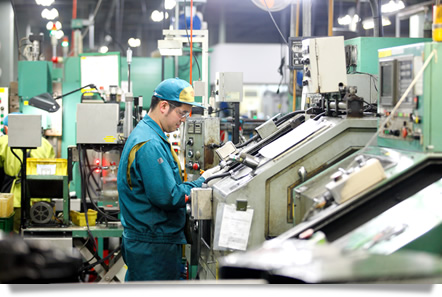
Whether you are running a small business or the enterprise arm of a major corporation, supply chain risk management is a necessary component to maintaining a robust operation. There are many risks that can occur, from the seemingly mundane to the potentially disastrous. Your organization can be protected from losses with a well-planned plan and an effective implementation strategy.
Data sharing is an essential part of a supply chain continuity program. If you rely on one supplier, your organization is more vulnerable to supplier problems and vendor disputes. However, if your company is part of a multi-supplier consortium, you are more likely to avoid supply disruptions. It may also be possible to negotiate with another supplier.
Also, vendor fraud, duplicate and improper related-party bills are all possible if your company has many contractors. You can create a risk assessment method to help reduce these risks. This can include a thorough assessment of your partners, suppliers, and other tier-one components.
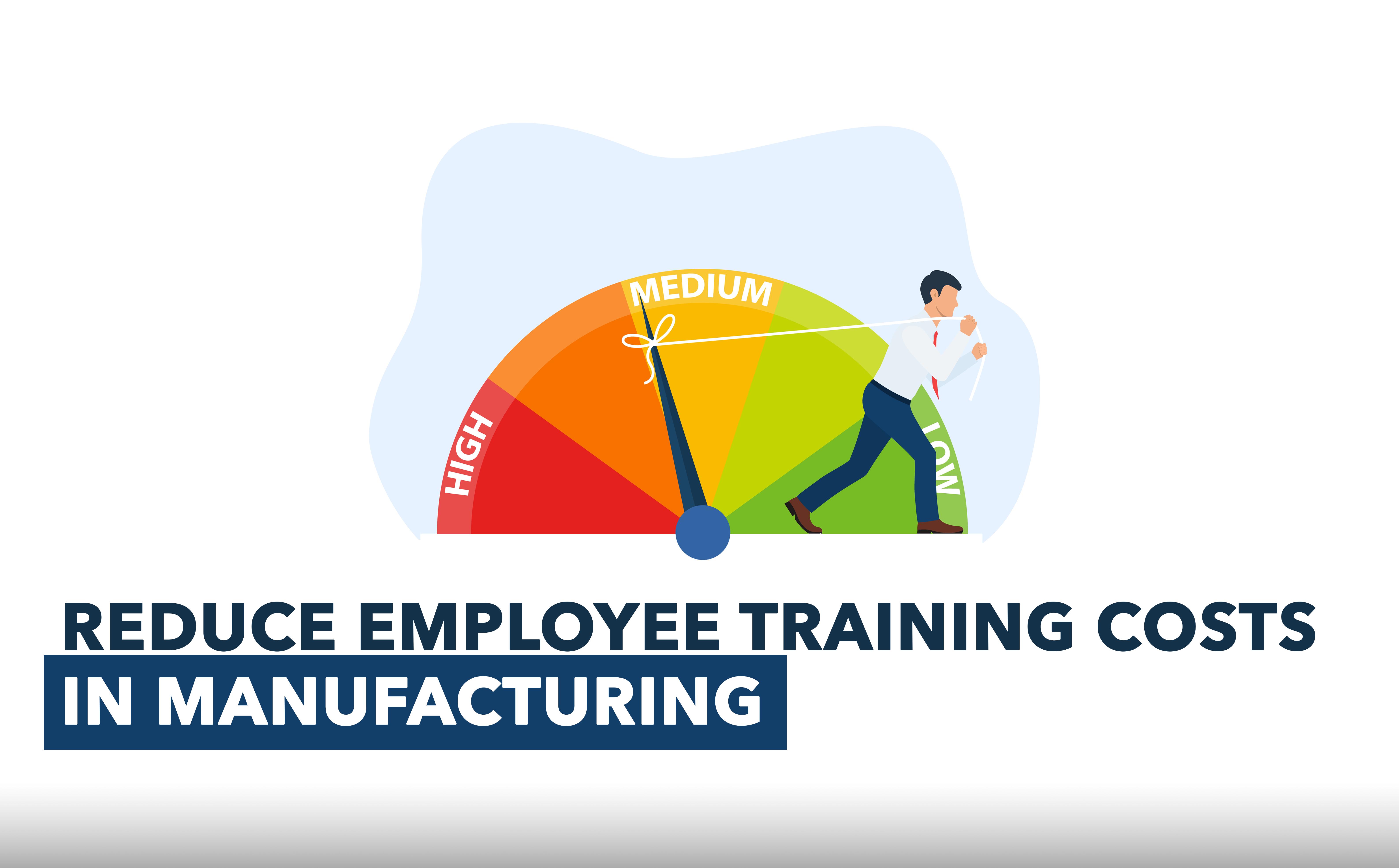
When developing a good supply chain risk management program, you should first identify the important elements of a good supply chain, then quantify and measure them, and then devise an action plan. It should include all of the above and a few other items. A proactive monitoring program is essential. It is important that your executives have access to real-time, accurate information regarding supply chain risk. You can make better decisions and react quickly by monitoring supply risk in real-time.
As you begin assessing and quantifying your risks, it is essential to keep in mind that your supply chain's resilience is a function of governance. It is important to take into account the role of stakeholders. A properly scorecarded supplier system could have saved the pharmacy from a bankruptcy.
The first step to reducing supply chain disruptions is having a plan. But, it is not always simple to put in place the right contingency strategies. Many businesses neglect to make the effort to have enough contingency planning for every risk they face. These plans should be designed to have the highest possible impact.
The PPPR (preventive, preparedness and response) method is an internationally recognized standard in supply chain risk management. This method is robust and can increase your ability to respond to supply chain disruptions. It's often used in conjunction to other strategies to protect the organization from risks. Using a PPPR guide to your organization can mean the difference between survival and success in today's market.
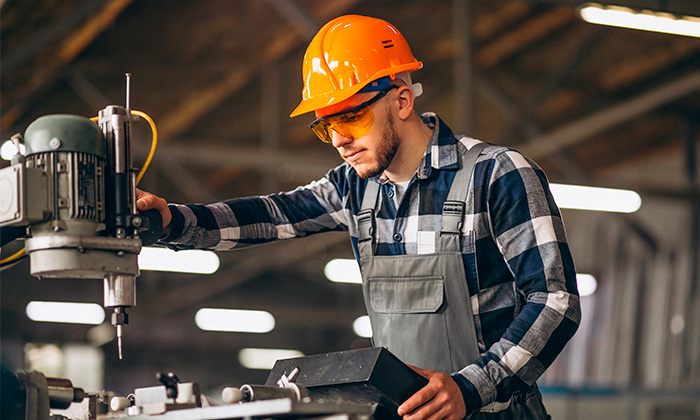
The right data can help you understand your suppliers' history and what they offer. This information can help you make informed decisions, regardless of whether you're looking to expand your sourcing efforts and/or improve your existing processes. Having reliable data can help you provide your insurers with the right risk premiums.
FAQ
What are the responsibilities of a manufacturing manager
A manufacturing manager must make sure that all manufacturing processes run smoothly and effectively. They should also be aware and responsive to any company problems.
They should also be able communicate with other departments, such as sales or marketing.
They must also keep up-to-date with the latest trends in their field and be able use this information to improve productivity and efficiency.
What jobs are available in logistics?
There are many kinds of jobs available within logistics. These are some of the jobs available in logistics:
-
Warehouse workers – They load and unload pallets and trucks.
-
Transportation drivers – They drive trucks or trailers to transport goods and perform pick-ups.
-
Freight handlers, - They sort out and pack freight in warehouses.
-
Inventory managers – They manage the inventory in warehouses.
-
Sales representatives - They sell products.
-
Logistics coordinators: They plan and manage logistics operations.
-
Purchasing agents – They buy goods or services necessary to run a company.
-
Customer service agents - They answer phone calls and respond to emails.
-
Shipping clerks - They process shipping orders and issue bills.
-
Order fillers - They fill orders based on what is ordered and shipped.
-
Quality control inspectors (QCI) - They inspect all incoming and departing products for potential defects.
-
Others - There is a variety of other jobs in logistics. These include transportation supervisors and cargo specialists.
What's the difference between Production Planning & Scheduling?
Production Planning (PP) refers to the process of determining how much production is needed at any given moment. This can be done by forecasting demand and identifying production capabilities.
Scheduling is the process of assigning specific dates to tasks so they can be completed within the specified timeframe.
What is the responsibility of a production planner?
Production planners make sure that every aspect of the project is delivered on-time, within budget, and within schedule. They make sure that the product and services meet client expectations.
Why should you automate your warehouse?
Modern warehouses have become more dependent on automation. With the rise of ecommerce, there is a greater demand for faster delivery times as well as more efficient processes.
Warehouses should be able adapt quickly to new needs. Technology investment is necessary to enable warehouses to respond quickly to changing demands. Automation warehouses can bring many benefits. Here are some of the reasons automation is worth your investment:
-
Increases throughput/productivity
-
Reduces errors
-
Accuracy is improved
-
Safety is boosted
-
Eliminates bottlenecks
-
Allows companies to scale more easily
-
Increases efficiency of workers
-
This gives you visibility into what happens in the warehouse
-
Enhances customer experience
-
Improves employee satisfaction
-
It reduces downtime, and increases uptime
-
Ensures quality products are delivered on time
-
Removes human error
-
Assure compliance with regulations
Statistics
- In 2021, an estimated 12.1 million Americans work in the manufacturing sector.6 (investopedia.com)
- In the United States, for example, manufacturing makes up 15% of the economic output. (twi-global.com)
- Job #1 is delivering the ordered product according to specifications: color, size, brand, and quantity. (netsuite.com)
- You can multiply the result by 100 to get the total percent of monthly overhead. (investopedia.com)
- (2:04) MTO is a production technique wherein products are customized according to customer specifications, and production only starts after an order is received. (oracle.com)
External Links
How To
How to Use Six Sigma in Manufacturing
Six Sigma can be described as "the use of statistical process control (SPC), techniques to achieve continuous improvement." Motorola's Quality Improvement Department developed it at their Tokyo plant in Japan in 1986. Six Sigma's basic concept is to improve quality and eliminate defects through standardization. Many companies have adopted this method in recent years. They believe there is no such thing a perfect product or service. Six Sigma's main objective is to reduce variations from the production average. This means that if you take a sample of your product, then measure its performance against the average, you can find out what percentage of the time the process deviates from the norm. If there is a significant deviation from the norm, you will know that something needs to change.
Understanding how variability works in your company is the first step to Six Sigma. Once you understand that, it is time to identify the sources of variation. This will allow you to decide if these variations are random and systematic. Random variations are caused by human errors. Systematic variations can be caused by outside factors. You could consider random variations if some widgets fall off the assembly lines. If however, you notice that each time you assemble a widget it falls apart in exactly the same spot, that is a problem.
Once you identify the problem areas, it is time to create solutions. It might mean changing the way you do business or redesigning it entirely. To verify that the changes have worked, you need to test them again. If they don't work, you will need to go back to the drawing boards and create a new plan.