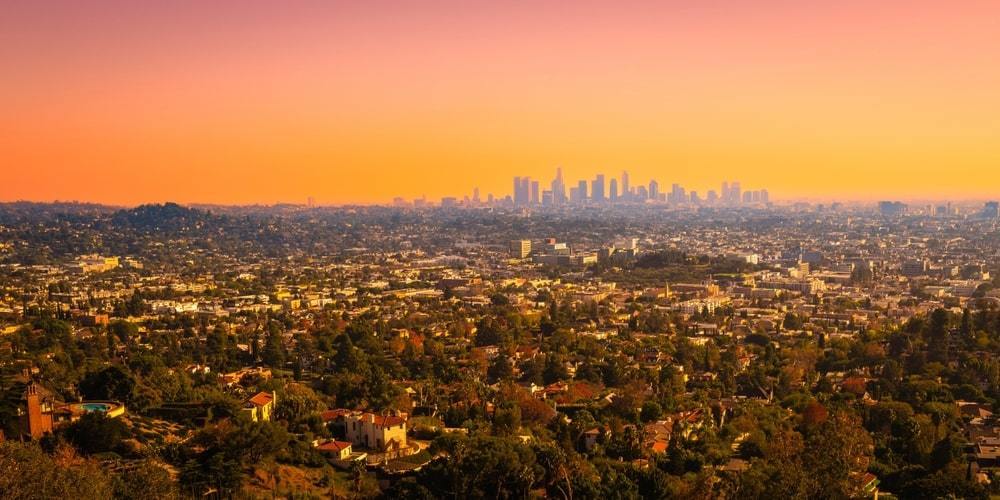
Flow refers to the state where all steps of a production cycle follow each other without interruption. Every step adds value to the product, and goods meander through the production process without being impeded. In many companies, the production of a specific quantity of stock is planned out so that production orders can be fulfilled as efficiently as possible. This is Lean Manufacturing's push production. Here are some key elements to flow:
Just-in-time manufacturing
When lean manufacturing was first introduced to the U.S. in the late 1970s, "just-in-time" manufacturing was the dominant paradigm. The concept isn't the best way to run a business, but it has its advantages. The process of reducing costs and increasing efficiency requires many new skills and mindsets. If you want to reap the full rewards, however, it is worthwhile.
Standardizing production processes and working in smaller batches are key aspects of just-in time manufacturing. It is crucial to have a well-planned facility layout in order to promote a just-in time mindset. For example, cellular manufacturing can help to support production flow. Cellular manufacturing can organize parts bins and workstations in a way that facilitates the flow of materials. Just-in-time producers should avoid lengthy changeovers.
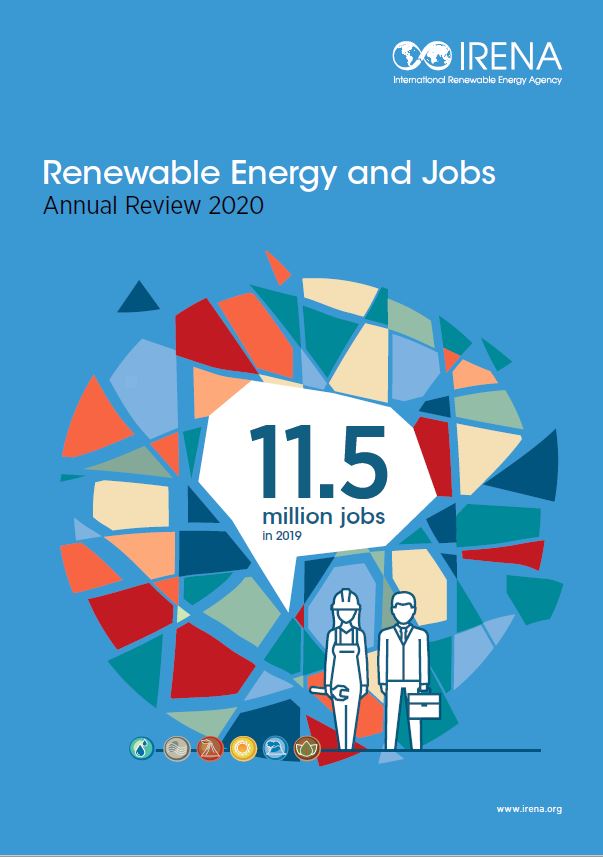
Standardized work
Before you can apply lean manufacturing to manufacturing, you need to first create standard work. This system of work places emphasis on the workers involved in the production process. This refers to the ongoing improvement of the system through kaizen. Standardized work documents are the responsibility of the cell leader and are updated when takt time changes. Standardized work documentation provides a base for improvement activities, including kaizen and improvement activities.
Organizations can improve their productivity as well as service quality by having standard work processes. They help to reduce product development and human error. As people have a better understanding of the process, this helps the organization solve problems faster. This allows the company to improve its customer service and implement continuous improvement. Once standardized, it is not difficult to implement these processes in a company. A mission statement is a great idea.
Continuous improvement
Lean principles encourage continuous improvement and provide a variety of benefits. These benefits are often additive but there is one thread that ties them all together: greater productivity, lower cost, and shorter lead time. Increasing value creation abilities is the ultimate goal of lean continuous improvement. How does continuous improvement work? This article will outline some of the many benefits of continuous optimization. It is simple: Continuous improvement saves money.
Continuous improvement focuses on small, incremental improvements and not large-scale changes. Although small improvements seem insignificant at first glance, the whole is important. Slow improvements are more effective than large leaps. Continuous improvement, which focuses on alignment of objectives, is key to lean manufacturing environments. It allows businesses to maximize productivity, profitability, and efficiency. Continuous improvement can make the entire production process more efficient and enable all processes to work together toward a common goal.
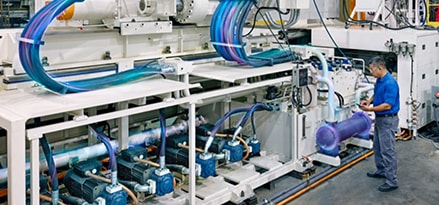
Kaizen
Kaizen in lean manufacturing focuses on waste elimination. It is sometimes used to improve production yield or reduce lead times. Employees are given specific roles that allow them to investigate the problem and find possible solutions. A kaizen activity usually starts with the creation a process value stream map. The team then conducts an analysis of time and other relevant operations. This process is repeated until each step has been improved and the overall process is leaner and more efficient.
An example is a manufacturing plant that has identified inefficiencies and may buy a new lift truck. The operator might move inventory around to speed up loading and unloading. The value stream is also a map of the processes that create products or services. Five S's will be used during the mapping to increase employee productivity as well as workplace practices. There are seven types. Each of these types focuses on a different aspect of a manufacturing process.
FAQ
How does a production planner differ from a project manager?
The difference between a product planner and project manager is that a planer is typically the one who organizes and plans the entire project. A production planner, however, is mostly involved in the planning stages.
What is the difference between Production Planning and Scheduling?
Production Planning (PP) refers to the process of determining how much production is needed at any given moment. Forecasting demand is one way to do this.
Scheduling refers to the process of allocating specific dates to tasks in order that they can be completed within a specified timeframe.
How can manufacturing avoid production bottlenecks
The key to avoiding bottlenecks in production is to keep all processes running smoothly throughout the entire production cycle, from the time you receive an order until the time when the product ships.
This includes both quality control and capacity planning.
Continuous improvement techniques such Six Sigma can help you achieve this.
Six Sigma management is a system that improves quality and reduces waste within your organization.
It focuses on eliminating variation and creating consistency in your work.
What does warehouse mean?
A warehouse or storage facility is where goods are stored before they are sold. You can have it indoors or outdoors. In some cases it could be both indoors and outdoors.
Statistics
- Job #1 is delivering the ordered product according to specifications: color, size, brand, and quantity. (netsuite.com)
- In 2021, an estimated 12.1 million Americans work in the manufacturing sector.6 (investopedia.com)
- (2:04) MTO is a production technique wherein products are customized according to customer specifications, and production only starts after an order is received. (oracle.com)
- [54][55] These are the top 50 countries by the total value of manufacturing output in US dollars for its noted year according to World Bank.[56] (en.wikipedia.org)
- In the United States, for example, manufacturing makes up 15% of the economic output. (twi-global.com)
External Links
How To
How to Use the Just In Time Method in Production
Just-in time (JIT), is a process that reduces costs and increases efficiency in business operations. This is where you have the right resources at the right time. This means that you only pay the amount you actually use. Frederick Taylor was the first to coin this term. He developed it while working as a foreman during the early 1900s. After observing how workers were paid overtime for late work, he realized that overtime was a common practice. He realized that workers should have enough time to complete their jobs before they begin work. This would help increase productivity.
JIT is a way to plan ahead and make sure you don't waste any money. You should also look at the entire project from start to finish and make sure that you have sufficient resources available to deal with any problems that arise during the course of your project. You'll be prepared to handle any potential problems if you know in advance. This way you won't be spending more on things that aren’t really needed.
There are many types of JIT methods.
-
Demand-driven JIT: You order the parts and materials you need for your project every other day. This will enable you to keep track of how much material is left after you use it. This will allow you to calculate how long it will take to make more.
-
Inventory-based : You can stock the materials you need in advance. This allows you to predict how much you can expect to sell.
-
Project-driven: This is an approach where you set aside enough funds to cover the cost of your project. Knowing how much money you have available will help you purchase the correct amount of materials.
-
Resource-based JIT: This is the most popular form of JIT. You assign certain resources based off demand. If you have many orders, you will assign more people to manage them. If you don’t have many orders you will assign less people to the work.
-
Cost-based : This is similar in concept to resource-based. But here, you aren't concerned about how many people your company has but how much each individual costs.
-
Price-based: This is similar to cost-based but instead of looking at individual workers' salaries, you look at the total company price.
-
Material-based: This is very similar to cost-based but instead of looking at total costs of the company you are concerned with how many raw materials you use on an average.
-
Time-based JIT: A variation on resource-based JIT. Instead of focusing only on how much each employee is costing, you should focus on how long it takes to complete your project.
-
Quality-based JIT is another variant of resource-based JIT. Instead of looking at the labor costs and time it takes to make a product, think about its quality.
-
Value-based JIT: One of the most recent forms of JIT. In this instance, you are not concerned about the product's performance or meeting customer expectations. Instead, your goal is to add value to the market.
-
Stock-based: This is an inventory-based method that focuses on the actual number of items being produced at any given time. This method is useful when you want to increase production while decreasing inventory.
-
Just-in-time planning (JIT): This is a combination JIT and supply-chain management. It is the process that schedules the delivery of components within a short time of their order. It reduces lead times and improves throughput.