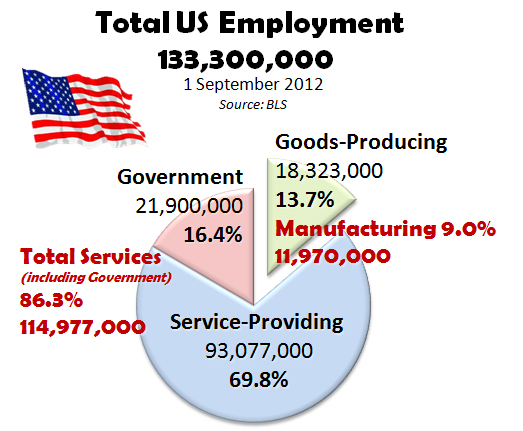
Heijunka was created originally by Toyota, a Japanese car manufacturer. It reduces the amount of waste in the production process by ensuring that the production schedule is consistent with customer demand. The production schedule is consistent with customer demand, which reduces waste. Heijunka allows manufacturers to respond to customer needs and maximize their profits.
Heijunka is the process of coordinating small production batches across manufacturing line lines. It is used to improve efficiency and productivity in multi-step manufacturing processes, especially when just/in-time principles apply. It is also part of Toyota Production System. It helps reduce waste by leveling production, mixing products and minimizing batch sizes.
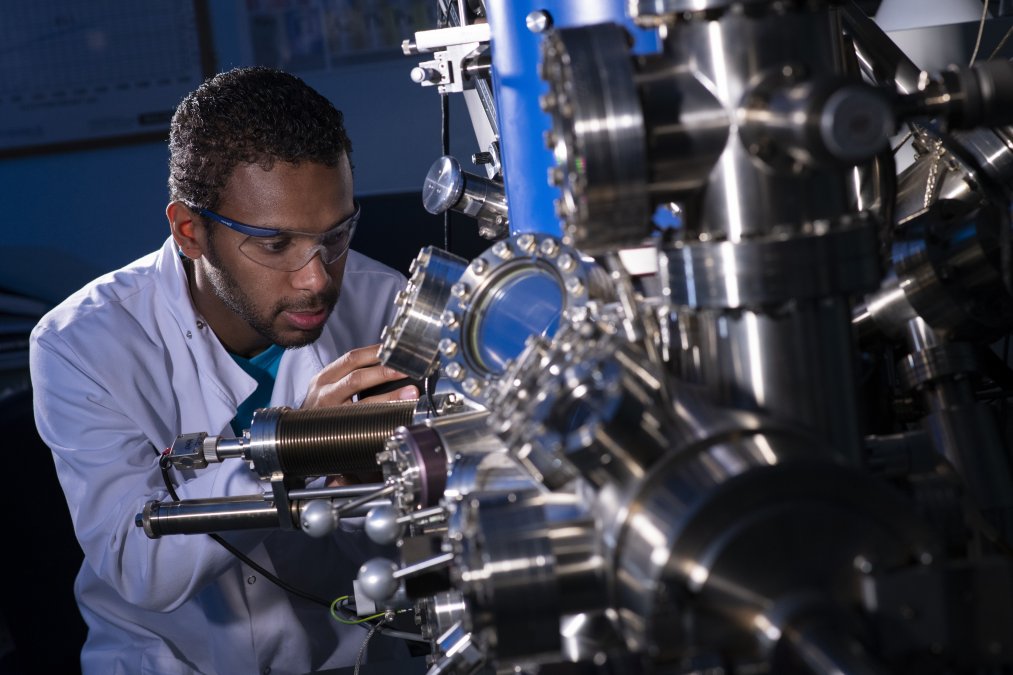
There are two possible ways to use heijunka. One method is the use of a Heijunka Box, which is a grid consisting of small boxes fixed to or mounted on a surface. It is a visual management tool that allows production personnel to schedule and visualize the production process. Magnetic cards are another way to implement the heijunka.
Toyota dealers use Heijunka to reduce changeover times. It is also a key method of Toyota's Lean framework. Heijunka not only allows manufacturers to produce at the required speed but also reduces inventory and improves production. Heijunka facilitates a better use of labor, equipment, and materials. It creates a lean manufacturing system that reduces waste. This makes it possible to offer better products to customers.
You must be able to understand the takt time (also known as the customer purchasing rate) before you can use heijunka. This refers to the time taken to complete a product in order for it to meet customer demand. Heijunka uses the takt time to determine the pace of production. You can use the takt to determine the product quantity and the pace at which customers buy the company's products. The takttime can also be used in back-office settings to determine the customer's purchase pace.
Production personnel can visual plan and schedule the production process with the help of the heijunkabox. The heijunka can also be used by shop workers to visualize the production process. The heijunka is composed of a set of rows and columns that represent each component or product type. The columns of boxes represent every time period, while the rows of boxes represent each product.
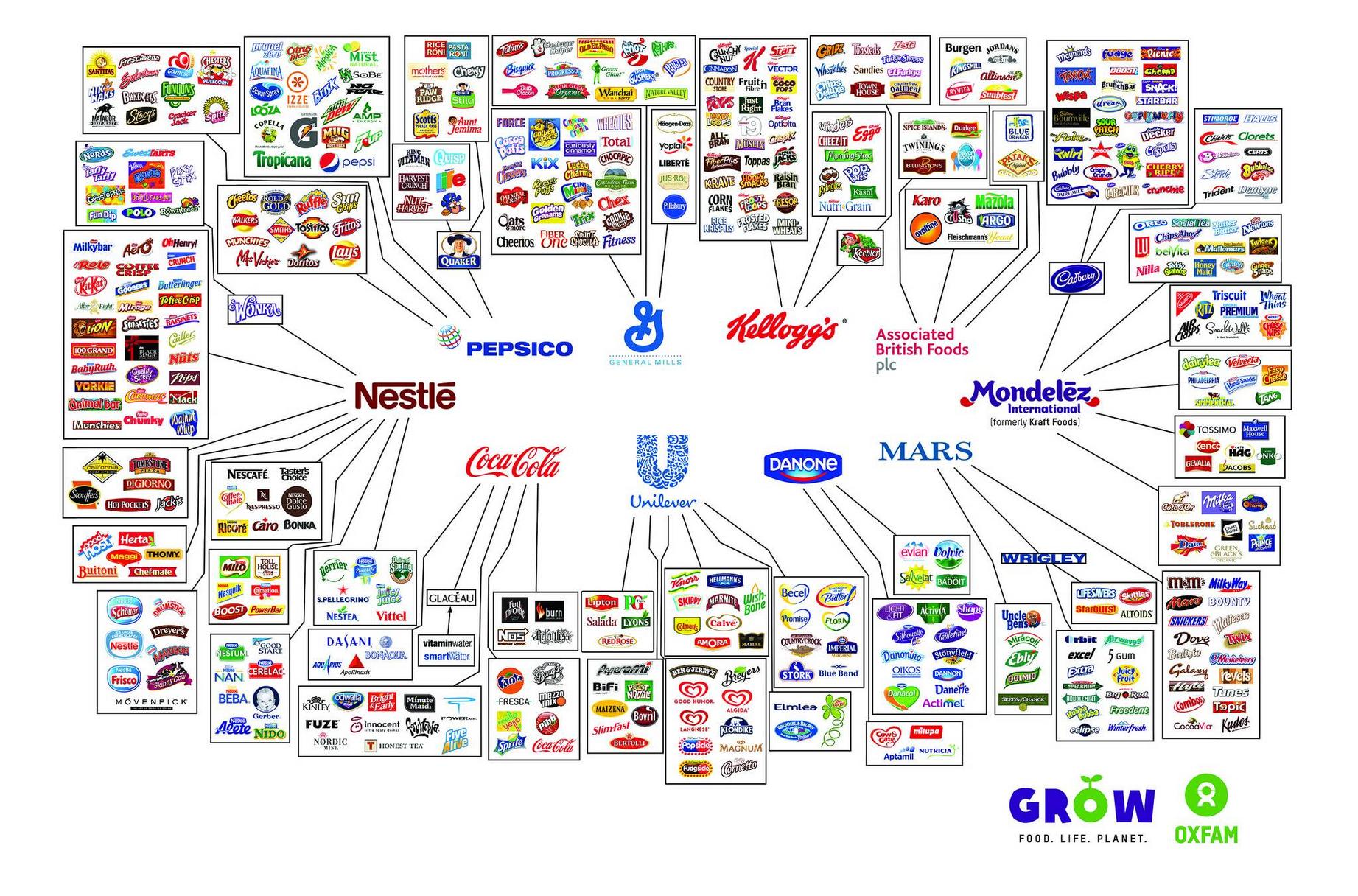
Heijunka Box (or Heijunka Box) is one of most commonly used visual management tools in manufacturing. This tool allows you to see the relationships between component production and product production. This tool also shows the weekly production schedule. It is often used with kanban card, which are colored cards that show the quantity of product required to complete a particular step in production. Kanban cards are typically taken from the heijunka at a specific time and delivered to the relevant production area.
FAQ
What is production management?
Production planning is the process of creating a plan that covers all aspects of production. This includes scheduling, budgeting and crew, location, equipment, props, and more. This document will ensure everything is in order and ready to go when you need it. This document should include information about how to achieve the best results on-set. This includes information on shooting times, locations, cast lists and crew details.
The first step is to outline what you want to film. You may have already decided where you would like to shoot, or maybe there are specific locations or sets that you want to use. Once you have identified your locations and scenes, you can start working out which elements you require for each scene. One example is if you are unsure of the exact model you want but decide that you require a car. If this is the case, you might start searching online for car models and then narrow your options by selecting from different makes.
After you have chosen the right car, you will be able to begin thinking about accessories. Are you looking for people to sit in the front seats? You might also need someone to help you get around the back. You might want to change your interior color from black and white. These questions will help to determine the style and feel of your car. Another thing you can do is think about what type of shots are desired. Are you going to be shooting close-ups? Or wide angles? Maybe you want to show your engine or the steering wheel. These details will help identify the exact car you wish to film.
Once you have made all the necessary decisions, you can start to create a schedule. You can create a schedule that will outline when you must start and finish your shoots. Each day will include the time when you need to arrive at the location, when you need to leave and when you need to return home. Everyone knows exactly what they should do and when. If you need to hire extra staff, you can make sure you book them in advance. It is not worth hiring someone who won’t show up because you didn’t tell him.
You will need to factor in the days that you have to film when creating your schedule. Some projects may only take a couple of days, while others could last for weeks. When creating your schedule, be aware of whether you need more shots per day. Shooting multiple takes over the same location will increase costs and take longer to complete. If you aren't sure whether you need multiple shots, it is best to take fewer photos than you would like.
Another important aspect of production planning is setting budgets. You will be able to manage your resources if you have a realistic budget. Remember that you can always reduce the budget later on if you run into unforeseen problems. But, don't underestimate how much money you'll spend. You'll end up with less money after paying for other things if the cost is underestimated.
Production planning can be a complex process. However, once you know how everything works together it will become easier to plan future projects.
What does it mean to warehouse?
A warehouse is a place where goods are stored until they are sold. It can be an outdoor or indoor area. In some cases, it may be a combination of both.
What are the responsibilities of a manufacturing manager
The manufacturing manager should ensure that every manufacturing process is efficient and effective. They should be aware of any issues within the company and respond accordingly.
They should also be able and comfortable communicating with other departments like sales and marketing.
They must also keep up-to-date with the latest trends in their field and be able use this information to improve productivity and efficiency.
What can I do to learn more about manufacturing?
You can learn the most about manufacturing by getting involved in it. You can read books, or watch instructional videos if you don't have the opportunity to do so.
Statistics
- Job #1 is delivering the ordered product according to specifications: color, size, brand, and quantity. (netsuite.com)
- In 2021, an estimated 12.1 million Americans work in the manufacturing sector.6 (investopedia.com)
- According to a Statista study, U.S. businesses spent $1.63 trillion on logistics in 2019, moving goods from origin to end user through various supply chain network segments. (netsuite.com)
- Many factories witnessed a 30% increase in output due to the shift to electric motors. (en.wikipedia.org)
- In the United States, for example, manufacturing makes up 15% of the economic output. (twi-global.com)
External Links
How To
How to use lean manufacturing in the production of goods
Lean manufacturing (or lean manufacturing) is a style of management that aims to increase efficiency, reduce waste and improve performance through continuous improvement. It was developed in Japan during the 1970s and 1980s by Taiichi Ohno, who received the Toyota Production System (TPS) award from TPS founder Kanji Toyoda. Michael L. Watkins published the original book on lean manufacturing, "The Machine That Changed the World," in 1990.
Lean manufacturing is often described as a set if principles that help improve the quality and speed of products and services. It emphasizes reducing defects and eliminating waste throughout the value chain. The five-steps of Lean Manufacturing are just-in time (JIT), zero defect and total productive maintenance (TPM), as well as 5S. Lean manufacturing emphasizes reducing non-value-added activities like inspection, rework and waiting.
Lean manufacturing can help companies improve their product quality and reduce costs. Additionally, it helps them achieve their goals more quickly and reduces employee turnover. Lean manufacturing can be used to manage all aspects of the value chain. Customers, suppliers, distributors, retailers and employees are all included. Many industries worldwide use lean manufacturing. For example, Toyota's philosophy underpins its success in automobiles, electronics, appliances, healthcare, chemical engineering, aerospace, paper, food, etc.
Lean manufacturing includes five basic principles:
-
Define Value: Identify the social value of your business and what sets you apart.
-
Reduce waste - Stop any activity that isn't adding value to the supply chains.
-
Create Flow - Ensure work moves smoothly through the process without interruption.
-
Standardize and simplify - Make your processes as consistent as possible.
-
Build Relationships - Establish personal relationships with both internal and external stakeholders.
Although lean manufacturing has always been around, it is gaining popularity in recent years because of a renewed interest for the economy after 2008's global financial crisis. Many businesses have adopted lean manufacturing techniques to help them become more competitive. Many economists believe lean manufacturing will play a major role in economic recovery.
Lean manufacturing, which has many benefits, is now a standard practice in the automotive industry. These include higher customer satisfaction levels, reduced inventory levels as well as lower operating costs.
The principles of lean manufacturing can be applied in almost any area of an organization. It is especially useful for the production aspect of an organization, as it ensures that every step in the value chain is efficient and effective.
There are three main types of lean manufacturing:
-
Just-in Time Manufacturing, (JIT): This kind of lean manufacturing is also commonly known as "pull-systems." JIT refers to a system in which components are assembled at the point of use instead of being produced ahead of time. This strategy aims to decrease lead times, increase availability of parts and reduce inventory.
-
Zero Defects Manufacturing (ZDM): ZDM focuses on ensuring that no defective units leave the manufacturing facility. Repairing a part that is damaged during assembly should be done, not scrapping. This applies to finished goods that may require minor repairs before shipment.
-
Continuous Improvement (CI): CI aims to improve the efficiency of operations by continuously identifying problems and making changes in order to eliminate or minimize waste. Continuous improvement involves continuous improvement of processes and people as well as tools.