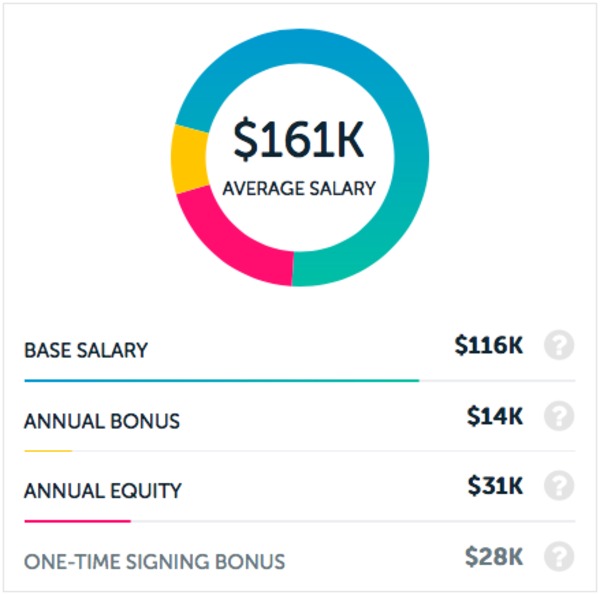
Robotics manufacturers and suppliers employ robotics technicians. They are responsible for the maintenance and repair of equipment used to build and operate robotic systems. You will need to have hands-on experience and a degree in order to do this job. The salary of a robot technician can vary depending upon the education level and previous experience.
Most robotics technicians obtain an associate's in a relevant field. This could be in electronics, mathematics or mechanical engineering. The degree provides students with a strong background in science and mathematics as well as computer programming. The program will prepare a robotics technician to work with a team that includes robotics professionals in order to build, test, and maintain robotic systems.
They are used in every aspect our lives. Robots can be found in many industries. They are used for material handling, transportation, the defense department, and the medical field. A robot can collect information (e.g., land mines) for the military. Mechatronics is an engineering discipline that combines electrical, mechanical, and computer engineering.
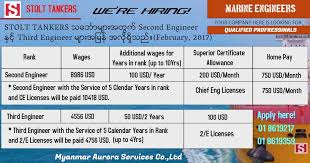
There are many colleges and universities in the United States that offer robotics technician programs. There are also opportunities for students to work directly with companies that hire robotics techs. Robot operators must be interested in solving problems and have an aptitude for math and science. Employers will generally require applicants to hold a high school diploma.
The salary for a robotics technician may not be very high, but it requires a great deal of education. Robotics technicians typically have a two year associate's degree. While it is not unusual to get additional training while working as a robotics technician, the majority of employers provide training on the job.
Robotics technicians may work shifts depending on their industry. Programming robots is the responsibility of operators. If the robot is malfunctioning, they must determine the cause of the trouble and then fix it. Additionally, operators will need to work nights and weekends.
Robotics Technicians usually earn between $44,175 - $84,520. Atlanta, GA has the highest quality of life for Robotics Technicians. It has the best quality of life. Robotics Technicians in Atlanta earn $1,841 a paycheck.
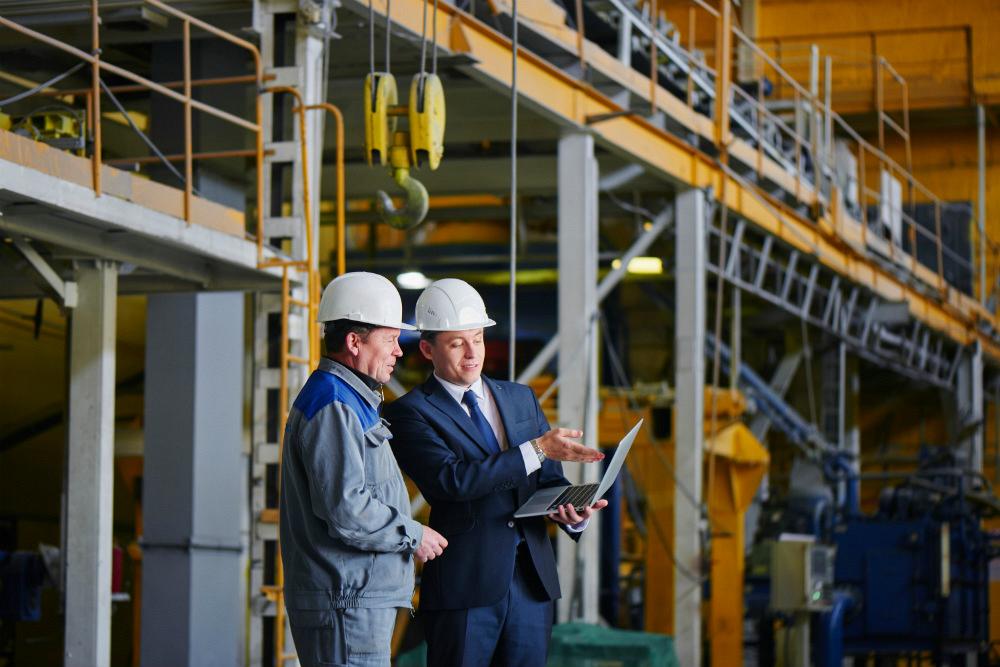
Atlanta residents also have the advantage of a lower state income tax. Georgia's robotics technician salaries are 6%. This is significantly more than the national standard. Atlanta is an affordable city, so it's a great place to live.
Robotics technicians can be a great fit for people who want a positive impact on the global community. A robotics technician can get a high salary as an expert in the field. These people can use their skills and knowledge to make the workplace and the world safer.
FAQ
How can efficiency in manufacturing be improved?
The first step is to determine the key factors that impact production time. Then we need to find ways to improve these factors. If you aren't sure where to begin, think about the factors that have the greatest impact on production time. Once you identify them, look for solutions.
What is production plan?
Production planning is the process of creating a plan that covers all aspects of production. This includes scheduling, budgeting and crew, location, equipment, props, and more. This document will ensure everything is in order and ready to go when you need it. It should also contain information on achieving the best results on set. This information includes locations, crew details and equipment requirements.
First, you need to plan what you want to film. You may have decided where to shoot or even specific locations you want to use. Once you have identified your locations and scenes, you can start working out which elements you require for each scene. If you decide you need a car and don't know what model to choose, this could be an example. In this case, you could start looking up cars online to find out what models are available and then narrow your choices by choosing between different makes and models.
After you've found the perfect car, it's time to start thinking about adding extras. Do you need people sitting in the front seats? You might also need someone to help you get around the back. You might want to change your interior color from black and white. These questions will help to determine the style and feel of your car. Also, think about what kind of shots you would like to capture. Will you be filming close-ups or wide angles? Maybe you want to show the engine and the steering wheel. All of these things will help you identify the exact style of car you want to film.
Once you've determined the above, it is time to start creating a calendar. A schedule will tell you when you need to start shooting and when you need to finish. Every day will have a time for you to arrive at the location, leave when you are leaving and return home when you are done. This way, everyone knows what they need to do and when. Hire extra staff by booking them ahead of time. It is not worth hiring someone who won’t show up because you didn’t tell him.
You will need to factor in the days that you have to film when creating your schedule. Some projects can be completed in a matter of days or weeks. Others may take several days. When creating your schedule, be aware of whether you need more shots per day. Multiple shots at the same location can increase costs and make it more difficult to complete. If you aren't sure whether you need multiple shots, it is best to take fewer photos than you would like.
Budgeting is another important aspect of production planning. As it will allow you and your team to work within your financial means, setting a realistic budget is crucial. If you have to reduce your budget due to unexpected circumstances, you can always lower it later. It is important to not overestimate how much you will spend. Underestimating the cost will result in less money after you have paid for other items.
Planning production is a tedious process. Once you have a good understanding of how everything works together, planning future projects becomes easy.
How can manufacturing overproduction be reduced?
In order to reduce excess production, you need to develop better inventory management methods. This would reduce the amount of time spent on unnecessary activities such as purchasing, storing, and maintaining excess stock. This could help us free up our time for other productive tasks.
This can be done by using a Kanban system. A Kanban Board is a visual display that tracks work progress. Kanban systems are where work items travel through a series of states until reaching their final destination. Each state represents an individual priority level.
If work is moving from one stage to the other, then the current task can be completed and moved on to the next. If a task is still in its beginning stages, it will continue to be so until it reaches the end.
This keeps work moving and ensures no work is lost. With a Kanban board, managers can see exactly how much work is being done at any given moment. This information allows them to adjust their workflow based on real-time data.
Lean manufacturing can also be used to reduce inventory levels. Lean manufacturing is about eliminating waste from all stages of the production process. Anything that doesn't add value to the product is considered waste. Some common types of waste include:
-
Overproduction
-
Inventory
-
Unnecessary packaging
-
Excess materials
By implementing these ideas, manufacturers can improve efficiency and cut costs.
Statistics
- In the United States, for example, manufacturing makes up 15% of the economic output. (twi-global.com)
- (2:04) MTO is a production technique wherein products are customized according to customer specifications, and production only starts after an order is received. (oracle.com)
- You can multiply the result by 100 to get the total percent of monthly overhead. (investopedia.com)
- In 2021, an estimated 12.1 million Americans work in the manufacturing sector.6 (investopedia.com)
- According to the United Nations Industrial Development Organization (UNIDO), China is the top manufacturer worldwide by 2019 output, producing 28.7% of the total global manufacturing output, followed by the United States, Japan, Germany, and India.[52][53] (en.wikipedia.org)
External Links
How To
How to Use lean manufacturing in the Production of Goods
Lean manufacturing (or lean manufacturing) is a style of management that aims to increase efficiency, reduce waste and improve performance through continuous improvement. It was first developed in Japan in the 1970s/80s by Taiichi Ahno, who was awarded the Toyota Production System (TPS), award from KanjiToyoda, the founder of TPS. Michael L. Watkins published the original book on lean manufacturing, "The Machine That Changed the World," in 1990.
Lean manufacturing is often described as a set if principles that help improve the quality and speed of products and services. It emphasizes eliminating waste and defects throughout the value stream. Lean manufacturing is also known as just in time (JIT), zero defect total productive maintenance(TPM), and five-star (S). Lean manufacturing seeks to eliminate non-value added activities, such as inspection, work, waiting, and rework.
In addition to improving product quality and reducing costs, lean manufacturing helps companies achieve their goals faster and reduces employee turnover. Lean manufacturing has been deemed one of the best ways to manage the entire value-chain, including customers, distributors as well retailers and employees. Lean manufacturing is widely practiced in many industries around the world. For example, Toyota's philosophy underpins its success in automobiles, electronics, appliances, healthcare, chemical engineering, aerospace, paper, food, etc.
Lean manufacturing includes five basic principles:
-
Define Value - Identify the value your business adds to society and what makes you different from competitors.
-
Reduce Waste - Eliminate any activity that doesn't add value along the supply chain.
-
Create Flow: Ensure that the work process flows without interruptions.
-
Standardize & simplify - Make processes consistent and repeatable.
-
Build Relationships - Establish personal relationships with both internal and external stakeholders.
Although lean manufacturing isn't a new concept in business, it has gained popularity due to renewed interest in the economy after the 2008 global financial crisis. Many businesses have adopted lean production techniques to make them more competitive. Economists think that lean manufacturing is a crucial factor in economic recovery.
With many benefits, lean manufacturing is becoming more common in the automotive industry. These include higher customer satisfaction, lower inventory levels, lower operating expenses, greater productivity, and improved overall safety.
Lean manufacturing can be applied to almost every aspect of an organization. Lean manufacturing is most useful in the production sector of an organisation because it ensures that each step in the value-chain is efficient and productive.
There are three main types in lean manufacturing
-
Just-in Time Manufacturing, (JIT): This kind of lean manufacturing is also commonly known as "pull-systems." JIT is a process in which components can be assembled at the point they are needed, instead of being made ahead of time. This approach is designed to reduce lead times and increase the availability of components. It also reduces inventory.
-
Zero Defects Manufacturing: ZDM ensures that no defective units leave the manufacturing plant. You should repair any part that needs to be repaired during an assembly line. This applies to finished products, which may need minor repairs before they are shipped.
-
Continuous Improvement (CI): CI aims to improve the efficiency of operations by continuously identifying problems and making changes in order to eliminate or minimize waste. Continuous Improvement involves continuous improvement of processes.