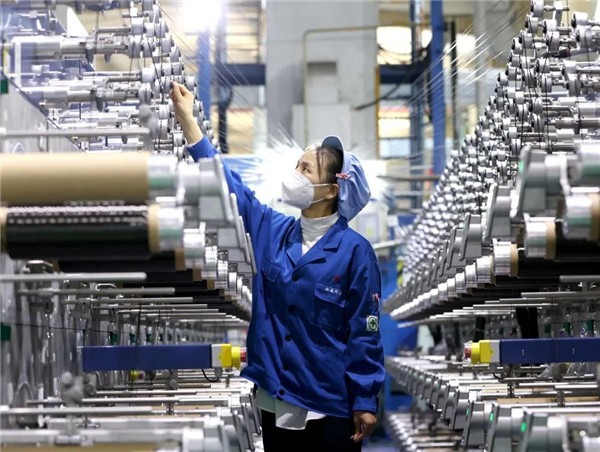
The United States' manufacturing sector is growing. The United States is the third largest manufacturer in the world. In Q1 2018, the country's total manufacturing output surpassed $1.95 trillion. It is expected to surpass that mark by 2022. This is due in large part to automation and productivity gains.
High-Wage America institutes
The High Wage America movement is an effort to improve the economy by creating high-wage jobs. Low wages and high levels in inequality continue to be a problem for the American economy, as the country continues its slow recovery after the Great Recession. However, there are some solutions to the current low wage crisis. States and local stakeholders can help improve the working conditions in America by developing an agenda that promotes high-wage work.
Implementing a sustainable manufacturing strategy is the first step. This requires a plan to address wage stagnation, poor working conditions, and a lack of training. This is why the United States should fight unfair trade practices, and create policies that support the growth of manufacturing communities.
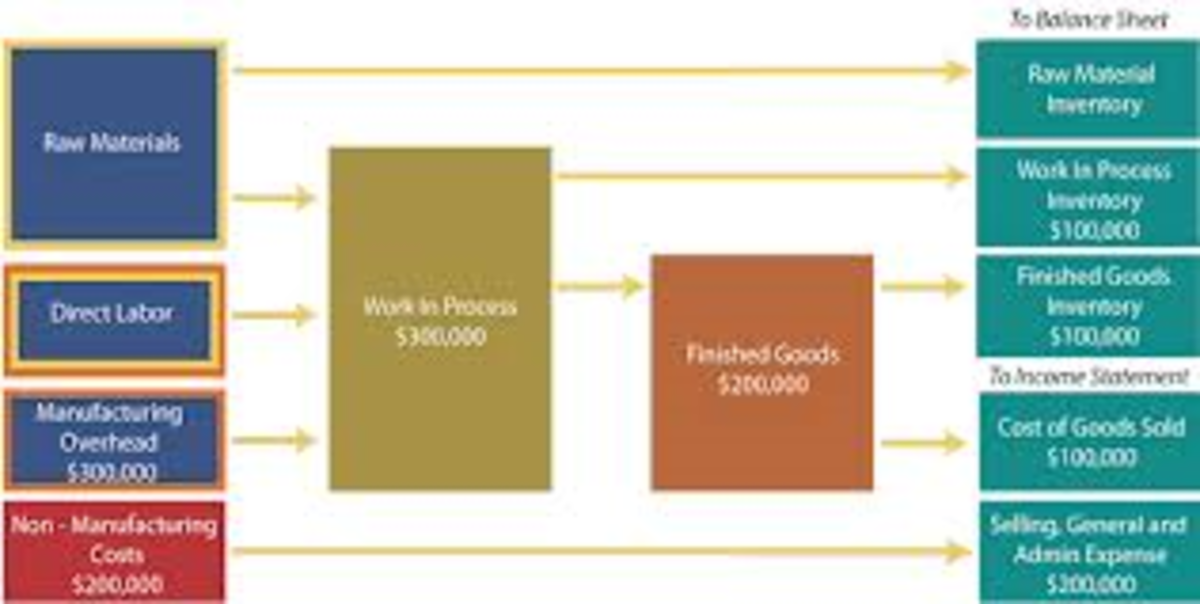
Automation of manufacturing
There is no doubt that automation technologies have changed the way we manufacture products. Automated manufacturing technologies have drastically reduced costs and raised profits for companies and workers. Government policy in the USA is helping to make a difference by encouraging the advancement of new technologies. By encouraging the development new technologies and creating jobs, government policies can actually be beneficial for businesses.
Automated manufacturing started in the US in early 1900s. The Ford Motor Company launched its first auto assembly line. This first-of-its-kind assembly line improved Ford's production. It reduced the time to assemble a car by about one-and-a-half hours from 12 hours.
Productivity growth
Many factors contribute to the growth of manufacturing productivity. Many industries have large gaps between the top companies and the rest. This shows that productivity growth is possible. As is the availability of technology and mobility that allows production to be moved from one location to another, it is vital to increase infrastructure investment. Productivity can be described as the sum of output and inputs. Most commonly, these are labor hours. Outputs can also be measured by units sold, produced, or both.
Labor productivity is the most common way to measure productivity. This measure links output to total hours work. However, labor productivity can be broken up by sector, wage levels, and technological advancement. Increased productivity directly impacts company profits. Employers who work more efficiently produce more output for every hour of their labor.
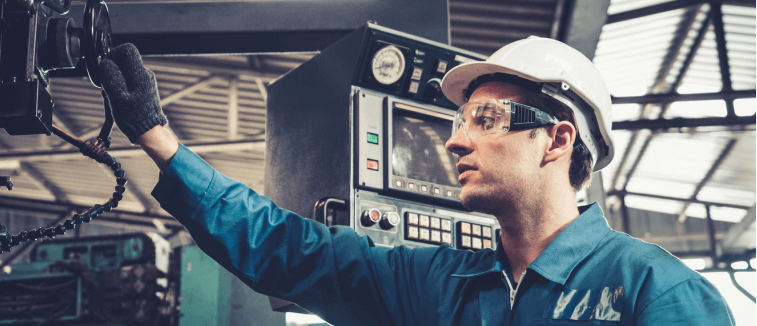
Impact of outsourcing
Multifaceted effects of outsourcing in the US on manufacturing are possible. Some outsourcing can be advantageous, as it allows the country's labor costs to be lower and allows them to compete with other countries. In other cases, outsourcing has the opposite effect, causing the loss of American jobs. Some outsourcing can result is American jobs being taken over by foreign workers. However, in others it can lead American workers earning lower wages.
Outsourcing started with American companies and then expanded to other countries. To reduce costs, some companies shirked all their core activities. Sodexo which provides food services, IBM, and UPS were just a few examples. Companies like Foxconn, which manufactures computers, also started outsourcing. Apple and Foxconn are two examples of companies that have outsourced all their manufacturing.
FAQ
Is automation necessary in manufacturing?
Automation is essential for both manufacturers and service providers. It allows them provide faster and more efficient services. It also helps to reduce costs and improve productivity.
What are the 7 R's of logistics?
The acronym 7R's of Logistic is an acronym that stands for seven fundamental principles of logistics management. It was developed and published by the International Association of Business Logisticians in 2004 as part of the "Seven Principles of Logistics Management".
The following letters form the acronym:
-
Responsible – ensure that all actions are legal and don't cause harm to anyone else.
-
Reliable - have confidence in the ability to deliver on commitments made.
-
Use resources effectively and sparingly.
-
Realistic – Consider all aspects, including cost-effectiveness as well as environmental impact.
-
Respectful - Treat people fairly and equitably
-
Responsive - Look for ways to save time and increase productivity.
-
Recognizable - provide customers with value-added services.
What does manufacturing mean?
Manufacturing Industries are companies that manufacture products. Consumers are the people who purchase these products. These companies employ many processes to achieve this purpose, such as production and distribution, retailing, management and so on. They create goods from raw materials, using machines and various other equipment. This includes all types manufactured goods such as clothing, building materials, furniture, electronics, tools and machinery.
What are the 4 types of manufacturing?
Manufacturing is the process of transforming raw materials into useful products using machines and processes. Manufacturing involves many activities, including designing, building, testing and packaging, shipping, selling, service, and so on.
How can manufacturing avoid production bottlenecks
Production bottlenecks can be avoided by ensuring that processes are running smoothly during the entire production process, starting with the receipt of an order and ending when the product ships.
This includes both planning for capacity and quality control.
Continuous improvement techniques such Six Sigma can help you achieve this.
Six Sigma Management System is a method to increase quality and reduce waste throughout your organization.
It seeks to eliminate variation and create consistency in your work.
Statistics
- In the United States, for example, manufacturing makes up 15% of the economic output. (twi-global.com)
- [54][55] These are the top 50 countries by the total value of manufacturing output in US dollars for its noted year according to World Bank.[56] (en.wikipedia.org)
- Job #1 is delivering the ordered product according to specifications: color, size, brand, and quantity. (netsuite.com)
- In 2021, an estimated 12.1 million Americans work in the manufacturing sector.6 (investopedia.com)
- According to a Statista study, U.S. businesses spent $1.63 trillion on logistics in 2019, moving goods from origin to end user through various supply chain network segments. (netsuite.com)
External Links
How To
How to Use 5S to Increase Productivity in Manufacturing
5S stands for "Sort", 'Set In Order", 'Standardize', & Separate>. Toyota Motor Corporation invented the 5S strategy in 1954. It helps companies achieve higher levels of efficiency by improving their work environment.
This method aims to standardize production processes so that they are repeatable, measurable and predictable. It means tasks like cleaning, sorting or packing, labeling, and storing are done every day. Through these actions, workers can perform their jobs more efficiently because they know what to expect from them.
Implementing 5S involves five steps: Sort, Set in Order, Standardize Separate, Store, and Each step involves a different action which leads to increased efficiency. You can make it easy for people to find things later by sorting them. You arrange items by placing them in an order. After you have divided your inventory into groups you can store them in easy-to-reach containers. Labeling your containers will ensure that everything is correctly labeled.
Employees need to reflect on how they do their jobs. Employees should understand why they do the tasks they do, and then decide if there are better ways to accomplish them. They must learn new skills and techniques in order to implement the 5S system.
The 5S method not only increases efficiency but also boosts morale and teamwork. Once they start to notice improvements, they are motivated to keep working towards their goal of increasing efficiency.