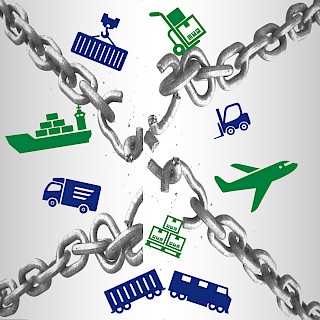
Lean service is a method that applies lean manufacturing production techniques in the service sector. Companies that have adopted this approach to their production processes include health care providers in the US and HMRC in the UK. Lean services aim to reduce waste, improve customer satisfaction and lower costs. Whether you're a small startup or a global giant, lean services can improve your business.
Lean manufacturing
Lean manufacturing is an approach to eliminating waste. This process can help businesses improve their overall productivity and reduce operating costs. It also increases employee satisfaction. Ultimately, it can increase profits. It can reduce the time it takes to produce a product, and increase profits. With lean manufacturing services, companies can expand their customer base as well as increase their revenue streams.
Lean manufacturing takes a team approach, and a lot of talent. It is important that everyone on the team understands the process and how it works. It is important that they are able to adapt practices to fit the organizational needs. To simplify manufacturing processes is the first step towards lean manufacturing. Complex manufacturing processes are difficult to spot waste and inefficiencies. This simplifies the process and creates a culture of continuous improvement. This will allow your employees the freedom to search for inefficiencies.
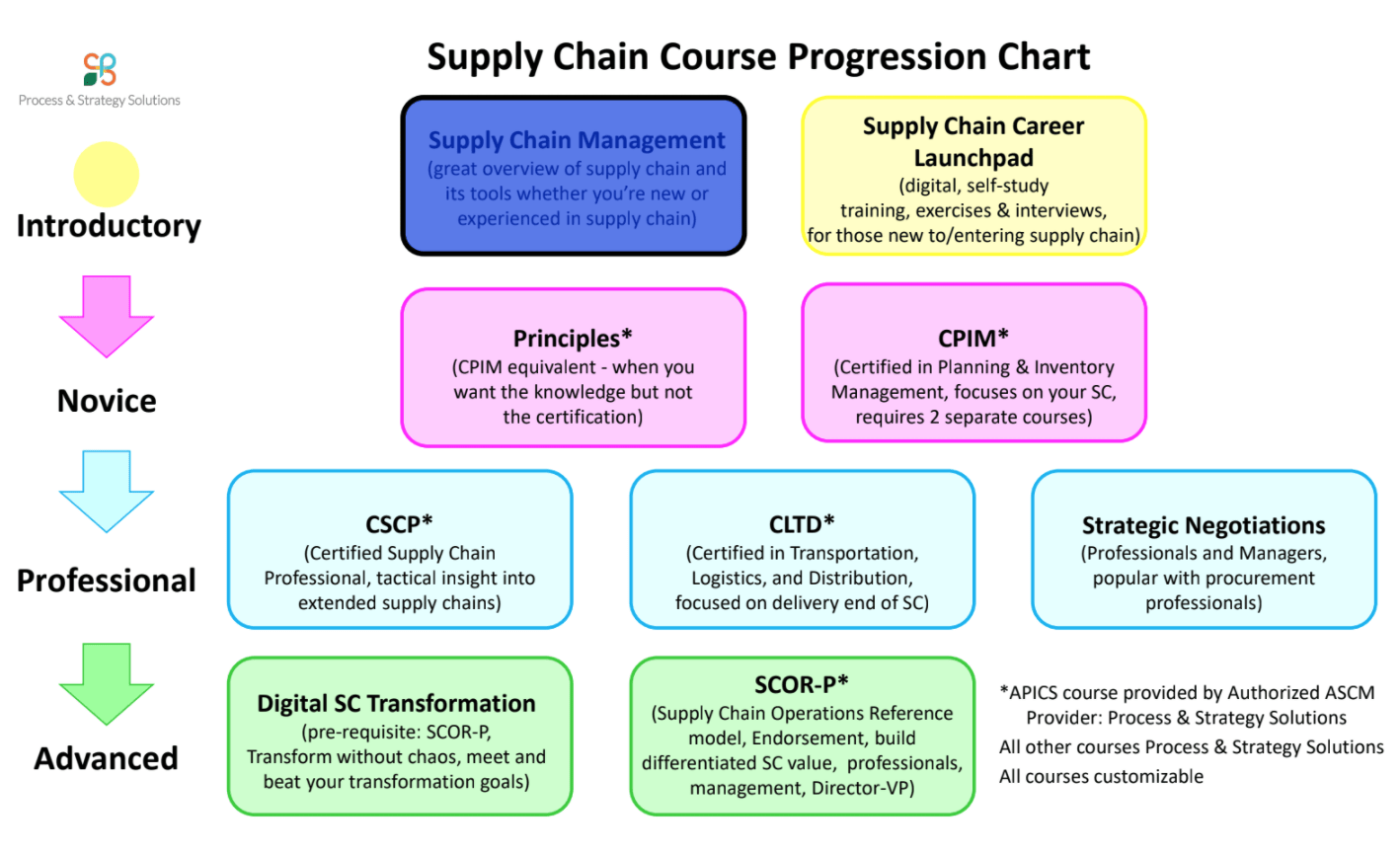
Companies can improve their efficiency and reduce their lead times by using lean manufacturing services. MXGlobal is one such company that provides lean implementation and has successfully consulted Japanese companies with a U.S. presence. Lean manufacturing services offered by the firm are designed to help businesses expand internationally and reach their business goals.
Lean manufacturing services help businesses create an environment that will maximize profits. They help businesses reduce waste and improve productivity. There are eight types. These include overproduction, inventory, transport, and defects. These wastes may increase customer satisfaction and cost more.
Lean operations management
Lean operations management is a process that enables organizations to identify their goals and objectives. This is a method that creates value for the customer. The value of a product or service is what consumers demand. It drives sales. To get started, consider mapping all steps in the creation of a product or service and ask, "What adds value to the customer?"
The goal of a lean management system is to continually improve your processes. Continuous improvement is the key to this system. It ensures that your team always delivers work assignments in less time and with less effort. In addition, this method reduces waste from production processes, and optimizes overhead and storage costs. The four principles of Lean Management include continuous improvement and minimization, minimizing waste, reducing cycles time, and ensuring continuous workflows.
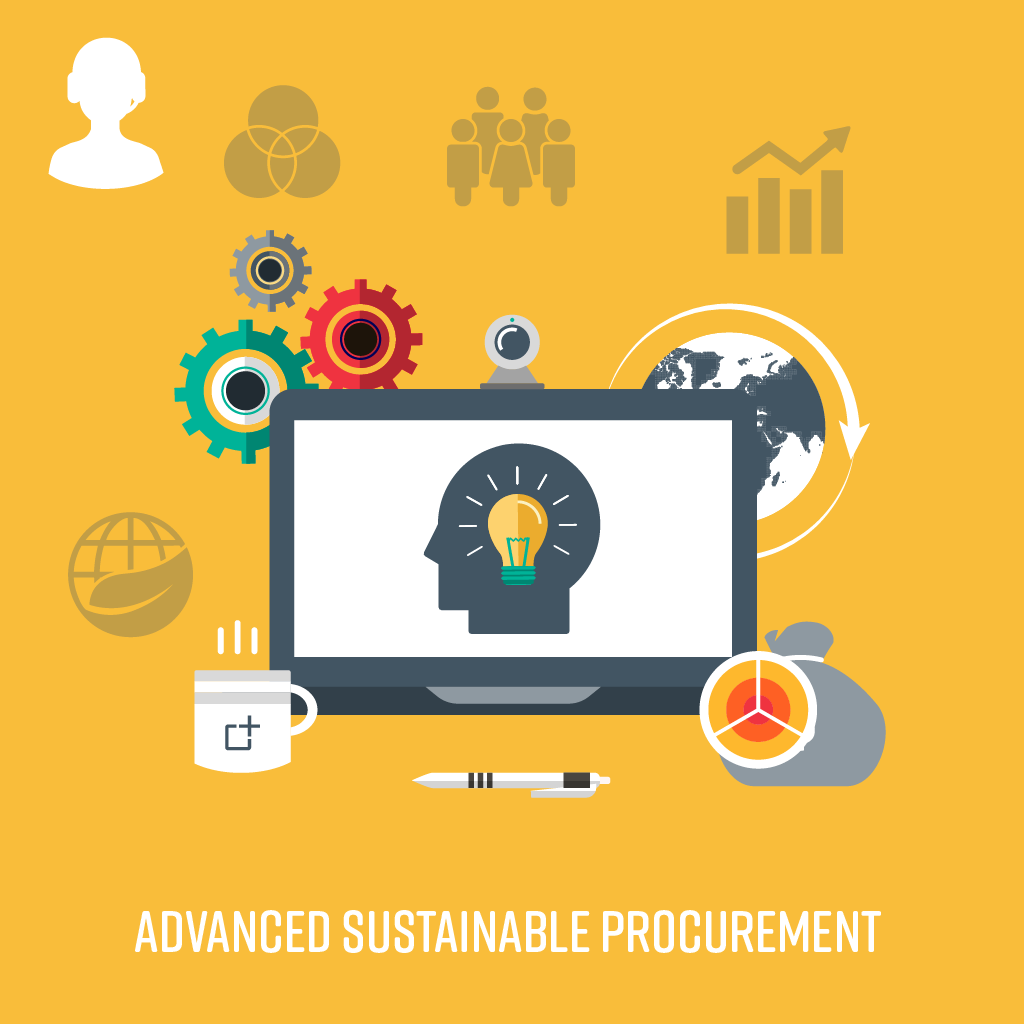
Lean operations management in lean services is focused on creating more value and utilizing fewer resources. Lean principles help to eliminate intangible wastes. However, it is difficult to identify them in a service environment. Businesses can maximise profits and create value by eliminating waste.
FAQ
What are the goods of logistics?
Logistics refers to the movement of goods from one place to another.
They include all aspects of transport, including packaging, loading, transporting, unloading, storing, warehousing, inventory management, customer service, distribution, returns, and recycling.
Logisticians ensure the product reaches its destination in the most efficient manner. Logisticians help companies improve their supply chain efficiency by providing information about demand forecasts and stock levels, production schedules, as well as availability of raw materials.
They keep track and monitor the transit of shipments, maintain quality standards, order replenishment and inventories, coordinate with suppliers, vendors, and provide support for sales and marketing.
What skills do production planners need?
To become a successful production planner, you need to be organized, flexible, and able to multitask. It is also important to be able communicate with colleagues and clients.
What does manufacturing industry mean?
Manufacturing Industries refers to businesses that manufacture products. Consumers are people who purchase these goods. These companies use a variety processes such as distribution, retailing and management to accomplish their purpose. They make goods from raw materials with machines and other equipment. This includes all types and varieties of manufactured goods, such as food items, clothings, building supplies, furnitures, toys, electronics tools, machinery vehicles, pharmaceuticals medical devices, chemicals, among others.
What is the difference between Production Planning, Scheduling and Production Planning?
Production Planning (PP), is the process of deciding what production needs to take place at any given time. Forecasting demand is one way to do this.
Scheduling is the process of assigning specific dates to tasks so they can be completed within the specified timeframe.
What are the 7 Rs of logistics?
The acronym "7R's" of Logistics stands for seven principles that underpin logistics management. It was published in 2004 by the International Association of Business Logisticians as part of their "Seven Principles of Logistics Management" series.
The acronym is composed of the following letters.
-
Responsible - to ensure that all actions are within the legal requirements and are not detrimental to others.
-
Reliable - have confidence in the ability to deliver on commitments made.
-
Reasonable - make sure you use your resources well and don't waste them.
-
Realistic - Consider all aspects of operations, including environmental impact and cost effectiveness.
-
Respectful - treat people fairly and equitably.
-
You are resourceful and look for ways to save money while increasing productivity.
-
Recognizable - Provide value-added services to customers
What kind of jobs are there in logistics?
There are many kinds of jobs available within logistics. These are some of the jobs available in logistics:
-
Warehouse workers – They load, unload and transport pallets and trucks.
-
Transportation drivers – These drivers drive trucks and wagons to transport goods and pick up the goods.
-
Freight handlers: They sort and package freight in warehouses.
-
Inventory managers - These are responsible for overseeing the stock of goods in warehouses.
-
Sales representatives - They sell products to customers.
-
Logistics coordinators: They plan and manage logistics operations.
-
Purchasing agents – They buy goods or services necessary to run a company.
-
Customer service representatives – They answer emails and phone calls from customers.
-
Ship clerks - They issue bills and process shipping orders.
-
Order fillers: They fill orders based off what has been ordered and shipped.
-
Quality control inspectors - They check incoming and outgoing products for defects.
-
Other - Logistics has many other job opportunities, including transportation supervisors, logistics specialists, and cargo specialists.
What are the responsibilities for a manufacturing manager
A manufacturing manager must make sure that all manufacturing processes run smoothly and effectively. They must also be alert to any potential problems and take appropriate action.
They must also be able to communicate with sales and marketing departments.
They should also be knowledgeable about the latest trends in the industry so they can use this information for productivity and efficiency improvements.
Statistics
- According to the United Nations Industrial Development Organization (UNIDO), China is the top manufacturer worldwide by 2019 output, producing 28.7% of the total global manufacturing output, followed by the United States, Japan, Germany, and India.[52][53] (en.wikipedia.org)
- Job #1 is delivering the ordered product according to specifications: color, size, brand, and quantity. (netsuite.com)
- In the United States, for example, manufacturing makes up 15% of the economic output. (twi-global.com)
- [54][55] These are the top 50 countries by the total value of manufacturing output in US dollars for its noted year according to World Bank.[56] (en.wikipedia.org)
- In 2021, an estimated 12.1 million Americans work in the manufacturing sector.6 (investopedia.com)
External Links
How To
How to Use 5S to Increase Productivity in Manufacturing
5S stands for "Sort", "Set In Order", "Standardize", "Separate" and "Store". Toyota Motor Corporation invented the 5S strategy in 1954. It assists companies in improving their work environments and achieving higher efficiency.
This method aims to standardize production processes so that they are repeatable, measurable and predictable. Cleaning, sorting and packing are all done daily. Because workers know what they can expect, this helps them perform their jobs more efficiently.
Five steps are required to implement 5S: Sort, Set In Order, Standardize. Separate. Each step has a different action and leads to higher efficiency. Sorting things makes it easier to find them later. You arrange items by placing them in an order. You then organize your inventory in groups. Make sure everything is correctly labeled when you label your containers.
Employees must be able to critically examine their work practices. Employees should understand why they do the tasks they do, and then decide if there are better ways to accomplish them. To implement the 5S system, employees must acquire new skills and techniques.
The 5S method not only increases efficiency but also boosts morale and teamwork. As they begin to see improvements, they feel motivated to continue working towards the goal of achieving higher levels of efficiency.