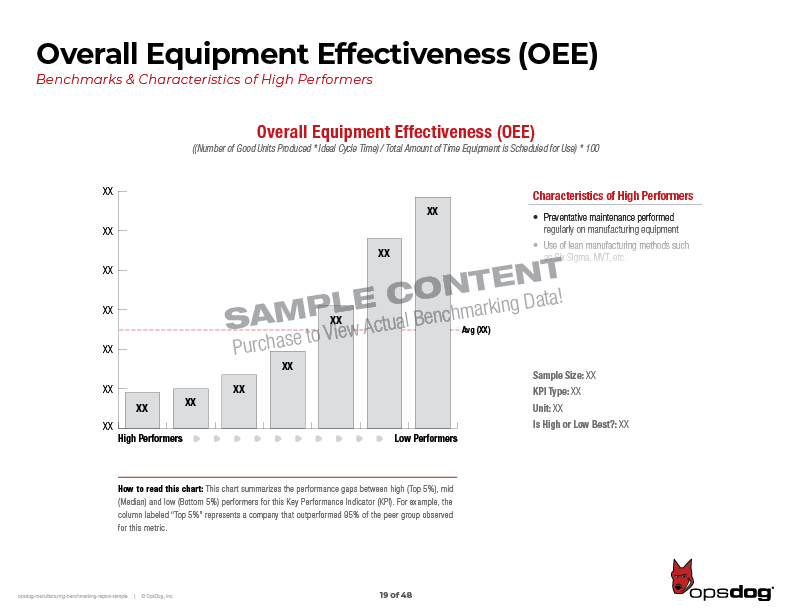
DFSS (Design for Six Sigma) is a design methodology that uses a number of techniques to design a product, service, or process. It's designed to decrease waste, increase quality, and increase market share. This is a powerful method that will help you improve the quality of your products and services.
DFSS is a process that takes customer needs into account throughout the design process. This ensures that the product or service you are designing is the best fit for your customer's needs. It also ensures that your product has a high level of quality when it is introduced to the market. DFSS is used often to design a product/service from scratch. It is also used to design products and services that replace existing products or services.
The DFSS team begins by determining what the customer needs. This could include collecting information about existing processes, interviewing customers and surveying customers. The design team will then assess alternative products and designs in order to determine the best fit. This phase also includes developing substitute concepts and classifying functional needs. The phase could include additional steps depending on the project's complexity.
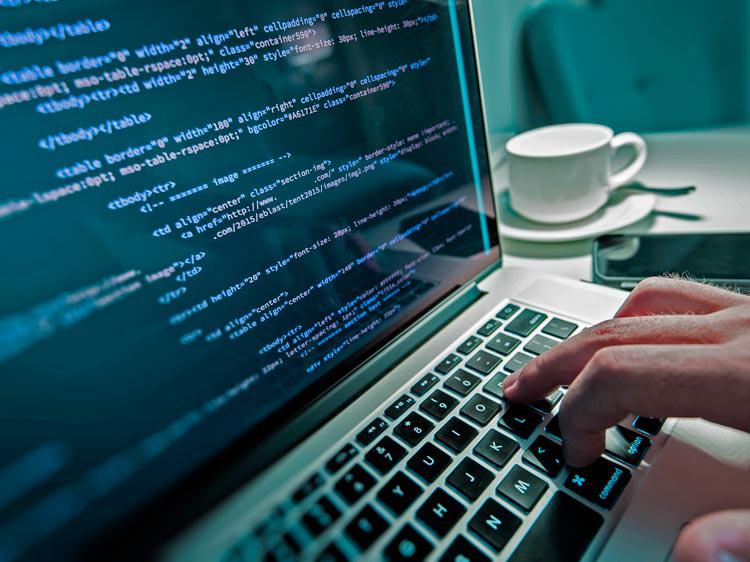
DFSS is a design methodology that helps companies design products and services efficiently and effectively. It helps to spot potential problems before they become major issues. It will also reduce waste and increase your company's profitability. It's designed to enhance the effectiveness and efficiency of a product or service through identifying process parameters that can make it more effective.
There are many ways to implement DFSS. DMADV is the most popular method. It involves a five-step process. It starts with defining the customer, identifying their needs, and developing a design concept. This methodology has a strong engineering foundation and is often used in the development of completely new products and services. This includes a measurement phase and an analysis phase to determine the product's effectiveness.
The second phase involves the optimization step. This involves evaluating performance of the product across multiple performance levels. This step is especially useful in developing new business procedures. This stage's goal is to reduce variation and ensure product stability over time.
The final stage involves the verification stage, which is often used to ensure that the product is stable. This stage also validates that the product is capable of performing over time. This step will also include validation testing. This step is usually completed after the design has been validated.
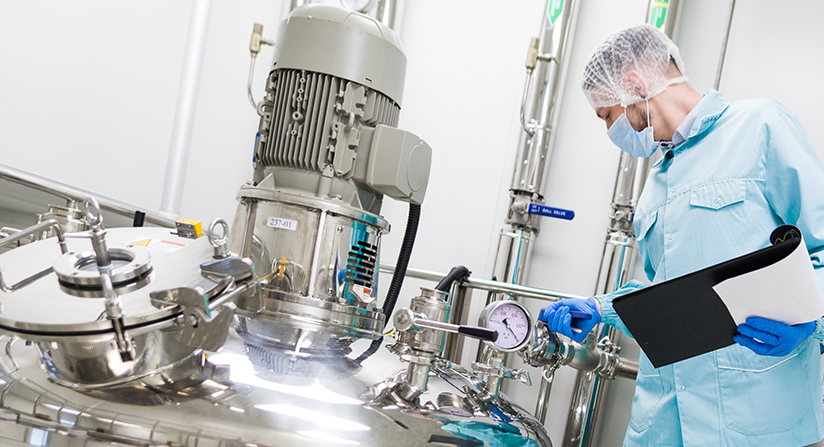
In order to successfully implement DFSS, you need to have a detailed process map that shows the different workflows involved in the design process. It should include details about resources, timelines and milestones. It is also important to be able identify any external involvement. To ensure the product meets customer needs, you may need to create a prototype. Implementing DFSS in an environment with clear rewards is a great way to achieve the project's goals.
FAQ
What is the responsibility for a logistics manager
A logistics manager ensures that all goods are delivered on time and without damage. This is done through his/her expertise and knowledge about the company's product range. He/she should make sure that enough stock is on hand to meet the demands.
How can overproduction in manufacturing be reduced?
Improved inventory management is the key to reducing overproduction. This would decrease the time that is spent on inefficient activities like purchasing, storing, or maintaining excess stock. We could use these resources to do other productive tasks.
Kanban systems are one way to achieve this. A Kanban board can be used to monitor work progress. Kanban systems allow work items to move through different states until they reach their final destination. Each state represents a different priority level.
To illustrate, work can move from one stage or another when it is complete enough for it to be moved to a new stage. However, if a task is still at the beginning stages, it will remain so until it reaches the end of the process.
This helps to keep work moving forward while ensuring that no work is left behind. Managers can see how much work has been done and the status of each task at any time with a Kanban Board. This allows them the ability to adjust their workflow using real-time data.
Lean manufacturing can also be used to reduce inventory levels. Lean manufacturing works to eliminate waste throughout every stage of the production chain. Anything that doesn't add value to the product is considered waste. These are some of the most common types.
-
Overproduction
-
Inventory
-
Unnecessary packaging
-
Material surplus
Manufacturers can reduce their costs and improve their efficiency by using these ideas.
What types of jobs can you find in logistics
There are many kinds of jobs available within logistics. Some of them are:
-
Warehouse workers – They load, unload and transport pallets and trucks.
-
Transportation drivers – They drive trucks or trailers to transport goods and perform pick-ups.
-
Freight handlers - They sort and pack freight in warehouses.
-
Inventory managers - These are responsible for overseeing the stock of goods in warehouses.
-
Sales reps are people who sell products to customers.
-
Logistics coordinators – They plan and coordinate logistics operations.
-
Purchasing agents - They buy goods and services that are necessary for company operations.
-
Customer service representatives - Answer calls and email from customers.
-
Shipping clerks: They process shipping requests and issue bills.
-
Order fillers are people who fill orders based only on what was ordered.
-
Quality control inspectors are responsible for inspecting incoming and outgoing products looking for defects.
-
Others - There are many other types of jobs available in logistics, such as transportation supervisors, cargo specialists, etc.
How important is automation in manufacturing?
Automating is not just important for manufacturers, but also for service providers. They can provide services more quickly and efficiently thanks to automation. They can also reduce their costs by reducing human error and improving productivity.
What does manufacturing mean?
Manufacturing Industries is a group of businesses that produce goods for sale. Consumers are those who purchase these products. These companies use a variety processes such as distribution, retailing and management to accomplish their purpose. They make goods from raw materials with machines and other equipment. This includes all types and varieties of manufactured goods, such as food items, clothings, building supplies, furnitures, toys, electronics tools, machinery vehicles, pharmaceuticals medical devices, chemicals, among others.
What is the role of a production manager?
A production planner ensures all aspects of the project are delivered on time, within budget, and within scope. They also ensure the quality of the product and service meets the client's requirements.
Statistics
- Many factories witnessed a 30% increase in output due to the shift to electric motors. (en.wikipedia.org)
- According to the United Nations Industrial Development Organization (UNIDO), China is the top manufacturer worldwide by 2019 output, producing 28.7% of the total global manufacturing output, followed by the United States, Japan, Germany, and India.[52][53] (en.wikipedia.org)
- In 2021, an estimated 12.1 million Americans work in the manufacturing sector.6 (investopedia.com)
- You can multiply the result by 100 to get the total percent of monthly overhead. (investopedia.com)
- [54][55] These are the top 50 countries by the total value of manufacturing output in US dollars for its noted year according to World Bank.[56] (en.wikipedia.org)
External Links
How To
Six Sigma: How to Use it in Manufacturing
Six Sigma can be described as "the use of statistical process control (SPC), techniques to achieve continuous improvement." Motorola's Quality Improvement Department in Tokyo, Japan developed Six Sigma in 1986. The basic idea behind Six Sigma is to improve quality by improving processes through standardization and eliminating defects. In recent years, many companies have adopted this method because they believe there is no such thing as perfect products or services. Six Sigma's primary goal is to reduce variation from the average value of production. You can calculate the percentage of deviation from the norm by taking a sample of your product and comparing it to the average. If it is too large, it means that there are problems.
Understanding the nature of variability in your business is the first step to Six Sigma. Once you've understood that, you'll want to identify sources of variation. It is important to identify whether the variations are random or systemic. Random variations are caused by human errors. Systematic variations can be caused by outside factors. Random variations would include, for example, the failure of some widgets to fall from the assembly line. It would be considered a systematic problem if every widget that you build falls apart at the same location each time.
Once you identify the problem areas, it is time to create solutions. That solution might involve changing the way you do things or redesigning the process altogether. To verify that the changes have worked, you need to test them again. If they don’t work, you’ll need to go back and rework the plan.