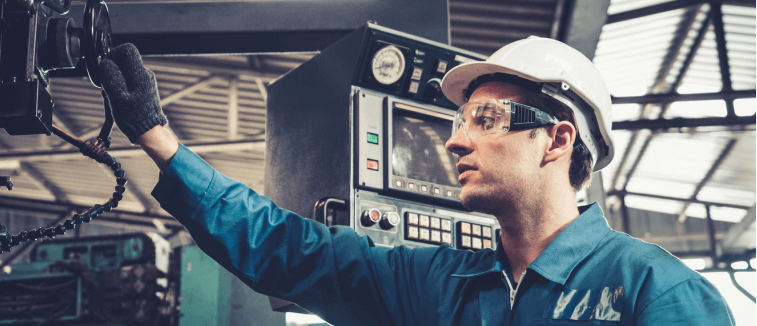
DFSS (Design for Six Sigma), is a design method that employs a variety of techniques to create a product, process, or service. It is intended to reduce waste, improve quality and increase market share. This is a highly effective method that can improve your products.
DFSS (Delivery for Customer Satisfaction) is a process that incorporates customer needs during the design process. This ensures that the product/service you design is most appropriate for the customer. Your product will also be of the highest quality once it goes on sale. DFSS can often be used to design a product/service completely from scratch. It can also be used in the design of products and/or services to replace or enhance existing products.
The DFSS team will determine what the customer wants and needs in the initial phase. This could include collecting information about existing processes, interviewing customers and surveying customers. To find the best match, the design team evaluates other products and designs. This phase includes the development and classification of functional requirements, as well as substitute concepts. Depending on the complexity and scope of the project, additional steps may be necessary.
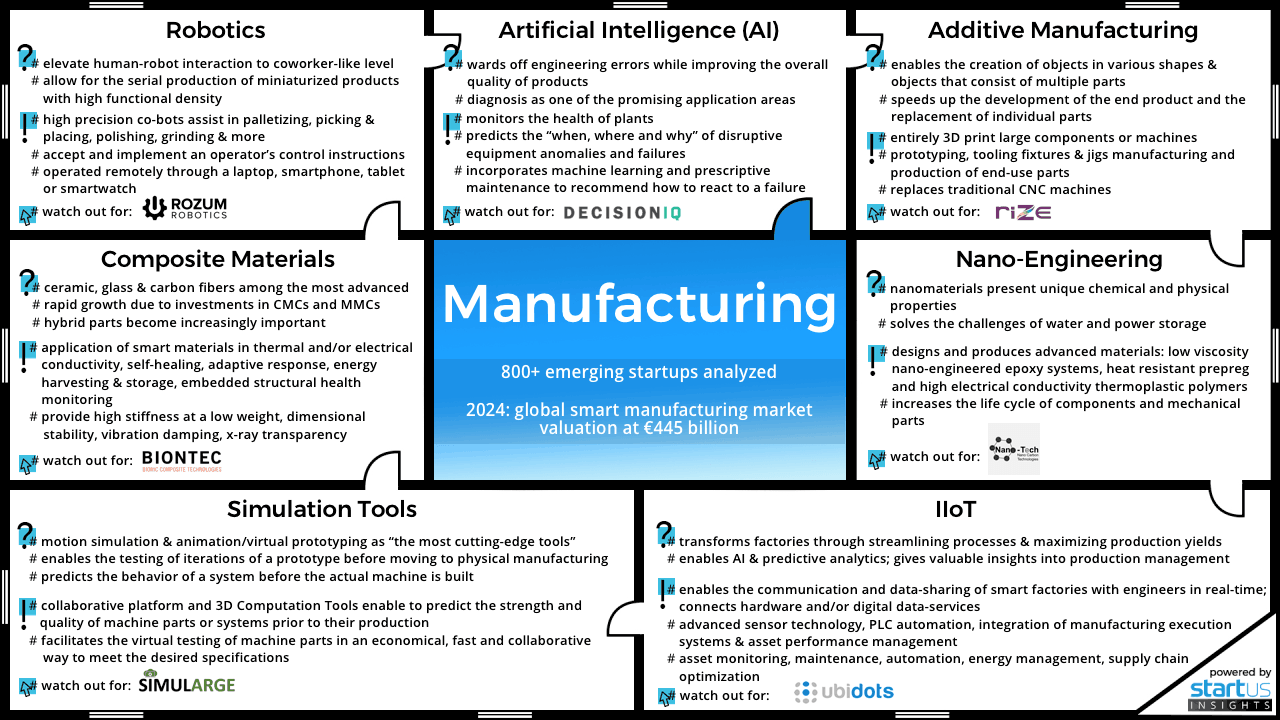
DFSS is a design methodology that helps companies design products and services efficiently and effectively. It is also used to identify potential problems before they become significant issues. It can also help reduce waste and increase profitability. Its aim is to increase the effectiveness of a product or service by identifying process parameters that make it more effective.
Different methods can be used to implement DFSS. DMADV is the most popular method. It involves a five-step process. It starts with defining the customer, identifying their needs, and developing a design concept. This methodology has a strong engineering foundation and is often used in the development of completely new products and services. It also includes an analysis and measurement phase to evaluate product performance.
Optimization is the next phase. This involves evaluating the product's performance across multiple performance levels. This step is crucial for the development of new business procedures. The goal of this stage is to reduce variability and ensure that the product will be stable over time.
The final stage involves the verification stage, which is often used to ensure that the product is stable. This stage also validates that the product is capable of performing over time. The process will also include validation testing. After the design is validated, validation testing is often completed.
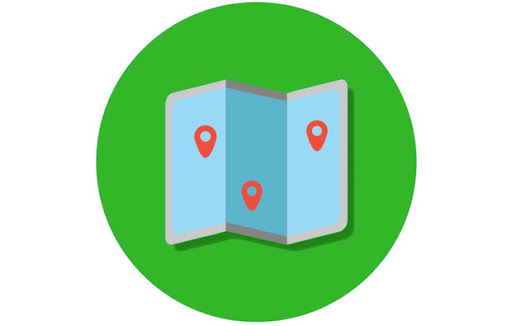
A detailed process map is essential to ensure that DFSS can be successfully implemented. It should show the various workflows involved in each step of the design process. Additionally, it is important to include information on resources and timeframes as well milestones. You must also be able pinpoint any external involvement required. It may be necessary to develop a prototype of the product to make sure it meets all customer requirements. Implementing DFSS in an environment with clear rewards is a great way to achieve the project's goals.
FAQ
What does it mean to be a manufacturer?
Manufacturing Industries is a group of businesses that produce goods for sale. Consumers are people who purchase these goods. To accomplish this goal, these companies employ a range of processes including distribution, sales, management, and production. They manufacture goods from raw materials using machines and other equipment. This covers all types of manufactured goods including clothing, food, building supplies and furniture, as well as electronics, tools, machinery, vehicles and pharmaceuticals.
What are manufacturing & logistics?
Manufacturing is the process of creating goods from raw materials by using machines and processes. Logistics is the management of all aspects of supply chain activities, including procurement, production planning, distribution, warehousing, inventory control, transportation, and customer service. Logistics and manufacturing are often referred to as one thing. It encompasses both the creation of products and their delivery to customers.
How can manufacturing avoid production bottlenecks
The key to avoiding bottlenecks in production is to keep all processes running smoothly throughout the entire production cycle, from the time you receive an order until the time when the product ships.
This includes planning to meet capacity requirements and quality control.
Continuous improvement techniques such Six Sigma can help you achieve this.
Six Sigma can be used to improve the quality and decrease waste in all areas of your company.
It's all about eliminating variation and creating consistency in work.
What are the 7 Rs of logistics?
The 7R's of Logistics is an acronym for the seven basic principles of logistics management. It was developed by International Association of Business Logisticians (IABL), and published as part of their "Seven Principles of Logistics Management Series" in 2004.
The following letters form the acronym:
-
Responsible - ensure that all actions taken are within legal requirements and are not harmful to others.
-
Reliable - Have confidence in your ability to fulfill all of your commitments.
-
Use resources effectively and sparingly.
-
Realistic – Consider all aspects, including cost-effectiveness as well as environmental impact.
-
Respectful: Treat others with fairness and equity
-
Responsive - Look for ways to save time and increase productivity.
-
Recognizable is a company that provides customers with value-added solutions.
How can I learn about manufacturing?
Practical experience is the best way of learning about manufacturing. If that is not possible, you could always read books or view educational videos.
Statistics
- You can multiply the result by 100 to get the total percent of monthly overhead. (investopedia.com)
- (2:04) MTO is a production technique wherein products are customized according to customer specifications, and production only starts after an order is received. (oracle.com)
- According to a Statista study, U.S. businesses spent $1.63 trillion on logistics in 2019, moving goods from origin to end user through various supply chain network segments. (netsuite.com)
- It's estimated that 10.8% of the U.S. GDP in 2020 was contributed to manufacturing. (investopedia.com)
- [54][55] These are the top 50 countries by the total value of manufacturing output in US dollars for its noted year according to World Bank.[56] (en.wikipedia.org)
External Links
How To
How to use 5S in Manufacturing to Increase Productivity
5S stands in for "Sort", the "Set In Order", "Standardize", or "Separate". Toyota Motor Corporation developed the 5S method in 1954. This methodology helps companies improve their work environment to increase efficiency.
The basic idea behind this method is to standardize production processes, so they become repeatable, measurable, and predictable. It means tasks like cleaning, sorting or packing, labeling, and storing are done every day. Workers can be more productive by knowing what to expect.
There are five steps that you need to follow in order to implement 5S. Each step is a different action that leads to greater efficiency. Sorting things makes it easier to find them later. When you arrange items, you place them together. After you have divided your inventory into groups you can store them in easy-to-reach containers. Finally, label all containers correctly.
Employees will need to be more critical about their work. Employees need to understand the reasons they do certain jobs and determine if there is a better way. To implement the 5S system, employees must acquire new skills and techniques.
In addition to improving efficiency, the 5S system also increases morale and teamwork among employees. Once they start to notice improvements, they are motivated to keep working towards their goal of increasing efficiency.