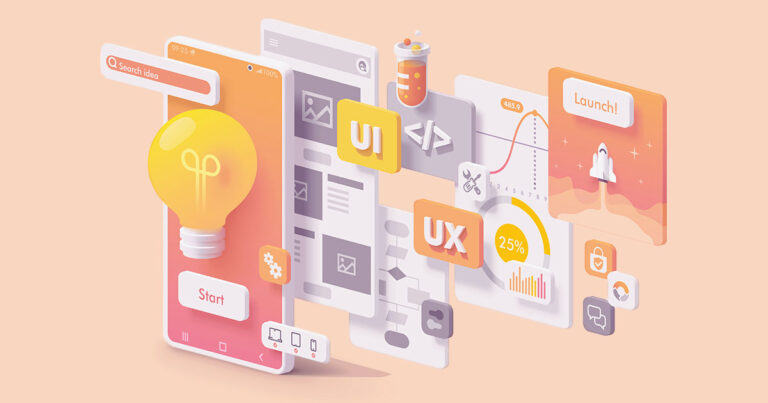
If you're looking to a career with chemistry, you might be curious as to what a salary for a chemical chemist. Below is an explanation of what the various degrees earn and an average chemist's salary. A bachelor's in chemistry can lead to a salary of $50,000 to more than a hundred thousand dollars. You can earn between fifty thousand and more than a million dollars annually depending on where you live, what degree you have, and which employer you work for.
Average chemist salary
According to Bureau of Labor Statistics, an average starting chemistry salary of $81,870 is per year. The highest-paid chemists make more than $130,000 per year. The lowest-paid chemists make around $42,960 annually. Pharmacist and medicine manufacturing companies are the most common places for chemists. The oil and gas industry offers the highest starting chemistry salary. The Bureau of Labor Statistics projects a 7 per cent increase in chemist positions over the next decade. Higher salaries are available for graduates with lab experience than for those without.
The average chemistry salary will vary depending on your experience and where you are located. The salary for a chemist will vary depending on the level of education, experience and additional skills. A California-based chemist who is experienced can earn an annual salary of $85,114. Salary ranges are different in other states. A PhD is a great way to increase your income if you are a chemist.

Bachelor's degree chemists can expect a range of salaries
A chemistry degree can help you find a job in many different industries. The Bureau of Labor Statistics reported that the United States had around 82,000 chemical professionals in 2010. Though a bachelor's degree is usually enough to secure a chemistry-related job, a graduate degree can lead to higher income and more responsibility. According to the American Chemical Society, a chemist's median salary was $40,000 in 2011, but the starting salary for a Ph.D. is about $85,000.
A chemistry-related career can be lucrative, but salary isn't the only factor to consider. A Ph.D. degree in chemistry can lead to a salary of upwards of $60,000 but this will depend on how experienced you are and what job you have. As a rule, the best-paid chemists work for the federal governments, research universities, or teaching.
Salary range for chemists with master's degree
A chemistry master's degree could earn you as much as 128,000 USD per annum. Salary ranges differ greatly for this profession, though they are often close to the median. For a graduate with less than two years of work experience, you can expect to make around 40 thousand euros. An experienced chemist can make as much as 239,000 USD per year if they have more than ten-years of experience.
Many chemistry positions require a master's degree or Ph.D., though they can be obtained with a bachelor's degree. Graduates may specialize in one subfield. According to American Chemical Society (ACS), the median starting pay for a chemist holding a bachelor's was $43,000. For those who worked in companies with over 25,000 employees, the salary was $50,000.
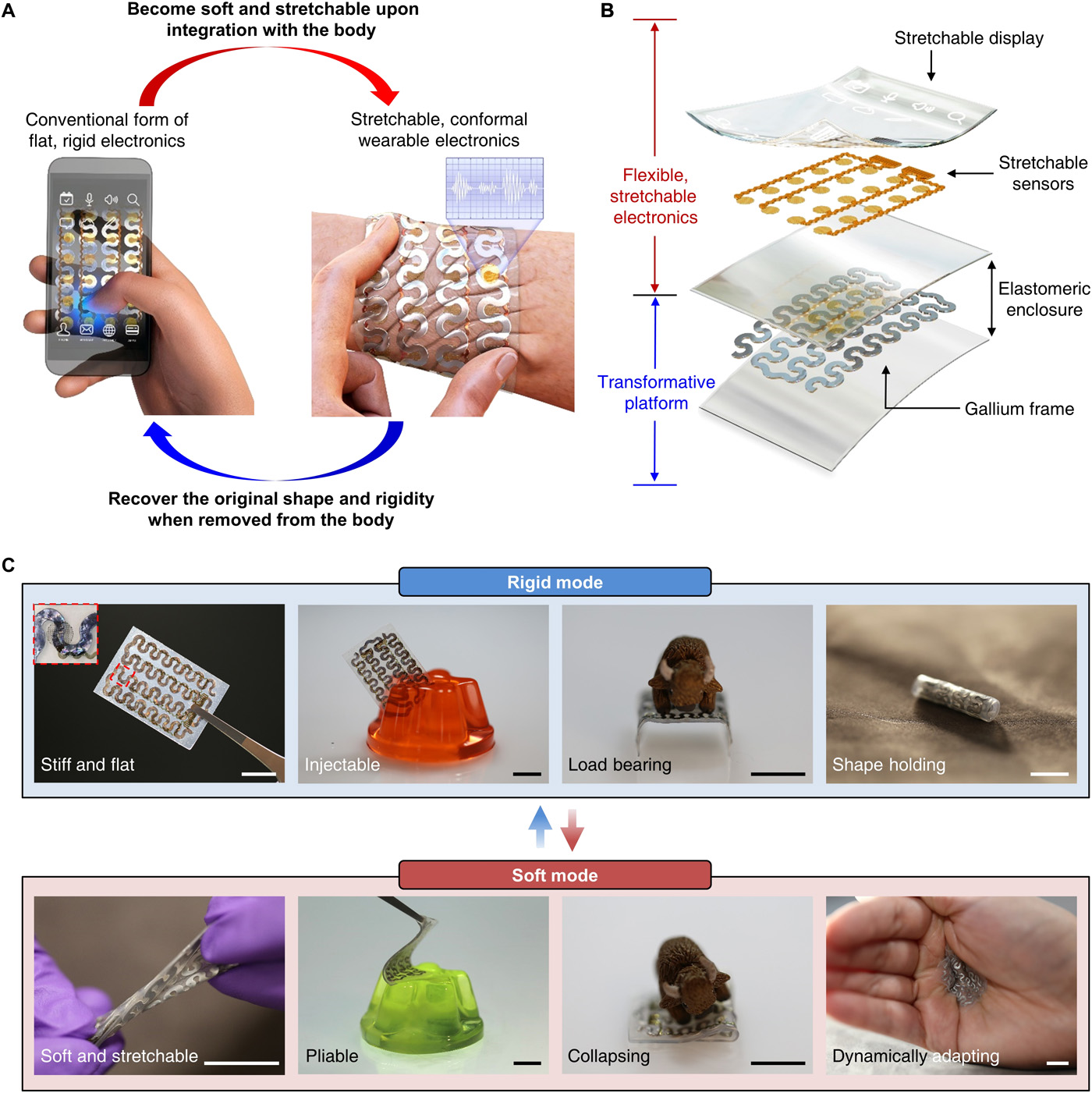
A range of salaries for chemists holding a Ph.D.
The salary for a PhD chemist depends on their work experience as well as the location and job that they apply for. For example, the average salary for scientists in Germany is 40,400 Euros per year in small firms. Salaries in large companies can reach up to 50,000 euros. However, scientists will be paid in accordance with the collective wage agreements.
The U.S. has a lot of chemists, and they make a great living. However, they also have responsibilities in education or research. University professors typically work on government-funded and private-industry-funded projects. This field is also available for secondary school teachers. According to American Chemical Society, a bachelor's-level chemist earns around $40,000 per annum, while a master's-level chemist earns around $46,000 per annum. A Ph.D. in Chemistry earned an average salary of $85,000 in 2011.
FAQ
What is production plan?
Production Planning is the creation of a plan to cover all aspects, such as scheduling, budgeting. Location, crew, equipment, props and other details. It is important to have everything ready and planned before you start shooting. This document should also include information on how to get the best result on set. It should include information about shooting locations, casting lists, crew details, equipment requirements, and shooting schedules.
The first step is to outline what you want to film. You may have already decided where you would like to shoot, or maybe there are specific locations or sets that you want to use. Once you have identified your locations and scenes it's time to begin figuring out what elements you will need for each one. You might decide you need a car, but not sure what make or model. In this case, you could start looking up cars online to find out what models are available and then narrow your choices by choosing between different makes and models.
After you have selected the car you want, you can begin to think about additional features. You might need to have people in the front seats. Or maybe you just need someone to push the car around. Perhaps you would like to change the interior colour from black to white. These questions can help you decide the right look for your car. It is also worth considering the types of shots that you wish to take. Will you be filming close-ups or wide angles? Maybe you want to show your engine or the steering wheel. This will allow you to determine the type of car you want.
Once you have determined all of the above, you can move on to creating a schedule. The schedule will show you when to begin shooting and when to stop. Each day will include the time when you need to arrive at the location, when you need to leave and when you need to return home. Everyone knows exactly what they should do and when. Book extra staff ahead of time if you need them. It's not worth paying someone to show up if you haven't told him.
You will need to factor in the days that you have to film when creating your schedule. Some projects only take one or two days, while others may last weeks. While creating your schedule, it is important to remember whether you will require more than one shot per day. Multiple takes at the same place will result in higher costs and longer completion times. If you are unsure if you need multiple takes, it is better to err on the side of caution and shoot fewer takes rather than risk wasting money.
Budgeting is another important aspect of production planning. It is important to set a realistic budget so you can work within your budget. You can always lower the budget if you encounter unexpected problems. However, it is important not to overestimate the amount that you will spend. You will end up spending less money if you underestimate the cost of something.
Production planning is a detailed process. But, once you understand the workings of everything, it becomes easier for future projects to be planned.
Why is logistics important in manufacturing
Logistics is an integral part of every business. They help you achieve great results by helping you manage all aspects of product flow, from raw materials to finished goods.
Logistics play a key role in reducing expenses and increasing efficiency.
What is meant by manufacturing industries?
Manufacturing Industries refers to businesses that manufacture products. These products are sold to consumers. These companies employ many processes to achieve this purpose, such as production and distribution, retailing, management and so on. They manufacture goods from raw materials using machines and other equipment. This covers all types of manufactured goods including clothing, food, building supplies and furniture, as well as electronics, tools, machinery, vehicles and pharmaceuticals.
What is the job of a manufacturer manager?
Manufacturing managers must ensure that manufacturing processes are efficient, effective, and cost-effective. They should also be aware and responsive to any company problems.
They should also know how to communicate with other departments such as sales and marketing.
They should be informed about industry trends and be able make use of this information to improve their productivity and efficiency.
Statistics
- Job #1 is delivering the ordered product according to specifications: color, size, brand, and quantity. (netsuite.com)
- According to the United Nations Industrial Development Organization (UNIDO), China is the top manufacturer worldwide by 2019 output, producing 28.7% of the total global manufacturing output, followed by the United States, Japan, Germany, and India.[52][53] (en.wikipedia.org)
- (2:04) MTO is a production technique wherein products are customized according to customer specifications, and production only starts after an order is received. (oracle.com)
- Many factories witnessed a 30% increase in output due to the shift to electric motors. (en.wikipedia.org)
- [54][55] These are the top 50 countries by the total value of manufacturing output in US dollars for its noted year according to World Bank.[56] (en.wikipedia.org)
External Links
How To
How to Use the 5S to Increase Productivity In Manufacturing
5S stands as "Sort", Set In Order", Standardize", Separate" and "Store". Toyota Motor Corporation invented the 5S strategy in 1954. It assists companies in improving their work environments and achieving higher efficiency.
The basic idea behind this method is to standardize production processes, so they become repeatable, measurable, and predictable. This means that every day tasks such cleaning, sorting/storing, packing, and labeling can be performed. This knowledge allows workers to be more efficient in their work because they are aware of what to expect.
Implementing 5S requires five steps. These are Sort, Set In Order, Standardize. Separate. And Store. Each step involves a different action which leads to increased efficiency. If you sort items, it makes them easier to find later. You arrange items by placing them in an order. Then, after you separate your inventory into groups, you store those groups in containers that are easy to access. Finally, when you label your containers, you ensure everything is labeled correctly.
This process requires employees to think critically about how they do their job. Employees need to be able understand their motivations and discover alternative ways to do them. In order to use the 5S system effectively, they must be able to learn new skills.
The 5S method increases efficiency and morale among employees. They will feel motivated to strive for higher levels of efficiency once they start to see results.