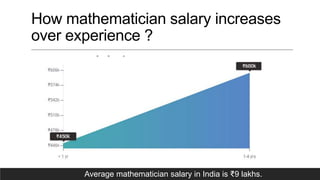
An artisan who works in the production process of chemical products is called a Chemical Technician. They are also responsible for performing tests on materials used in the manufacturing process. They may work in research and development, in manufacturing lines or laboratories.
They are typically supervised and assisted by chemists. They are responsible for monitoring product quality, testing new materials and collecting samples. They might be promoted after they have gained experience. Many pharmaceutical companies hire them. Earn more if you have a bachelor's in engineering, biology, or chemistry.
Although the pay for Chemical Technicians varies by location, the average salary is $48,990. This includes taxable wages as well as bonuses. It also takes into account the skills, education, and experience of workers. Chemical Technicians with the highest earnings earned more than $60,000 annually.
As a Chemical Technician, you will be responsible for conducting research and developing new chemicals and pharmaceuticals. They are responsible for analysing the ingredients of pharmaceuticals, food, as well as other products. They can supervise workers on the production lines.
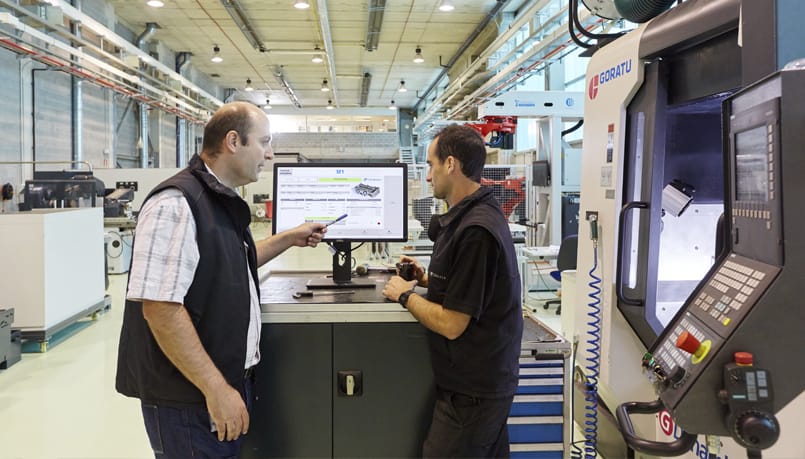
An associate's or bachelors degree in biology, chemistry, physics or computer science will be required for a career as Chemical Technician. You can also earn a graduate degree or doctoral. Some companies prefer to hire chemical technicians who have a college degree. A master's degree may be required for other jobs.
Visit a school placement office to find out more about job opportunities. There are many job banks available online. American Chemical Society is another great resource. Local chapters can often post job listings.
If you're looking for a job as a Chemical Technician, you should be prepared to work long hours. Although most laboratories work seven days a week, experienced workers may be called in for odd-hours inspections and experiments.
The majority of Chemical Technicians earn between $36,000- $47,000. Experienced workers can earn up to $11,000 more. On the other hand, entry-level workers are able to earn as little as $15 to 18 per hour.
San Francisco and San Jose are the most highly ranked cities in the United States for Chemical Technician salaries. Both cities beat the national average of over 20%. In addition, the BLS reported that Chemical Technicians in these areas earned more than $83,600.
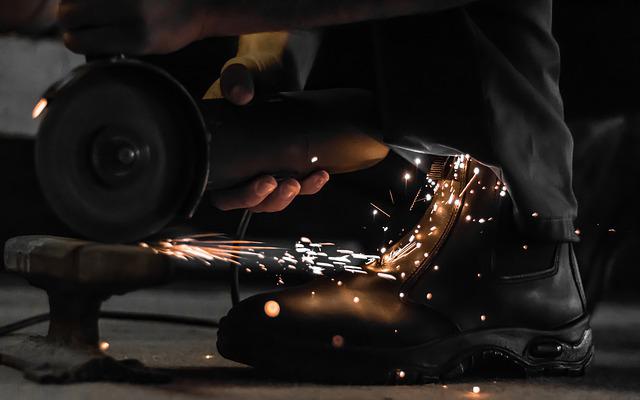
According to the Bureau of Labor Statistics, Chemical Technicians are expected to see a slower growth rate than average in terms of job opportunities. Their employment is expected growth of 3 percent through 2014 but only 4 percent in the next ten. This will likely lead to a higher demand for skilled technicians.
Chemistry R&D will become more important as the environment becomes more prominent. These workers will find the most rewarding jobs in laboratories that conduct testing on new materials.
FAQ
What are the 4 types of manufacturing?
Manufacturing refers the process of turning raw materials into useful products with machines and processes. Manufacturing can include many activities such as designing and building, testing, packaging shipping, selling, servicing, and other related activities.
What skills should a production planner have?
You must be flexible and organized to become a productive production planner. Communication skills are essential to ensure that you can communicate effectively with clients, colleagues, and customers.
Why automate your warehouse
Modern warehouses have become more dependent on automation. E-commerce has increased the demand for quicker delivery times and more efficient processes.
Warehouses should be able adapt quickly to new needs. In order to do this, they need to invest in technology. Automating warehouses is a great way to save money. These are some of the benefits that automation can bring to warehouses:
-
Increases throughput/productivity
-
Reduces errors
-
Improves accuracy
-
Safety is boosted
-
Eliminates bottlenecks
-
Allows companies scale more easily
-
Workers are more productive
-
It gives visibility to everything that happens inside the warehouse
-
Enhances customer experience
-
Improves employee satisfaction
-
Minimizes downtime and increases uptime
-
This ensures that quality products are delivered promptly
-
Human error can be eliminated
-
Assure compliance with regulations
What is the job of a manufacturer manager?
A manufacturing manager must ensure that all manufacturing processes are efficient and effective. They should be alert for any potential problems in the company and react accordingly.
They must also be able to communicate with sales and marketing departments.
They should also be aware of the latest trends in their industry and be able to use this information to help improve productivity and efficiency.
Statistics
- (2:04) MTO is a production technique wherein products are customized according to customer specifications, and production only starts after an order is received. (oracle.com)
- In the United States, for example, manufacturing makes up 15% of the economic output. (twi-global.com)
- [54][55] These are the top 50 countries by the total value of manufacturing output in US dollars for its noted year according to World Bank.[56] (en.wikipedia.org)
- Many factories witnessed a 30% increase in output due to the shift to electric motors. (en.wikipedia.org)
- It's estimated that 10.8% of the U.S. GDP in 2020 was contributed to manufacturing. (investopedia.com)
External Links
How To
How to use Lean Manufacturing in the production of goods
Lean manufacturing is an approach to management that aims for efficiency and waste reduction. It was developed in Japan during the 1970s and 1980s by Taiichi Ohno, who received the Toyota Production System (TPS) award from TPS founder Kanji Toyoda. Michael L. Watkins published the first book on lean manufacturing in 1990.
Lean manufacturing is often described as a set if principles that help improve the quality and speed of products and services. It emphasizes the elimination of defects and waste throughout the value stream. Lean manufacturing is also known as just in time (JIT), zero defect total productive maintenance(TPM), and five-star (S). Lean manufacturing is about eliminating activities that do not add value, such as inspection, rework, and waiting.
Lean manufacturing not only improves product quality but also reduces costs. Companies can also achieve their goals faster by reducing employee turnover. Lean manufacturing has been deemed one of the best ways to manage the entire value-chain, including customers, distributors as well retailers and employees. Lean manufacturing can be found in many industries. Toyota's philosophy is the foundation of its success in automotives, electronics and appliances, healthcare, chemical engineers, aerospace, paper and food, among other industries.
Five fundamental principles underlie lean manufacturing.
-
Define Value- Identify the added value your company brings to society. What makes you stand out from your competitors?
-
Reduce Waste - Remove any activity which doesn't add value to your supply chain.
-
Create Flow. Ensure that your work is uninterrupted and flows seamlessly.
-
Standardize and simplify – Make processes as repeatable and consistent as possible.
-
Build relationships - Develop and maintain personal relationships with both your internal and external stakeholders.
Although lean manufacturing isn't a new concept in business, it has gained popularity due to renewed interest in the economy after the 2008 global financial crisis. To increase their competitiveness, many businesses have turned to lean manufacturing. In fact, some economists believe that lean manufacturing will be an important factor in economic recovery.
Lean manufacturing is now becoming a common practice in the automotive industry, with many benefits. These include better customer satisfaction and lower inventory levels. They also result in lower operating costs.
The principles of lean manufacturing can be applied in almost any area of an organization. Because it makes sure that all value chains are efficient and effectively managed, Lean Manufacturing is particularly helpful for organizations.
There are three types of lean manufacturing.
-
Just-in-Time Manufacturing (JIT): This type of lean manufacturing is commonly referred to as "pull systems." JIT stands for a system where components are assembled on the spot rather than being made in advance. This method reduces lead times, increases availability, and decreases inventory.
-
Zero Defects Manufacturing (ZDM),: ZDM is a system that ensures no defective units are left the manufacturing facility. You should repair any part that needs to be repaired during an assembly line. This also applies to finished products that need minor repairs before being shipped.
-
Continuous Improvement (CI: Continuous improvement aims to increase the efficiency of operations by constantly identifying and making improvements to reduce or eliminate waste. Continuous Improvement (CI) involves continuous improvement in processes, people, tools, and infrastructure.