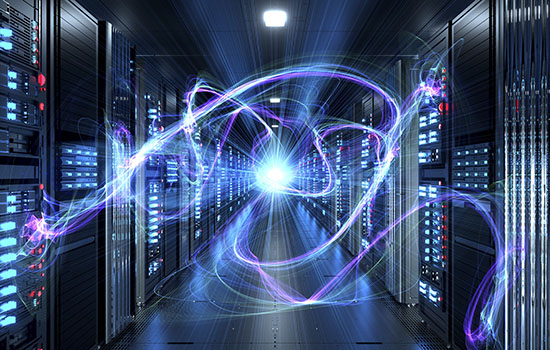
CEVA Logistics is a company that provides logistics services. Whether you're looking for a new career or simply need a new place to work, these logistics companies offer a variety of benefits to their employees. Here's how you apply for a logistics job with one of these companies. You can start by searching for jobs based on location.
Job description
CEVA Logistics has a variety of jobs for people with a variety of education and work experience. The company's core values revolve around customer service and prompt delivery. The company is also looking for individuals who are passionate and willing to work hard. Candidates who have some or no previous experience in logistics and who have a positive attitude will be given preference when applying for a job.
CEVA Logistics is seeking a Process/Industrial Engineer to design and implement new processes and improve efficiency. The ideal candidate is energetic, self-driven and able to work with other plant employees. They are responsible for designing and implementing process plans, managing projects, as well as using modeling and analytical skills. They must also be familiar with robotics and other manufacturing processes to increase efficiency and quality.
Education required
CEVA Logistics has many career options for those who are interested in working there. These include warehouse manager and sales rep. You can also choose to be operations supervisors. This involves overseeing all aspects of the company's day, including inventory and scheduling. They may have several employees working under them. Candidates for these roles typically have a bachelor’s degree and supervisory or management experience.
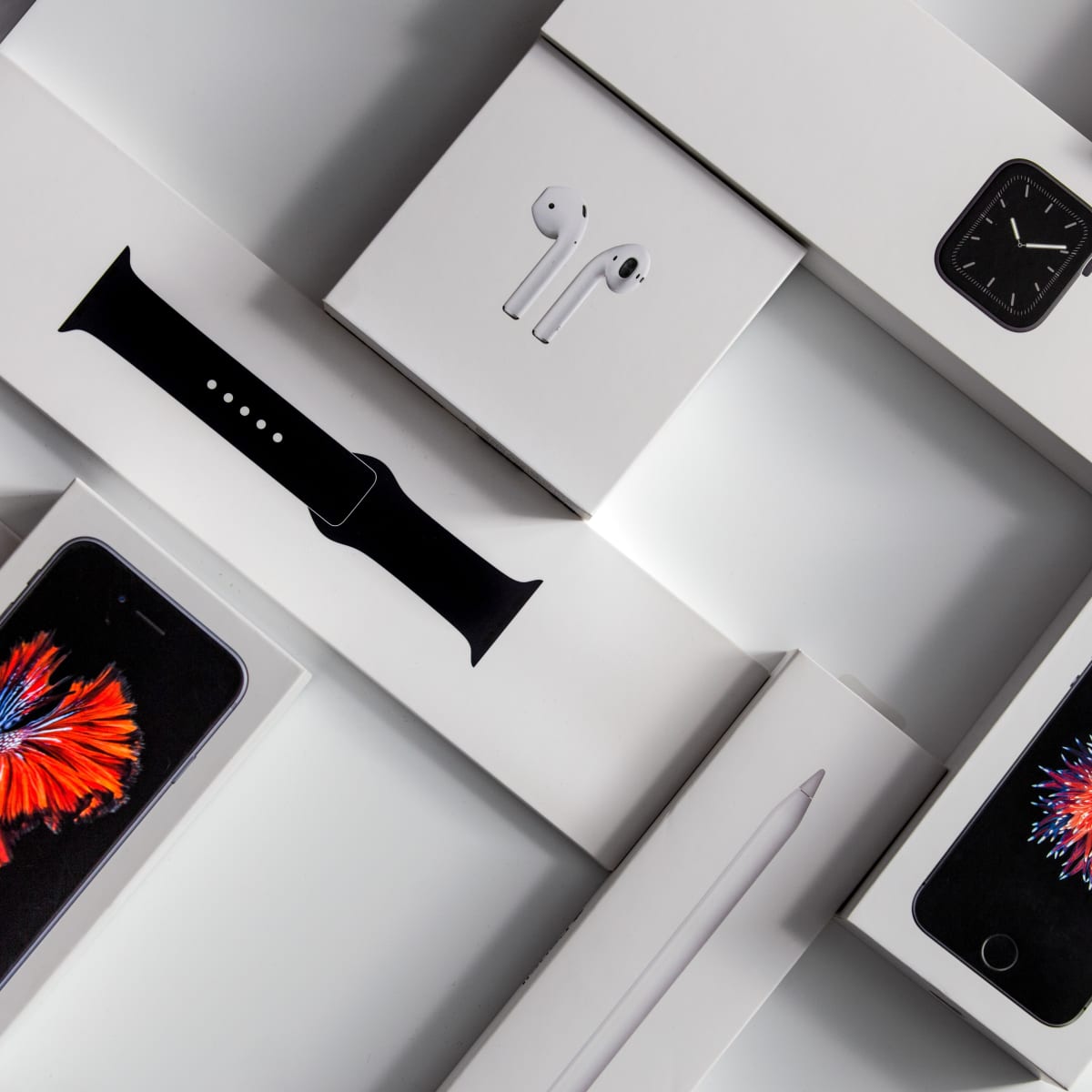
Online applications are accepted from interested applicants. Online applications require candidates to first create a career profile in the company's portal. Candidates can connect to their LinkedIn profiles to create a profile and attach their resumes. After creating their profile, they can choose the desired country or region and get in touch to a recruiter.
Salary range
If you are interested in applying for a CEVA Logistics career, the first thing to do is create a profile at the company's online job portal. This allows you to connect with your LinkedIn profile and upload your resume. You can also input details about your work experience, skills, or other pertinent information. The next step is to select a region or country where you're interested in working. You'll then receive contact information for a recruiter in the region.
CEVA Logistics has a variety of salaries. These vary depending on your job title, work experience, and geographic location. The Vice President of CEVA Logistics makes $166,000 a year, while an Air Break Bulk Specialist earns $24,000. The economic environment in each area can affect the salaries.
Locations
If you're looking for a great career in logistics, consider a position with CEVA Logistics. There are many positions available at different locations. Each position has different responsibilities and requirements. Simply type the job title and your location into the search box to apply for a job. You can search for Edison job listings. Experience in driving is a must. You also need to be able communicate with customers and other employees.
CEVA Logistics offers many career opportunities, including supervisory positions. Supervisors manage the company's day-to-day operations. They oversee inventory and coordinate work schedules. Operations supervisors are typically responsible for managing a team, coordinating schedules and overseeing employees. It is also important to have strong leadership and management abilities.
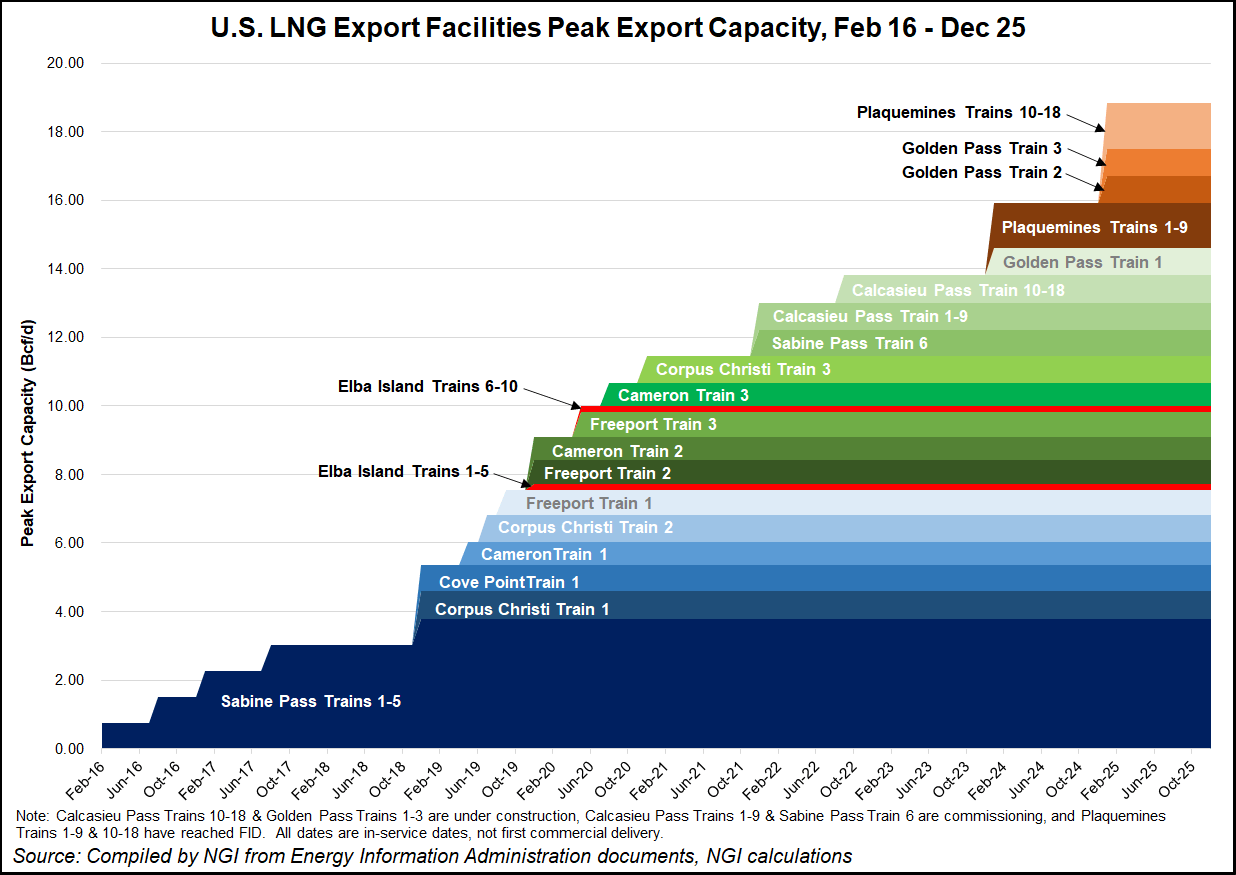
Apply online
CEVA Logistics is an online job board for those looking for jobs in the logistics sector. This international company was founded in 2006 and is a result of the merger of two Texan and Australian contract logistics companies. Its operations now span over 950 locations in 170 different countries. You can apply for part-time and full-time jobs.
Although many positions at CEVA do require some experience, most are entry-level. Other positions require little or no experience. Customer service representative and admin clerk are just a few of the positions that can be found in this entry-level category.
FAQ
What is the difference between manufacturing and logistics
Manufacturing is the process of creating goods from raw materials by using machines and processes. Logistics is the management of all aspects of supply chain activities, including procurement, production planning, distribution, warehousing, inventory control, transportation, and customer service. Manufacturing and logistics are often considered together as a broader term that encompasses both the process of creating products and delivering them to customers.
What are the goods of logistics?
Logistics refers to the movement of goods from one place to another.
They encompass all aspects transport, including packaging and loading, transporting, storage, unloading.
Logisticians ensure that the right product reaches the right place at the right time and under safe conditions. Logisticians assist companies in managing their supply chains by providing information such as demand forecasts, stock levels and production schedules.
They coordinate with vendors and suppliers, keep track of shipments, monitor quality standards and perform inventory and order replenishment.
What is the role and responsibility of a Production Planner?
Production planners ensure all aspects of the project are delivered within time and budget. They also ensure that the product/service meets the client’s needs.
How can we reduce manufacturing overproduction?
Improved inventory management is the key to reducing overproduction. This would reduce the time needed to manage inventory. This could help us free up our time for other productive tasks.
A Kanban system is one way to achieve this. A Kanban board is a visual display used to track work in progress. Kanban systems are where work items travel through a series of states until reaching their final destination. Each state is assigned a different priority.
To illustrate, work can move from one stage or another when it is complete enough for it to be moved to a new stage. However, if a task is still at the beginning stages, it will remain so until it reaches the end of the process.
This helps to keep work moving forward while ensuring that no work is left behind. With a Kanban board, managers can see exactly how much work is being done at any given moment. This information allows managers to adjust their workflow based off real-time data.
Lean manufacturing is another way to manage inventory levels. Lean manufacturing emphasizes eliminating waste in all phases of production. Anything that does nothing to add value to a product is waste. Here are some examples of common types.
-
Overproduction
-
Inventory
-
Unnecessary packaging
-
Overstock materials
By implementing these ideas, manufacturers can improve efficiency and cut costs.
What skills is required for a production planner?
You must be flexible and organized to become a productive production planner. Also, you must be able and willing to communicate with clients and coworkers.
Statistics
- Many factories witnessed a 30% increase in output due to the shift to electric motors. (en.wikipedia.org)
- [54][55] These are the top 50 countries by the total value of manufacturing output in US dollars for its noted year according to World Bank.[56] (en.wikipedia.org)
- (2:04) MTO is a production technique wherein products are customized according to customer specifications, and production only starts after an order is received. (oracle.com)
- You can multiply the result by 100 to get the total percent of monthly overhead. (investopedia.com)
- It's estimated that 10.8% of the U.S. GDP in 2020 was contributed to manufacturing. (investopedia.com)
External Links
How To
How to Use the Just-In-Time Method in Production
Just-intime (JIT), which is a method to minimize costs and maximize efficiency in business process, is one way. It is a process where you get the right amount of resources at the right moment when they are needed. This means that only what you use is charged to your account. Frederick Taylor first coined this term while working in the early 1900s as a foreman. Taylor observed that overtime was paid to workers if they were late in working. He concluded that if workers were given enough time before they start work, productivity would increase.
JIT is an acronym that means you need to plan ahead so you don’t waste your money. The entire project should be looked at from start to finish. You need to ensure you have enough resources to tackle any issues that might arise. You'll be prepared to handle any potential problems if you know in advance. This will ensure that you don't spend more money on things that aren't necessary.
There are several types of JIT techniques:
-
Demand-driven JIT: This is a JIT that allows you to regularly order the parts/materials necessary for your project. This will allow you to track how much material you have left over after using it. You'll also be able to estimate how long it will take to produce more.
-
Inventory-based : You can stock the materials you need in advance. This allows you to forecast how much you will sell.
-
Project-driven : This is a method where you make sure that enough money is set aside to pay the project's cost. Knowing how much money you have available will help you purchase the correct amount of materials.
-
Resource-based JIT : This is probably the most popular type of JIT. This is where you assign resources based upon demand. You might assign more people to help with orders if there are many. You'll have fewer orders if you have fewer.
-
Cost-based : This is similar in concept to resource-based. But here, you aren't concerned about how many people your company has but how much each individual costs.
-
Price-based: This approach is very similar to the cost-based method except that you don't look at individual workers costs but the total cost of the company.
-
Material-based: This is quite similar to cost-based, but instead of looking at the total cost of the company, you're concerned with how much raw materials you spend on average.
-
Time-based JIT: A variation on resource-based JIT. Instead of focusing only on how much each employee is costing, you should focus on how long it takes to complete your project.
-
Quality-based: This is yet another variation of resource-based JIT. Instead of focusing on the cost of each worker or how long it takes, think about how high quality your product is.
-
Value-based JIT: One of the most recent forms of JIT. In this case, you're not concerned with how well the products perform or whether they meet customer expectations. Instead, you are focused on adding value to the marketplace.
-
Stock-based: This stock-based method focuses on the actual quantity of products being made at any given time. This method is useful when you want to increase production while decreasing inventory.
-
Just-intime (JIT), planning is a combination JIT management and supply chain management. It's the process of scheduling delivery of components immediately after they are ordered. This is important as it reduces lead time and increases throughput.