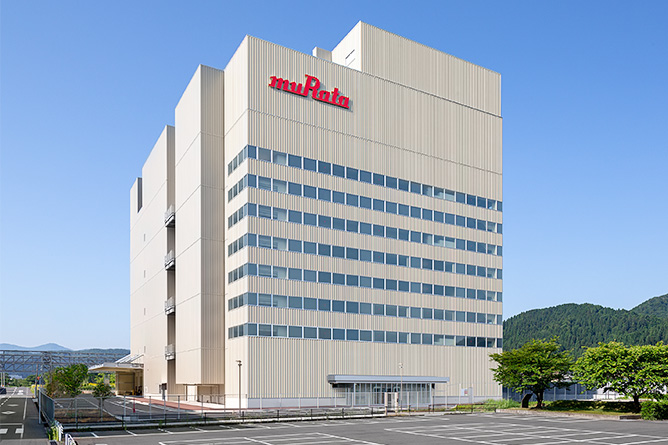
Alaska is a challenging place to offer logistics services. From the climate to the rugged terrain, Alaska offers a unique set of logistical challenges. The state is also one among the least populated in the United States. Because of this, transportation options are limited during some months. Alaska is home to many logistics companies that will help you move your products around the state. These services can be anything from freight forwarding to intermodal transport.
One of the largest logistics providers in Alaska is the Port of Alaska. This gateway services 85% the state's residents. It is the only reliable gateway for large-volume freight deliveries to Anchorage and Fairbanks. Port of Alaska not only serves as a major hub for cargo transport, but also offers support to the seafood industry.
Another Alaska logistics provider that has a significant impact on the state is CP Logistics. The company offers supply chain management services in the United States, Canada, and Caribbean. Third-party audits are used by the company to ensure safety and quality. A robust SQF Food Safety Program is also in place. The company has recently made a name for itself in the logistics industry by offering a mobile app that gives real-time shipment information.
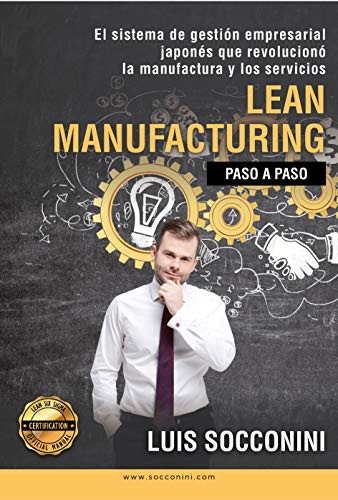
Carlile Logistics, another logistics company worth considering is Carlile Logistics. The company is a provider of truck cabs, fuel tanksers and cargo trailers. This company is part of the Saltchuk Resources group of companies. It places an emphasis on innovation and technology. Located in Alaska, the company supports a wide range of projects, from oil exploration to building projects. The company continues to adapt to changing client demands.
PRL Logistics Inc. in Alaska is another notable logistics company. This company provides logistical support for Gallagher Marine Systems. They have a long history of providing logistics support in Alaska. They have worked with PenAir, Bristow Aviation and DHL. Their team has also worked in the Aleutians, Southeast and elsewhere.
Alaska Logistics, LLC, is another logistics company making a splash in Alaska. Alaska Logistics LLC offers container and barge transport to Alaska customers. Additionally, they now offer transportation of other cargo types. Their services include transporting bulk commodities and containers, as well as sanitary bulk commodities. They serve the ports of Western Alaska and nearby villages.
Any logistics company in Alaska should have a good reputation for providing excellent service. It is vital to be ready for anything. Alaska is home of some of most extreme weather. There are also risks of flooding and eruptions from volcanoes. This can lead to major damage. A limited highway system is another problem. It is therefore essential that logistics providers are prepared to meet all the state's logistical needs.
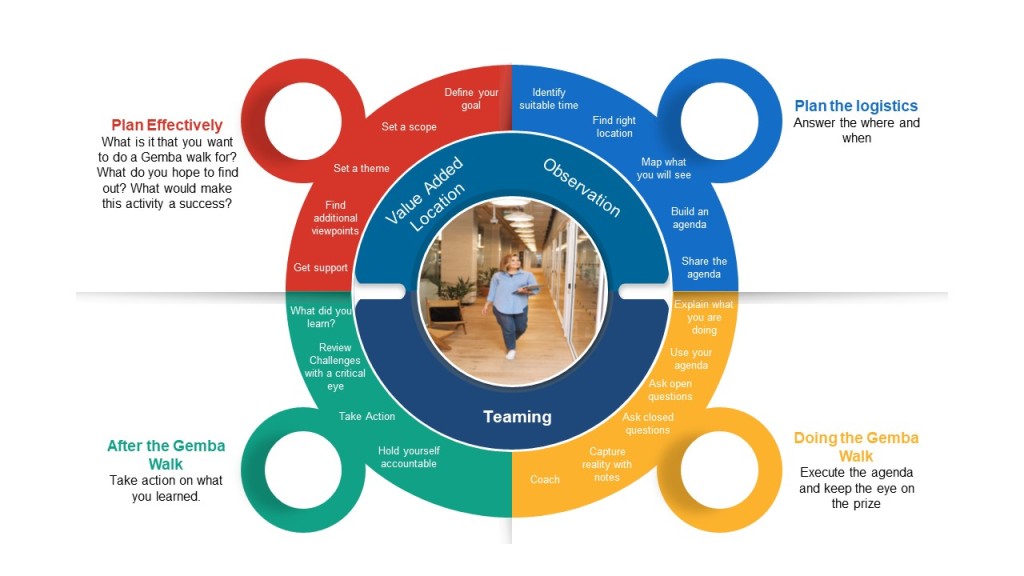
Finally, moving cement in Alaska is one of the most difficult logistical problems. Cement is necessary for construction projects. It must often be transported by plane. This can be tricky, so it is worth planning ahead.
FAQ
What are the four types in manufacturing?
Manufacturing refers the process of turning raw materials into useful products with machines and processes. Manufacturing can include many activities such as designing and building, testing, packaging shipping, selling, servicing, and other related activities.
Can certain manufacturing steps be automated?
Yes! Automation has been around since ancient times. The wheel was invented by the Egyptians thousands of years ago. To help us build assembly lines, we now have robots.
There are many applications for robotics in manufacturing today. These include:
-
Automated assembly line robots
-
Robot welding
-
Robot painting
-
Robotics inspection
-
Robots that make products
Manufacturing could also benefit from automation in other ways. 3D printing is a way to make custom products quickly and without waiting weeks or months for them to be manufactured.
What is the job of a production plan?
A production planner ensures all aspects of the project are delivered on time, within budget, and within scope. They also ensure the quality of the product and service meets the client's requirements.
Statistics
- Job #1 is delivering the ordered product according to specifications: color, size, brand, and quantity. (netsuite.com)
- In 2021, an estimated 12.1 million Americans work in the manufacturing sector.6 (investopedia.com)
- Many factories witnessed a 30% increase in output due to the shift to electric motors. (en.wikipedia.org)
- You can multiply the result by 100 to get the total percent of monthly overhead. (investopedia.com)
- According to a Statista study, U.S. businesses spent $1.63 trillion on logistics in 2019, moving goods from origin to end user through various supply chain network segments. (netsuite.com)
External Links
How To
How to use Lean Manufacturing in the production of goods
Lean manufacturing (or lean manufacturing) is a style of management that aims to increase efficiency, reduce waste and improve performance through continuous improvement. It was created in Japan by Taiichi Ohno during the 1970s and 80s. He received the Toyota Production System award (TPS), from Kanji Toyoda, founder of TPS. Michael L. Watkins published the original book on lean manufacturing, "The Machine That Changed the World," in 1990.
Lean manufacturing is often described as a set if principles that help improve the quality and speed of products and services. It is about eliminating defects and waste from all stages of the value stream. Lean manufacturing can be described as just-in–time (JIT), total productive maintenance, zero defect (TPM), or even 5S. Lean manufacturing seeks to eliminate non-value added activities, such as inspection, work, waiting, and rework.
Lean manufacturing is a way for companies to achieve their goals faster, improve product quality, and lower costs. Lean manufacturing has been deemed one of the best ways to manage the entire value-chain, including customers, distributors as well retailers and employees. Many industries worldwide use lean manufacturing. Toyota's philosophy is the foundation of its success in automotives, electronics and appliances, healthcare, chemical engineers, aerospace, paper and food, among other industries.
Five fundamental principles underlie lean manufacturing.
-
Define Value - Identify the value your business adds to society and what makes you different from competitors.
-
Reduce Waste - Remove any activity which doesn't add value to your supply chain.
-
Create Flow - Ensure work moves smoothly through the process without interruption.
-
Standardize and simplify - Make your processes as consistent as possible.
-
Build Relationships - Establish personal relationships with both internal and external stakeholders.
Lean manufacturing isn’t new, but it has seen a renewed interest since 2008 due to the global financial crisis. Many businesses have adopted lean manufacturing techniques to help them become more competitive. Many economists believe lean manufacturing will play a major role in economic recovery.
Lean manufacturing is becoming a popular practice in automotive. It has many advantages. These include better customer satisfaction and lower inventory levels. They also result in lower operating costs.
The principles of lean manufacturing can be applied in almost any area of an organization. This is because it ensures efficiency and effectiveness in all stages of the value chain.
There are three main types:
-
Just-in-Time Manufacturing (JIT): This type of lean manufacturing is commonly referred to as "pull systems." JIT stands for a system where components are assembled on the spot rather than being made in advance. This strategy aims to decrease lead times, increase availability of parts and reduce inventory.
-
Zero Defects Manufacturing, (ZDM): ZDM is focused on ensuring that no defective products leave the manufacturing facility. Repairing a part that is damaged during assembly should be done, not scrapping. This is true even for finished products that only require minor repairs prior to shipping.
-
Continuous Improvement (CI): CI aims to improve the efficiency of operations by continuously identifying problems and making changes in order to eliminate or minimize waste. It involves continuous improvement of processes, people, and tools.