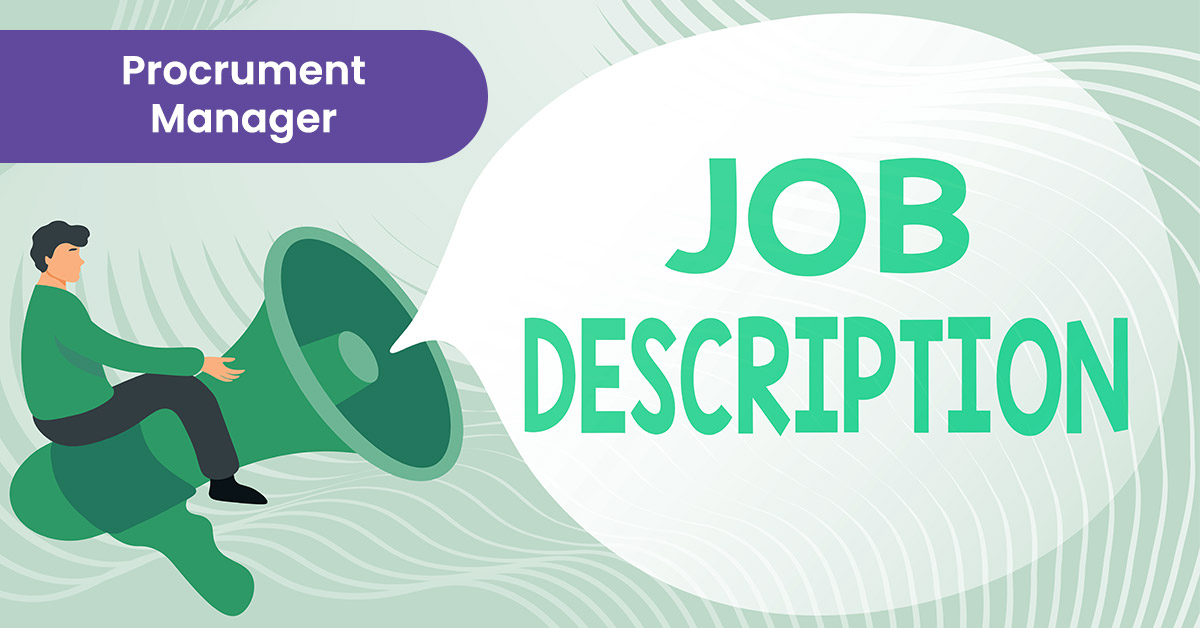
Chemical manufacturing is an important industry in America that transforms organic raw materials into useful products. It supplies raw materials to industries such as plastics and explosives. However, the chemical industry also faces many challenges. Many chemical workers are at-risk of safety and health concerns.
Chemical manufacturing is organized into two main segments: commodity chemicals and specialty chemicals. These two segments share the same infrastructure and processes. The types of products they produce are however different. Specialty chemical are often designed to be used by customers. Some of the most expensive chemicals are manufactured by specialty manufacturers. Many of these chemicals are protected under patents.
Although some chemicals are produced in a single location, most petrochemicals and commodity chemicals are produced in large-scale facilities. Rotterdam (the Netherlands) and Texas are examples of large scale chemical plants. Large scale chemical plants often share utilities and other infrastructures, creating economies of scale.
The United States is China's second largest chemical producer. According to Statista, the chemical industry is worth more than $4 trillion annually. About half the industry's revenues are generated by the top 50 US businesses.
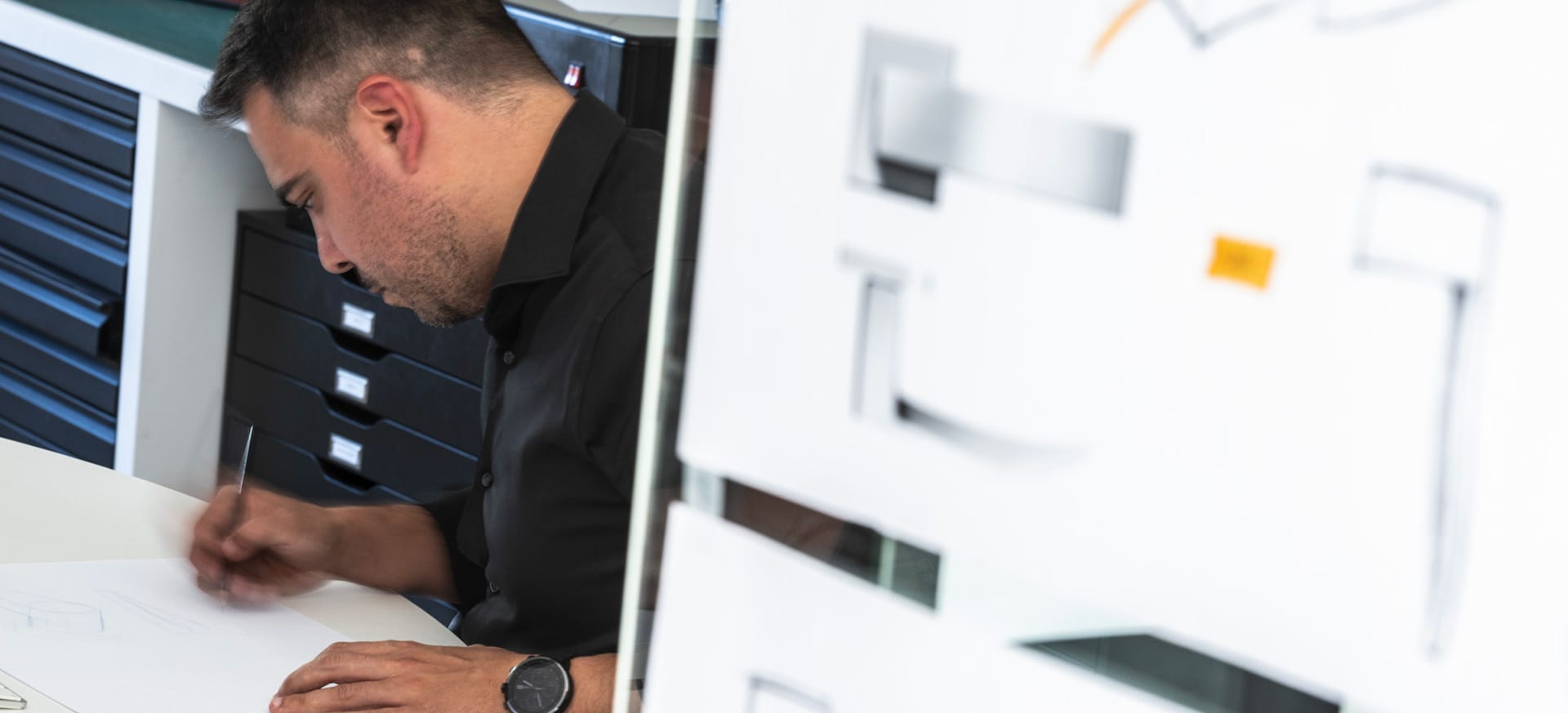
The chemical manufacturing industry employs approximately 20 million people worldwide. While most of these workers are in large-scale facilities, a small number are part-time or contract employees. The sector's employment is being affected by technological advances and increased competition.
The overall U.S. economy drives the demand for chemicals. The chemical industry, in particular, is highly regulated. Governing bodies set regulations and standards for the manufacturing process. Companies must implement environmentally sustainable operations. Some chemicals manufacturing raw materials are extremely dangerous to extract.
This industry is facing a difficult procurement process. A high cost of raw material acquisition is another problem. Some companies move their operations to lower-cost locations in order to keep costs down. Lastly, some companies are merging or moving their production activities to developing countries. This will lead to the loss of jobs.
In 2008, basic chemical manufacturing accounted for 80 percent. This group includes manufacturers of dyes, pesticides, and other material. Pfizer, Dow, and BASF are the most prominent manufacturers in this segment. Other major players include DuPont, Formosa Plastics, and Sinopec Group.
Large-scale production facilities are usually clean. Workers are required to wear safety goggles and work in a temperature-controlled environment. Nevertheless, some workers are replaced by sophisticated machines with computerized controls. Many of these workers work nights.
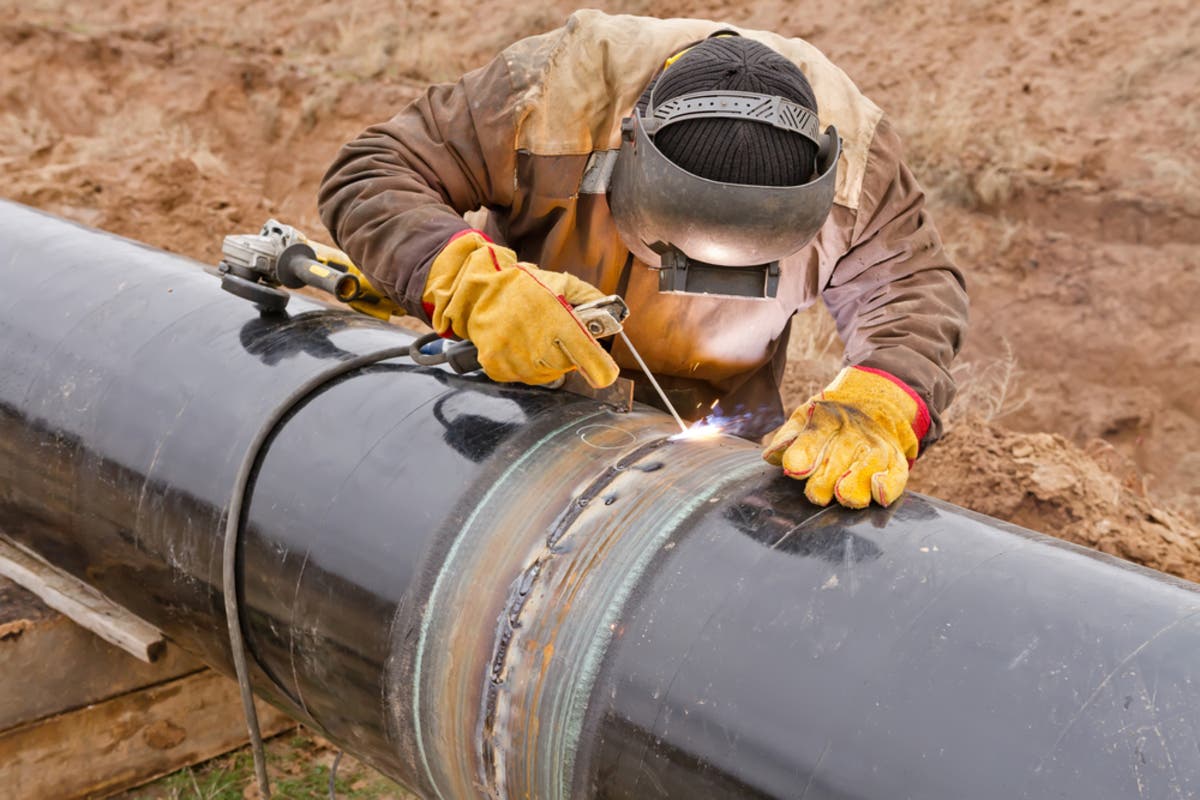
Modifications to chemical manufacturing plants are possible to accommodate new production techniques. New processes can increase accuracy and lower labor costs. Nanotechnology will also make chemical manufacturing more efficient. Nanotechnology can also be used to reduce waste and energy consumption.
Some of the other factors affecting the employment of the chemical manufacturing industry are increased foreign competition, technological advancements, and environmental health and safety concerns. Generally, the industry's employment is projected to decrease 13 percent over the next four years.
FAQ
What are the products and services of logistics?
Logistics refers to all activities that involve moving goods from A to B.
They include all aspects associated with transport including packaging, loading transporting, unloading storage, warehousing inventory management customer service, distribution returns and recycling.
Logisticians ensure that the right product reaches the right place at the right time and under safe conditions. They provide information on demand forecasts as well stock levels, production schedules and availability of raw material.
They also keep track of shipments in transit, monitor quality standards, perform inventories and order replenishment, coordinate with suppliers and vendors, and provide support services for sales and marketing.
Is automation important in manufacturing?
Automation is essential for both manufacturers and service providers. Automation allows them to deliver services quicker and more efficiently. It also helps to reduce costs and improve productivity.
What is the role of a logistics manager
Logistics managers ensure that goods arrive on time and are unharmed. This is done using his/her knowledge of the company's products. He/she should ensure that sufficient stock is available in order to meet customer demand.
How does a Production Planner differ from a Project Manager?
The main difference between a production planner and a project manager is that a project manager is usually the person who plans and organizes the entire project, whereas a production planner is mainly involved in the planning stage of the project.
Statistics
- In 2021, an estimated 12.1 million Americans work in the manufacturing sector.6 (investopedia.com)
- According to the United Nations Industrial Development Organization (UNIDO), China is the top manufacturer worldwide by 2019 output, producing 28.7% of the total global manufacturing output, followed by the United States, Japan, Germany, and India.[52][53] (en.wikipedia.org)
- [54][55] These are the top 50 countries by the total value of manufacturing output in US dollars for its noted year according to World Bank.[56] (en.wikipedia.org)
- (2:04) MTO is a production technique wherein products are customized according to customer specifications, and production only starts after an order is received. (oracle.com)
- Many factories witnessed a 30% increase in output due to the shift to electric motors. (en.wikipedia.org)
External Links
How To
How to Use 5S to Increase Productivity in Manufacturing
5S stands for "Sort", "Set In Order", "Standardize", "Separate" and "Store". Toyota Motor Corporation created the 5S methodology in 1954. It assists companies in improving their work environments and achieving higher efficiency.
This method has the basic goal of standardizing production processes to make them repeatable. It means tasks like cleaning, sorting or packing, labeling, and storing are done every day. Workers can be more productive by knowing what to expect.
There are five steps that you need to follow in order to implement 5S. Each step has a different action and leads to higher efficiency. You can make it easy for people to find things later by sorting them. Once you have placed items in an ordered fashion, you will put them together. Next, organize your inventory into categories and store them in containers that are easily accessible. You can also label your containers to ensure everything is properly labeled.
This requires employees to critically evaluate how they work. Employees should understand why they do the tasks they do, and then decide if there are better ways to accomplish them. To implement the 5S system, employees must acquire new skills and techniques.
The 5S method not only increases efficiency but also boosts morale and teamwork. They feel more motivated to work towards achieving greater efficiency as they see the results.