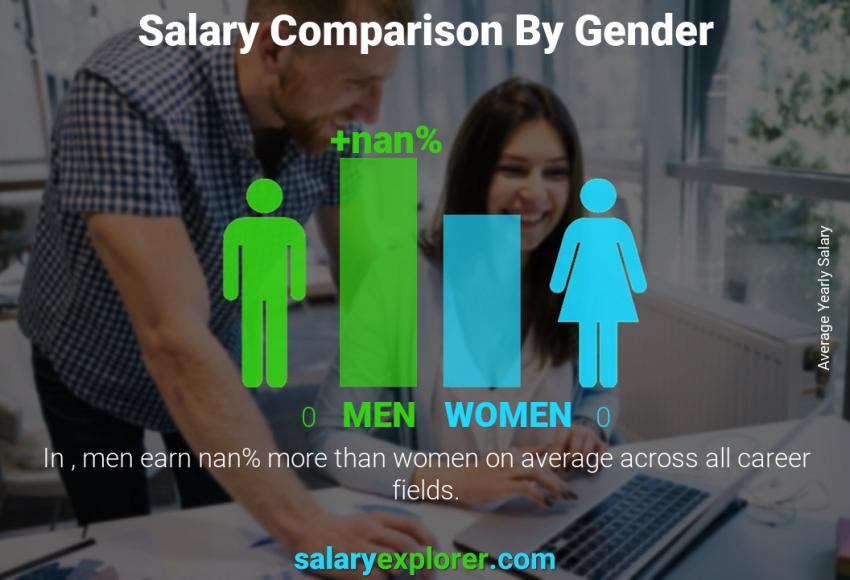
There are many types and styles of manufacturers. Which one is best for you business? Learn more about Continuous manufacturing, Process manufacturing and Job shop manufacturing. Each type comes with its own set of advantages and disadvantages. This article will discuss the differences between these four types. The factors that are most relevant to your business include your industry, geographical location, and product type. Once you've decided on the right type, you should consider your sales, manufacturing, and quality control.
Discrete Manufacturing
Discrete Manufacturing is the process of producing distinct products. Some examples of such products include aeroplanes, automobiles, and toys. Discrete Manufacturing allows companies to focus more on their individual products than on mass production. It is possible, for instance, to make unique parts of an aeroplane through the integration of several manufacturing processes. High-tech products are made using discrete manufacturing.
Discrete manufacturing produces distinct items. Instead of making multiple identical products, discrete manufacture produces distinct items that can easily be identified using serial numbers, labels, or other numerical attributes. For example, a smartphone could be composed of several parts that were manufactured in different states. Each part is assembled only after the final product has been sold. The same applies to the bag that holds your smartphone. It might contain different parts of several plants, including the Missouri plant and headquarters.
Process manufacturing
Process manufacturing refers to a type of manufacturing that uses formulas and recipes. Distinctive manufacturing, which focuses on the manufacture of single units, bills, and components, is called process manufacturing. Both manufacturing methods have different goals. Each of these methods is important in the manufacturing process. There are three main ways to distinguish process manufacturing from discrete manufacturing. Let's have a look at them all.
Batch process manufacturing works in a similar way to continuous production, but it requires larger batches of raw material and is available around the clock. It is commonly used in pharmaceuticals as well as paper production, bookbinding and newspaper printing. This process is not the best for every industry. It can often be too costly and complicated for smaller companies. Therefore, most companies use this method when they need to create large quantities of the same product.
Factory job shop
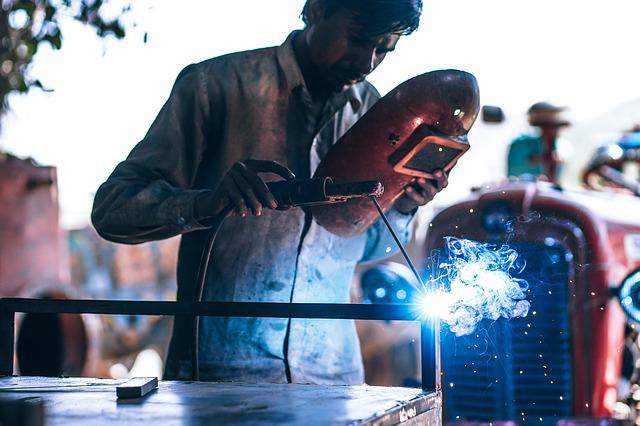
Job shop manufacturing is a small-scale system of production that specializes in custom, batch, and semi-custom manufacturing. After each job is complete, job shop systems can move to the next. This production method is also known as lean manufacturing. A single shift operation is more efficient than other methods. These are just a few of the many benefits of job-shop manufacturing. This manufacturing process is described in detail below. It might be a good option for your business if you need to manufacture products or services.
First, job shops have to be more efficient. New manufacturing principles are a critical component of a lean manufacturing system. These principles emphasize total quality control and just-in-time production, and are highly relevant to high-volume operations. A job shop can improve productivity and reduce costs by adopting new manufacturing principles. Also, each job should be completed one by one, so there shouldn't be any queues.
Continuous manufacturing
Continuous manufacturing's greatest benefit is its flexibility in tracking. This is especially useful when it comes down to product failure. Because the production lines can track the amount of raw materials and the time stamp, this information can be used to identify defective batches of drugs. The increased tracking also helps the manufacturer reduce waste and the chance of a product shortage. Continuous manufacturing is also becoming more popular in the pharmaceutical sector.
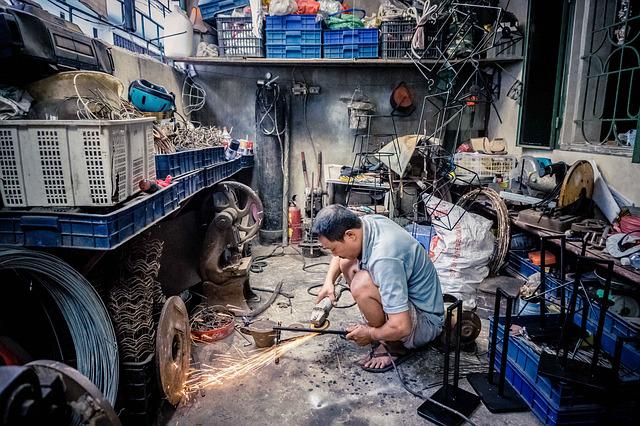
Although continuous manufacturing has many benefits, implementation can be difficult. Implementation is often hampered by the fact that the process is not fully integrated with the rest of the company. Continuous manufacturing, despite its potential benefits, has the potential for a major shift in the pharmaceutical industry. To be successful, however, the entire process must be integrated with continuous flow as well as end-to–end integration. While the benefits of continuous manufacturing have been well-known in the pharmaceutical sector, implementation has been slow.
FAQ
What do you mean by warehouse?
A warehouse is an area where goods are stored before being sold. It can be indoors or out. In some cases, it may be a combination of both.
Why automate your warehouse
Modern warehousing is becoming more automated. E-commerce has brought increased demand for more efficient and quicker delivery times.
Warehouses should be able adapt quickly to new needs. In order to do this, they need to invest in technology. The benefits of automating warehouses are numerous. These are just a few reasons to invest in automation.
-
Increases throughput/productivity
-
Reduces errors
-
Accuracy is improved
-
Safety Boosts
-
Eliminates bottlenecks
-
This allows companies to scale easily
-
It makes workers more efficient
-
Gives you visibility into all that is happening in your warehouse
-
Enhances customer experience
-
Improves employee satisfaction
-
It reduces downtime, and increases uptime
-
High quality products delivered on-time
-
Eliminates human error
-
Assure compliance with regulations
What are my options for learning more about manufacturing
You can learn the most about manufacturing by getting involved in it. But if that is not possible you can always read books and watch educational videos.
What is the difference between Production Planning and Scheduling?
Production Planning (PP), or production planning, is the process by which you determine what products are needed at any given time. This is done through forecasting demand and identifying production capacities.
Scheduling is the process that assigns dates to tasks so they can get completed within a given timeframe.
What are the 7 Rs of logistics?
The acronym 7Rs of Logistics refers to the seven core principles of logistics management. It was developed by the International Association of Business Logisticians (IABL) and published in 2004 as part of its "Seven Principles of Logistics Management" series.
The acronym consists of the following letters:
-
Responsive - ensure all actions are legal and not harmful to others.
-
Reliable: Have faith in your ability or the ability to honor any promises made.
-
Reasonable - use resources efficiently and don't waste them.
-
Realistic – Consider all aspects, including cost-effectiveness as well as environmental impact.
-
Respectful - Treat people fairly and equitably
-
You are resourceful and look for ways to save money while increasing productivity.
-
Recognizable - Provide value-added services to customers
Statistics
- In 2021, an estimated 12.1 million Americans work in the manufacturing sector.6 (investopedia.com)
- It's estimated that 10.8% of the U.S. GDP in 2020 was contributed to manufacturing. (investopedia.com)
- (2:04) MTO is a production technique wherein products are customized according to customer specifications, and production only starts after an order is received. (oracle.com)
- According to the United Nations Industrial Development Organization (UNIDO), China is the top manufacturer worldwide by 2019 output, producing 28.7% of the total global manufacturing output, followed by the United States, Japan, Germany, and India.[52][53] (en.wikipedia.org)
- [54][55] These are the top 50 countries by the total value of manufacturing output in US dollars for its noted year according to World Bank.[56] (en.wikipedia.org)
External Links
How To
How to use the Just-In Time Method in Production
Just-in-time (JIT) is a method that is used to reduce costs and maximize efficiency in business processes. It allows you to get the right amount resources at the right time. This means that only what you use is charged to your account. Frederick Taylor first coined this term while working in the early 1900s as a foreman. He noticed that workers were often paid overtime when they had to work late. He decided to ensure workers have enough time to do their jobs before starting work to improve productivity.
JIT is an acronym that means you need to plan ahead so you don’t waste your money. The entire project should be looked at from start to finish. You need to ensure you have enough resources to tackle any issues that might arise. If you expect problems to arise, you will be able to provide the necessary equipment and personnel to address them. This will ensure that you don't spend more money on things that aren't necessary.
There are different types of JIT methods:
-
Demand-driven: This JIT is where you place regular orders for the parts/materials that are needed for your project. This will allow you to track how much material you have left over after using it. You'll also be able to estimate how long it will take to produce more.
-
Inventory-based : You can stock the materials you need in advance. This allows one to predict how much they will sell.
-
Project-driven: This means that you have enough money to pay for your project. When you know how much you need, you'll purchase the appropriate amount of materials.
-
Resource-based: This is the most common form of JIT. You assign certain resources based off demand. For example, if there is a lot of work coming in, you will have more people assigned to them. You'll have fewer orders if you have fewer.
-
Cost-based: This is similar to resource-based, except that here you're not just concerned about how many people you have but how much each person costs.
-
Price-based: This is similar to cost-based but instead of looking at individual workers' salaries, you look at the total company price.
-
Material-based is an alternative to cost-based. Instead of looking at the total cost in the company, this method focuses on the average amount of raw materials that you consume.
-
Time-based JIT: A variation on resource-based JIT. Instead of focusing solely on the amount each employee costs, focus on how long it takes for the project to be completed.
-
Quality-based JIT: Another variation on resource-based JIT. Instead of worrying about the costs of each employee or how long it takes for something to be made, you should think about how quality your product is.
-
Value-based JIT: This is the latest form of JIT. You don't worry about whether the products work or if they meet customer expectations. Instead, you focus on the added value that you provide to your market.
-
Stock-based: This inventory-based approach focuses on how many items are being produced at any one time. It is used when production goals are met while inventory is kept to a minimum.
-
Just-in time (JIT), planning: This is a combination JIT/supply chain management. It's the process of scheduling delivery of components immediately after they are ordered. It's important because it reduces lead times and increases throughput.