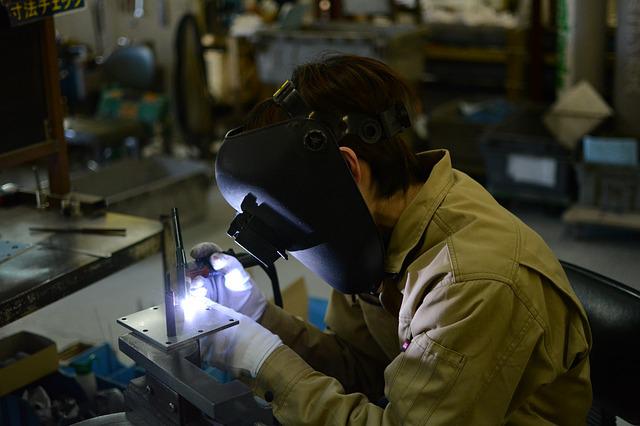
Japanese factories produce high-quality goods at low costs. They make up five percent of the country’s GDP and are the economic backbone. They have been challenged by tighter standards and increased competition as well as the cost pressures from the recent recession.
For example, last year, a government white paper found that Japanese firms were unprepared to deal with a parts procurement cutoff. The Japanese auto industry was hard hit by the recession. The car manufacturing industry is dependent on around 30,000 parts. Therefore, a disruption in the supply chain can cause production to stop. Some parts cannot be replaced.
Japanese manufacturers closely work with suppliers to address problems and improve efficiency, in order not to compromise the quality of their products. They welcome feedback from employees, salesmen, quality inspectors and others.
Japanese manufacturers have been concerned by the increasing number of factory floor accidents. There have been many safety scandals throughout the country's production sector. This has led the government to pay more attention to the standards of work in factories.
Another issue that has been negatively affecting production of Japanese goods has been the influx non-regular workforce. The influx of non-regular labor allows companies to lower labor costs but increases the risk of accidents, and de-skills the production floor. To make their workers safer and more productive, companies have started to train regular employees.
Japan's increasing labor shortage is due to its declining birthrate. A 25-year high number of Japanese companies are complaining of a lack of labor. Japanese companies will face further challenges if their labor force shrinks.
Despite the shortage of skilled workers, a large percentage of factories have been cutting costs. A growing number of so-called "factries" employ fewer than ten people. Many of these small workshops create the finest equipment in the entire world.
China and South Korea are threatening the Japanese manufacturing industry. Many factories are working to reduce costs and improve productivity. The Japanese government warns that the industry could lose its competitive edge on overseas markets.
As Japan faces increased competition from Asia and abroad, it is facing questions about whether it can adjust its processes to meet demand and adapt quickly enough. The demand for skilled workers will rise even if Japan can adapt its processes to meet the increased competition from Asia and abroad.
Japanese factories are a major source of components for global markets. They also supply advanced materials like silicon chips which are used in computers and smart phone. While Chinese factories specialize in low-cost assembly operations, they rely on Japan for essential components.
Despite their efforts to improve productivity and quality, Japanese companies have been subject to increased competition from overseas. Due to the economic downturn, their products were less valued in the domestic markets. This has forced them to cut costs. Despite these challenges the Japanese have managed to maintain a high level production standard.
FAQ
What skills does a production planner need?
A production planner must be organized, flexible, and able multitask to succeed. You must also be able to communicate effectively with clients and colleagues.
What are the 7 Rs of logistics?
The acronym 7Rs of Logistics refers to the seven core principles of logistics management. It was developed and published by the International Association of Business Logisticians in 2004 as part of the "Seven Principles of Logistics Management".
The following letters make up the acronym:
-
Responsible - ensure that actions are in compliance with legal requirements and do not cause harm to others.
-
Reliable: Have faith in your ability or the ability to honor any promises made.
-
Be responsible - Use resources efficiently and avoid wasting them.
-
Realistic – Consider all aspects, including cost-effectiveness as well as environmental impact.
-
Respectful: Treat others with fairness and equity
-
Reliable - Find ways to save money and increase your productivity.
-
Recognizable - provide customers with value-added services.
How can manufacturing avoid production bottlenecks
The key to avoiding bottlenecks in production is to keep all processes running smoothly throughout the entire production cycle, from the time you receive an order until the time when the product ships.
This includes planning for both capacity requirements and quality control measures.
The best way to do this is to use continuous improvement techniques such as Six Sigma.
Six Sigma Management System is a method to increase quality and reduce waste throughout your organization.
It focuses on eliminating variation and creating consistency in your work.
How can we increase manufacturing efficiency?
The first step is to determine the key factors that impact production time. We must then find ways that we can improve these factors. If you don’t know where to begin, consider which factors have the largest impact on production times. Once you've identified them all, find solutions to each one.
Statistics
- Job #1 is delivering the ordered product according to specifications: color, size, brand, and quantity. (netsuite.com)
- In 2021, an estimated 12.1 million Americans work in the manufacturing sector.6 (investopedia.com)
- In the United States, for example, manufacturing makes up 15% of the economic output. (twi-global.com)
- According to the United Nations Industrial Development Organization (UNIDO), China is the top manufacturer worldwide by 2019 output, producing 28.7% of the total global manufacturing output, followed by the United States, Japan, Germany, and India.[52][53] (en.wikipedia.org)
- It's estimated that 10.8% of the U.S. GDP in 2020 was contributed to manufacturing. (investopedia.com)
External Links
How To
Six Sigma: How to Use it in Manufacturing
Six Sigma can be described as "the use of statistical process control (SPC), techniques to achieve continuous improvement." It was developed by Motorola's Quality Improvement Department at their plant in Tokyo, Japan, in 1986. Six Sigma's core idea is to improve the quality of processes by standardizing and eliminating defects. Many companies have adopted this method in recent years. They believe there is no such thing a perfect product or service. The main goal of Six Sigma is to reduce variation from the mean value of production. If you take a sample and compare it with the average, you will be able to determine how much of the production process is different from the norm. If the deviation is excessive, it's likely that something needs to be fixed.
Understanding the dynamics of variability within your business is the first step in Six Sigma. Once you've understood that, you'll want to identify sources of variation. This will allow you to decide if these variations are random and systematic. Random variations are caused when people make mistakes. While systematic variations are caused outside of the process, they can occur. For example, if you're making widgets, and some of them fall off the assembly line, those would be considered random variations. You might notice that your widgets always fall apart at the same place every time you put them together.
Once you have identified the problem, you can design solutions. This could mean changing your approach or redesigning the entire process. You should then test the changes again after they have been implemented. If they don't work, you will need to go back to the drawing boards and create a new plan.