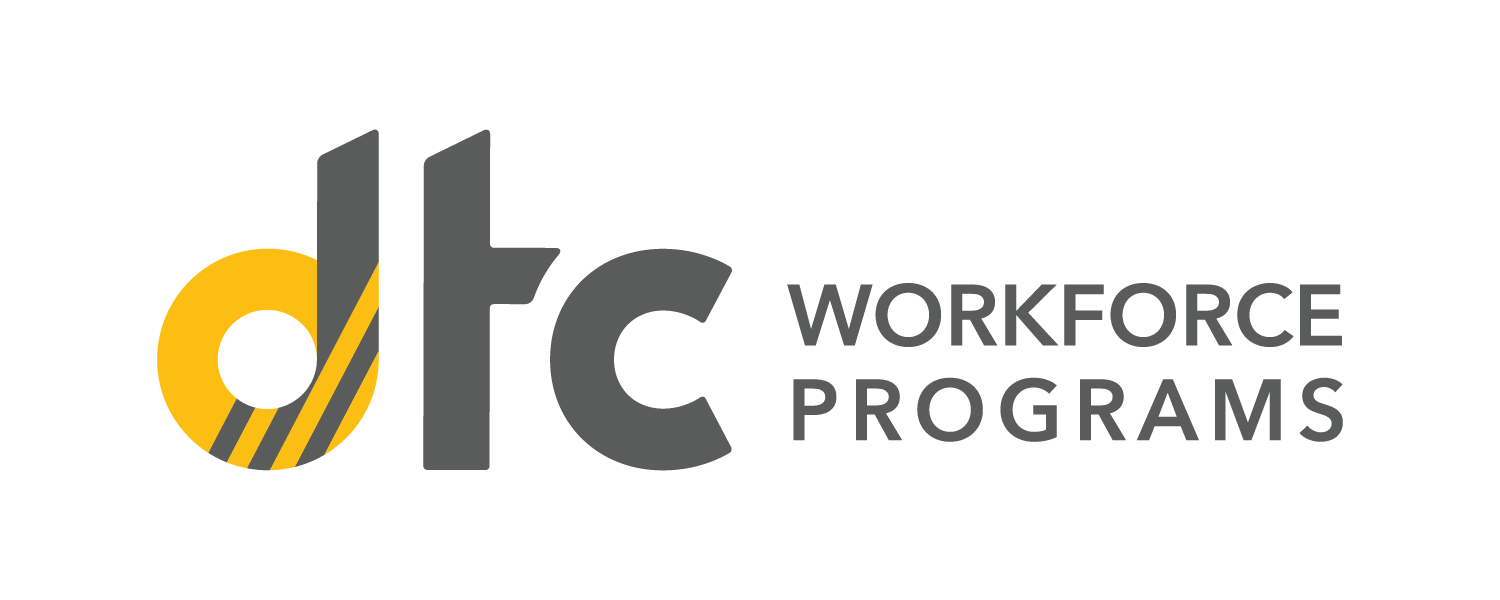
Management of a supply chain requires many aspects. It encompasses both internal processes. Marketing also includes supply chain management. Supply chains are used in almost every industry. The primary function of the supply chains is to deliver products to customers. It is common to deliver products on schedule.
An operations manager is responsible for managing business processes. This includes supervising staffing, hiring and managing equipment. They also oversee production planning. They are tasked with creating a strategy to improve operations. The operations manager has to ensure sufficient inventory for production, budget compliance, and conformance with company specifications. He coordinates with the supply chain manager to ship orders to retailers and consumers.

The operations and supply chain program at UTSA aims to improve your leadership and analytical skills. It's a hands-on program that combines classroom instruction with an experiential learning approach. The program provides training in data analysis, business improvement, and Lean Six Sigma certification. It also gives a complete overview of the supply chain and operations industry. You will also have the opportunity to learn new technologies and apply them to your business.
The supply and operations program focuses on value adding processes. The program equips students to make better business choices. The program employs a variety case studies and industrial examples. It teaches students computer skills and communication skills. This program also offers a minor. The minor complements the major and helps students maximize their supply chain effectiveness. The minor may also be used in Context and Perspectives courses or as an unrestricted elective.
Students have the chance to gain valuable knowledge about operations and supply chain. The program also gives students the opportunity to apply concepts in their own business. You can use it as a steppingstone to other careers, such as marketing, management, and technology. Students can also apply for the Lean Six Sigma greenbelt certification. It provides students with the opportunity to network with industry professionals, learn about new technologies, and keep up to date on current trends.
Students can also gain insight into the manufacturing and supply chain processes through the operations program. It also teaches students to communicate effectively, a skill that is important in both business and management.
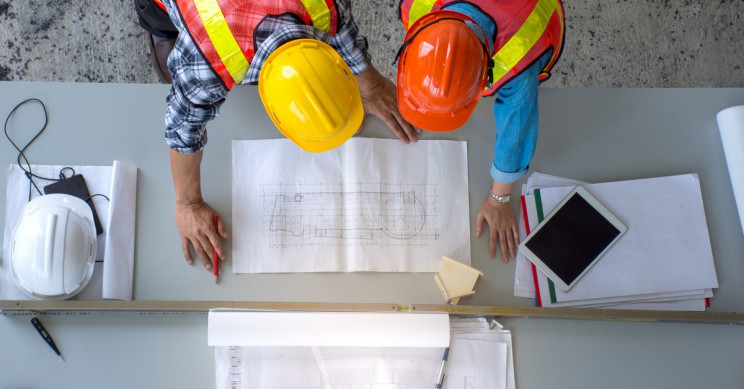
The book is written in a simple and understandable style. It's suitable for students from all backgrounds. In addition to explaining how the supply chain works the book also presents case studies and discusses how to build a supply system. This book also offers quantitative methods of comparing supply to demand. This book also provides information on how to include customers in your supply chain.
FAQ
How does a Production Planner differ from a Project Manager?
The main difference between a production planner and a project manager is that a project manager is usually the person who plans and organizes the entire project, whereas a production planner is mainly involved in the planning stage of the project.
How can I learn about manufacturing?
Experience is the best way for you to learn about manufacturing. But if that is not possible you can always read books and watch educational videos.
What kind of jobs are there in logistics?
There are different kinds of jobs available in logistics. Some examples are:
-
Warehouse workers - They load and unload trucks and pallets.
-
Transportation drivers: They drive trucks and trailers and deliver goods and make pick-ups.
-
Freight handlers - They sort and pack freight in warehouses.
-
Inventory managers - These are responsible for overseeing the stock of goods in warehouses.
-
Sales reps are people who sell products to customers.
-
Logistics coordinators - They plan and organize logistics operations.
-
Purchasing agents: They are responsible for purchasing goods and services to support company operations.
-
Customer service representatives - Answer calls and email from customers.
-
Shippers clerks - They process shipping order and issue bills.
-
Order fillers are people who fill orders based only on what was ordered.
-
Quality control inspectors are responsible for inspecting incoming and outgoing products looking for defects.
-
Other - Logistics has many other job opportunities, including transportation supervisors, logistics specialists, and cargo specialists.
What is the role of a logistics manager
A logistics manager makes sure that all goods are delivered on-time and in good condition. This is achieved by using their knowledge and experience with the products of the company. He/she also needs to ensure adequate stock to meet demand.
What skills should a production planner have?
To become a successful production planner, you need to be organized, flexible, and able to multitask. Communication skills are essential to ensure that you can communicate effectively with clients, colleagues, and customers.
How can manufacturing avoid production bottlenecks
You can avoid bottlenecks in production by making sure that everything runs smoothly throughout the production cycle, from the moment you receive an order to the moment the product is shipped.
This includes planning to meet capacity requirements and quality control.
Continuous improvement techniques like Six Sigma are the best way to achieve this.
Six Sigma Management System is a method to increase quality and reduce waste throughout your organization.
It seeks to eliminate variation and create consistency in your work.
Is there anything we should know about Manufacturing Processes prior to learning about Logistics.
No. It doesn't matter if you don't know anything about manufacturing before you learn about logistics. It is important to know about the manufacturing processes in order to understand how logistics works.
Statistics
- [54][55] These are the top 50 countries by the total value of manufacturing output in US dollars for its noted year according to World Bank.[56] (en.wikipedia.org)
- Job #1 is delivering the ordered product according to specifications: color, size, brand, and quantity. (netsuite.com)
- In the United States, for example, manufacturing makes up 15% of the economic output. (twi-global.com)
- According to the United Nations Industrial Development Organization (UNIDO), China is the top manufacturer worldwide by 2019 output, producing 28.7% of the total global manufacturing output, followed by the United States, Japan, Germany, and India.[52][53] (en.wikipedia.org)
- It's estimated that 10.8% of the U.S. GDP in 2020 was contributed to manufacturing. (investopedia.com)
External Links
How To
Six Sigma and Manufacturing
Six Sigma is defined by "the application SPC (statistical process control) techniques to achieve continuous improvements." Motorola's Quality Improvement Department in Tokyo, Japan developed Six Sigma in 1986. Six Sigma is a method to improve quality through standardization and elimination of defects. Many companies have adopted Six Sigma in recent years because they believe that there are no perfect products and services. Six Sigma aims to reduce variation in the production's mean value. This means that if you take a sample of your product, then measure its performance against the average, you can find out what percentage of the time the process deviates from the norm. If there is a significant deviation from the norm, you will know that something needs to change.
Understanding how variability works in your company is the first step to Six Sigma. Once you understand that, it is time to identify the sources of variation. You'll also want to determine whether these variations are random or systematic. Random variations occur when people do mistakes. Symmetrical variations are caused due to factors beyond the process. For example, if you're making widgets, and some of them fall off the assembly line, those would be considered random variations. You might notice that your widgets always fall apart at the same place every time you put them together.
Once you identify the problem areas, it is time to create solutions. It might mean changing the way you do business or redesigning it entirely. You should then test the changes again after they have been implemented. If they don't work you need to rework them and come up a better plan.