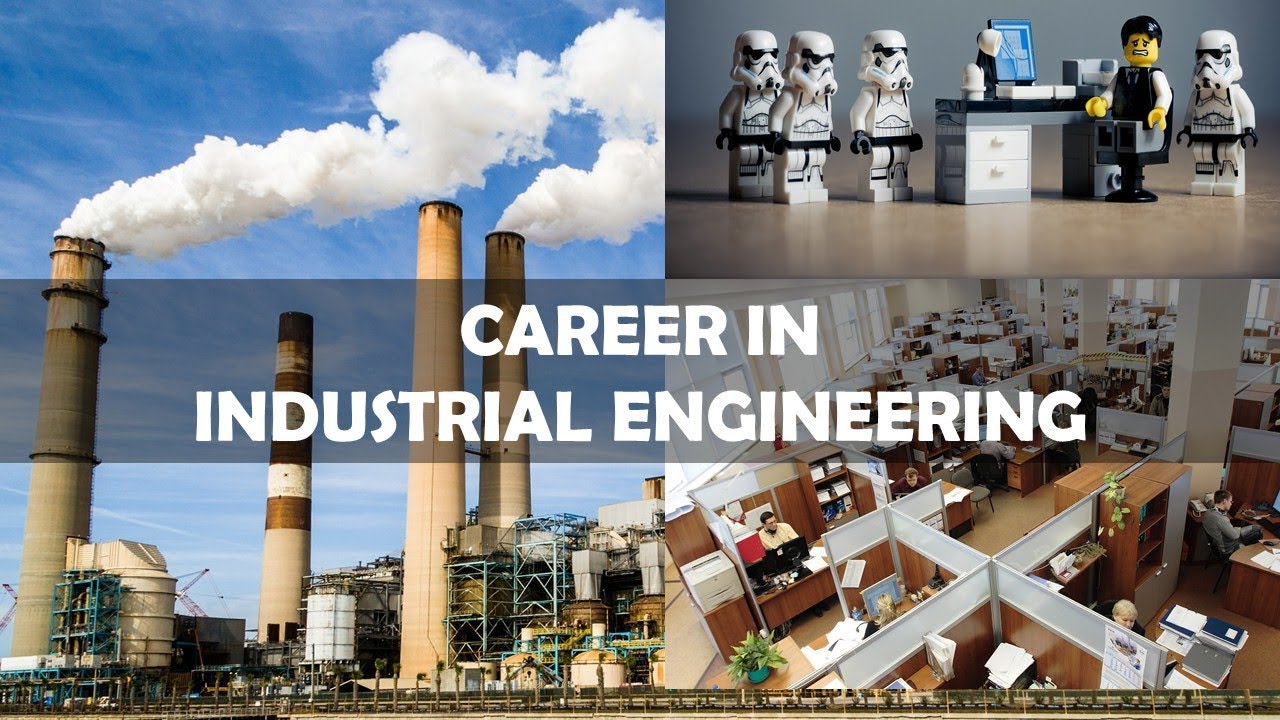
The Defense Industrial Base (DIB) is a network of more than 200,000 companies that supply goods and services to the Department of Defense. It includes startups, big corporations, small businesses. The Government Accountability Office released a report that highlighted the risks facing the DIB and its challenges in dealing with these threats.
Over the past 10 years, the defense industrial base has declined by nearly 40 percent. Accordingly, the Department of Defense is having difficulty recruiting new members to the sector. To address this issue, the Defense Department has tried a variety of efforts to encourage new businesses to participate. Despite these attempts, many smaller firms are being left behind. This has created a growing national security risk.
Diverse DOD offices are working on mitigation of risks in the DIB. However, there is no comprehensive strategy in place to assess and manage these risk. GAO conducted an analysis of several department reports and interviewed DOD representatives to determine where improvements could be made. Ultimately, GAO identified five elements that could help the department achieve its goals:
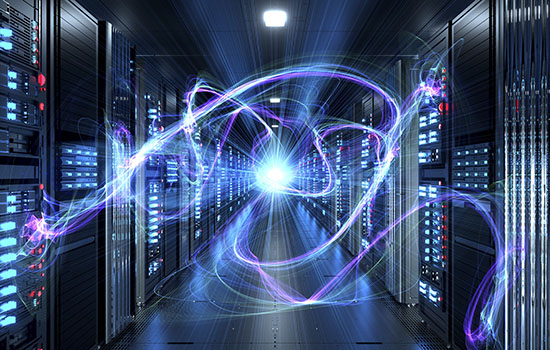
Loss or reduction of commercial suppliers is one concern. Many of these businesses provide parts for weapon systems used by the Pentagon. The number of small businesses in the industry has dwindled over the past decade, and there are not clear metrics on how many new companies are entering the market.
Material shortages and dependence on foreign suppliers are two other issues. Intellectual property restrictions often slow down the acquisition process for the military, as well as the lack of a standard definition of what constitutes a "new entry" to the defense industrial base.
GAO recommended that Defense review its policy regarding mitigating risk in the DIB. In addition, the department needs to continue to engage traditional defense contractors and implement tools that will make it easier for commercial technology providers to enter the DoD marketplace. These recommendations should be part of an overall strategy for addressing industrial base concerns.
The Defense Department should examine how its OTAs, CSOs, and other resources can be used to accelerate acquisition strategy development. The supply chain can be restructured to produce dynamic outcomes by using the right people and processes.
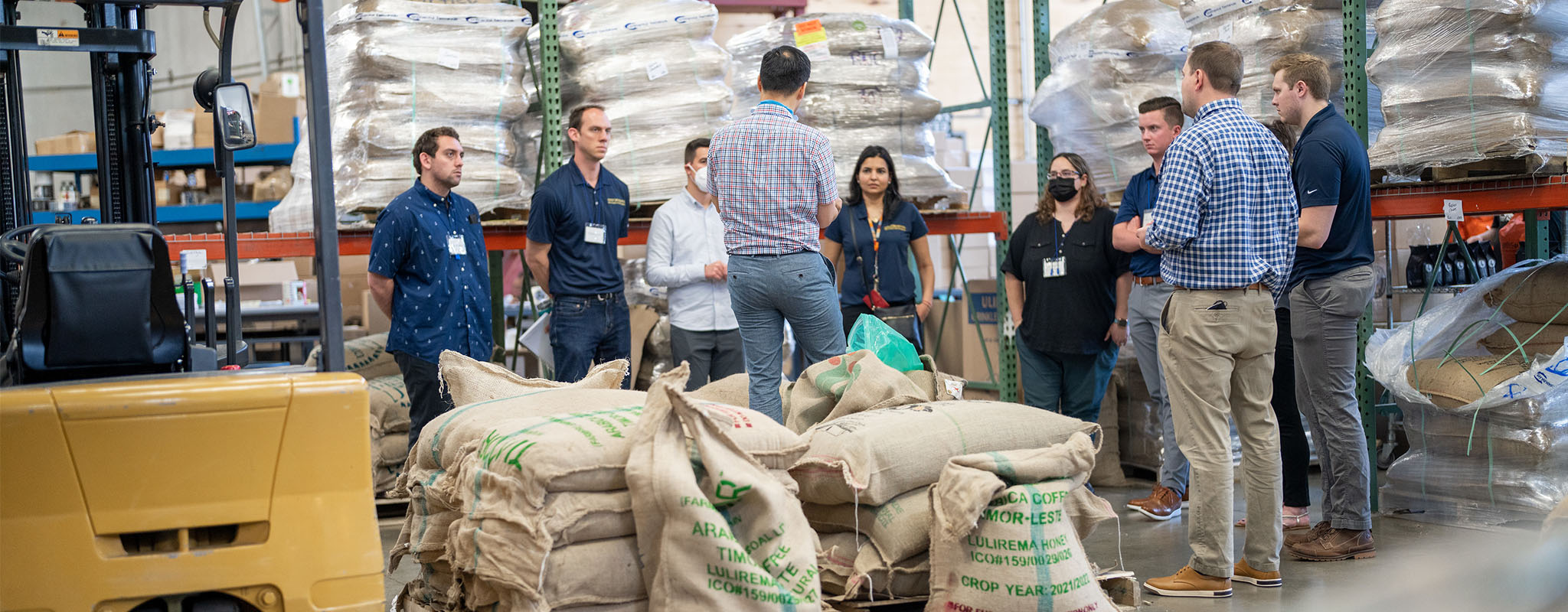
The number of new entrants to the defense industrial base has declined over the past decade, but the industry is still in development. Many companies aren’t familiar with the Federal Acquisition Regulations process (FAR). Additionally, small businesses might not have as many opportunities to compete with the larger companies in the current market.
Innovation is key for the defense industrial sector. Small businesses and startups play a crucial role. Resilient DIB members can help support National Security and allow the Department of Defense develop better military equipment.
The defense industrial base is complex and requires a comprehensive strategy in order to ensure that the resources are available for the military's needs. In the meantime, it is essential that the Department of Defense learn more about best practices for integrating technology into its business processes, which will allow for more efficient and innovative products and services.
FAQ
What skills does a production planner need?
To become a successful production planner, you need to be organized, flexible, and able to multitask. It is also important to be able communicate with colleagues and clients.
What are the 7 R's of logistics?
The acronym 7R's of Logistic is an acronym that stands for seven fundamental principles of logistics management. It was developed by the International Association of Business Logisticians (IABL) and published in 2004 as part of its "Seven Principles of Logistics Management" series.
The acronym consists of the following letters:
-
Responsible - to ensure that all actions are within the legal requirements and are not detrimental to others.
-
Reliable - have confidence in the ability to deliver on commitments made.
-
Use resources effectively and sparingly.
-
Realistic - consider all aspects of operations, including cost-effectiveness and environmental impact.
-
Respectful - Treat people fairly and equitably
-
Reliable - Find ways to save money and increase your productivity.
-
Recognizable - provide customers with value-added services.
What does it take to run a logistics business?
To be a successful businessman in logistics, you will need many skills and knowledge. Effective communication skills are necessary to work with suppliers and clients. You should be able analyse data and draw inferences. You must be able to work well under pressure and handle stressful situations. To improve efficiency, you must be innovative and creative. You will need strong leadership skills to motivate and direct your team members towards achieving their organizational goals.
It is important to be organized and efficient in order to meet tight deadlines.
How can manufacturing reduce production bottlenecks?
To avoid production bottlenecks, ensure that all processes run smoothly from the moment you receive your order to the time the product ships.
This includes planning for capacity requirements as well as quality control measures.
This can be done by using continuous improvement techniques, such as Six Sigma.
Six Sigma is a management system used to improve quality and reduce waste in every aspect of your organization.
It focuses on eliminating variation and creating consistency in your work.
Statistics
- In 2021, an estimated 12.1 million Americans work in the manufacturing sector.6 (investopedia.com)
- Job #1 is delivering the ordered product according to specifications: color, size, brand, and quantity. (netsuite.com)
- In the United States, for example, manufacturing makes up 15% of the economic output. (twi-global.com)
- It's estimated that 10.8% of the U.S. GDP in 2020 was contributed to manufacturing. (investopedia.com)
- (2:04) MTO is a production technique wherein products are customized according to customer specifications, and production only starts after an order is received. (oracle.com)
External Links
How To
How to use the Just-In Time Method in Production
Just-intime (JIT), a method used to lower costs and improve efficiency in business processes, is called just-in-time. It's a way to ensure that you get the right resources at just the right time. This means that your only pay for the resources you actually use. Frederick Taylor first coined this term while working in the early 1900s as a foreman. He noticed that workers were often paid overtime when they had to work late. He concluded that if workers were given enough time before they start work, productivity would increase.
JIT is about planning ahead. You should have all the necessary resources ready to go so that you don’t waste money. It is important to look at your entire project from beginning to end and ensure that you have enough resources to handle any issues that may arise. You will have the resources and people to solve any problems you anticipate. This will prevent you from spending extra money on unnecessary things.
There are many types of JIT methods.
-
Demand-driven JIT: You order the parts and materials you need for your project every other day. This will allow you to track how much material you have left over after using it. This will allow to you estimate the time it will take for more to be produced.
-
Inventory-based: This is a type where you stock the materials required for your projects in advance. This allows you to forecast how much you will sell.
-
Project-driven: This is an approach where you set aside enough funds to cover the cost of your project. You will be able to purchase the right amount of materials if you know what you need.
-
Resource-based JIT: This is the most popular form of JIT. Here, you allocate certain resources based on demand. If you have many orders, you will assign more people to manage them. If you don't receive many orders, then you'll assign fewer employees to handle the load.
-
Cost-based: This approach is very similar to resource-based. However, you don't just care about the number of people you have; you also need to consider how much each person will cost.
-
Price-based: This is a variant of cost-based. However, instead of focusing on the individual workers' costs, this looks at the total price of the company.
-
Material-based: This is quite similar to cost-based, but instead of looking at the total cost of the company, you're concerned with how much raw materials you spend on average.
-
Time-based: This is another variation of resource-based JIT. Instead of focusing only on how much each employee is costing, you should focus on how long it takes to complete your project.
-
Quality-based JIT - This is another form of resource-based JIT. Instead of thinking about how much each employee costs or how long it takes to manufacture something, you think about how good the quality of your product is.
-
Value-based JIT is the newest form of JIT. In this instance, you are not concerned about the product's performance or meeting customer expectations. Instead, you focus on the added value that you provide to your market.
-
Stock-based: This inventory-based approach focuses on how many items are being produced at any one time. It's used when you want to maximize production while minimizing inventory.
-
Just-in-time (JIT) planning: This is a combination of JIT and supply chain management. This refers to the scheduling of the delivery of components as soon after they are ordered. It's important because it reduces lead times and increases throughput.