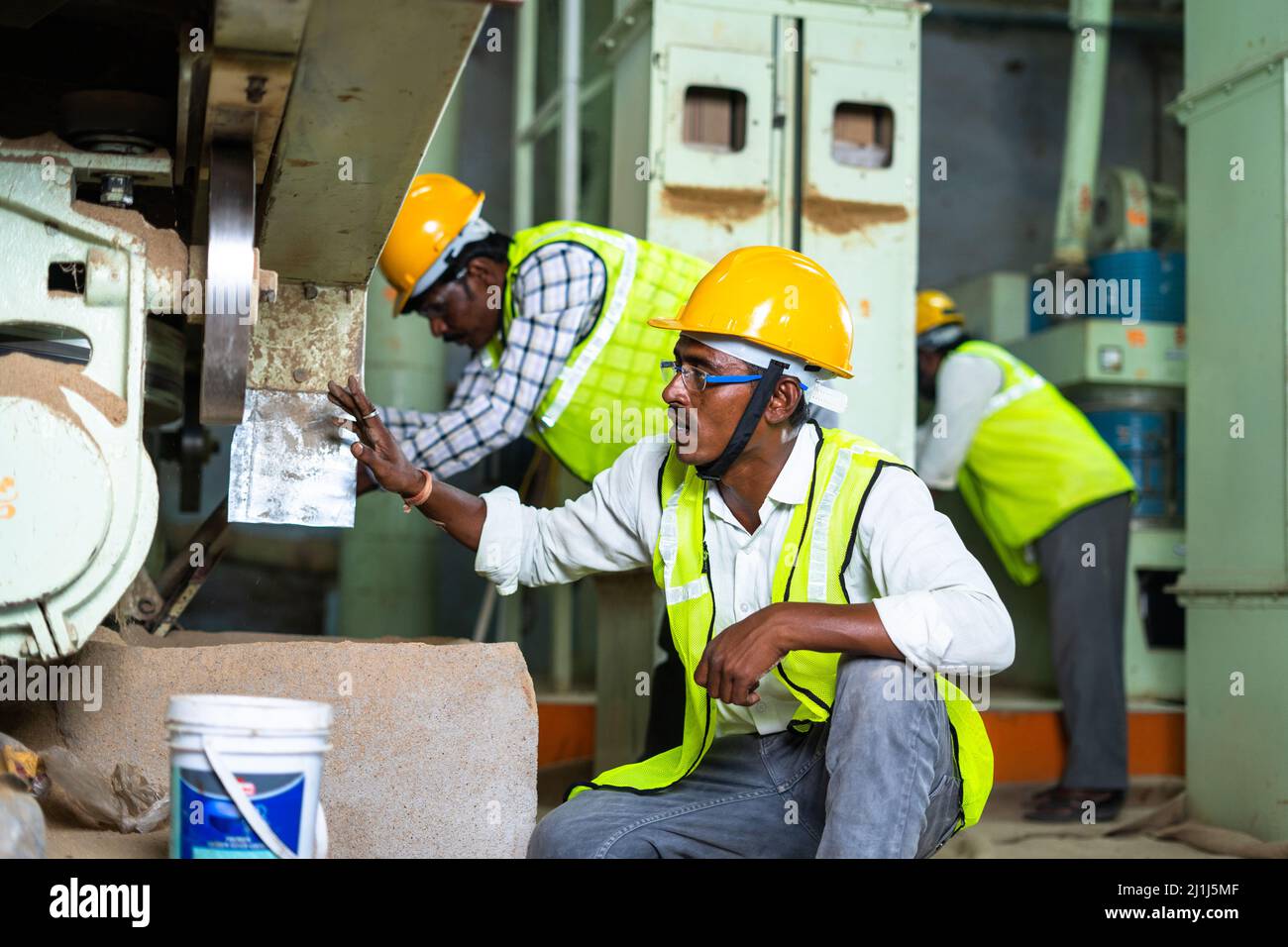
It doesn't matter if you're looking for work or are interested in earning a degree, it is important to understand how much you can make. The pay scale for industrial engineers will vary depending on your field of study, experience and industry. The average industrial engineer salary is $95,300. However, salaries are often higher in the top paying metropolitan areas.
Industrial engineers are responsible for designing, developing and installing systems that increase the productivity of the production process. They also develop ways to keep workplaces safer. Industrial engineers may also design equipment, plan facilities and analyze the specifications of products. This is done by analyzing how design changes affect production costs.
With experience in the field, industrial engineers may be able to earn a high-paying job. With a master's level in industrial engineering, they may be eligible for a higher income. This degree is highly sought-after by international students. It can lead to a career within manufacturing, engineering services, and healthcare.
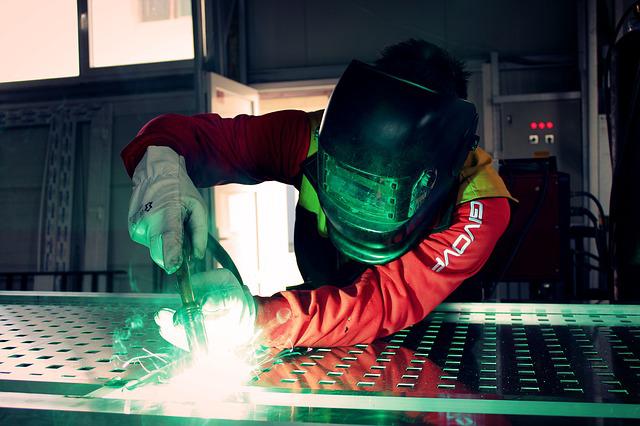
Industrial engineers are also expected to have a high employment growth rate over the next decade. From 2021 to 2031, the employment of industrial engineers will grow by 10 percent. This is higher that the average for all occupations. The top 10 percent of industrial engineers make more than $85,000 a year. With management experience, they are likely to earn more. Industrial engineers who have advanced degrees in industrial engineering can perform cost-benefit analyses, evaluate cost distribution in operational processes, negotiate for purchasing decisions, and even conduct cost-benefit reviews.
Industrial engineers can think outside the box to find innovative ways to improve efficiency. Many industrial engineers work from offices. They also may interact regularly with production workers. Industrial engineers can also handle telephone calls, emails and face-to–face conversations. They can present their plans in either written reports or oral presentation.
Many industries include construction, manufacturing, transport, energy, utilities, pharmaceuticals and other. They might be involved in the development of systems to reduce waste within production processes, depending on what industry they work in.
A bachelor's degree typically required for industrial engineers is a bachelor of engineering. A master's degree can be obtained in industrial engineering for a career as an engineer consultant or manufacturer. Many programs include courses that cover mathematics, science, engineering, and general topics. It may take up to seven years for the program to be completed.
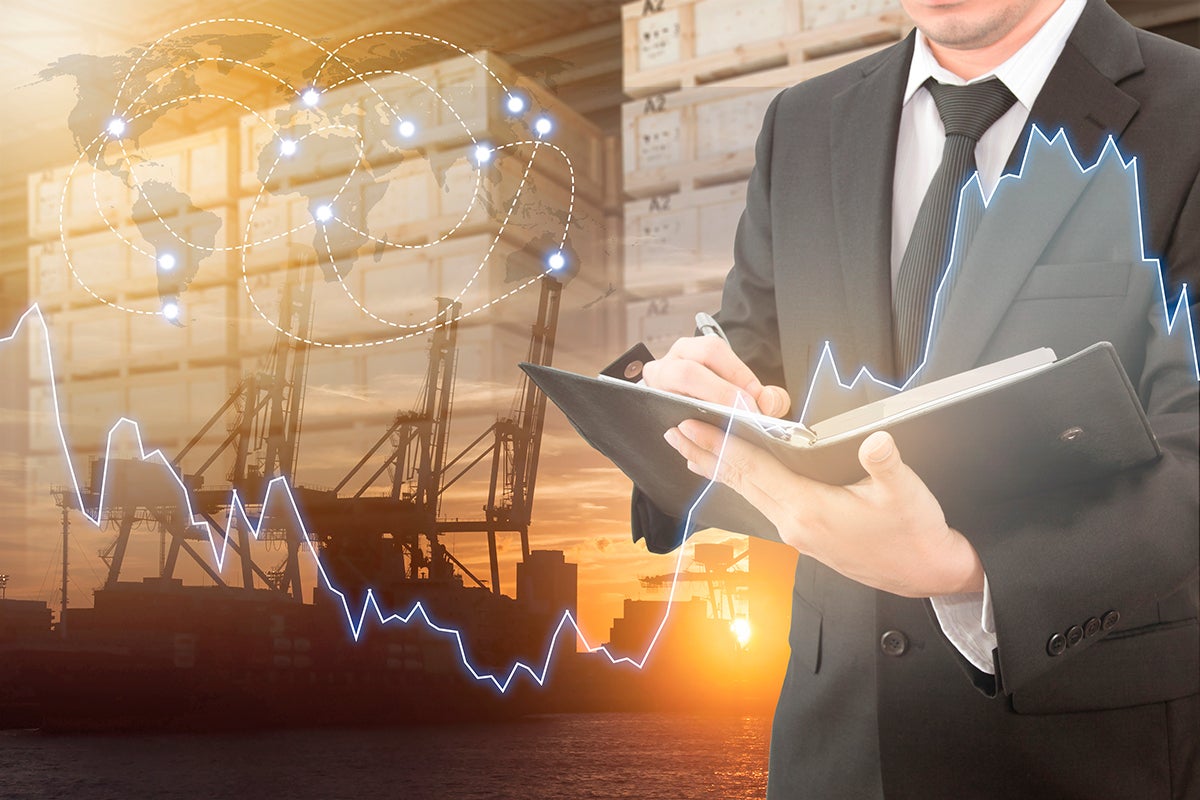
The average salary for an entry-level industrial engineer is $65,000 to $75,000, although the range of salary increases with experience. An experienced industrial engineer can earn $86,809 an year. A master's or doctorate degree is required to increase the salary of an industrial engineer.
Industrial engineers need to have good communication skills and technical knowledge. They need to be able to think outside the box to solve problems. They should be able combine materials, equipment, workers and workers to create efficient solutions. They should also possess good interpersonal skills. This is a challenging job that can also be very rewarding.
FAQ
How can manufacturing prevent production bottlenecks?
The key to avoiding bottlenecks in production is to keep all processes running smoothly throughout the entire production cycle, from the time you receive an order until the time when the product ships.
This includes both quality control and capacity planning.
Continuous improvement techniques such Six Sigma are the best method to accomplish this.
Six Sigma can be used to improve the quality and decrease waste in all areas of your company.
It is focused on creating consistency and eliminating variation in your work.
What is the importance of automation in manufacturing?
Automation is essential for both manufacturers and service providers. It enables them to provide services faster and more efficiently. It also helps to reduce costs and improve productivity.
What skills do production planners need?
Being a production planner is not easy. You need to be organized and flexible. Also, you must be able and willing to communicate with clients and coworkers.
What type of jobs is there in logistics
There are many types of jobs in logistics. Here are some:
-
Warehouse workers – They load, unload and transport pallets and trucks.
-
Transportation drivers – They drive trucks or trailers to transport goods and perform pick-ups.
-
Freight handlers are people who sort and pack freight into warehouses.
-
Inventory managers - These are responsible for overseeing the stock of goods in warehouses.
-
Sales representatives - They sell products.
-
Logistics coordinators – They plan and coordinate logistics operations.
-
Purchasing agents – They buy goods or services necessary to run a company.
-
Customer service representatives are available to answer customer calls and emails.
-
Shipping clerks – They process shipping orders, and issue bills.
-
Order fillers – They fill orders based upon what was ordered and shipped.
-
Quality control inspectors (QCI) - They inspect all incoming and departing products for potential defects.
-
Others - There are many types of jobs in logistics such as transport supervisors and cargo specialists.
What are the 7 Rs of logistics?
The acronym "7R's" of Logistics stands for seven principles that underpin logistics management. It was developed and published by the International Association of Business Logisticians in 2004 as part of the "Seven Principles of Logistics Management".
The following letters make up the acronym:
-
Responsive - ensure all actions are legal and not harmful to others.
-
Reliable - You can have confidence that you will fulfill your promises.
-
Use resources effectively and sparingly.
-
Realistic – consider all aspects of operations, from cost-effectiveness to environmental impact.
-
Respectful - Treat people fairly and equitably
-
You are resourceful and look for ways to save money while increasing productivity.
-
Recognizable - Provide value-added services to customers
How can manufacturing efficiency be improved?
The first step is to identify the most important factors affecting production time. We must then find ways that we can improve these factors. You can start by identifying the most important factors that impact production time. Once you've identified them all, find solutions to each one.
What is meant by manufacturing industries?
Manufacturing Industries are businesses that produce products for sale. Consumers are people who purchase these goods. To accomplish this goal, these companies employ a range of processes including distribution, sales, management, and production. These companies produce goods using raw materials and other equipment. This includes all types manufactured goods such as clothing, building materials, furniture, electronics, tools and machinery.
Statistics
- According to a Statista study, U.S. businesses spent $1.63 trillion on logistics in 2019, moving goods from origin to end user through various supply chain network segments. (netsuite.com)
- [54][55] These are the top 50 countries by the total value of manufacturing output in US dollars for its noted year according to World Bank.[56] (en.wikipedia.org)
- Many factories witnessed a 30% increase in output due to the shift to electric motors. (en.wikipedia.org)
- (2:04) MTO is a production technique wherein products are customized according to customer specifications, and production only starts after an order is received. (oracle.com)
- Job #1 is delivering the ordered product according to specifications: color, size, brand, and quantity. (netsuite.com)
External Links
How To
How to Use Six Sigma in Manufacturing
Six Sigma is defined by "the application SPC (statistical process control) techniques to achieve continuous improvements." It was developed by Motorola's Quality Improvement Department at their plant in Tokyo, Japan, in 1986. The basic idea behind Six Sigma is to improve quality by improving processes through standardization and eliminating defects. Many companies have adopted this method in recent years. They believe there is no such thing a perfect product or service. Six Sigma's main objective is to reduce variations from the production average. You can calculate the percentage of deviation from the norm by taking a sample of your product and comparing it to the average. If this deviation is too big, you know something needs fixing.
Understanding how your business' variability is a key step towards Six Sigma implementation is the first. Once you understand that, it is time to identify the sources of variation. You'll also want to determine whether these variations are random or systematic. Random variations happen when people make errors; systematic variations are caused externally. Random variations would include, for example, the failure of some widgets to fall from the assembly line. It would be considered a systematic problem if every widget that you build falls apart at the same location each time.
Once you've identified where the problems lie, you'll want to design solutions to eliminate those problems. The solution could involve changing how you do things, or redesigning your entire process. After implementing the new changes, you should test them again to see if they worked. If they don’t work, you’ll need to go back and rework the plan.