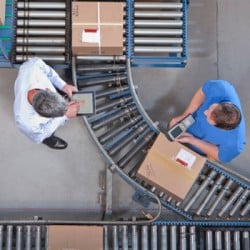
Manufacturers have a significant role to play in the economy. The manufacturing sector creates jobs, supports our nation's infrastructure, and provides materials for national defense. Manufacturing is actually one of our largest industries. It is the source of goods for almost every person in society. Manufacturing is also an essential source of innovation. While some economists believe manufacturing will decline, others believe it'll continue to grow.
Manufacturers can produce many products such as furniture, lighting, cabinets and blinds. Each product is unique and requires a set of processes and tools. Many highly skilled workers are employed in manufacturing industries, which have high productivity jobs. In 2019, the average annual earnings of manufacturing workers in the United States was $79,000.
Manufacturers must use circular processes to remain competitive in the global economy. These processes can be extended to the whole supply chain, beyond the plant. Manufacturers should consider the social impacts of their production processes. Many processes use hazardous materials that can pose a risk to workers' health. Depending on the level of safety, hazardous waste cleanup may be outweighed by the benefits of the product itself.
The manufacturing sector can play a key role in driving the economic recovery in the United States. Manufacturing's "indirect employment multiplier" is large, and the sector's purchasing power supports more than 1.4 jobs elsewhere in the economy. Manufacturing's strength can also lead to the development of local economies and communities.
While manufacturing plays an important role in economic development, the sector is also under pressure worldwide. While many economists predict that manufacturing will continue growing, others think it will be outpaced by the post-goods economic. However, manufacturing's role in innovation and economic resilience will remain important to policymakers.
Manufacturing employs a diverse workforce. It also provides employment for workers with all levels of skill. Manufacturing wages are higher than the average, even for workers without college degrees. Many industries employ manufacturing workers. They often work as technicians, engineers, or management. There are four main types that can be done in manufacturing: Continuous manufacturing (batch process manufacturing), scale-based or standardized activities, discrete manufacturing, and scale-based manufacturing.
Continuous manufacturing (also known as batch processing manufacturing) involves many processes that run 24 hours a days. Continuous manufacturing is used in oil refining, and food production. Batch process manufacturing is similar to continuous manufacturing, but involves a more diverse set of raw materials and processes. Batch process manufacturing also uses machinery that is cleaned for the next batch of products.
The manufacturing sector is a strong driver for inclusive growth and resilience in the U.S. Manufacturing is an important driver of inclusive growth and resilience in the United States. It provides employment opportunities for many skilled workers. In addition, its purchases of domestic goods support many other jobs. Manufacturing is a key driver of economic growth due to its high wages and "indirect unemployment multiplier".
FAQ
How can manufacturing avoid production bottlenecks
The key to avoiding bottlenecks in production is to keep all processes running smoothly throughout the entire production cycle, from the time you receive an order until the time when the product ships.
This includes both planning for capacity and quality control.
This can be done by using continuous improvement techniques, such as Six Sigma.
Six Sigma Management System is a method to increase quality and reduce waste throughout your organization.
It seeks to eliminate variation and create consistency in your work.
How can we reduce manufacturing overproduction?
The key to reducing overproduction lies in developing better ways to manage inventory. This would reduce the time needed to manage inventory. This will allow us to free up resources for more productive tasks.
One way to do this is to adopt a Kanban system. A Kanban board can be used to monitor work progress. Kanban systems are where work items travel through a series of states until reaching their final destination. Each state has a different priority level.
For instance, when work moves from one stage to another, the current task is complete enough to be moved to the next stage. However, if a task is still at the beginning stages, it will remain so until it reaches the end of the process.
This allows work to move forward and ensures that no work is missed. With a Kanban board, managers can see exactly how much work is being done at any given moment. This allows them the ability to adjust their workflow using real-time data.
Lean manufacturing can also be used to reduce inventory levels. Lean manufacturing works to eliminate waste throughout every stage of the production chain. Waste includes anything that does not add value to the product. The following are examples of common waste types:
-
Overproduction
-
Inventory
-
Unnecessary packaging
-
Materials in excess
By implementing these ideas, manufacturers can improve efficiency and cut costs.
Is automation important in manufacturing?
Automation is essential for both manufacturers and service providers. They can provide services more quickly and efficiently thanks to automation. In addition, it helps them reduce costs by reducing human errors and improving productivity.
What are the responsibilities of a logistic manager?
Logistics managers make sure all goods are delivered on schedule and without damage. This is done using his/her knowledge of the company's products. He/she should ensure that sufficient stock is available in order to meet customer demand.
What skills is required for a production planner?
A production planner must be organized, flexible, and able multitask to succeed. Communication skills are essential to ensure that you can communicate effectively with clients, colleagues, and customers.
Statistics
- (2:04) MTO is a production technique wherein products are customized according to customer specifications, and production only starts after an order is received. (oracle.com)
- In 2021, an estimated 12.1 million Americans work in the manufacturing sector.6 (investopedia.com)
- [54][55] These are the top 50 countries by the total value of manufacturing output in US dollars for its noted year according to World Bank.[56] (en.wikipedia.org)
- According to the United Nations Industrial Development Organization (UNIDO), China is the top manufacturer worldwide by 2019 output, producing 28.7% of the total global manufacturing output, followed by the United States, Japan, Germany, and India.[52][53] (en.wikipedia.org)
- According to a Statista study, U.S. businesses spent $1.63 trillion on logistics in 2019, moving goods from origin to end user through various supply chain network segments. (netsuite.com)
External Links
How To
How to use 5S to increase Productivity in Manufacturing
5S stands to stand for "Sort", “Set In Order", “Standardize", and "Store". Toyota Motor Corporation developed the 5S method in 1954. This methodology helps companies improve their work environment to increase efficiency.
The idea behind standardizing production processes is to make them repeatable and measurable. This means that daily tasks such as cleaning and sorting, storage, packing, labeling, and packaging are possible. Workers can be more productive by knowing what to expect.
Implementing 5S requires five steps. These are Sort, Set In Order, Standardize. Separate. And Store. Each step involves a different action which leads to increased efficiency. For example, when you sort things, you make them easy to find later. You arrange items by placing them in an order. After you have divided your inventory into groups you can store them in easy-to-reach containers. You can also label your containers to ensure everything is properly labeled.
Employees need to reflect on how they do their jobs. Employees need to understand the reasons they do certain jobs and determine if there is a better way. To implement the 5S system, employees must acquire new skills and techniques.
In addition to improving efficiency, the 5S system also increases morale and teamwork among employees. They will feel motivated to strive for higher levels of efficiency once they start to see results.