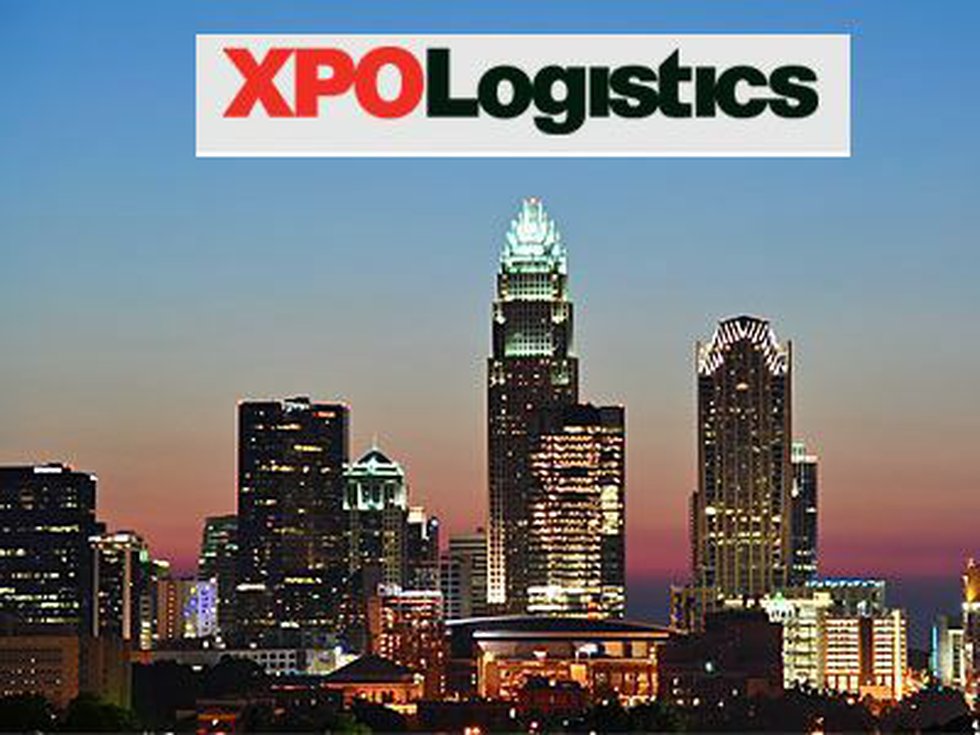
The five s's are the key to lean manufacturing. They are Standardize, Straighten, Shine, and Sustain. These are the steps to follow. You must train your team leaders and frontline operators to maximize your lean transformation.
Standardize
Clean and organize the workspace. This is the first step to the 5S process. This may be a one-time job, but if you standardize the process, it can become a routine. To make sure you have a consistent approach when performing 5S tasks, visual cues or checklist templates are all options.
These five s's can help your workplace be more productive and efficient. This approach will encourage employees to be organized and help them do their jobs efficiently. This will help improve your efficiency by organizing your work area. You can improve safety in your workplace by using the five s’s of lean. A well-organized workspace can help to avoid accidents, decrease mistakes, and increase productivity.
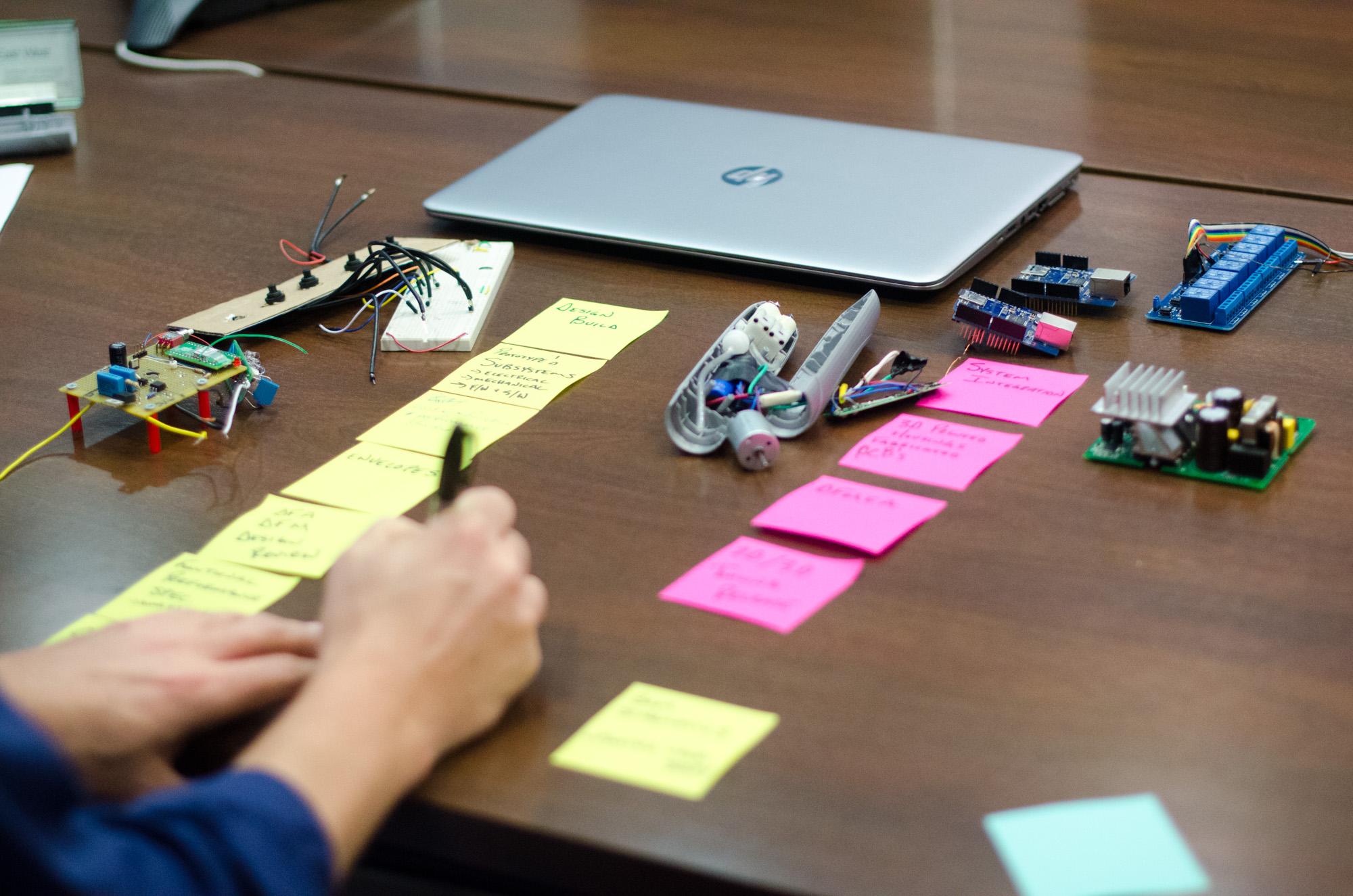
Straighten
It doesn't need to be hard to get your 5 s's in order. Companies can improve their business processes and practice lean principles consistently. For example, by organizing the components of an assembly line, workers will be able to find the components they need more easily. This can reduce the amount of time spent looking for misplaced parts, and improve workflow efficiency and company safety.
By reducing the number of items in each work area, you'll also save money on consumables and tools. This can significantly cut down on your office supply expenses. Straightening work cells not only helps you save money but it also increases the efficiency of your production process by improving quality, safety, and standard work.
Shine
Shine is about inspecting your workspace and identifying possible issues. Shine examines equipment and tools in order to improve flow. Shine can improve the maintenance of a workspace. It allows workers to spot potential problems before they hinder production. Shine can also be used to standardize a workspace to improve output.
Shine is one the 5S tools in lean manufacturing. This technique helps to automate work processes and reduce waste. It can be applied to any industry, including manufacturing. In this way, it applies the 5S principles across a business. It reduces inventory, work in progress, and supplies stock.
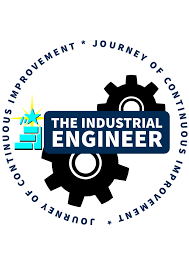
Keep it up
Re-instating a standardized system in a facility is key to maintaining the 5 S's of Lean. This is a continuous process that should be repeated until the facility functions at its best. Employees should learn how to perform 5S audits.
The 5S approach is about reducing waste, maximising productivity, and maintaining order in the workplace. It is basically a way to organize workplaces according to the five principles of Toyota Production System. Hiroyuki Hirano designed it to increase the efficiency of manufacturing plants in Japan after World War II.
FAQ
What does it take for a logistics enterprise to succeed?
A successful logistics business requires a lot more than just knowledge. To communicate effectively with clients and suppliers, you must be able to communicate well. You should be able analyse data and draw inferences. You need to be able work under pressure and manage stressful situations. In order to innovate and create new ways to improve efficiency, creativity is essential. To motivate and guide your team towards reaching organizational goals, you must have strong leadership skills.
It is important to be organized and efficient in order to meet tight deadlines.
How can I find out more about manufacturing?
Practical experience is the best way of learning about manufacturing. You can also read educational videos or take classes if this isn't possible.
How does a Production Planner differ from a Project Manager?
The difference between a product planner and project manager is that a planer is typically the one who organizes and plans the entire project. A production planner, however, is mostly involved in the planning stages.
How can manufacturing avoid production bottlenecks
The key to avoiding bottlenecks in production is to keep all processes running smoothly throughout the entire production cycle, from the time you receive an order until the time when the product ships.
This includes both planning for capacity and quality control.
This can be done by using continuous improvement techniques, such as Six Sigma.
Six Sigma can be used to improve the quality and decrease waste in all areas of your company.
It's all about eliminating variation and creating consistency in work.
What skills do production planners need?
You must be flexible and organized to become a productive production planner. You must also be able to communicate effectively with clients and colleagues.
What is production planning?
Production Planning refers to the development of a plan for every aspect of production. This document ensures that everything is prepared and available when you are ready for shooting. It should also contain information on achieving the best results on set. This includes shooting schedules, locations, cast lists, crew details, and equipment requirements.
First, you need to plan what you want to film. You may have decided where to shoot or even specific locations you want to use. Once you've identified the locations and scenes you want to use, you can begin to plan what elements you need for each scene. If you decide you need a car and don't know what model to choose, this could be an example. In this case, you could start looking up cars online to find out what models are available and then narrow your choices by choosing between different makes and models.
After you have chosen the right car, you will be able to begin thinking about accessories. Are you looking for people to sit in the front seats? Perhaps you have someone who needs to be able to walk around the back of your car. You may want to change the interior's color from black or white. These questions will help to determine the style and feel of your car. It is also worth considering the types of shots that you wish to take. What type of shots will you choose? Perhaps you want to show the engine or the steering wheel? These details will help identify the exact car you wish to film.
Once you have determined all of the above, you can move on to creating a schedule. You can use a schedule to determine when and where you need it to be shot. A schedule for each day will detail when you should arrive at the location and when you need leave. Everyone knows exactly what they should do and when. Book extra staff ahead of time if you need them. You don't want to hire someone who won't show up because he didn't know.
Also, consider how many days you will be filming your schedule. Some projects only take one or two days, while others may last weeks. While creating your schedule, it is important to remember whether you will require more than one shot per day. Shooting multiple takes over the same location will increase costs and take longer to complete. If you are unsure if you need multiple takes, it is better to err on the side of caution and shoot fewer takes rather than risk wasting money.
Budgeting is another important aspect of production planning. It is important to set a realistic budget so you can work within your budget. You can always lower the budget if you encounter unexpected problems. However, it is important not to overestimate the amount that you will spend. You will end up spending less money if you underestimate the cost of something.
Production planning is a complicated process. But once you understand how everything works together, it becomes much easier to plan future project.
What is meant by manufacturing industries?
Manufacturing Industries are those businesses that make products for sale. Consumers are the people who purchase these products. These companies use various processes such as production, distribution, retailing, management, etc., to fulfill this purpose. They create goods from raw materials, using machines and various other equipment. This covers all types of manufactured goods including clothing, food, building supplies and furniture, as well as electronics, tools, machinery, vehicles and pharmaceuticals.
Statistics
- In 2021, an estimated 12.1 million Americans work in the manufacturing sector.6 (investopedia.com)
- In the United States, for example, manufacturing makes up 15% of the economic output. (twi-global.com)
- Many factories witnessed a 30% increase in output due to the shift to electric motors. (en.wikipedia.org)
- (2:04) MTO is a production technique wherein products are customized according to customer specifications, and production only starts after an order is received. (oracle.com)
- You can multiply the result by 100 to get the total percent of monthly overhead. (investopedia.com)
External Links
How To
How to Use Lean Manufacturing in the Production of Goods
Lean manufacturing refers to a method of managing that seeks to improve efficiency and decrease waste. It was developed by Taiichi Okono in Japan, during the 1970s & 1980s. TPS founder Kanji Takoda awarded him the Toyota Production System Award (TPS). Michael L. Watkins published the "The Machine That Changed the World", the first book about lean manufacturing. It was published in 1990.
Lean manufacturing, often described as a set and practice of principles, is aimed at improving the quality, speed, cost, and efficiency of products, services, and other activities. It emphasizes reducing defects and eliminating waste throughout the value chain. Lean manufacturing can be described as just-in–time (JIT), total productive maintenance, zero defect (TPM), or even 5S. Lean manufacturing seeks to eliminate non-value added activities, such as inspection, work, waiting, and rework.
Lean manufacturing is a way for companies to achieve their goals faster, improve product quality, and lower costs. Lean manufacturing is considered one of the most effective ways to manage the entire value chain, including suppliers, customers, distributors, retailers, and employees. Lean manufacturing is widely practiced in many industries around the world. Toyota's philosophy is the foundation of its success in automotives, electronics and appliances, healthcare, chemical engineers, aerospace, paper and food, among other industries.
Five basic principles of Lean Manufacturing are included in lean manufacturing
-
Define Value - Identify the value your business adds to society and what makes you different from competitors.
-
Reduce Waste - Remove any activity which doesn't add value to your supply chain.
-
Create Flow - Ensure work moves smoothly through the process without interruption.
-
Standardize & Simplify - Make processes as consistent and repeatable as possible.
-
Build Relationships - Establish personal relationships with both internal and external stakeholders.
Although lean manufacturing isn't a new concept in business, it has gained popularity due to renewed interest in the economy after the 2008 global financial crisis. To increase their competitiveness, many businesses have turned to lean manufacturing. Many economists believe lean manufacturing will play a major role in economic recovery.
Lean manufacturing has many benefits in the automotive sector. These include higher customer satisfaction levels, reduced inventory levels as well as lower operating costs.
The principles of lean manufacturing can be applied in almost any area of an organization. It is especially useful for the production aspect of an organization, as it ensures that every step in the value chain is efficient and effective.
There are three main types in lean manufacturing
-
Just-in-Time Manufacturing: Also known as "pull systems", this type of lean manufacturing uses just-in-time manufacturing (JIT). JIT stands for a system where components are assembled on the spot rather than being made in advance. This approach reduces lead time, increases availability and reduces inventory.
-
Zero Defects Manufacturing: ZDM ensures that no defective units leave the manufacturing plant. It is better to repair a part than have it removed from the production line if it needs to be fixed. This applies to finished goods that may require minor repairs before shipment.
-
Continuous Improvement: Continuous Improvement aims to improve efficiency by continually identifying problems and making adjustments to eliminate or minimize waste. Continuous Improvement (CI) involves continuous improvement in processes, people, tools, and infrastructure.