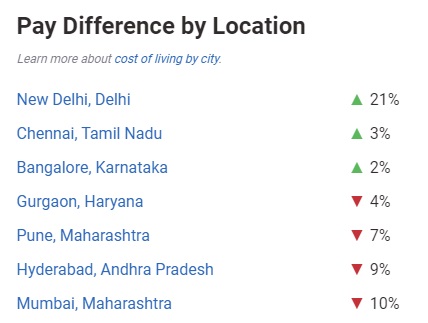
Typically, tool and die makers work in machine shops. They operate lathes, milling machines, and other types of machine tools. They can also repair dies and tools for machinists. They may also design and manufacture tools for customers.
Tool and diemakers are required to adhere to high quality standards and maintain precision in their work. They ensure that their work is accurate and inspect finished products. To improve processes, tool- and die-makers can work with engineers. They may also visit the plant of a customer to test the tool's performance. They are expected also to keep their work area tidy and organized. They may also wear protective gear. They may suggest new tools to make the process more efficient.
Tool and die-makers typically work 40 hours per week. They might also be expected to do some moderately heavy lifting. A strong education background is also necessary. Employers prefer associate's or bachelors degrees in related fields. They may also get formal on-thejob training or be part of apprenticeship programs.
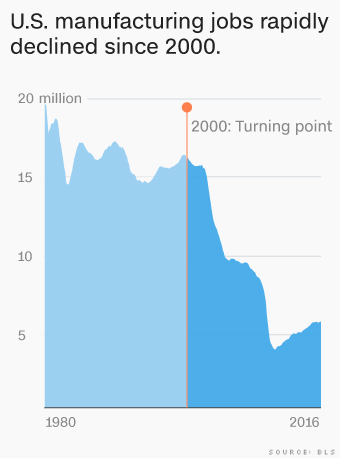
For tool and diemakers, four-year apprenticeship programs usually take place with employers. They get on-the job training from an experienced worker throughout the apprenticeship program. They also attend technical college courses at night. The program includes classroom instruction, hands-on training and practical experience. They may also be given the chance to program computer controlled machine tools. They may also advance to supervisory positions.
Tool and die makers typically have a high school diploma or equivalent. A degree in engineering or physics may also be an option. They might have also had training in science, math, or both. This training is often beneficial.
Good eyesight is essential for tool and die makers. They need to be patient and able to focus. They must also have the physical strength to operate machinery. They should be hardworking and able to lift heavy items. They should be capable of reading engineering drawings and specifications. They should have strong interpersonal skills. They must also be proficient in computer use. They may also be required to maintain computer numerically controlled (CNC) machines.
An analytical mind is essential for tool and die makers. They have to understand how tools and dies work and how to repair them. They also need to be problem-solving and have mechanical aptitude. They may also be required to learn new methods of machining. They will need to be proficient in digital skills like computer-aided planning (CAD) and computer aided manufacturing (CAM). They should also possess sales skills. They should be able collaborate with others and work independently.
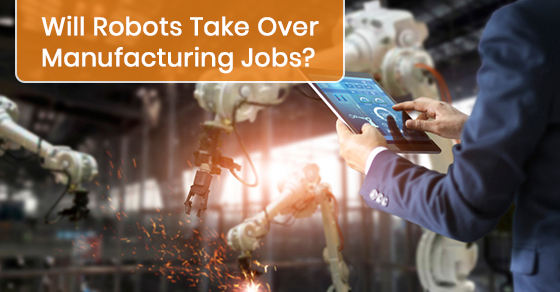
Apprentices work on average 40 hours per week during an apprenticeship program. They are required to attend school at night and do a job during work hours. They eventually accept more challenging jobs. Most apprenticeships require a high school diploma or equivalent. They should also be able to learn science and math.
Some tool or die makers continue on to pursue a bachelor’s or master’s degree. Average income for tool and denter makers is $56,186. Their job prospects will likely decrease due to automation.
FAQ
What is the job of a production plan?
A production planner makes sure all project elements are delivered on schedule, within budget, as well as within the agreed scope. They ensure that the product or service is of high quality and meets client requirements.
What is the responsibility of a manufacturing manager?
Manufacturing managers must ensure that manufacturing processes are efficient, effective, and cost-effective. They should also be aware and responsive to any company problems.
They should also be able and comfortable communicating with other departments like sales and marketing.
They must also keep up-to-date with the latest trends in their field and be able use this information to improve productivity and efficiency.
What are the 7 Rs of logistics management?
The acronym 7R's of Logistic is an acronym that stands for seven fundamental principles of logistics management. It was developed and published by the International Association of Business Logisticians in 2004 as part of the "Seven Principles of Logistics Management".
The acronym is made up of the following letters:
-
Responsive - ensure all actions are legal and not harmful to others.
-
Reliable - Have confidence in your ability to fulfill all of your commitments.
-
It is reasonable to use resources efficiently and not waste them.
-
Realistic – Consider all aspects, including cost-effectiveness as well as environmental impact.
-
Respectful - treat people fairly and equitably.
-
You are resourceful and look for ways to save money while increasing productivity.
-
Recognizable: Provide customers with value-added service
What does warehouse mean?
A warehouse is a place where goods are stored until they are sold. It can be an indoor space or an outdoor area. In some cases it could be both indoors and outdoors.
What is the job of a logistics manger?
Logistics managers make sure all goods are delivered on schedule and without damage. This is accomplished by using the experience and knowledge gained from working with company products. He/she should also ensure enough stock is available to meet demand.
What is the distinction between Production Planning or Scheduling?
Production Planning (PP), also known as forecasting and identifying production capacities, is the process that determines what product needs to be produced at any particular time. This is done through forecasting demand and identifying production capacities.
Scheduling is the process of assigning specific dates to tasks so they can be completed within the specified timeframe.
Statistics
- Job #1 is delivering the ordered product according to specifications: color, size, brand, and quantity. (netsuite.com)
- In the United States, for example, manufacturing makes up 15% of the economic output. (twi-global.com)
- [54][55] These are the top 50 countries by the total value of manufacturing output in US dollars for its noted year according to World Bank.[56] (en.wikipedia.org)
- (2:04) MTO is a production technique wherein products are customized according to customer specifications, and production only starts after an order is received. (oracle.com)
- Many factories witnessed a 30% increase in output due to the shift to electric motors. (en.wikipedia.org)
External Links
How To
How to use Lean Manufacturing in the production of goods
Lean manufacturing is a management style that aims to increase efficiency and reduce waste through continuous improvement. It was developed in Japan between 1970 and 1980 by Taiichi Ohno. TPS founder Kanji Tyoda gave him the Toyota Production System, or TPS award. The first book published on lean manufacturing was titled "The Machine That Changed the World" written by Michael L. Watkins and published in 1990.
Lean manufacturing is often described as a set if principles that help improve the quality and speed of products and services. It emphasizes the elimination of defects and waste throughout the value stream. Lean manufacturing is called just-in-time (JIT), zero defect, total productive maintenance (TPM), or 5S. Lean manufacturing focuses on eliminating non-value-added activities such as rework, inspection, and waiting.
Lean manufacturing improves product quality and costs. It also helps companies reach their goals quicker and decreases employee turnover. Lean manufacturing can be used to manage all aspects of the value chain. Customers, suppliers, distributors, retailers and employees are all included. Lean manufacturing is widely practiced in many industries around the world. Toyota's philosophy is the foundation of its success in automotives, electronics and appliances, healthcare, chemical engineers, aerospace, paper and food, among other industries.
Lean manufacturing is based on five principles:
-
Define Value: Identify the social value of your business and what sets you apart.
-
Reduce Waste – Eliminate all activities that don't add value throughout the supply chain.
-
Create Flow - Make sure work runs smoothly without interruptions.
-
Standardize and Simplify – Make processes as consistent, repeatable, and as simple as possible.
-
Develop Relationships: Establish personal relationships both with internal and external stakeholders.
Lean manufacturing isn’t new, but it has seen a renewed interest since 2008 due to the global financial crisis. To increase their competitiveness, many businesses have turned to lean manufacturing. According to some economists, lean manufacturing could be a significant factor in the economic recovery.
Lean manufacturing has many benefits in the automotive sector. These benefits include increased customer satisfaction, reduced inventory levels and lower operating costs.
Any aspect of an enterprise can benefit from Lean manufacturing. It is especially useful for the production aspect of an organization, as it ensures that every step in the value chain is efficient and effective.
There are three main types in lean manufacturing
-
Just-in Time Manufacturing, (JIT): This kind of lean manufacturing is also commonly known as "pull-systems." JIT stands for a system where components are assembled on the spot rather than being made in advance. This approach reduces lead time, increases availability and reduces inventory.
-
Zero Defects Manufacturing: ZDM ensures that no defective units leave the manufacturing plant. It is better to repair a part than have it removed from the production line if it needs to be fixed. This applies to finished goods that may require minor repairs before shipment.
-
Continuous Improvement (CI),: Continuous improvement aims improve the efficiency and effectiveness of operations by continuously identifying issues and making changes to reduce waste. Continuous improvement involves continuous improvement of processes and people as well as tools.