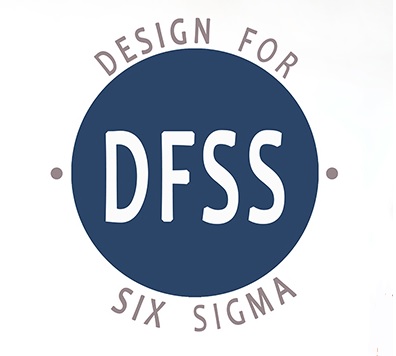
Understanding the five s’s of lean manufacturing is essential if you want to transform your manufacturing processes into a lean machine. These are Standardize. Here are some steps that you should take. Your lean transformation will be maximized if you train your frontline employees and team leaders.
Standardize
Clean and organize your workspace is the first step in the 5S process. While this may seem like an insignificant task at first, standardizing the process can make it easier. To ensure a consistent approach to 5S tasks, you can use visual cues, checklist templates, and checklists.
You can make your workplace more productive by using the five s's. This approach will encourage employees to be organized and help them do their jobs efficiently. A clean and well-organized work environment will improve efficiency. You can improve safety in your workplace by using the five s’s of lean. A well-organized space will prevent accidents, minimize mistakes and increase the chance of producing productive work.
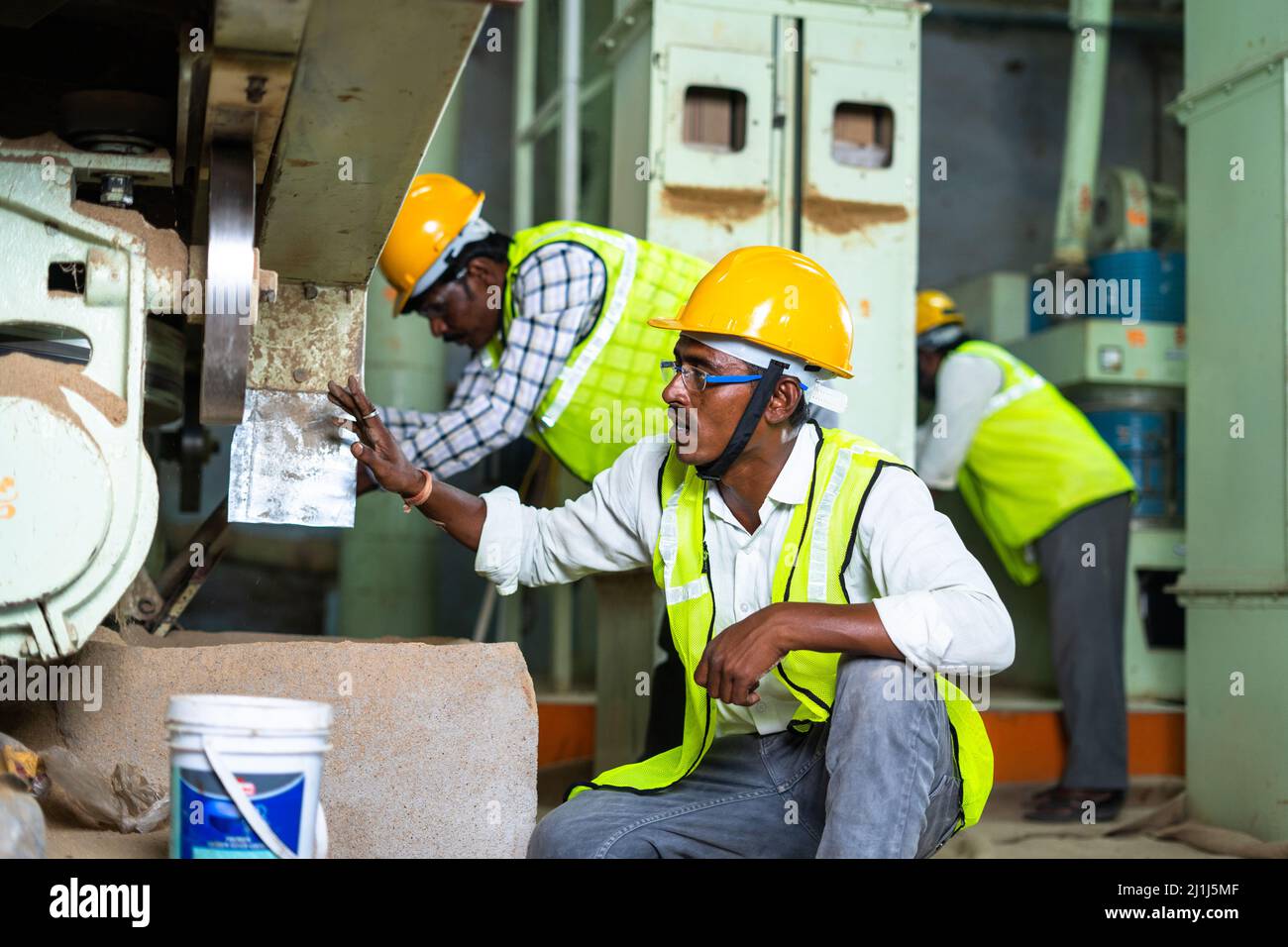
Straighten
Your 5 s's can be done easily. Companies can improve their business processes and practice lean principles consistently. Workers will find the parts they need easier if the assembly lines are organized. This will reduce time spent searching for missing parts and increase safety and efficiency in the company's workflow.
You can also reduce the amount of items that are in each work area and save money on consumables. This can significantly cut down on your office supply expenses. Straightening work cells can not only help you save money, but it will also improve your production processes and increase quality, safety, standard work, and efficiency.
Shine
Shine involves inspecting and identifying problems in the workspace. Shine is a process that examines equipment and tools to improve flow and reduce waste. Shine can improve the maintenance of a workspace. It allows workers to spot potential problems before they hinder production. Shine helps improve productivity by standardizing the layout.
Shine is one of the 5S tools used in lean manufacturing. This technique streamlines and automates work processes to reduce waste and increase efficiency. It can be used in all industries, including manufacturing. This applies the 5S principles throughout a company. It assists companies in reducing inventory, work-in progress, and stock.
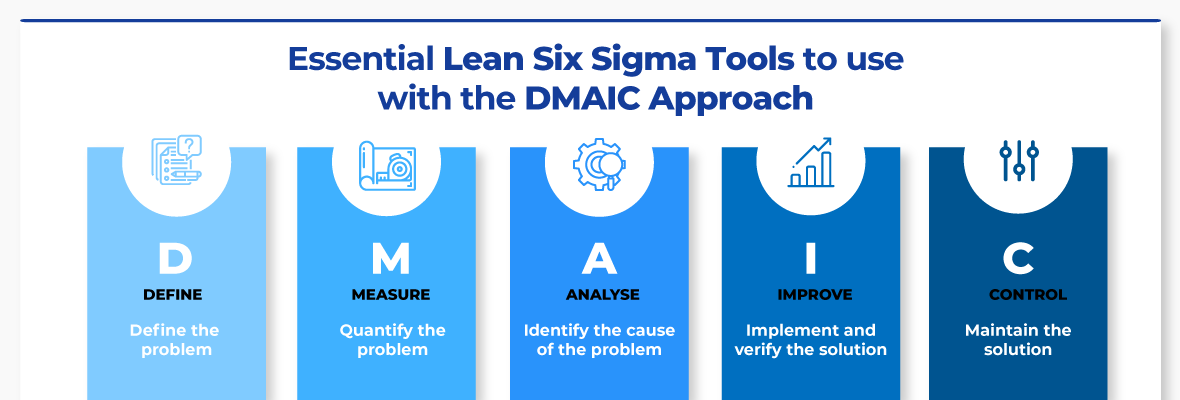
Continue to Sustain
The 5 s's are about introducing a standardized system to a facility in order to maintain the 5S. This is a process that is meant to be continuous and should be repeated often to ensure the facility works at its best. Employees should be trained to conduct 5S audits.
The 5S approach focuses on reducing waste and optimizing productivity while maintaining a clean and orderly workplace. The five principles of Toyota Production System are applied to it. It's a system that organizes workplaces. Hiroyuki Hirano designed it to increase the efficiency of manufacturing plants in Japan after World War II.
FAQ
What are the 7 Rs of logistics?
The acronym 7R's of Logistic is an acronym that stands for seven fundamental principles of logistics management. It was developed and published by the International Association of Business Logisticians in 2004 as part of the "Seven Principles of Logistics Management".
The acronym is composed of the following letters.
-
Responsible - ensure that all actions taken are within legal requirements and are not harmful to others.
-
Reliable - have confidence in the ability to deliver on commitments made.
-
Use resources effectively and sparingly.
-
Realistic - consider all aspects of operations, including cost-effectiveness and environmental impact.
-
Respectful – Treat others fairly and equitably.
-
Reliable - Find ways to save money and increase your productivity.
-
Recognizable - provide customers with value-added services.
What are the logistics products?
Logistics is the process of moving goods from one point to another.
They include all aspects of transport, including packaging, loading, transporting, unloading, storing, warehousing, inventory management, customer service, distribution, returns, and recycling.
Logisticians ensure the product reaches its destination in the most efficient manner. They provide information on demand forecasts as well stock levels, production schedules and availability of raw material.
They can also track shipments in transit and monitor quality standards.
What is the job of a logistics manger?
A logistics manager makes sure that all goods are delivered on-time and in good condition. This is done by using his/her experience and knowledge of the company's products. He/she should also ensure enough stock is available to meet demand.
Is it necessary to be familiar with Manufacturing Processes before we learn about Logistics.
No. No. It is important to know about the manufacturing processes in order to understand how logistics works.
What are manufacturing & logistics?
Manufacturing is the act of producing goods from raw materials using machines and processes. Logistics is the management of all aspects of supply chain activities, including procurement, production planning, distribution, warehousing, inventory control, transportation, and customer service. Manufacturing and logistics can often be grouped together to describe a larger term that covers both the creation of products, and the delivery of them to customers.
Are there ways to automate parts of manufacturing?
Yes! Yes! Automation has existed since ancient times. The Egyptians discovered the wheel thousands and years ago. Robots are now used to assist us in assembly lines.
In fact, there are several applications of robotics in manufacturing today. These include:
-
Robots for assembly line
-
Robot welding
-
Robot painting
-
Robotics inspection
-
Robots that produce products
Automation can be applied to manufacturing in many other ways. 3D printing makes it possible to produce custom products in a matter of days or weeks.
Statistics
- Job #1 is delivering the ordered product according to specifications: color, size, brand, and quantity. (netsuite.com)
- Many factories witnessed a 30% increase in output due to the shift to electric motors. (en.wikipedia.org)
- (2:04) MTO is a production technique wherein products are customized according to customer specifications, and production only starts after an order is received. (oracle.com)
- You can multiply the result by 100 to get the total percent of monthly overhead. (investopedia.com)
- [54][55] These are the top 50 countries by the total value of manufacturing output in US dollars for its noted year according to World Bank.[56] (en.wikipedia.org)
External Links
How To
How to use 5S in Manufacturing to Increase Productivity
5S stands to stand for "Sort", “Set In Order", “Standardize", and "Store". Toyota Motor Corporation invented the 5S strategy in 1954. It assists companies in improving their work environments and achieving higher efficiency.
The idea behind standardizing production processes is to make them repeatable and measurable. This means that every day tasks such cleaning, sorting/storing, packing, and labeling can be performed. This knowledge allows workers to be more efficient in their work because they are aware of what to expect.
Five steps are required to implement 5S: Sort, Set In Order, Standardize. Separate. Each step has a different action and leads to higher efficiency. You can make it easy for people to find things later by sorting them. When you set items in an order, you put items together. Once you have separated your inventory into groups and organized them, you will store these groups in easily accessible containers. Make sure everything is correctly labeled when you label your containers.
This requires employees to critically evaluate how they work. Employees must be able to see why they do what they do and find a way to achieve them without having to rely on their old methods. They will need to develop new skills and techniques in order for the 5S system to be implemented.
In addition to increasing efficiency, the 5S method also improves morale and teamwork among employees. As they begin to see improvements, they feel motivated to continue working towards the goal of achieving higher levels of efficiency.