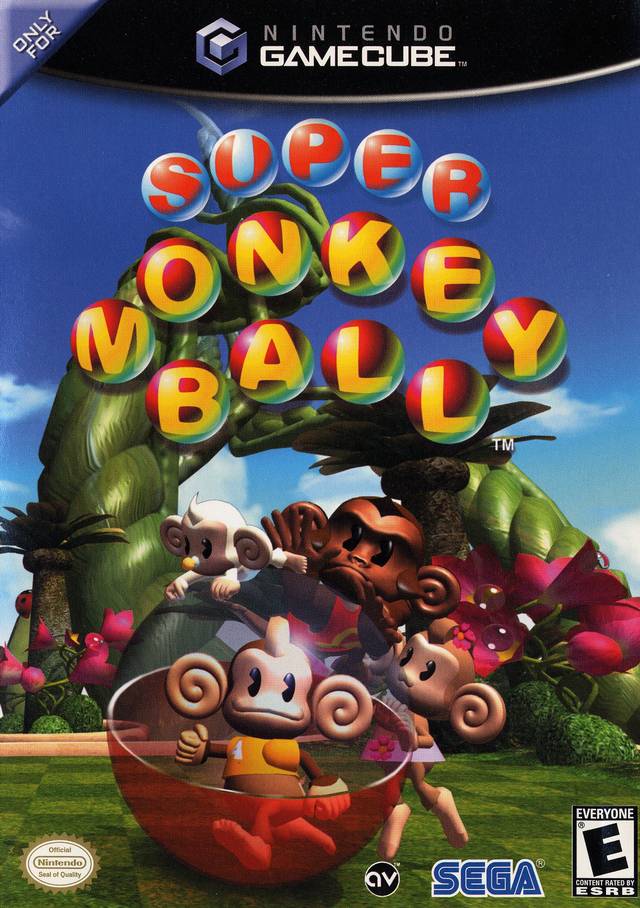
Machines are just one of the many tools that machinists use. These machines repair metal products like cars. They can also create precision metal parts or new alloys. As a result, machinists are often exposed to toxic substances. A good machinist is meticulous, can communicate well, and can interpret blueprints.
Machinists typically work full-time or part-time. Many of these machinists begin work right out high school. Some machinists go on to complete an apprenticeship before they can move up to a full time position. Others earn associate degrees. Some machinists might even choose to pursue engineering or computer-aided designing (CAD) degrees.
Machinists are often employed in factories or specialty shops. While these jobs can be noisy and expose to hazardous materials, they also offer excellent opportunities for problem-solving. A machinist can use either manual or automatically. Those with a lot of experience in the field can move up to supervisory or managerial positions. As the baby boomers begin to retire, so does the need for machine operators. As machine shops modernize for automation, job security increases.
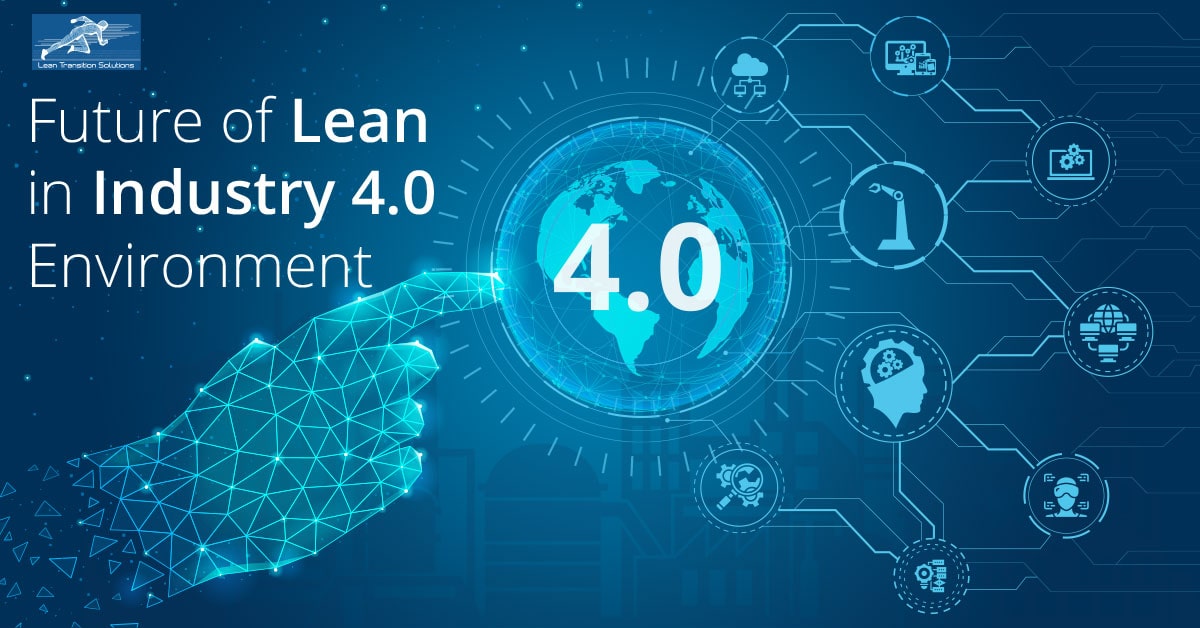
Depending on the employer, machinists can be assigned to specific duties, including setting up machines, repairing them, and making sure that the parts they produce meet quality standards. They can also work on assembly lines, which are machines that are operated by a human or a robot. Other responsibilities include programming and monitoring machines, as well as interpreting blueprints.
Machinists are skilled in working with a wide range of materials including steel, aluminum and brass as well as other metals. Although most machinists work on a machine that makes metal parts, they are sometimes required to work on other materials as well.
A high school diploma is the norm for machinists, but some employers may require an associate's or higher degree. A four-year training program is available for those who are interested in machinist careers. To get more experience and learn, you can work alongside a mentor at work. Ask your mentor about opportunities for additional education or apprenticeships.
Machinists need to work together, regardless of company. They can either work as part of a larger team or individually, but they must always follow safety procedures. It includes proper safety equipment such earplugs. Machinists are often exposed to chemicals and fumes. Fortunately, machinists do not have to be under constant time pressure.
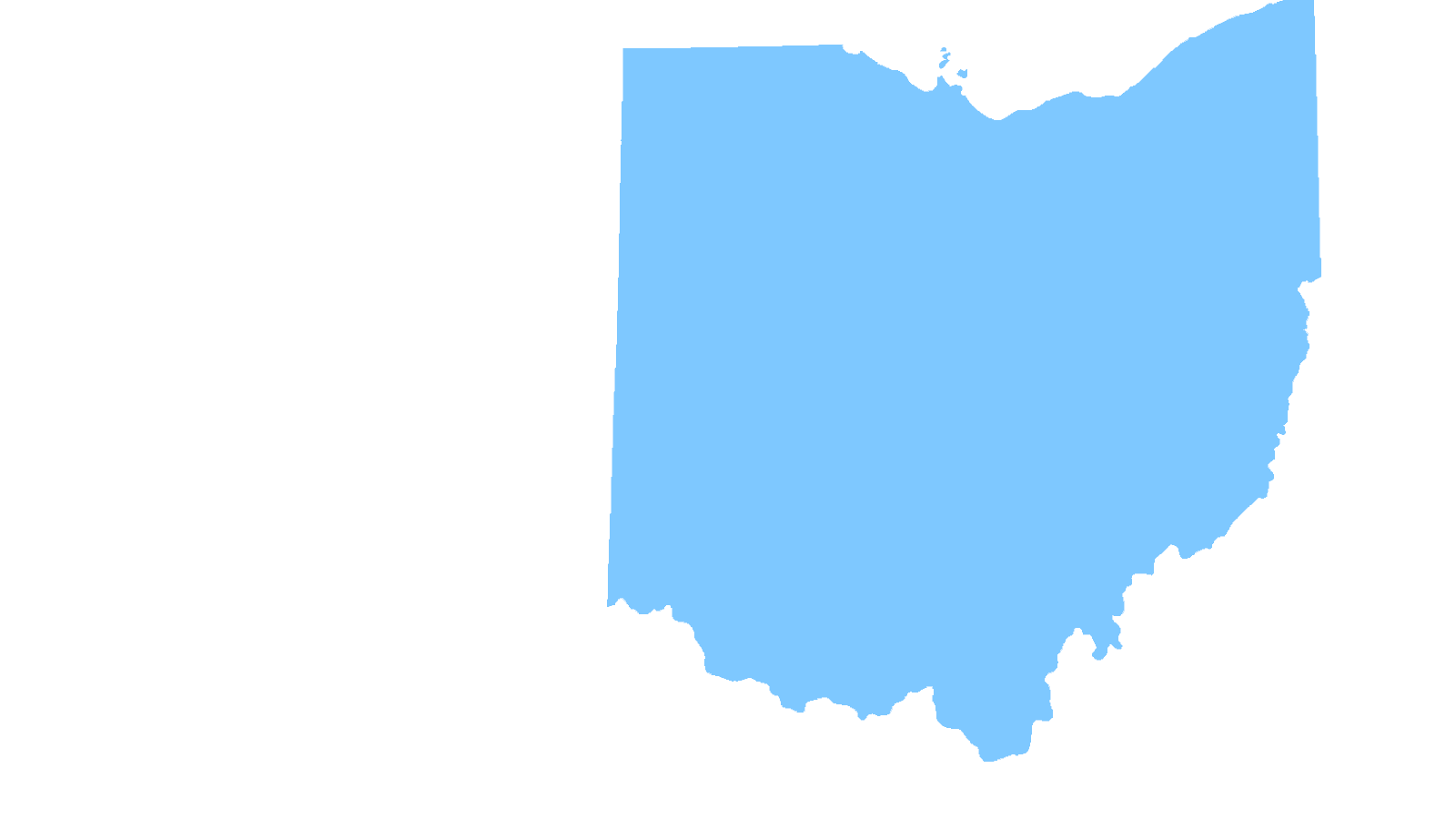
Machinists can also take college courses, or join trade unions. Union membership offers machinists greater benefits and more job security. Many union members have health insurance and retirement plans. Numerous colleges offer programs that allow you to become a machinist associate in two years.
You can work your way up the corporate ladder by obtaining a degree with machinist. As demand for auto parts grows, machinists are more in-demand. Between 2020 and 2030, job growth is expected to be 7%. In the coming decades, machinists will remain in high demand due to increased use of artificial Intelligence and retooling of automation.
FAQ
What are manufacturing and logistics?
Manufacturing refers the process of producing goods from raw materials through machines and processes. Logistics includes all aspects related to supply chain management, such as procurement, distribution planning, inventory control and transportation. Manufacturing and logistics can often be grouped together to describe a larger term that covers both the creation of products, and the delivery of them to customers.
What can I do to learn more about manufacturing?
You can learn the most about manufacturing by getting involved in it. But if that is not possible you can always read books and watch educational videos.
What are the goods of logistics?
Logistics refers to all activities that involve moving goods from A to B.
They encompass all aspects transport, including packaging and loading, transporting, storage, unloading.
Logisticians ensure that products reach the right destination at the right moment and under safe conditions. Logisticians help companies improve their supply chain efficiency by providing information about demand forecasts and stock levels, production schedules, as well as availability of raw materials.
They can also track shipments in transit and monitor quality standards.
What are the 7 Rs of logistics?
The acronym 7R's of Logistic is an acronym that stands for seven fundamental principles of logistics management. It was published in 2004 by the International Association of Business Logisticians as part of their "Seven Principles of Logistics Management" series.
The acronym is composed of the following letters.
-
Responsible - ensure that actions are in compliance with legal requirements and do not cause harm to others.
-
Reliable - Have confidence in your ability to fulfill all of your commitments.
-
Be responsible - Use resources efficiently and avoid wasting them.
-
Realistic - Consider all aspects of operations, including environmental impact and cost effectiveness.
-
Respectful - show respect and treat others fairly and fairly
-
Reliable - Find ways to save money and increase your productivity.
-
Recognizable: Provide customers with value-added service
Statistics
- In the United States, for example, manufacturing makes up 15% of the economic output. (twi-global.com)
- [54][55] These are the top 50 countries by the total value of manufacturing output in US dollars for its noted year according to World Bank.[56] (en.wikipedia.org)
- In 2021, an estimated 12.1 million Americans work in the manufacturing sector.6 (investopedia.com)
- Many factories witnessed a 30% increase in output due to the shift to electric motors. (en.wikipedia.org)
- (2:04) MTO is a production technique wherein products are customized according to customer specifications, and production only starts after an order is received. (oracle.com)
External Links
How To
How to Use 5S for Increasing Productivity in Manufacturing
5S stands to stand for "Sort", “Set In Order", “Standardize", and "Store". Toyota Motor Corporation was the first to develop the 5S approach in 1954. It assists companies in improving their work environments and achieving higher efficiency.
The basic idea behind this method is to standardize production processes, so they become repeatable, measurable, and predictable. Cleaning, sorting and packing are all done daily. These actions allow workers to perform their job more efficiently, knowing what to expect.
There are five steps that you need to follow in order to implement 5S. Each step requires a different action to increase efficiency. You can make it easy for people to find things later by sorting them. When you arrange items, you place them together. Next, organize your inventory into categories and store them in containers that are easily accessible. Finally, when you label your containers, you ensure everything is labeled correctly.
Employees must be able to critically examine their work practices. Employees need to be able understand their motivations and discover alternative ways to do them. They will need to develop new skills and techniques in order for the 5S system to be implemented.
The 5S Method not only improves efficiency, but it also helps employees to be more productive and happier. They will feel motivated to strive for higher levels of efficiency once they start to see results.