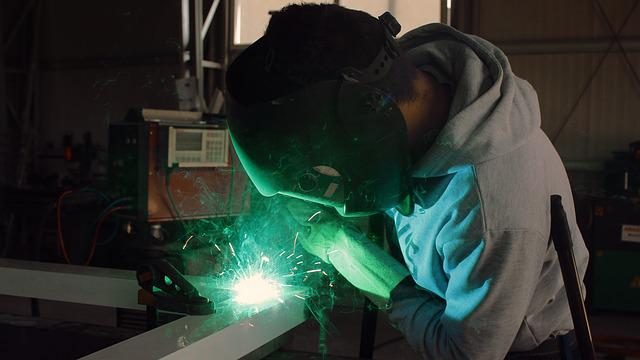
If you want to ensure your product is profitable, it is important to factor in manufacturing costs. If you intend to sell wooden tabletops furniture, you might need to purchase glue, wood and other materials. It is essential that you find a trusted supplier of top quality raw material to ensure your product lasts. You might end up with a substandard product that is not durable and could lose your revenue.
The most effective way to understand manufacturing cost is to break it down into three main categories. Each one of these costs will influence the final product price. One of the most important components in a manufacturing cost is its unit cost. This is the price it takes to produce an item. This number is a good way to begin, but it is not easy to determine.
The units-per-hour or unit-per-unit ratio is a good rule of thumb to use when determining the most cost-effective manufacturing process for your company. To illustrate, let's say you want to make 5,000 wooden table tops. You can find the average cost by subtracting the amount of time required to complete the project.
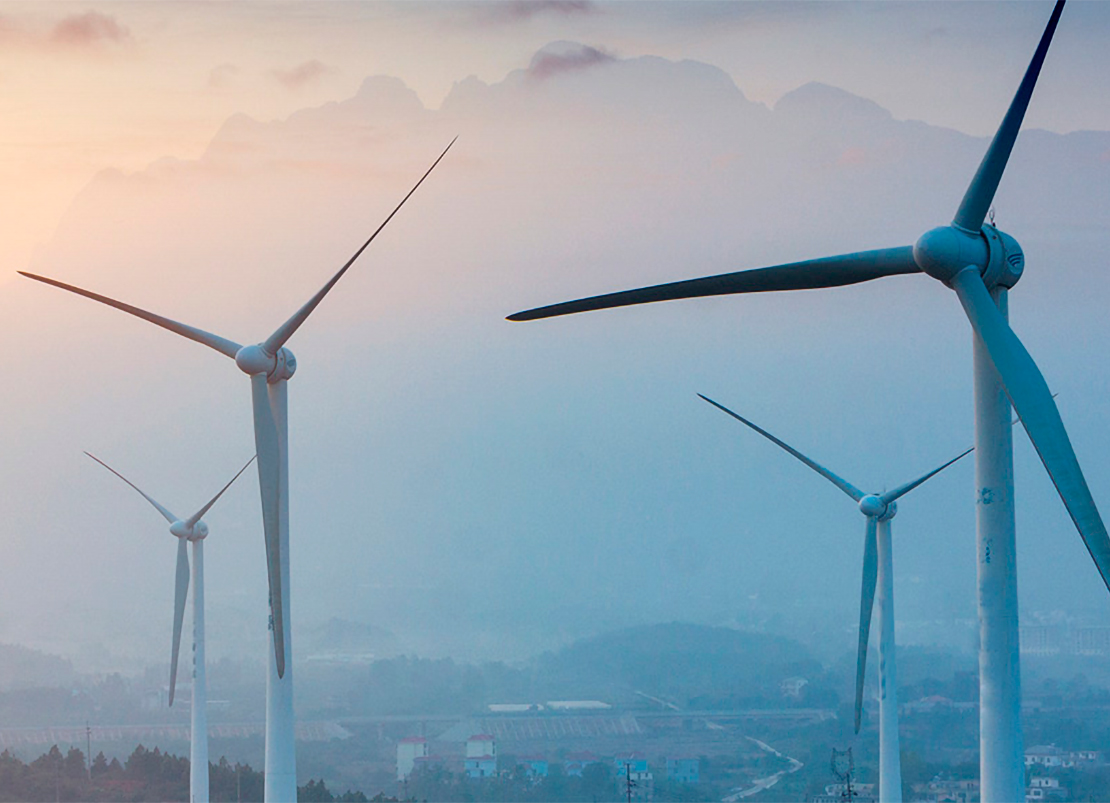
In addition to direct labor and manufacturing equipment, you'll also need to budget for administrative and general expenses. Advertising costs, office supplies and rent are all possible. Also, you'll need to spend a lot of money to comply with regulatory requirements. However, online inventory control software is available to track and forecast production.
Direct labor costs are wages paid to workers in factories. This includes those who actually prepare the goods for production. They may also include maintenance staff, sanitation personnel, and bookkeepers. The hourly rate of direct labor averages around $150.
Manufacturing has indirect costs. These include utility bills and maintenance costs. In order to calculate the unit per hour, you must first calculate the labor costs involved in preparing the material and assembling it. Then, you must also consider the delivery costs to the customer. A manufacturing overhead account will help you to calculate the total cost of your operation, and will provide you with an estimate of what your overhead will be for the coming fiscal year.
Other items to consider when calculating the manufacturing cost are the direct and indirect materials used to manufacture a particular product. These include cotton, thread, and wood. A poor quality product can lead to inferior results. You will also need to test the safety of your products if you are a food processor in certain areas.
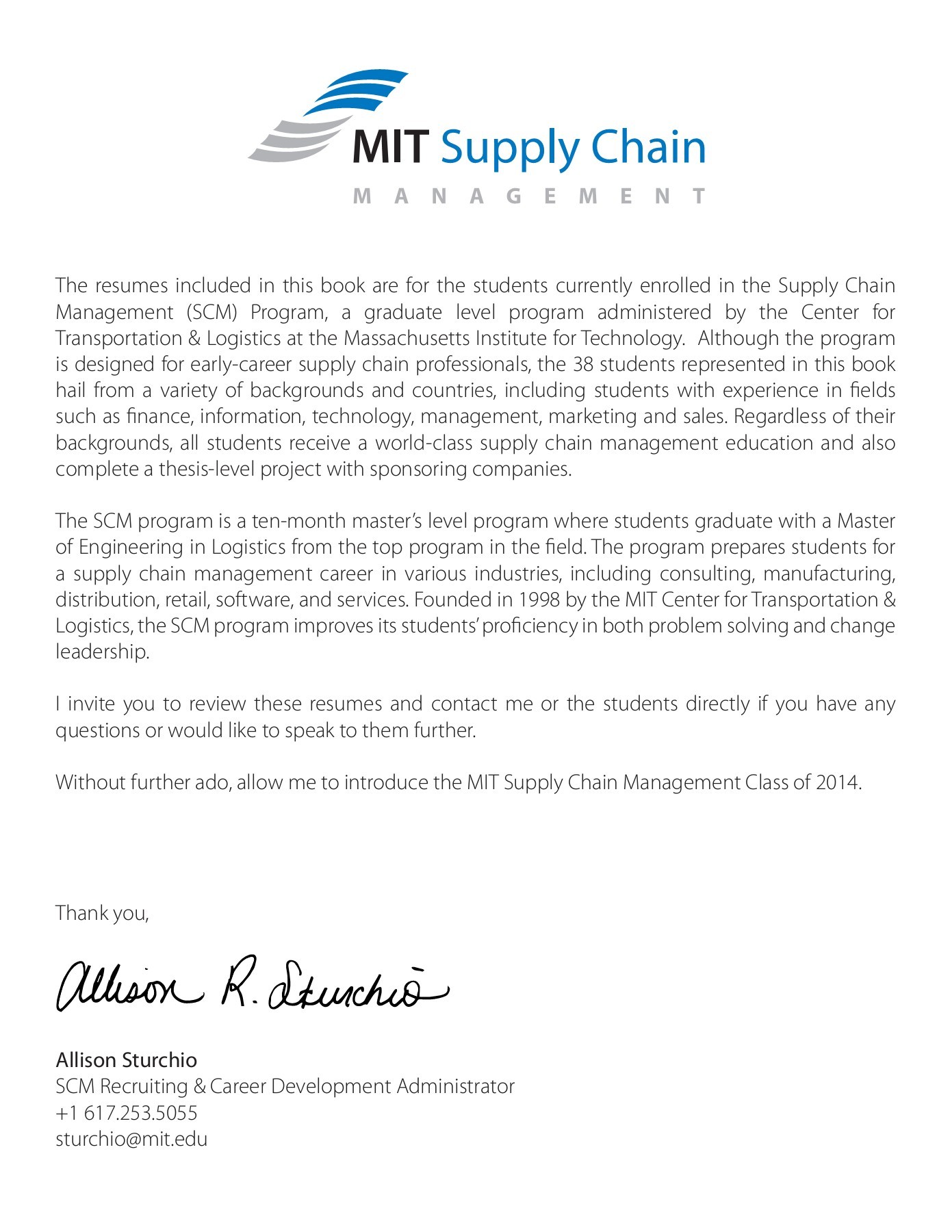
It is important to determine whether you should begin producing new products by knowing how much each unit costs. You should also know the price you should charge for your products to increase your business' profitability.
FAQ
What does manufacturing mean?
Manufacturing Industries are businesses that produce products for sale. Consumers are the people who purchase these products. These companies employ many processes to achieve this purpose, such as production and distribution, retailing, management and so on. These companies produce goods using raw materials and other equipment. This includes all types if manufactured goods.
How can we improve manufacturing efficiency?
First, determine which factors have the greatest impact on production time. Then we need to find ways to improve these factors. If you aren't sure where to begin, think about the factors that have the greatest impact on production time. Once you have identified the factors, then try to find solutions.
What makes a production planner different from a project manger?
The main difference between a production planner and a project manager is that a project manager is usually the person who plans and organizes the entire project, whereas a production planner is mainly involved in the planning stage of the project.
What is the role of a production manager?
Production planners ensure that all project aspects are completed on time, within budget and within the scope. They also ensure the quality of the product and service meets the client's requirements.
What does it take for a logistics enterprise to succeed?
To be a successful businessman in logistics, you will need many skills and knowledge. Good communication skills are essential to effectively communicate with your suppliers and clients. You need to understand how to analyze data and draw conclusions from it. You will need to be able handle pressure well and work in stressful situations. To increase efficiency and creativity, you need to be creative. You must be a strong leader to motivate others and direct them to achieve organizational goals.
You must be organized to meet tight deadlines.
Can we automate some parts of manufacturing?
Yes! Yes. The Egyptians discovered the wheel thousands and years ago. Today, robots assist in the assembly of lines.
In fact, there are several applications of robotics in manufacturing today. These include:
-
Automated assembly line robots
-
Robot welding
-
Robot painting
-
Robotics inspection
-
Robots create products
There are many other examples of how manufacturing could benefit from automation. For example, 3D printing allows us to make custom products without having to wait for weeks or months to get them manufactured.
Statistics
- Job #1 is delivering the ordered product according to specifications: color, size, brand, and quantity. (netsuite.com)
- According to a Statista study, U.S. businesses spent $1.63 trillion on logistics in 2019, moving goods from origin to end user through various supply chain network segments. (netsuite.com)
- According to the United Nations Industrial Development Organization (UNIDO), China is the top manufacturer worldwide by 2019 output, producing 28.7% of the total global manufacturing output, followed by the United States, Japan, Germany, and India.[52][53] (en.wikipedia.org)
- You can multiply the result by 100 to get the total percent of monthly overhead. (investopedia.com)
- [54][55] These are the top 50 countries by the total value of manufacturing output in US dollars for its noted year according to World Bank.[56] (en.wikipedia.org)
External Links
How To
How to use lean manufacturing in the production of goods
Lean manufacturing is a management system that aims at increasing efficiency and reducing waste. It was developed in Japan during the 1970s and 1980s by Taiichi Ohno, who received the Toyota Production System (TPS) award from TPS founder Kanji Toyoda. Michael L. Watkins published the "The Machine That Changed the World", the first book about lean manufacturing. It was published in 1990.
Lean manufacturing, often described as a set and practice of principles, is aimed at improving the quality, speed, cost, and efficiency of products, services, and other activities. It emphasizes eliminating waste and defects throughout the value stream. Just-in-time (JIT), zero defect (TPM), and 5S are all examples of lean manufacturing. Lean manufacturing focuses on eliminating non-value-added activities such as rework, inspection, and waiting.
Lean manufacturing not only improves product quality but also reduces costs. Companies can also achieve their goals faster by reducing employee turnover. Lean manufacturing is a great way to manage the entire value chain including customers, suppliers, distributors and retailers as well as employees. Lean manufacturing practices are widespread in many industries. Toyota's philosophy, for example, is what has enabled it to be successful in electronics, automobiles, medical devices, healthcare and chemical engineering as well as paper and food.
Five fundamental principles underlie lean manufacturing.
-
Define Value- Identify the added value your company brings to society. What makes you stand out from your competitors?
-
Reduce Waste – Eliminate all activities that don't add value throughout the supply chain.
-
Create Flow - Make sure work runs smoothly without interruptions.
-
Standardize and simplify – Make processes as repeatable and consistent as possible.
-
Build Relationships- Develop personal relationships with both internal as well as external stakeholders.
Although lean manufacturing has always been around, it is gaining popularity in recent years because of a renewed interest for the economy after 2008's global financial crisis. Many businesses are now using lean manufacturing to improve their competitiveness. Some economists even believe that lean manufacturing can be a key factor in economic recovery.
Lean manufacturing is now becoming a common practice in the automotive industry, with many benefits. These include higher customer satisfaction, lower inventory levels, lower operating expenses, greater productivity, and improved overall safety.
You can apply Lean Manufacturing to virtually any aspect of your organization. It is especially useful for the production aspect of an organization, as it ensures that every step in the value chain is efficient and effective.
There are three main types in lean manufacturing
-
Just-in-Time Manufacturing: Also known as "pull systems", this type of lean manufacturing uses just-in-time manufacturing (JIT). JIT is a process in which components can be assembled at the point they are needed, instead of being made ahead of time. This method reduces lead times, increases availability, and decreases inventory.
-
Zero Defects Manufacturing (ZDM),: ZDM is a system that ensures no defective units are left the manufacturing facility. If a part needs to be fixed during the assembly line, it should be repaired rather than scrapped. This applies to finished products, which may need minor repairs before they are shipped.
-
Continuous Improvement (CI),: Continuous improvement aims improve the efficiency and effectiveness of operations by continuously identifying issues and making changes to reduce waste. Continuous Improvement involves continuous improvement of processes.