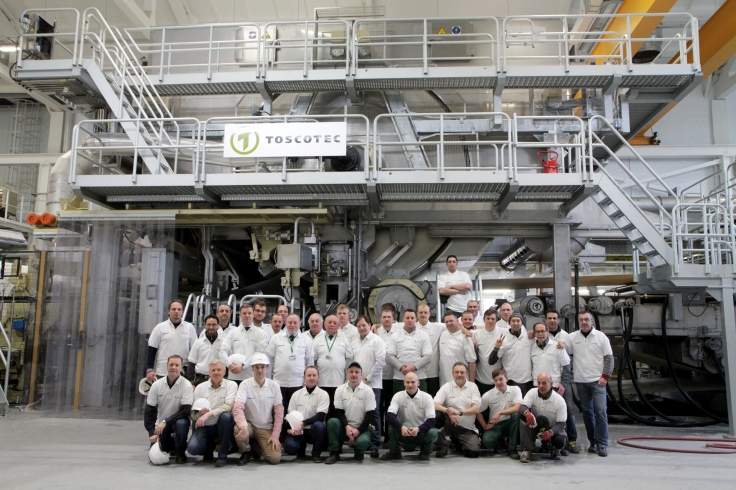
Materials engineers create, design, and test new materials in order to develop tomorrow's technologies. They work with metals, ceramics, plastics, and composites to create materials that meet certain chemical, electrical, and mechanical requirements.
What does a material engineer do?
Material engineers process, test and develop raw materials to be used for a variety products like aircraft wings, computer chip, biomedical device, or golf clubs. These engineers study and evaluate the structures and properties of metals, ceramics, plastics, nanomaterials (extremely small substances), and other substances in order to create new materials that meet particular chemical, electrical, and mechanical requirements.
The responsibilities of a materials engineer vary according to the specific type of materials that they are working with and the industry in which they are employed. They are usually responsible for budgeting, quality control and assessing production costs.
What is an materials science engineer (MSI)?
A materials science engineer works with a variety of different materials including metals, ceramics, and composites to make them stronger, lighter, and more durable. A materials science engineer can create new materials or improve on existing ones.
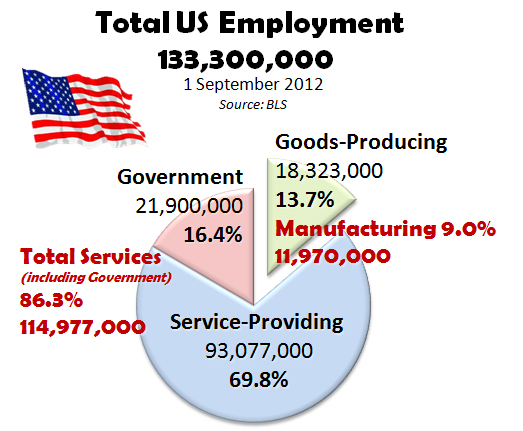
What does a materials engineer need?
A bachelor's in engineering or materials sciences is required to become a material engineer. This degree should be a combination of classroom and lab work, with a focus on engineering principles. It can take a few years to complete the program.
After graduation you can get a job as materials engineer and you will earn around PS25,000 each year. Your salary will rise significantly as you gain experience.
How to become a material engineer
The qualifications that you need to become a materials engineer differ between industries and employers. However, most jobs require at least a bachelor's degree in materials science or engineering. This will include studies of chemistry, physics, and mathematics.
Qualifications for a career as a materials science engineer are generally high school diploma and a bachelor's degree in a relevant field such as physics, chemistry or engineering. Most research positions at higher levels require a PhD or a Master's.
How much can I earn as a materials engineering?
The salaries of materials engineers can vary depending on their level of expertise, the industry in which they work and the size of the company. They can also expect to receive bonuses and other perks for their work.
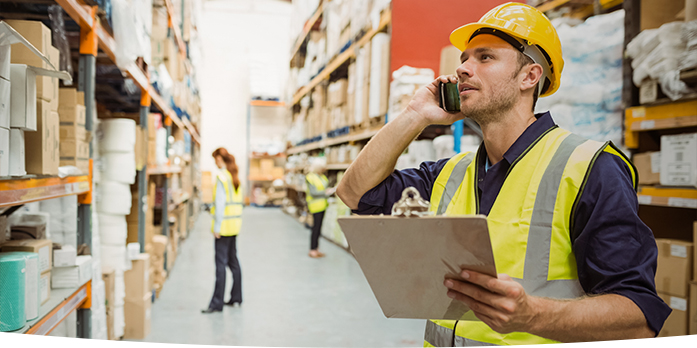
What will the future look like for the Materials Engineering career?
It is predicted that the future of materials engineering will be bright, and there are many opportunities available to those who choose to pursue this career. This is due to an increasing demand for better, more advanced materials, especially in fields like medicine, architecture, and communications.
By obtaining a degree, you can become a materials engineering. You may choose to study metallurgy. chemistry or physics. You will gain the knowledge necessary to start a career and possibly open more doors for you. A degree in a subject such as chemistry will help you with your research and development skills. For more experience, you could work at an engineering company specializing in a particular field of materials.
FAQ
What does it mean to be a manufacturer?
Manufacturing Industries are those businesses that make products for sale. Consumers are the people who purchase these products. These companies use various processes such as production, distribution, retailing, management, etc., to fulfill this purpose. They produce goods from raw materials by using machines and other machinery. This includes all types and varieties of manufactured goods, such as food items, clothings, building supplies, furnitures, toys, electronics tools, machinery vehicles, pharmaceuticals medical devices, chemicals, among others.
Why automate your warehouse
Modern warehousing has seen automation take center stage. With the rise of ecommerce, there is a greater demand for faster delivery times as well as more efficient processes.
Warehouses need to adapt quickly to meet changing needs. Technology investment is necessary to enable warehouses to respond quickly to changing demands. The benefits of automating warehouses are numerous. These are some of the benefits that automation can bring to warehouses:
-
Increases throughput/productivity
-
Reduces errors
-
Increases accuracy
-
Safety is boosted
-
Eliminates bottlenecks
-
Allows companies scale more easily
-
Increases efficiency of workers
-
It gives visibility to everything that happens inside the warehouse
-
Enhances customer experience
-
Improves employee satisfaction
-
Minimizes downtime and increases uptime
-
This ensures that quality products are delivered promptly
-
Eliminates human error
-
Helps ensure compliance with regulations
What is the best way to learn about manufacturing?
The best way to learn about manufacturing is through hands-on experience. If that is not possible, you could always read books or view educational videos.
What's the difference between Production Planning & Scheduling?
Production Planning (PP), also known as forecasting and identifying production capacities, is the process that determines what product needs to be produced at any particular time. Forecasting and identifying production capacity are two key elements to this process.
Scheduling involves the assignment of dates and times to tasks in order to complete them within the timeframe.
What kind of jobs are there in logistics?
Logistics can offer many different jobs. These are some of the jobs available in logistics:
-
Warehouse workers – They load and unload pallets and trucks.
-
Transportation drivers: They drive trucks and trailers and deliver goods and make pick-ups.
-
Freight handlers – They sort and package freight at warehouses.
-
Inventory managers – These people oversee inventory at warehouses.
-
Sales representatives - They sell products to customers.
-
Logistics coordinators - They organize and plan logistics operations.
-
Purchasing agents – They buy goods or services necessary to run a company.
-
Customer service representatives – They answer emails and phone calls from customers.
-
Ship clerks - They issue bills and process shipping orders.
-
Order fillers - They fill orders based on what is ordered and shipped.
-
Quality control inspectors – They inspect incoming and outgoing products to ensure that there are no defects.
-
Others - There is a variety of other jobs in logistics. These include transportation supervisors and cargo specialists.
Statistics
- In the United States, for example, manufacturing makes up 15% of the economic output. (twi-global.com)
- (2:04) MTO is a production technique wherein products are customized according to customer specifications, and production only starts after an order is received. (oracle.com)
- According to the United Nations Industrial Development Organization (UNIDO), China is the top manufacturer worldwide by 2019 output, producing 28.7% of the total global manufacturing output, followed by the United States, Japan, Germany, and India.[52][53] (en.wikipedia.org)
- Many factories witnessed a 30% increase in output due to the shift to electric motors. (en.wikipedia.org)
- In 2021, an estimated 12.1 million Americans work in the manufacturing sector.6 (investopedia.com)
External Links
How To
Six Sigma and Manufacturing
Six Sigma refers to "the application and control of statistical processes (SPC) techniques in order to achieve continuous improvement." It was developed by Motorola's Quality Improvement Department at their plant in Tokyo, Japan, in 1986. Six Sigma is a method to improve quality through standardization and elimination of defects. In recent years, many companies have adopted this method because they believe there is no such thing as perfect products or services. The main goal of Six Sigma is to reduce variation from the mean value of production. This means that if you take a sample of your product, then measure its performance against the average, you can find out what percentage of the time the process deviates from the norm. If this deviation is too big, you know something needs fixing.
Understanding the nature of variability in your business is the first step to Six Sigma. Once you understand this, you can then identify the causes of variation. These variations can also be classified as random or systematic. Random variations are caused by human errors. Systematic variations can be caused by outside factors. You could consider random variations if some widgets fall off the assembly lines. However, if you notice that every time you assemble a widget, it always falls apart at exactly the same place, then that would be a systematic problem.
Once you've identified where the problems lie, you'll want to design solutions to eliminate those problems. That solution might involve changing the way you do things or redesigning the process altogether. Test them again once you've implemented the changes. If they don't work you need to rework them and come up a better plan.