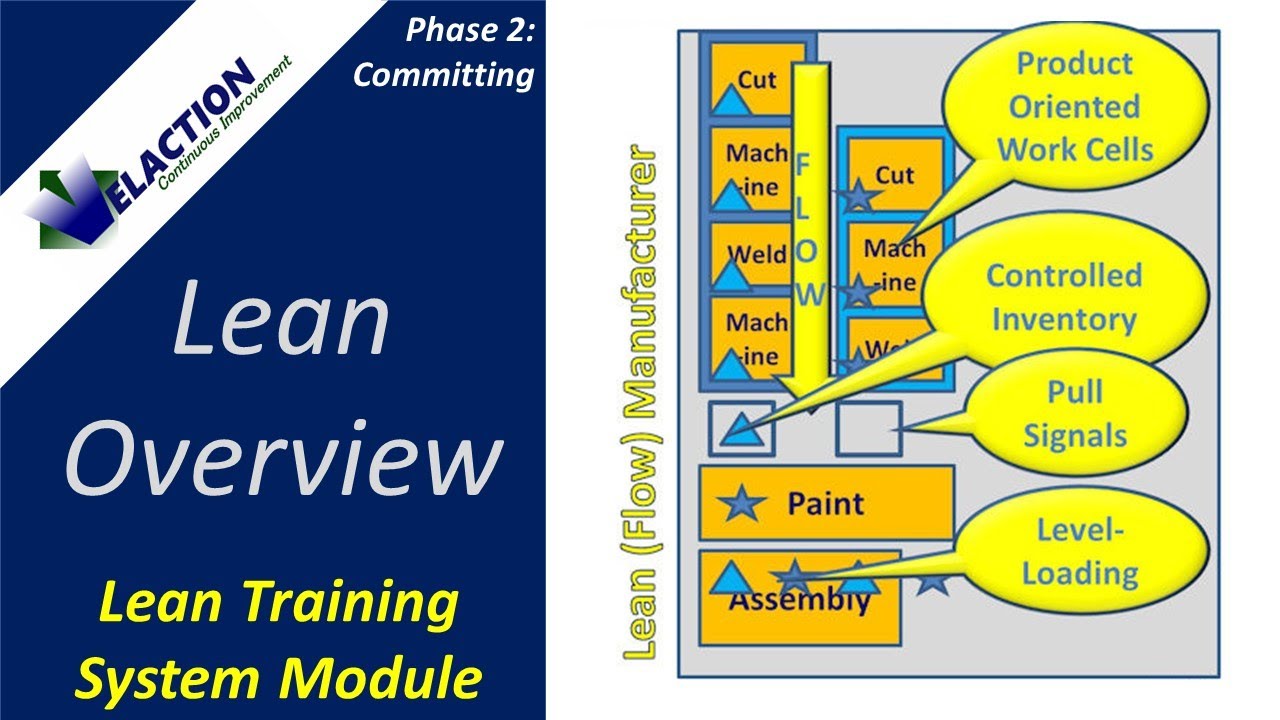
After the design has been completed, the Product Development Engineer will coordinate all activities with other departments and develop a quality control plan to ensure that the product meets its requirements. This includes addressing safety and environmental concerns. The engineer will then deliver the approved product plans to production.
A Production Development Engineer should have an excellent working knowledge of surface modeling software and 3D modeling. It is also a plus if the candidate has a background in the assembly industry.
FAQ
What does it take to run a logistics business?
It takes a lot of skills and knowledge to run a successful logistics business. Effective communication skills are necessary to work with suppliers and clients. You must be able analyze data and draw out conclusions. You must be able and able to handle stress situations and work under pressure. In order to innovate and create new ways to improve efficiency, creativity is essential. You will need strong leadership skills to motivate and direct your team members towards achieving their organizational goals.
You must be organized to meet tight deadlines.
How can manufacturing reduce production bottlenecks?
Production bottlenecks can be avoided by ensuring that processes are running smoothly during the entire production process, starting with the receipt of an order and ending when the product ships.
This includes planning to meet capacity requirements and quality control.
Continuous improvement techniques such Six Sigma can help you achieve this.
Six Sigma Management System is a method to increase quality and reduce waste throughout your organization.
It focuses on eliminating variation and creating consistency in your work.
What is the importance of logistics in manufacturing?
Logistics are essential to any business. They enable you to achieve outstanding results by helping manage product flow from raw materials through to finished goods.
Logistics are also important in reducing costs and improving efficiency.
What skills are required to be a production manager?
A production planner must be organized, flexible, and able multitask to succeed. You must also be able to communicate effectively with clients and colleagues.
What is the responsibility of a logistics manager?
A logistics manager makes sure that all goods are delivered on-time and in good condition. This is done using his/her knowledge of the company's products. He/she also needs to ensure adequate stock to meet demand.
What are my options for learning more about manufacturing
The best way to learn about manufacturing is through hands-on experience. But if that is not possible you can always read books and watch educational videos.
What are the products of logistics?
Logistics involves the transportation of goods from point A and point B.
They include all aspects associated with transport including packaging, loading transporting, unloading storage, warehousing inventory management customer service, distribution returns and recycling.
Logisticians ensure the product reaches its destination in the most efficient manner. They assist companies with their supply chain efficiency through information on demand forecasts. Stock levels, production times, and availability.
They monitor shipments in transit, ensure quality standards, manage inventories, replenish orders, coordinate with suppliers and other vendors, and offer support services for sales, marketing, and customer service.
Statistics
- In the United States, for example, manufacturing makes up 15% of the economic output. (twi-global.com)
- (2:04) MTO is a production technique wherein products are customized according to customer specifications, and production only starts after an order is received. (oracle.com)
- Job #1 is delivering the ordered product according to specifications: color, size, brand, and quantity. (netsuite.com)
- In 2021, an estimated 12.1 million Americans work in the manufacturing sector.6 (investopedia.com)
- You can multiply the result by 100 to get the total percent of monthly overhead. (investopedia.com)
External Links
How To
How to Use the Just In Time Method in Production
Just-in-time (JIT) is a method that is used to reduce costs and maximize efficiency in business processes. It's a way to ensure that you get the right resources at just the right time. This means that your only pay for the resources you actually use. Frederick Taylor, a 1900s foreman, first coined the term. After observing how workers were paid overtime for late work, he realized that overtime was a common practice. He then concluded that if he could ensure that workers had enough time to do their job before starting to work, this would improve productivity.
JIT is about planning ahead. You should have all the necessary resources ready to go so that you don’t waste money. It is important to look at your entire project from beginning to end and ensure that you have enough resources to handle any issues that may arise. If you expect problems to arise, you will be able to provide the necessary equipment and personnel to address them. This way you won't be spending more on things that aren’t really needed.
There are many JIT methods.
-
Demand-driven: This JIT is where you place regular orders for the parts/materials that are needed for your project. This will let you track the amount of material left over after you've used it. This will allow you to calculate how long it will take to make more.
-
Inventory-based: This type allows you to stock the materials needed for your projects ahead of time. This allows you to forecast how much you will sell.
-
Project-driven: This means that you have enough money to pay for your project. If you know the amount you require, you can buy the materials you need.
-
Resource-based: This is the most common form of JIT. You allocate resources based on the demand. If you have many orders, you will assign more people to manage them. If you don't receive many orders, then you'll assign fewer employees to handle the load.
-
Cost-based : This is similar in concept to resource-based. But here, you aren't concerned about how many people your company has but how much each individual costs.
-
Price-based: This is similar to cost-based but instead of looking at individual workers' salaries, you look at the total company price.
-
Material-based: This is quite similar to cost-based, but instead of looking at the total cost of the company, you're concerned with how much raw materials you spend on average.
-
Time-based JIT: This is another variant of resource-based JIT. Instead of worrying about how much each worker costs, you can focus on how long the project takes.
-
Quality-based JIT - This is another form of resource-based JIT. Instead of worrying about the costs of each employee or how long it takes for something to be made, you should think about how quality your product is.
-
Value-based JIT : This is the newest type of JIT. This is where you don't care about how the products perform or whether they meet customers' expectations. Instead, you're focused on how much value you add to the market.
-
Stock-based: This stock-based method focuses on the actual quantity of products being made at any given time. This method is useful when you want to increase production while decreasing inventory.
-
Just-in time (JIT), planning: This is a combination JIT/supply chain management. It refers to the process of scheduling the delivery of components as soon as they are ordered. It reduces lead times and improves throughput.