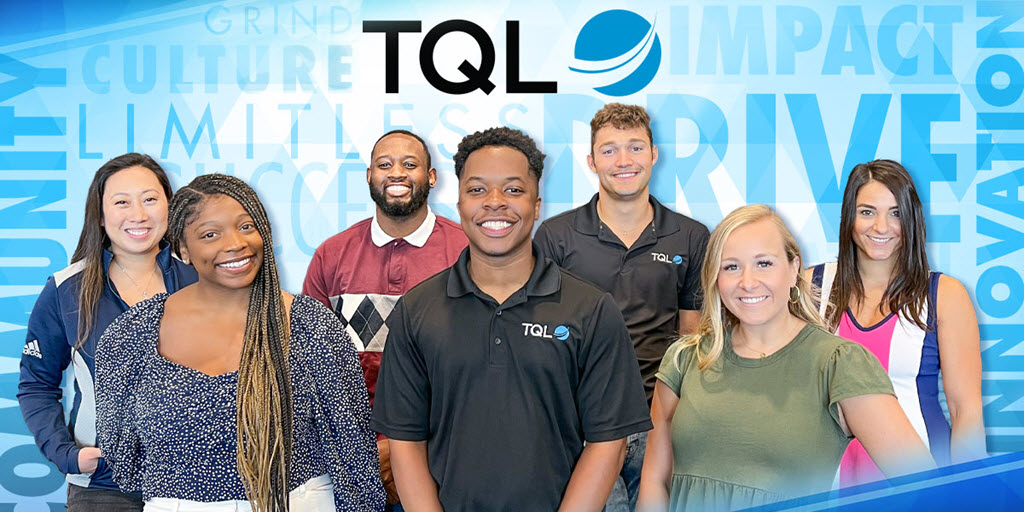
For industrial engineers, you will need strong math skills, knowledge of physical science and the ability to solve problems. These people can work in various sectors, such as manufacturing and construction. They could be found in offices or on the production floor.
Industrial engineers study production processes and develop manufacturing techniques to improve efficiency. They can also design quality control procedures. They may also be responsible for creating manufacturing standards and training staff. Those who are interested in becoming industrial engineers should be willing to work with others. They should be driven to improve efficiency and streamline their processes. They should possess excellent leadership and communication skills and be adept at solving problems.
Industrial engineers can create cost analysis tools and help robots run more efficiently. They analyze data to determine if processes are efficient or not. They can also design and develop standards for manufacturing and will ensure that safety standards are adhered to. They may also design procedures for equipment and inventory management, as well as create documentation. They might also present their plans via oral presentations or written reports.
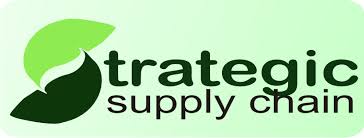
Industrial engineers can work in factories, offices, or warehouses. They may also travel to their clients' sites. They may be required to work in noisy and cramped areas. They may need to wear safety clothing. Sometimes they will need to work more than normal in order to meet production deadlines.
The job of industrial engineers is to design and implement processes and ensure they run efficiently and produce quality products. They can also help solve production problems. Some industrial engineers also start manufacturing companies. They may have to train new workers and make sure that they know how to do their jobs properly. They may also have the responsibility of ensuring that raw materials meet certain quality standards before they can be used in manufacturing.
Industrial engineers are part of other departments that create integrated systems to manage industrial production. They may also specialize within a specific engineering field. They might be required to work in a noisy and cramped environment. They may be required to travel to factories or other construction sites in order to collect data.
An education or work experience can help industrial engineers move up to managerial positions. They could also set up their own consulting businesses or become specialists in a certain area. They may also specialize in quality control procedures or facility planning. They could also be responsible in designing production layouts. They may also be responsible for developing wage and salary administration systems. They may also be responsible scheduling deliveries based in production forecasts, storage, handling, and maintenance requirements. They might also be required to travel to other locations and carry out administrative tasks. They can also supervise technicians.
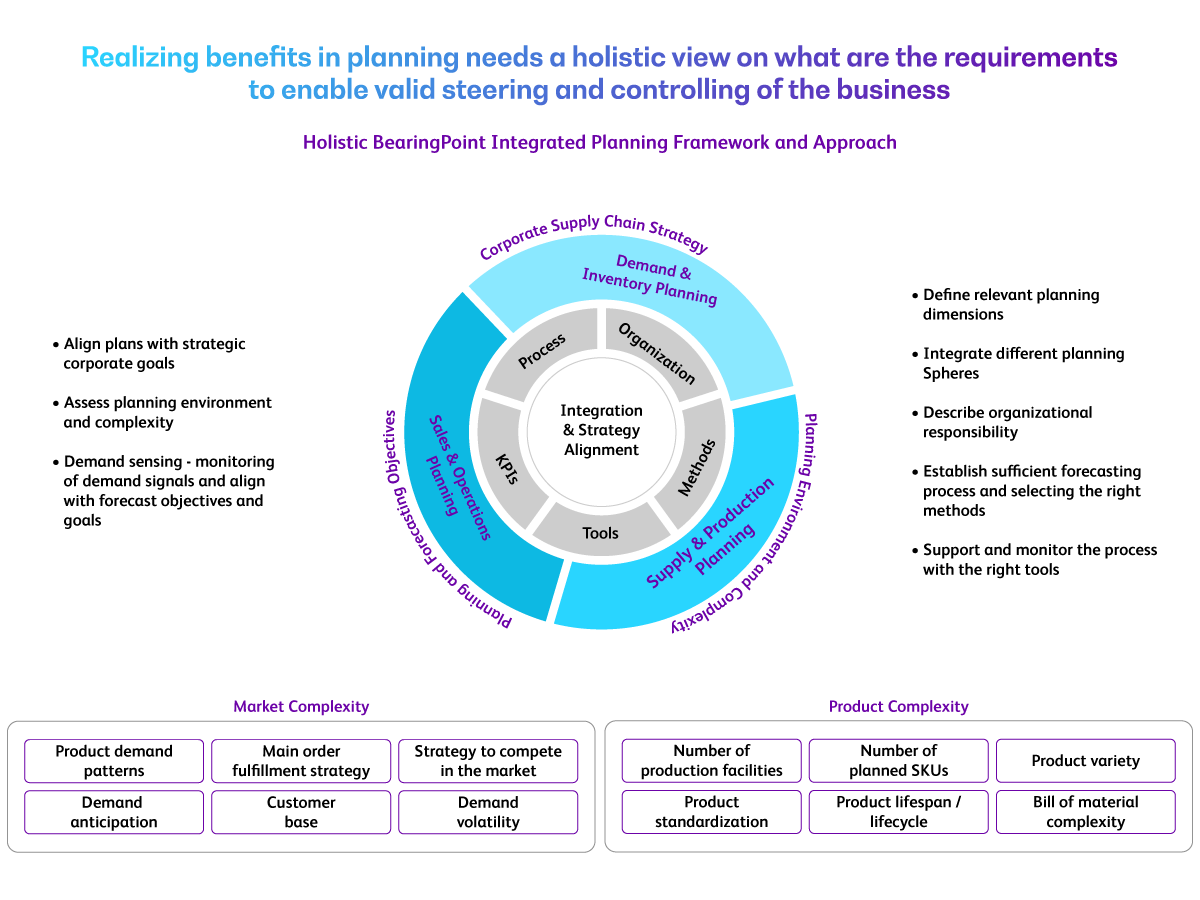
Industrial engineers might work for a company or as consultants. They may work a standard 40-hour work week or more, depending on the company's needs. If they provide technical support to a company, they may work longer than 40 hours.
FAQ
What is the role and responsibility of a Production Planner?
Production planners ensure all aspects of the project are delivered within time and budget. They make sure that the product and services meet client expectations.
What are the 7 Rs of logistics?
The acronym 7R's for Logistics stands to represent the seven basic principles in logistics management. It was published in 2004 by the International Association of Business Logisticians as part of their "Seven Principles of Logistics Management" series.
The acronym consists of the following letters:
-
Responsible – ensure that all actions are legal and don't cause harm to anyone else.
-
Reliable - have confidence in the ability to deliver on commitments made.
-
Be responsible - Use resources efficiently and avoid wasting them.
-
Realistic - Consider all aspects of operations, including environmental impact and cost effectiveness.
-
Respectful - show respect and treat others fairly and fairly
-
Responsive - Look for ways to save time and increase productivity.
-
Recognizable - Provide value-added services to customers
What are manufacturing and logistic?
Manufacturing is the process of creating goods from raw materials by using machines and processes. Logistics is the management of all aspects of supply chain activities, including procurement, production planning, distribution, warehousing, inventory control, transportation, and customer service. Manufacturing and logistics can often be grouped together to describe a larger term that covers both the creation of products, and the delivery of them to customers.
What are the four types of manufacturing?
Manufacturing refers to the transformation of raw materials into useful products by using machines and processes. Manufacturing involves many activities, including designing, building, testing and packaging, shipping, selling, service, and so on.
What skills is required for a production planner?
A production planner must be organized, flexible, and able multitask to succeed. Also, you must be able and willing to communicate with clients and coworkers.
Why is logistics important in manufacturing
Logistics are essential to any business. They can help you achieve great success by helping you manage product flow from raw material to finished goods.
Logistics play an important role in reducing costs as well as increasing efficiency.
Statistics
- You can multiply the result by 100 to get the total percent of monthly overhead. (investopedia.com)
- According to the United Nations Industrial Development Organization (UNIDO), China is the top manufacturer worldwide by 2019 output, producing 28.7% of the total global manufacturing output, followed by the United States, Japan, Germany, and India.[52][53] (en.wikipedia.org)
- Many factories witnessed a 30% increase in output due to the shift to electric motors. (en.wikipedia.org)
- Job #1 is delivering the ordered product according to specifications: color, size, brand, and quantity. (netsuite.com)
- [54][55] These are the top 50 countries by the total value of manufacturing output in US dollars for its noted year according to World Bank.[56] (en.wikipedia.org)
External Links
How To
How to Use the Just In Time Method in Production
Just-in time (JIT), is a process that reduces costs and increases efficiency in business operations. This is where you have the right resources at the right time. This means that only what you use is charged to your account. Frederick Taylor, a 1900s foreman, first coined the term. Taylor observed that overtime was paid to workers if they were late in working. He decided that workers would be more productive if they had enough time to complete their work before they started to work.
JIT is an acronym that means you need to plan ahead so you don’t waste your money. Also, you should look at the whole project from start-to-finish and make sure you have the resources necessary to address any issues. You can anticipate problems and have enough equipment and people available to fix them. You won't have to pay more for unnecessary items.
There are different types of JIT methods:
-
Demand-driven: This is a type of JIT where you order the parts/materials needed for your project regularly. This will allow you to track how much material you have left over after using it. You'll also be able to estimate how long it will take to produce more.
-
Inventory-based: This is a type where you stock the materials required for your projects in advance. This allows for you to anticipate how much you can sell.
-
Project-driven : This is a method where you make sure that enough money is set aside to pay the project's cost. Knowing how much money you have available will help you purchase the correct amount of materials.
-
Resource-based JIT: This type of JIT is most commonly used. You assign certain resources based off demand. You might assign more people to help with orders if there are many. If there aren't many orders, you will assign fewer people.
-
Cost-based: This is the same as resource-based except that you don't care how many people there are but how much each one of them costs.
-
Price-based pricing: This is similar in concept to cost-based but instead you look at how much each worker costs, it looks at the overall company's price.
-
Material-based: This is quite similar to cost-based, but instead of looking at the total cost of the company, you're concerned with how much raw materials you spend on average.
-
Time-based JIT: A variation on resource-based JIT. Instead of focusing on the cost of each employee, you will focus on the time it takes to complete a project.
-
Quality-based JIT is another variant of resource-based JIT. Instead of worrying about the costs of each employee or how long it takes for something to be made, you should think about how quality your product is.
-
Value-based JIT: One of the most recent forms of JIT. You don't worry about whether the products work or if they meet customer expectations. Instead, your goal is to add value to the market.
-
Stock-based: This inventory-based approach focuses on how many items are being produced at any one time. This method is useful when you want to increase production while decreasing inventory.
-
Just-in-time planning (JIT): This is a combination JIT and supply-chain management. This refers to the scheduling of the delivery of components as soon after they are ordered. It reduces lead times and improves throughput.