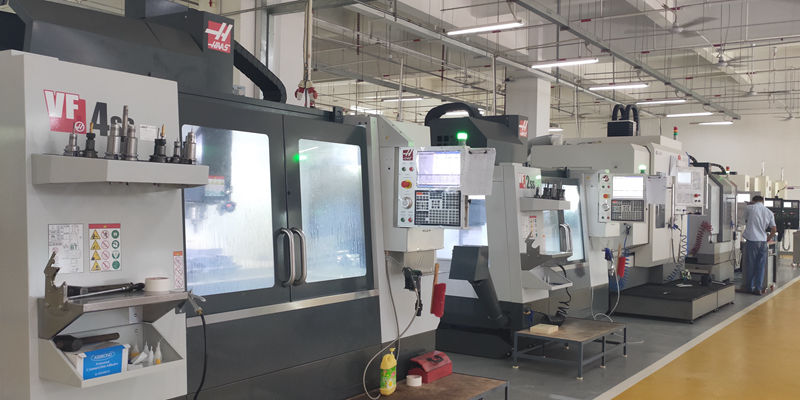
There are many types and styles of manufacturers. Which one is best for you business? Learn about Discrete manufacturing, Process manufacturing, Job shop manufacturing, and Continuous manufacturing. Each type has its own advantages and disadvantages. This article will discuss the differences between these four types. Based on your industry, location and product type, you will be able to choose the right model for your business. Once you decide which type is best for your company, you'll need to consider your sales, production, and quality control.
Discrete manufacturing
Discrete Manufacturing is the process of producing distinct products. Toys, cars, and aeroplanes are just a few examples of discrete manufacturing. Discrete manufacturing allows companies to focus on individual products, rather than bulk production of all items. Distinct manufacturing, for example, allows the creation of unique parts for aeroplanes by integrating several manufacturing processes. Discrete manufacturing is a popular way to manufacture high-tech items.
Discrete manufacturing produces distinct items. Instead of making many identical products, discrete production produces unique items that can be easily identified with serial numbers, labels and other numerical attributes. For example, a smartphone may consist of different parts manufactured in multiple factories in different states, and the individual parts are assembled only once the finished product is ready to be sold. The same applies to the bag that holds your smartphone. It may include parts from multiple plants, including the Missouri headquarters.
Process manufacturing
Process manufacturing refers to a type of manufacturing that uses formulas and recipes. This term contrasts with discrete manufacture, which is concerned only with the production of individual units and bills of materials. The process manufacturing concept also includes the assembly of parts. The two manufacturing methods have very different goals. Each of these methods is important in the manufacturing process. Here are three methods to distinguish between discrete and process manufacturing. Let's take a closer look at each.
Batch process manufacturing works in a similar way to continuous production, but it requires larger batches of raw material and is available around the clock. Batch process manufacturing can be found in paper production, pharmaceuticals, bookbinding, newspaper printing, and other industries. This process is not the best for every industry. This method is often too complicated and expensive for small-scale businesses. This is why large-scale companies often use it when they need to make large quantities.
Manufacturing job shop
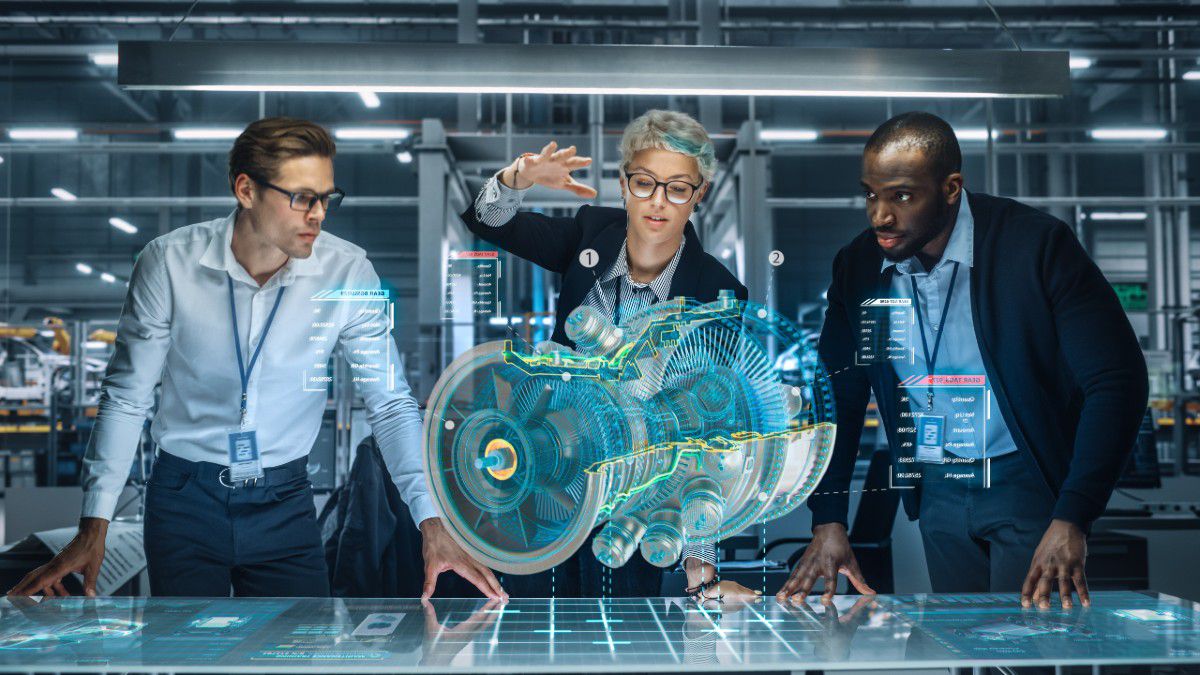
Job shop manufacturing is small-scale manufacturing that specializes in custom, semi-custom, and batch manufacturing. After each job is complete, job shop systems can move to the next. This method of production is also called lean manufacturing, as a single-shift operation is more efficient than many other methods. These are just a few of the many benefits of job-shop manufacturing. This manufacturing process is described in detail below. This method of manufacturing might be beneficial for your business.
First, job shops must be more efficient. Incorporating new manufacturing principles is key to achieving lean manufacturing systems. These principles focus on quality control and justin-time production and are especially relevant for high-volume operations. By adopting new manufacturing principles, a job shop can increase productivity while lowering costs at the same time. Also, each job should be completed one by one, so there shouldn't be any queues.
Continuous manufacturing
Continuous manufacturing allows for flexible tracking which is one of the greatest advantages. This is particularly helpful when it comes to product failure, since the quantity of raw input material and the time stamp on each production line can help to identify when a batch of drug is defective. This increased tracking helps manufacturers reduce waste and decrease the likelihood of product shortages. Continuous manufacturing is also becoming more popular in the pharmaceutical sector.
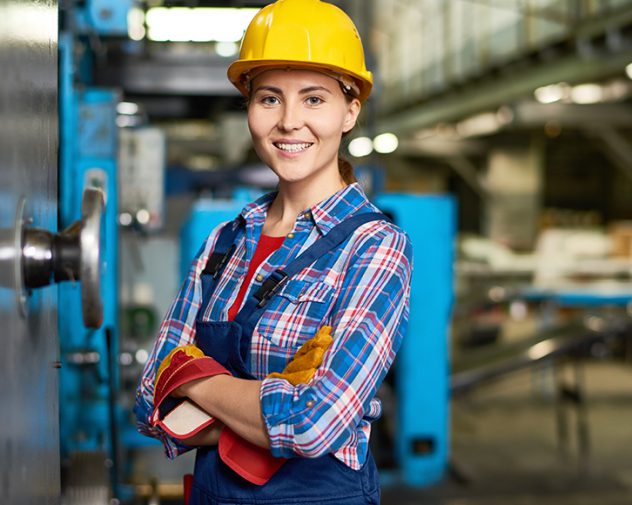
However, while the benefits of continuous manufacturing are clear, implementation is slow. The lack of integration with other departments can often make implementation difficult. Continuous manufacturing has the potential of being a game changer in the pharmaceutical business, despite the limitations. To be successful, however, the entire process must be integrated with continuous flow as well as end-to–end integration. While the benefits of continuous manufacturing have been well-known in the pharmaceutical sector, implementation has been slow.
FAQ
What's the difference between Production Planning & Scheduling?
Production Planning (PP), also known as forecasting and identifying production capacities, is the process that determines what product needs to be produced at any particular time. Forecasting and identifying production capacity are two key elements to this process.
Scheduling refers to the process of allocating specific dates to tasks in order that they can be completed within a specified timeframe.
What is the responsibility for a logistics manager
Logistics managers ensure that goods arrive on time and are unharmed. This is done using his/her knowledge of the company's products. He/she also needs to ensure adequate stock to meet demand.
What are the products and services of logistics?
Logistics refers to all activities that involve moving goods from A to B.
They encompass all aspects transport, including packaging and loading, transporting, storage, unloading.
Logisticians ensure the product reaches its destination in the most efficient manner. They assist companies with their supply chain efficiency through information on demand forecasts. Stock levels, production times, and availability.
They monitor shipments in transit, ensure quality standards, manage inventories, replenish orders, coordinate with suppliers and other vendors, and offer support services for sales, marketing, and customer service.
What are the four types in manufacturing?
Manufacturing is the process by which raw materials are transformed into useful products through machines and processes. Manufacturing can include many activities such as designing and building, testing, packaging shipping, selling, servicing, and other related activities.
What does it mean to warehouse?
Warehouses and storage facilities are where goods are kept before being sold. It can be an indoor space or an outdoor area. It could be one or both.
What are the 7 Rs of logistics.
The 7R's of Logistics is an acronym for the seven basic principles of logistics management. It was developed and published by the International Association of Business Logisticians in 2004 as part of the "Seven Principles of Logistics Management".
The acronym is made up of the following letters:
-
Responsible - ensure that all actions taken are within legal requirements and are not harmful to others.
-
Reliable - Have confidence in your ability to fulfill all of your commitments.
-
Reasonable - make sure you use your resources well and don't waste them.
-
Realistic – consider all aspects of operations, from cost-effectiveness to environmental impact.
-
Respectful - Treat people fairly and equitably
-
Be resourceful: Look for opportunities to save money or increase productivity.
-
Recognizable: Provide customers with value-added service
Statistics
- [54][55] These are the top 50 countries by the total value of manufacturing output in US dollars for its noted year according to World Bank.[56] (en.wikipedia.org)
- In 2021, an estimated 12.1 million Americans work in the manufacturing sector.6 (investopedia.com)
- Job #1 is delivering the ordered product according to specifications: color, size, brand, and quantity. (netsuite.com)
- You can multiply the result by 100 to get the total percent of monthly overhead. (investopedia.com)
- In the United States, for example, manufacturing makes up 15% of the economic output. (twi-global.com)
External Links
How To
How to Use Lean Manufacturing for the Production of Goods
Lean manufacturing is an approach to management that aims for efficiency and waste reduction. It was developed in Japan between 1970 and 1980 by Taiichi Ohno. TPS founder Kanji Tyoda gave him the Toyota Production System, or TPS award. The first book published on lean manufacturing was titled "The Machine That Changed the World" written by Michael L. Watkins and published in 1990.
Lean manufacturing can be described as a set or principles that are used to improve quality, speed and cost of products or services. It emphasizes the elimination of defects and waste throughout the value stream. Lean manufacturing is called just-in-time (JIT), zero defect, total productive maintenance (TPM), or 5S. Lean manufacturing is about eliminating activities that do not add value, such as inspection, rework, and waiting.
Lean manufacturing is a way for companies to achieve their goals faster, improve product quality, and lower costs. Lean manufacturing is considered one of the most effective ways to manage the entire value chain, including suppliers, customers, distributors, retailers, and employees. Lean manufacturing is widely practiced in many industries around the world. Toyota's philosophy has been a key driver of success in many industries, including automobiles and electronics.
Five basic principles of Lean Manufacturing are included in lean manufacturing
-
Define Value- Identify the added value your company brings to society. What makes you stand out from your competitors?
-
Reduce waste - Stop any activity that isn't adding value to the supply chains.
-
Create Flow. Ensure that your work is uninterrupted and flows seamlessly.
-
Standardize and Simplify – Make processes as consistent, repeatable, and as simple as possible.
-
Build Relationships- Develop personal relationships with both internal as well as external stakeholders.
Although lean manufacturing isn't a new concept in business, it has gained popularity due to renewed interest in the economy after the 2008 global financial crisis. To increase their competitiveness, many businesses have turned to lean manufacturing. In fact, some economists believe that lean manufacturing will be an important factor in economic recovery.
Lean manufacturing, which has many benefits, is now a standard practice in the automotive industry. These benefits include increased customer satisfaction, reduced inventory levels and lower operating costs.
Any aspect of an enterprise can benefit from Lean manufacturing. Lean manufacturing is most useful in the production sector of an organisation because it ensures that each step in the value-chain is efficient and productive.
There are three main types in lean manufacturing
-
Just-in Time Manufacturing, (JIT): This kind of lean manufacturing is also commonly known as "pull-systems." JIT stands for a system where components are assembled on the spot rather than being made in advance. This strategy aims to decrease lead times, increase availability of parts and reduce inventory.
-
Zero Defects Manufacturing - ZDM: ZDM focuses its efforts on making sure that no defective units leave a manufacturing facility. If a part needs to be fixed during the assembly line, it should be repaired rather than scrapped. This also applies to finished products that need minor repairs before being shipped.
-
Continuous Improvement (CI: Continuous improvement aims to increase the efficiency of operations by constantly identifying and making improvements to reduce or eliminate waste. Continuous improvement involves continuous improvement of processes and people as well as tools.