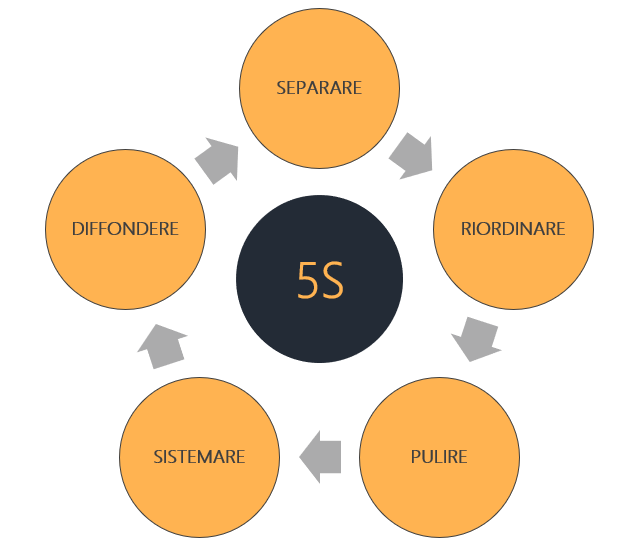
Visual management involves the transmission of information via visual signals. This method increases efficiency and clarity by recognizing information immediately. There are many visual control methods, such as process control charts, FIFO lanes, and Lean daily manager board. These are just a few of the most commonly used examples. Also, you can read more about visual control in Lean manufacturing. Continue reading for more information. This is a great way for your company to adopt lean manufacturing.
Lean manufacturing
Andon is a Japanese term for status-display visualization. It is one of many methods for visual management in lean manufacturing. This technique allows supervisors and workers alike to see work-in progress, process flow, or any other pertinent information. Visual management also allows for simple labeling of workspaces, materials, parts, finished goods, and waste. It can help identify inefficiencies, streamline processes and improve efficiency. These are just a few of the benefits that visual management can bring to lean manufacturing.
Visible tools for visual management are a crucial component of the Lean methodology. Clear visual signals enable supervisors to spot waste, improve flow, and avoid making mistakes. It can also reduce safety risks. Floor markings and other visual indicators help forklift drivers to stay in the right areas. Visual management can help workers work more efficiently in lean manufacturing. In addition to reducing waste, visual management also minimizes safety risks.
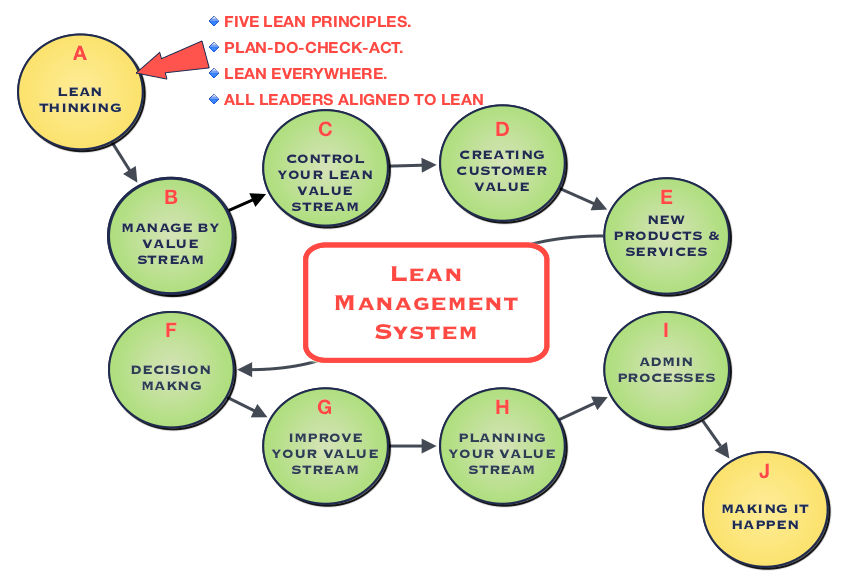
Process control charts
Process control charts can be a useful tool to visualize performance metrics and set a baseline for future enhancements. They also help improve output. They help management, operators, and other stakeholders get on the same page by identifying common causes of variation and setting the correct path for improvement. Because of their unusual patterns of variation, these charts can be very useful in identifying out-of-control processes. Process control charts are great for visual management. These charts are easy-to-create and can be used visually to monitor the status of any processes or systems.
The primary function of a control chart is to track process performance over time. These charts provide information about the sequence of measurements and samples taken. Managers can see if the process remains stable or not. These charts can also be used as an analytical tool to spot potential problems and offer solutions. A line segment is a segment that connects the centerline of a control chart. This allows an operator to easily compare the process's performance to its baseline. The control limits typically have three standard deviations above or below the centerline.
FIFO lane
FIFO lanes are a way to increase system throughput and utilization. Take a look at a production line or counter that sells fast food. It is likely that you have felt the frustration of having to wait in long lines for something. The FiFo lane is a visual management tool that helps you control the flow of work. It establishes priority in queues and allows for visual management. You can define these lanes by placing painted lines on the floor, markings on roller conveyors, and clearly marked shelf spaces. The first job that arrives from Process A would be placed in the first FIFO lane position. The next job would go into the open position.
Implementing time registration can be a great way to improve FIFO lane visual organization. Employees can track the date and time that carts are placed in a FIFO lane by recording the time and date. Some employees use digital clocks for counting the products as soon as they are placed in the FIFO lane. Whiteboard stickers can be used to record times on carts. These stickers can be used by downstream employees to write down times on carts.
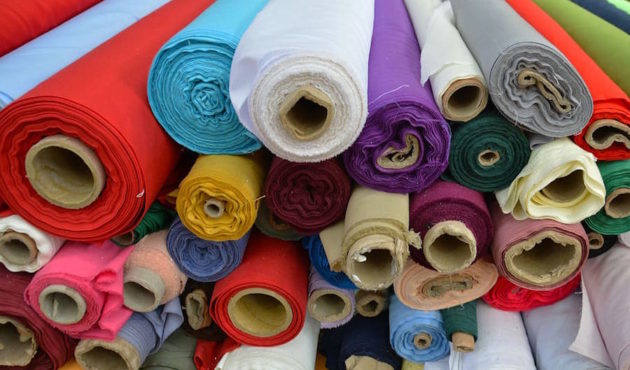
Lean daily management board
The Lean Daily Management Board was established by a multidisciplinary team that was based upon five predetermined metrics. They were: patient outcomes and documentation adherence, employee engagement, productivity, and employee engagement. Each day, this team met to assess progress in each area. To verify every daily activity, the team used a checklist. The team also used a problem solving tool in order to address any potential fallouts. In January 2014, the initial data showed a 75% medication scan rate and a fall rate at 1.32/1000 patient-days. These data are not applicable to patient care and continuing education.
Instead of simply looking at a company's performance over time, daily managing makes it visible. Managers can then respond to problems as soon as they happen. Poor performers are able to stretch their work in order to not be asked to do more. The poor performers need to be aware of the extra effort and time they spend on their work by making stretching work visible. While daily management isn't meant to be punitive, it does highlight any processes that may be inefficient or ineffective. People should be able to point out the failure of a process.
FAQ
What does it take to run a logistics business?
You need to have a lot of knowledge and skills to manage a successful logistic business. Effective communication skills are necessary to work with suppliers and clients. You need to understand how to analyze data and draw conclusions from it. You must be able manage stress and pressure under pressure. In order to innovate and create new ways to improve efficiency, creativity is essential. You need to have strong leadership qualities to motivate team members and direct them towards achieving organizational goals.
You must be organized to meet tight deadlines.
What does manufacturing mean?
Manufacturing Industries are companies that manufacture products. Consumers are the people who purchase these products. These companies use various processes such as production, distribution, retailing, management, etc., to fulfill this purpose. They produce goods from raw materials by using machines and other machinery. This covers all types of manufactured goods including clothing, food, building supplies and furniture, as well as electronics, tools, machinery, vehicles and pharmaceuticals.
What skills does a production planner need?
Production planners must be flexible, organized, and able handle multiple tasks. Communication skills are essential to ensure that you can communicate effectively with clients, colleagues, and customers.
What do we need to know about Manufacturing Processes in order to learn more about Logistics?
No. No. But, being familiar with manufacturing processes will give you a better understanding about how logistics works.
How can manufacturing efficiency improved?
First, we need to identify which factors are most critical in affecting production times. We must then find ways that we can improve these factors. If you don't know where to start, then think about which factor(s) have the biggest impact on production time. Once you have identified the factors, then try to find solutions.
Are there ways to automate parts of manufacturing?
Yes! Since ancient times, automation has been in existence. The Egyptians created the wheel thousands years ago. Robots are now used to assist us in assembly lines.
Robotics is used in many manufacturing processes today. They include:
-
Robots for assembly line
-
Robot welding
-
Robot painting
-
Robotics inspection
-
Robots that produce products
There are many other examples of how manufacturing could benefit from automation. 3D printing makes it possible to produce custom products in a matter of days or weeks.
Statistics
- [54][55] These are the top 50 countries by the total value of manufacturing output in US dollars for its noted year according to World Bank.[56] (en.wikipedia.org)
- In 2021, an estimated 12.1 million Americans work in the manufacturing sector.6 (investopedia.com)
- According to the United Nations Industrial Development Organization (UNIDO), China is the top manufacturer worldwide by 2019 output, producing 28.7% of the total global manufacturing output, followed by the United States, Japan, Germany, and India.[52][53] (en.wikipedia.org)
- (2:04) MTO is a production technique wherein products are customized according to customer specifications, and production only starts after an order is received. (oracle.com)
- Job #1 is delivering the ordered product according to specifications: color, size, brand, and quantity. (netsuite.com)
External Links
How To
Six Sigma: How to Use it in Manufacturing
Six Sigma refers to "the application and control of statistical processes (SPC) techniques in order to achieve continuous improvement." Motorola's Quality Improvement Department in Tokyo, Japan developed Six Sigma in 1986. Six Sigma's basic concept is to improve quality and eliminate defects through standardization. Since there are no perfect products, or services, this approach has been adopted by many companies over the years. Six Sigma's main objective is to reduce variations from the production average. If you take a sample and compare it with the average, you will be able to determine how much of the production process is different from the norm. If it is too large, it means that there are problems.
Understanding the dynamics of variability within your business is the first step in Six Sigma. Once you have this understanding, you will need to identify sources and causes of variation. These variations can also be classified as random or systematic. Random variations occur when people do mistakes. Symmetrical variations are caused due to factors beyond the process. Random variations would include, for example, the failure of some widgets to fall from the assembly line. If however, you notice that each time you assemble a widget it falls apart in exactly the same spot, that is a problem.
After identifying the problem areas, you will need to devise solutions. The solution could involve changing how you do things, or redesigning your entire process. After implementing the new changes, you should test them again to see if they worked. If they don't work you need to rework them and come up a better plan.