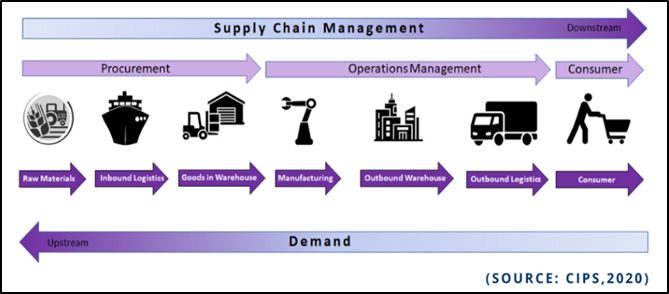
Lean to agility is a great method to reduce waste, increase team productivity and increase efficiency. It focuses on prioritizing work and eliminating waste, while empowering teams and scrum masters to do the rest. Agile teams should be empowered to assume the roles of product owners and servant leaders, who are committed towards the success of their projects.
Time-to-market
The time it takes from ideation to full release is one of the most critical measures of product success. A shorter time frame will allow your company to gain market share and increase revenue faster. Companies need to know their development processes, and how they use them. Companies will then be able to optimize their processes to meet the objectives of their business and to maximize their capabilities to improve their time to market.
Using outsourcing as a tool to reduce time-to-market is one way to shorten the time required to market a new product. You can also reduce the time required to market a new product by creating a network of trusted support partners. This will help you reduce risk and to share your resources.
Iteration
Iteration plays a critical role in agile software development. Iteration is a key element of agile software development. This concept emphasizes the value of small, measured steps that can be evaluated faster than a complete process. The chances of success are greater for features that are more detailed. This approach can be time-bound. The end product of an iteration should be running and releasable. This is possible by integrating, testing, and deploying the code on an internal server.
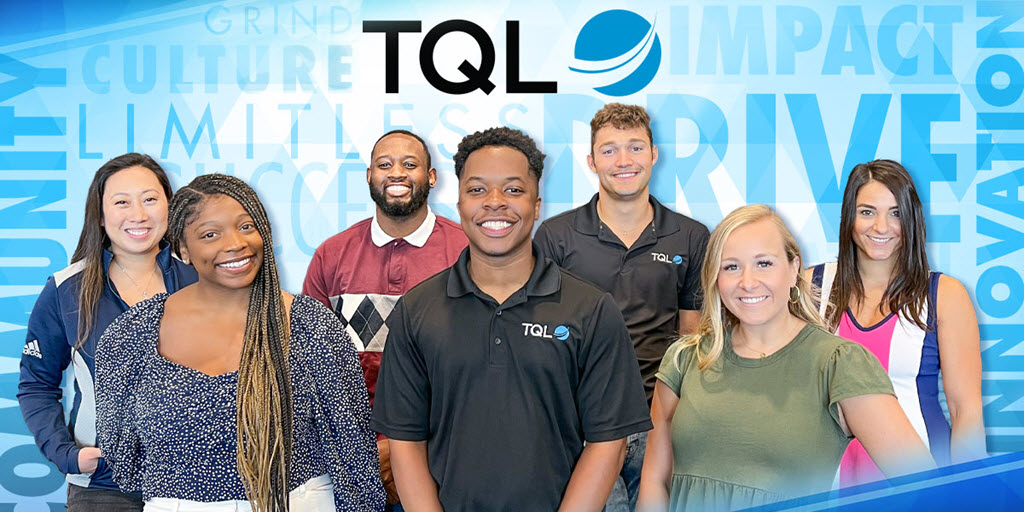
Iterations allow teams to refine their backlog, identify risks and fix them. The aim is to make each iteration better than the one before. Developers may modify existing features or create new ones. This process is repeated until the product is ready to be released.
Collaborative processes
The Agile Manifesto emphasizes the need for collaboration between business stakeholders and developers. This allows teams to prioritise work based upon business goals. A value stream is also promoted by lean processes. This is the complete list of actions that produces the product or service customers want. These two approaches are very similar, but they have key differences.
Agile is more flexible than Lean. Lean UX teams can work together, scale up quickly, or use rigid project management tools. Agile is a system which consists of small-world networks, deliverables, and other elements. It emphasizes autonomy, exploration, collaboration, and teamwork. An agile approach is required for scaling from one project to multiple projects.
User research is key to agile teams
Agile teams increasingly incorporate user research into their work processes. This mindset is becoming more common in product development. However, it's also spreading to other areas. As usability and user experiences become more important, teams realize the need to be flexible and fast in their research. To get user-centric research on the front line of development, agile teams are applying the agile mindset to research processes that connect to the product backlog.
It is also essential to make user research workflows simpler and more democratized. This is done by creating user research templates that can be used for testing purposes. These templates should answer most of the questions and cover all phases of product development. To ensure consistent results, teams can also take advantage of UX platforms that offer preloaded templates and automated workflows.
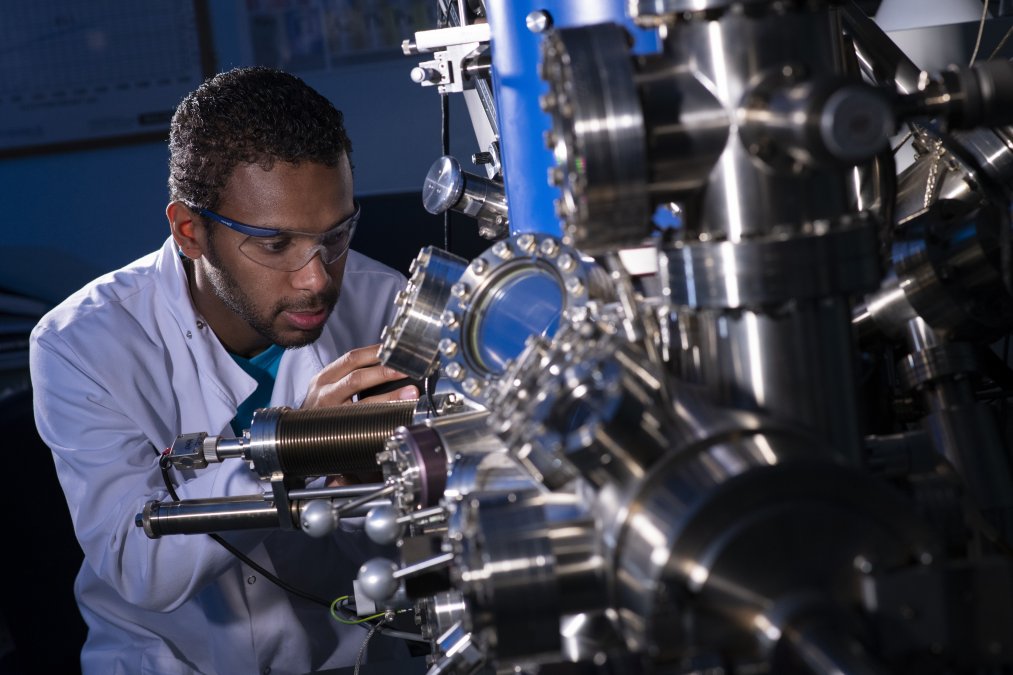
Creation of value
The idea of value generation is somewhat baffling, even though it seems to make sense. It is possible to create value with either a narrower scope or a more expansive one. But, in neither case is it completely binary. In some cases, a smaller scope produces less value and a greater scope generates more. But, it is possible to have a comprehensive scope.
Lean and agile are two different ways to deliver a better product to customers. Combining both these methods can help companies deliver a superior product quicker. These methods reduce overhead and empower employees to work together, focusing on the customer's needs.
FAQ
Can certain manufacturing steps be automated?
Yes! Since ancient times, automation has been in existence. The Egyptians created the wheel thousands years ago. Nowadays, we use robots for assembly lines.
There are many uses of robotics today in manufacturing. These include:
-
Assembly line robots
-
Robot welding
-
Robot painting
-
Robotics inspection
-
Robots create products
There are many other examples of how manufacturing could benefit from automation. For example, 3D printing allows us to make custom products without having to wait for weeks or months to get them manufactured.
What is the responsibility of a production planner?
A production planner makes sure all project elements are delivered on schedule, within budget, as well as within the agreed scope. They make sure that the product and services meet client expectations.
What are the logistics products?
Logistics is the process of moving goods from one point to another.
These include all aspects related to transport such as packaging, loading and transporting, storing, transporting, unloading and warehousing inventory management, customer service. Distribution, returns, recycling are some of the options.
Logisticians ensure that products reach the right destination at the right moment and under safe conditions. Logisticians help companies improve their supply chain efficiency by providing information about demand forecasts and stock levels, production schedules, as well as availability of raw materials.
They monitor shipments in transit, ensure quality standards, manage inventories, replenish orders, coordinate with suppliers and other vendors, and offer support services for sales, marketing, and customer service.
What is the best way to learn about manufacturing?
Hands-on experience is the best way to learn more about manufacturing. However, if that's not possible, you can always read books or watch educational videos.
What are the four types in manufacturing?
Manufacturing refers to the transformation of raw materials into useful products by using machines and processes. It includes many different activities like designing, building and testing, packaging, shipping and selling, as well as servicing.
What does manufacturing mean?
Manufacturing Industries are those businesses that make products for sale. Consumers are those who purchase these products. These companies use a variety processes such as distribution, retailing and management to accomplish their purpose. They manufacture goods from raw materials using machines and other equipment. This includes all types if manufactured goods.
Statistics
- [54][55] These are the top 50 countries by the total value of manufacturing output in US dollars for its noted year according to World Bank.[56] (en.wikipedia.org)
- In 2021, an estimated 12.1 million Americans work in the manufacturing sector.6 (investopedia.com)
- Job #1 is delivering the ordered product according to specifications: color, size, brand, and quantity. (netsuite.com)
- In the United States, for example, manufacturing makes up 15% of the economic output. (twi-global.com)
- It's estimated that 10.8% of the U.S. GDP in 2020 was contributed to manufacturing. (investopedia.com)
External Links
How To
Six Sigma in Manufacturing
Six Sigma is "the application statistical process control (SPC), techniques for continuous improvement." Motorola's Quality Improvement Department developed it at their Tokyo plant in Japan in 1986. The basic idea behind Six Sigma is to improve quality by improving processes through standardization and eliminating defects. Many companies have adopted Six Sigma in recent years because they believe that there are no perfect products and services. Six Sigma's primary goal is to reduce variation from the average value of production. If you take a sample and compare it with the average, you will be able to determine how much of the production process is different from the norm. If you notice a large deviation, then it is time to fix it.
Understanding the dynamics of variability within your business is the first step in Six Sigma. Once you understand this, you can then identify the causes of variation. Also, you will need to identify the sources of variation. Random variations happen when people make errors; systematic variations are caused externally. For example, if you're making widgets, and some of them fall off the assembly line, those would be considered random variations. It would be considered a systematic problem if every widget that you build falls apart at the same location each time.
Once you've identified where the problems lie, you'll want to design solutions to eliminate those problems. You might need to change the way you work or completely redesign the process. Test them again once you've implemented the changes. If they didn't work, then you'll need to go back to the drawing board and come up with another plan.