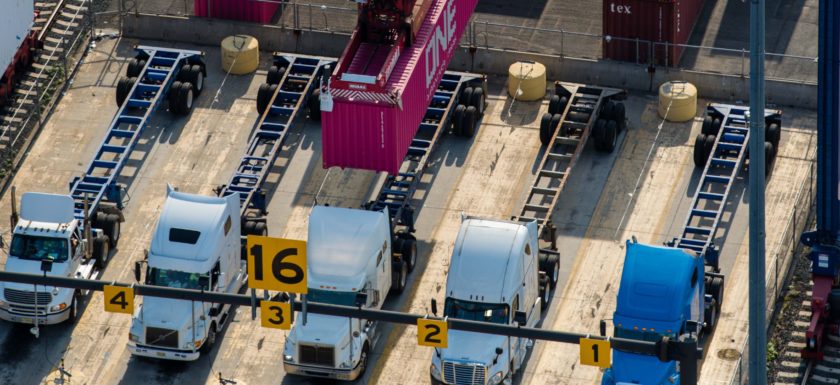
OSHA compliance is just as important as experience for food producers. These are the three main things you should consider when selecting a company that will automate your production.
Food manufacturers must have experience
A food manufacturer's position often requires a high level of experience in the industry. There are opportunities for people with less or no experience. Many food producers prefer to hire within their own ranks. A high school education may be helpful, but not necessarily necessary. As assistants to more skilled workers, entry-level employees begin as such. They then learn on-the-job. Some entry-level jobs are straightforward and can be completed in a few days. Common entry-level jobs include operating bread slicers and washing vegetables before processing. It is important to have experience in all areas of food manufacturing.
Conformance to OSHA regulations
The enforcement process for OSHA regulations for food manufacturers begins with an inspection, which is either triggered by an incident, complaint, or a "programmed inspection." OSHA enforcement visits at yogurt manufacturing plants are usually triggered by a report and preceded with a planned inspector. The citations often include multiple violations to the process safety management standard as well as standards for hazard communication and guarding machinery, platforms, emergency evacuation, forklift operation and hearing protection.
Develop a plan that will prevent food safety hazards
Most companies are subject to federal regulations. However, there are some exceptions. While it is impossible to anticipate every food safety issue, there are ways to prevent and manage potential hazards in the food manufacturing process. Food safety is not only an issue for the health of the consumer, but it can also have negative effects on the business. Recalls may affect supply chain operations as well. They can occur for various reasons, including adulteration, misbranding, or violative products. Food recalls are not only dangerous for the consumer, but can also be costly for food manufacturers.
Automation costs
As utilities costs rise, automation is becoming more expensive for food manufacturers. Therefore, some regions have to import raw materials to keep up with local producers. Suppliers face declining profits as they pass the costs on to consumers. However, automation can help lower these costs and increase production efficiency. This article will explain how automation can improve food manufacturing's overall efficiency. You can also get access to our expertise in this industry.
Challenges of competing with dominant food companies
Three broad strategies are used by dominant food companies to maintain market dominance, avoid unwanted competition, and increase their profit margins. These strategies include acquiring and developing intangible assets, controlling the supply chain, marketing efficiency, and enforcing production and market efficiencies. These strategies create barriers for entry. These are the main challenges that emerging food & beverage companies face. Let's look into each strategy more in detail.
FAQ
What is the difference between Production Planning and Scheduling?
Production Planning (PP) is the process of determining what needs to be produced at any given point in time. This can be done by forecasting demand and identifying production capabilities.
Scheduling refers to the process of allocating specific dates to tasks in order that they can be completed within a specified timeframe.
What is meant by manufacturing industries?
Manufacturing Industries are businesses that produce products for sale. These products are sold to consumers. These companies use various processes such as production, distribution, retailing, management, etc., to fulfill this purpose. They manufacture goods from raw materials using machines and other equipment. This includes all types if manufactured goods.
What is production planning?
Production planning is the process of creating a plan that covers all aspects of production. This includes scheduling, budgeting and crew, location, equipment, props, and more. This document is designed to make sure everything is ready for when you're ready to shoot. This document should include information about how to achieve the best results on-set. This information includes locations, crew details and equipment requirements.
First, you need to plan what you want to film. You may have already decided where you would like to shoot, or maybe there are specific locations or sets that you want to use. Once you have identified your locations and scenes it's time to begin figuring out what elements you will need for each one. Perhaps you have decided that you need to buy a car but aren't sure which model. To narrow your options, you can search online for available models.
After you have chosen the right car, you will be able to begin thinking about accessories. Are you looking for people to sit in the front seats? Or maybe you just need someone to push the car around. You might want to change your interior color from black and white. These questions will help determine the look and feel you want for your car. You can also think about the type of shots you want to get. What type of shots will you choose? Maybe you want to show your engine or the steering wheel. This will allow you to determine the type of car you want.
Once you've determined the above, it is time to start creating a calendar. A schedule will tell you when you need to start shooting and when you need to finish. You will need to know when you have to be there, what time you have to leave and when your return home. This way, everyone knows what they need to do and when. You can also make sure to book extra staff in advance if you have to hire them. You don't want to hire someone who won't show up because he didn't know.
Your schedule will also have to be adjusted to reflect the number of days required to film. Some projects only take one or two days, while others may last weeks. While creating your schedule, it is important to remember whether you will require more than one shot per day. Shooting multiple takes over the same location will increase costs and take longer to complete. If you aren't sure whether you need multiple shots, it is best to take fewer photos than you would like.
Budget setting is an important part of production planning. As it will allow you and your team to work within your financial means, setting a realistic budget is crucial. You can always lower the budget if you encounter unexpected problems. But, don't underestimate how much money you'll spend. You'll end up with less money after paying for other things if the cost is underestimated.
Production planning is a complicated process. But once you understand how everything works together, it becomes much easier to plan future project.
Are there ways to automate parts of manufacturing?
Yes! Since ancient times, automation has been in existence. The Egyptians invented the wheel thousands of years ago. Nowadays, we use robots for assembly lines.
There are many applications for robotics in manufacturing today. These include:
-
Automated assembly line robots
-
Robot welding
-
Robot painting
-
Robotics inspection
-
Robots create products
Automation could also be used to improve manufacturing. For example, 3D printing allows us to make custom products without having to wait for weeks or months to get them manufactured.
Is there anything we should know about Manufacturing Processes prior to learning about Logistics.
No. You don't have to know about manufacturing processes before learning about logistics. But, being familiar with manufacturing processes will give you a better understanding about how logistics works.
Statistics
- In the United States, for example, manufacturing makes up 15% of the economic output. (twi-global.com)
- According to a Statista study, U.S. businesses spent $1.63 trillion on logistics in 2019, moving goods from origin to end user through various supply chain network segments. (netsuite.com)
- Job #1 is delivering the ordered product according to specifications: color, size, brand, and quantity. (netsuite.com)
- It's estimated that 10.8% of the U.S. GDP in 2020 was contributed to manufacturing. (investopedia.com)
- You can multiply the result by 100 to get the total percent of monthly overhead. (investopedia.com)
External Links
How To
Six Sigma and Manufacturing
Six Sigma is "the application statistical process control (SPC), techniques for continuous improvement." Motorola's Quality Improvement Department in Tokyo, Japan developed Six Sigma in 1986. Six Sigma is a method to improve quality through standardization and elimination of defects. Since there are no perfect products, or services, this approach has been adopted by many companies over the years. Six Sigma's primary goal is to reduce variation from the average value of production. This means that if you take a sample of your product, then measure its performance against the average, you can find out what percentage of the time the process deviates from the norm. If you notice a large deviation, then it is time to fix it.
Understanding the dynamics of variability within your business is the first step in Six Sigma. Once you've understood that, you'll want to identify sources of variation. It is important to identify whether the variations are random or systemic. Random variations happen when people make errors; systematic variations are caused externally. These are, for instance, random variations that occur when widgets are made and some fall off the production line. But if you notice that every widget you make falls apart at the exact same place each time, this would indicate that there is a problem.
Once you've identified the problem areas you need to find solutions. It might mean changing the way you do business or redesigning it entirely. To verify that the changes have worked, you need to test them again. If they don't work, you will need to go back to the drawing boards and create a new plan.