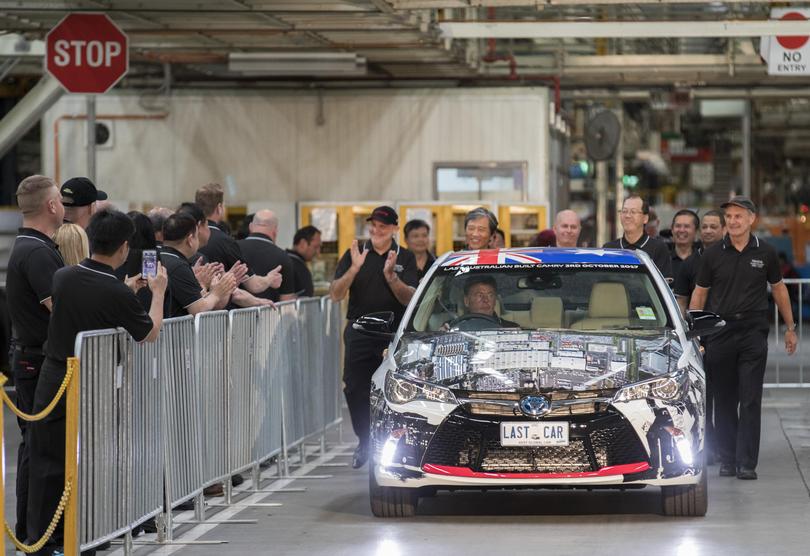
US manufacturing is our largest and most dynamic industry. It's a major driver of economic growth. Its production adds approximately $2 trillion to the United States every year. This generates jobs, and supports hundreds or local economies all over the country.
Since the global crisis, there has been a drastic decline in manufacturing employment. The underlying problems - the loss in American jobs to China, and the trade deficit that results - may be difficult to understand. However, it is clear that this has had a significant impact on the overall economy.
Manufacturing in the US supports approximately 17 million jobs. The output of this industry contributes to the US Gross Domestic Product (GDP) significantly. It is a critical part of our economy, accounting for 20 percent of our capital investment, 35 percent of productivity growth, 60 percent of exports and 70 percent of business R&D spending (Exhibit 1).
While these industries have seen declines and disruptions in many cases, the US Manufacturing sector is currently undergoing a massive transformation. It is facing competition from Asian low-cost producers and may soon undergo a change that could aid in the recovery of US growth.
Rebuilding our battered manufacturing sector will require a long-term commitment to support the industry and the people who make it happen. This will require a long-term commitment to support our workforce, innovation, technology and the infrastructure.
We need to build an innovative and more competitive manufacturing industry, which will allow our economy thrive and be competitive. This is not an annual project but a multi-decade effort to rebuild our manufacturing sector. We want to ensure that we remain a leader in technological innovation and industrial production for many years to come.
A sustainable and strong manufacturing economy can strengthen our economy and contribute to our nation's security. It also provides important employment and advancement opportunities for a broad segment of our population. It can also be used to recalibrate the US economy and boost our middle class, as well as improve the lives for millions of Americans.
Many programs are underway to help strengthen the manufacturing sector. There is a manufacturing council which advises the secretary for commerce and other government agencies about policies that impact the manufacturing sector. We also have many federal departments and organizations actively involved in supporting our manufacturing industry.
The manufacturing sector is a key economic engine that drives growth and creates jobs in many of the nation's most diverse communities. It is a sector that employs a wider than average swath and allows workers to upgrade their skills without a four year degree.
For example, the average earnings of non-college-educated workers in manufacturing are 10.9 percent higher than those of similar workers in the economy overall. The U.S. has been able to achieve a more equitable distribution of wealth and income. The manufacturing sector was also a key route for the poor to rise up the economic ladder.
FAQ
How can we reduce manufacturing overproduction?
Better inventory management is key to reducing excess production. This would reduce the time spent on unproductive activities like purchasing, storing and maintaining excess stock. We could use these resources to do other productive tasks.
You can do this by adopting a Kanban method. A Kanban board is a visual display used to track work in progress. Kanban systems are where work items travel through a series of states until reaching their final destination. Each state has a different priority level.
For instance, when work moves from one stage to another, the current task is complete enough to be moved to the next stage. A task that is still in the initial stages of a process will be considered complete until it moves on to the next stage.
This allows work to move forward and ensures that no work is missed. With a Kanban board, managers can see exactly how much work is being done at any given moment. This allows them to adjust their workflows based on real-time information.
Another way to control inventory levels is to implement lean manufacturing. Lean manufacturing focuses on eliminating waste throughout the entire production chain. Anything that does nothing to add value to a product is waste. Here are some examples of common types.
-
Overproduction
-
Inventory
-
Packaging that is not necessary
-
Material surplus
By implementing these ideas, manufacturers can improve efficiency and cut costs.
Can some manufacturing processes be automated?
Yes! Automation has been around since ancient times. The Egyptians created the wheel thousands years ago. Robots are now used to assist us in assembly lines.
There are many uses of robotics today in manufacturing. These include:
-
Assembly line robots
-
Robot welding
-
Robot painting
-
Robotics inspection
-
Robots create products
Manufacturing could also benefit from automation in other ways. 3D printing makes it possible to produce custom products in a matter of days or weeks.
What is production planning?
Production Planning refers to the development of a plan for every aspect of production. This document aims to ensure that everything is planned and ready when you are ready to shoot. It should also provide information about how best to produce the best results while on set. This information includes locations, crew details and equipment requirements.
First, you need to plan what you want to film. You may already know where you want the film to be shot, or perhaps you have specific locations and sets you wish to use. Once you have determined your scenes and locations, it is time to start figuring out the elements that you will need for each scene. For example, you might decide that you need a car but don't know exactly what model you want. If this is the case, you might start searching online for car models and then narrow your options by selecting from different makes.
Once you have found the right car, you can start thinking about extras. Are you looking for people to sit in the front seats? Or maybe you just need someone to push the car around. Perhaps you would like to change the interior colour from black to white. These questions will help to determine the style and feel of your car. You can also think about the type of shots you want to get. What type of shots will you choose? Maybe you want to show your engine or the steering wheel. These details will help identify the exact car you wish to film.
Once you have made all the necessary decisions, you can start to create a schedule. The schedule will show you when to begin shooting and when to stop. Each day will include the time when you need to arrive at the location, when you need to leave and when you need to return home. Everyone knows exactly what they should do and when. If you need to hire extra staff, you can make sure you book them in advance. It is not worth hiring someone who won’t show up because you didn’t tell him.
When creating your schedule, you will also need to consider the number of days you need to film. Some projects may only take a couple of days, while others could last for weeks. While creating your schedule, it is important to remember whether you will require more than one shot per day. Multiple takes of the same location will lead to higher costs and take more time. You can't be certain if you will need multiple takes so it is better not to shoot too many.
Budgeting is another crucial aspect of production plan. As it will allow you and your team to work within your financial means, setting a realistic budget is crucial. It is possible to reduce the budget at any time if you experience unexpected problems. You shouldn't underestimate the amount you'll spend. If you underestimate the cost of something, you will have less money left after paying for other items.
Production planning is a complicated process. But once you understand how everything works together, it becomes much easier to plan future project.
Statistics
- In 2021, an estimated 12.1 million Americans work in the manufacturing sector.6 (investopedia.com)
- You can multiply the result by 100 to get the total percent of monthly overhead. (investopedia.com)
- Job #1 is delivering the ordered product according to specifications: color, size, brand, and quantity. (netsuite.com)
- Many factories witnessed a 30% increase in output due to the shift to electric motors. (en.wikipedia.org)
- According to a Statista study, U.S. businesses spent $1.63 trillion on logistics in 2019, moving goods from origin to end user through various supply chain network segments. (netsuite.com)
External Links
How To
How to Use the 5S to Increase Productivity In Manufacturing
5S stands as "Sort", Set In Order", Standardize", Separate" and "Store". Toyota Motor Corporation was the first to develop the 5S approach in 1954. It allows companies to improve their work environment, thereby achieving greater efficiency.
The basic idea behind this method is to standardize production processes, so they become repeatable, measurable, and predictable. This means that every day tasks such cleaning, sorting/storing, packing, and labeling can be performed. Through these actions, workers can perform their jobs more efficiently because they know what to expect from them.
Implementing 5S involves five steps: Sort, Set in Order, Standardize Separate, Store, and Each step is a different action that leads to greater efficiency. You can make it easy for people to find things later by sorting them. When you arrange items, you place them together. Next, organize your inventory into categories and store them in containers that are easily accessible. Finally, when you label your containers, you ensure everything is labeled correctly.
Employees need to reflect on how they do their jobs. Employees need to understand the reasons they do certain jobs and determine if there is a better way. They will need to develop new skills and techniques in order for the 5S system to be implemented.
In addition to improving efficiency, the 5S system also increases morale and teamwork among employees. As they begin to see improvements, they feel motivated to continue working towards the goal of achieving higher levels of efficiency.