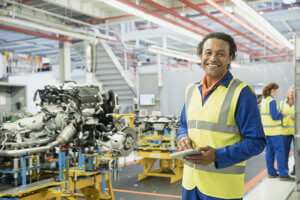
Despite the numerous benefits of lean manufacturing, a number of companies have faced challenges in implementing this strategy. Companies must develop a plan to overcome these challenges. Companies who have implemented Lean found three main problems that hamper the success rate of the initiative.
Whatever the company's size, it is essential that they are committed to lean manufacturing. Although there is no way to know how committed a company to lean manufacturing, it is essential that they educate their employees on the new corporate culture.
It is also crucial to ensure that resources get allocated correctly. Many public organizations have found that they are wasting allocated budgets on items that are not necessary. Some managers have also been reported to purchase equipment that is not needed in order to use the budget. This can create operational bottlenecks, leading to an inefficient implementation of lean manufacturing.
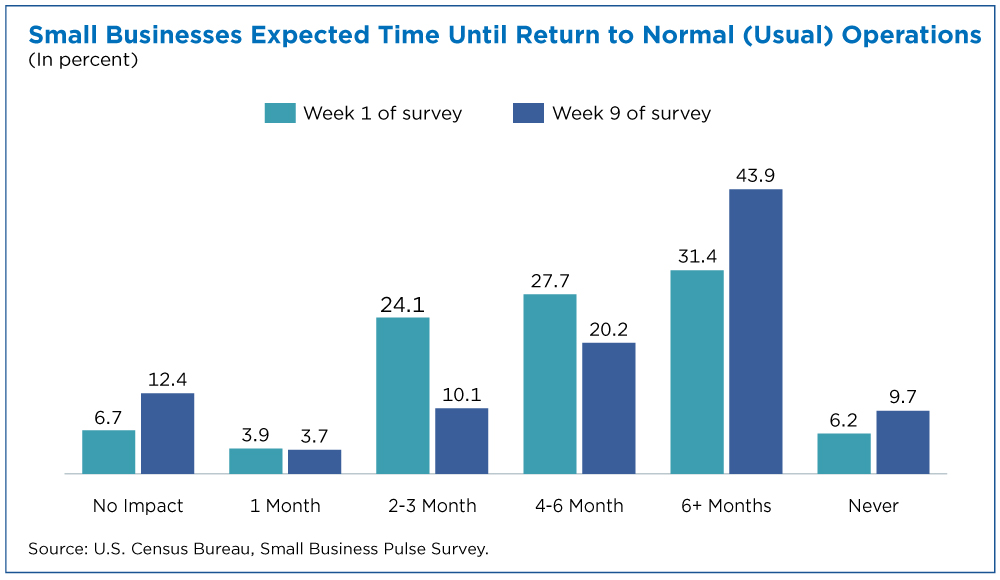
One of the biggest challenges in implementing lean manufacturing is resistance to cultural change. Many employees are uncomfortable with change, particularly those who have been working in the company for a while. Some employees may wait to hear the majority's support before they make the change. Management must explain the benefits of the program to employees and why they are necessary for the change to be successful.
The lack of a plan for strategic transformation is another significant problem. Although companies often manage multiple business operations at once it is essential to develop a long-term strategy. This strategy allows companies to identify and mentor future leaders, ensure competitiveness in the face of technological advancements, and continue to improve operations. It can also help identify and resolve operational bottlenecks as well as identify growth opportunities.
It is vital to train workers to overcome resistance. Proper training will help workers understand their responsibilities, and what they should expect. Workers also learn multi-skills that they can use to be more independent. Workers also learn problem solving skills through training, which can help them maintain Lean through performance improvements.
Managers must be open with workers in order to overcome resistance. Managers may try to force workers to follow their instructions but they must also explain why it is necessary. In some cases, managers have been found giving workers incorrect instructions, which led to ineffective implementation.
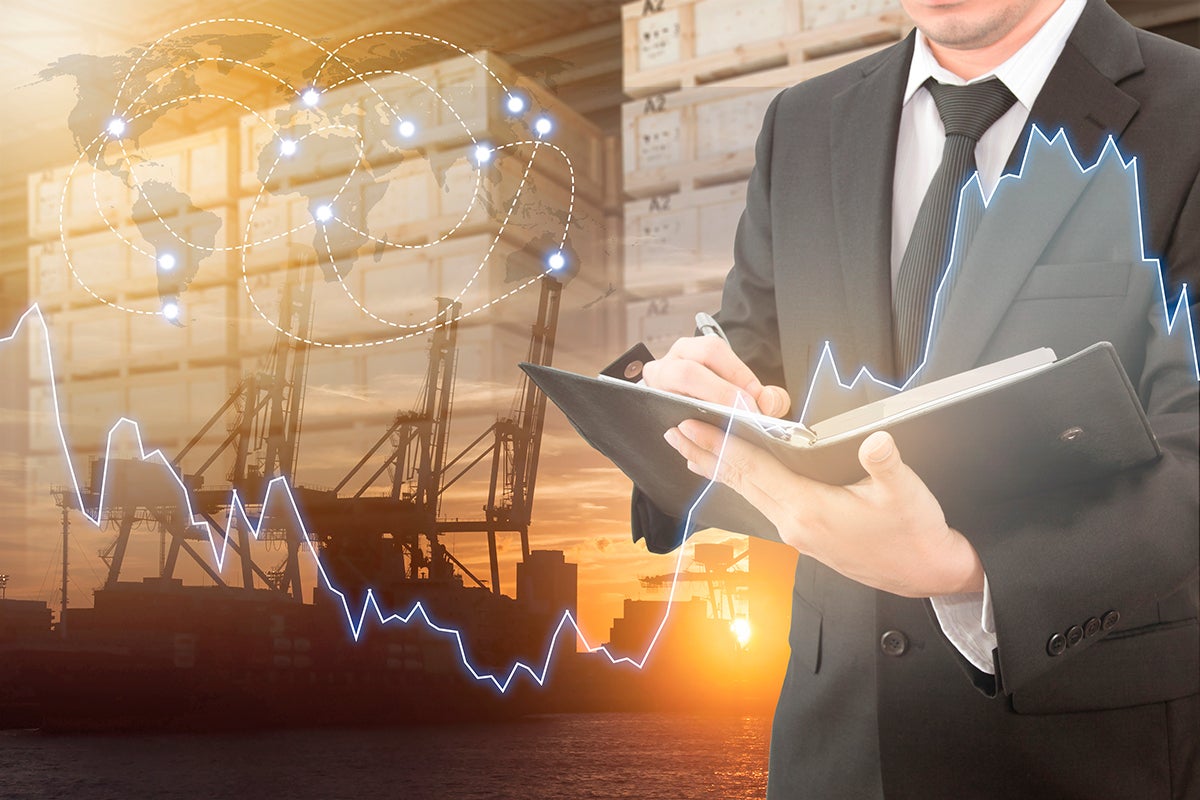
Managers need to be present at work, no matter how large or small the company. They can identify the areas where improvements can be made. They should also design and implement structured training programs for staff, as well as introduce digital tools to their work environment. These tools such as 5S improve visual management.
It is vital to create and communicate a clear vision regarding the implementation of lean manufacturing. This vision should include the responsibilities for employees, a schedule and a method of measuring success.
FAQ
Can certain manufacturing steps be automated?
Yes! Yes! Automation has existed since ancient times. The wheel was invented by the Egyptians thousands of years ago. Robots are now used to assist us in assembly lines.
There are many uses of robotics today in manufacturing. These include:
-
Automated assembly line robots
-
Robot welding
-
Robot painting
-
Robotics inspection
-
Robots that make products
Automation could also be used to improve manufacturing. 3D printing makes it possible to produce custom products in a matter of days or weeks.
What is production plan?
Production Planning is the creation of a plan to cover all aspects, such as scheduling, budgeting. Location, crew, equipment, props and other details. It is important to have everything ready and planned before you start shooting. It should also provide information about how best to produce the best results while on set. It should include information about shooting locations, casting lists, crew details, equipment requirements, and shooting schedules.
The first step is to decide what you want. You might have an idea of where you want to film, or you may have specific locations or sets in mind. Once you have identified your locations and scenes it's time to begin figuring out what elements you will need for each one. If you decide you need a car and don't know what model to choose, this could be an example. To narrow your options, you can search online for available models.
Once you have found the right car, you can start thinking about extras. What about additional seating? Or maybe you just need someone to push the car around. Perhaps you would like to change the interior colour from black to white. These questions can help you decide the right look for your car. It is also worth considering the types of shots that you wish to take. Will you be filming close-ups or wide angles? Maybe the engine or steering wheel is what you are looking to film. These things will help you to identify the car that you are looking for.
Once you have all the information, you are ready to create a plan. You can use a schedule to determine when and where you need it to be shot. You will need to know when you have to be there, what time you have to leave and when your return home. Everyone knows exactly what they should do and when. Hire extra staff by booking them ahead of time. You should not hire anyone who doesn't show up because of your inaction.
Also, consider how many days you will be filming your schedule. Some projects may only take a couple of days, while others could last for weeks. When you are creating your schedule, you should always keep in mind whether you need more than one shot per day or not. Multiple shots at the same location can increase costs and make it more difficult to complete. It's better to be safe than sorry and shoot less takes if you're not certain whether you need more takes.
Budgeting is another important aspect of production planning. You will be able to manage your resources if you have a realistic budget. If you have to reduce your budget due to unexpected circumstances, you can always lower it later. However, it is important not to overestimate the amount that you will spend. If you underestimate how much something costs, you'll have less money to pay for other items.
Production planning can be a complex process. However, once you know how everything works together it will become easier to plan future projects.
What do we need to know about Manufacturing Processes in order to learn more about Logistics?
No. It doesn't matter if you don't know anything about manufacturing before you learn about logistics. But, being familiar with manufacturing processes will give you a better understanding about how logistics works.
Statistics
- According to the United Nations Industrial Development Organization (UNIDO), China is the top manufacturer worldwide by 2019 output, producing 28.7% of the total global manufacturing output, followed by the United States, Japan, Germany, and India.[52][53] (en.wikipedia.org)
- In the United States, for example, manufacturing makes up 15% of the economic output. (twi-global.com)
- According to a Statista study, U.S. businesses spent $1.63 trillion on logistics in 2019, moving goods from origin to end user through various supply chain network segments. (netsuite.com)
- It's estimated that 10.8% of the U.S. GDP in 2020 was contributed to manufacturing. (investopedia.com)
- In 2021, an estimated 12.1 million Americans work in the manufacturing sector.6 (investopedia.com)
External Links
How To
Six Sigma in Manufacturing
Six Sigma is defined as "the application of statistical process control (SPC) techniques to achieve continuous improvement." Motorola's Quality Improvement Department in Tokyo, Japan developed Six Sigma in 1986. Six Sigma is a method to improve quality through standardization and elimination of defects. Many companies have adopted Six Sigma in recent years because they believe that there are no perfect products and services. Six Sigma aims to reduce variation in the production's mean value. It is possible to measure the performance of your product against an average and find the percentage of time that it differs from the norm. If this deviation is too big, you know something needs fixing.
Understanding how variability works in your company is the first step to Six Sigma. Once you understand that, it is time to identify the sources of variation. You'll also want to determine whether these variations are random or systematic. Random variations are caused by human errors. Systematic variations can be caused by outside factors. You could consider random variations if some widgets fall off the assembly lines. However, if you notice that every time you assemble a widget, it always falls apart at exactly the same place, then that would be a systematic problem.
Once you have identified the problem, you can design solutions. The solution could involve changing how you do things, or redesigning your entire process. After implementing the new changes, you should test them again to see if they worked. If they fail, you can go back to the drawing board to come up with a different plan.