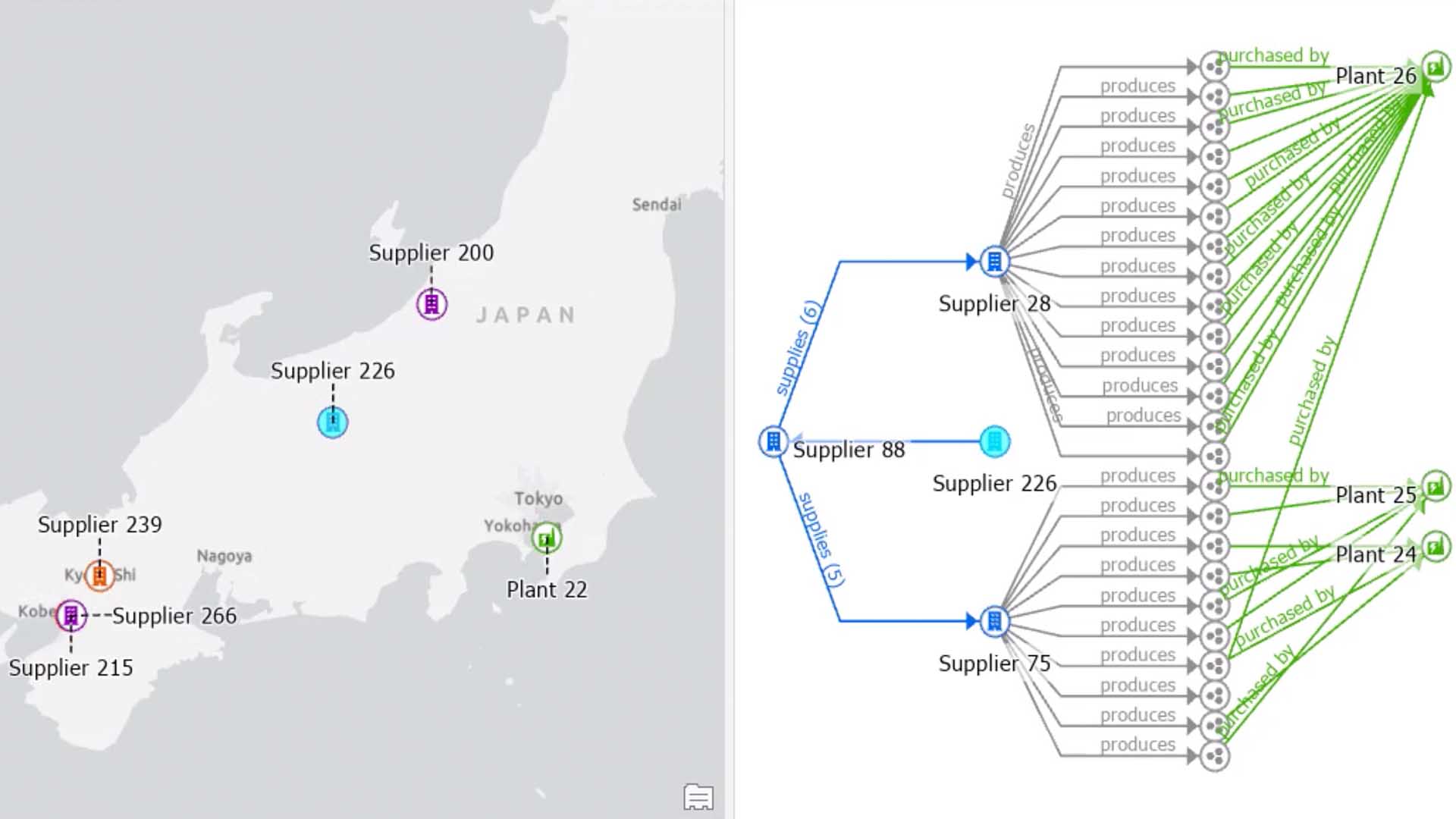
Columbus, Ohio is central Ohio's largest city has a wide range of activities and attractions. Columbus is a destination that attracts both locals as well as tourists. The city boasts four top-class golf courses, an internationally acclaimed park system and plenty of entertainment and arts. It is also ranked among America's most charming metropolitan areas. A number of high-tech companies are located in the area, which makes them a great choice for corporate recruiting. Visit the Columbus Tech Council site to see a list all of the tech companies located in the region. The council serves as a hub for all things technology related, including job opportunities or networking opportunities. You can find a job, or a new hobby, in Columbus' tech scene. Columbus offers everything you need, whether you are looking for a job as an entry-level employee or a senior executive position. You will find a variety of employers looking to hire you in the city, such as JP Morgan, Limited Brands, Time Warner and JP Morgan. Columbus is home not only to the many obvious perks but also to several museums and art gallery, such as the Franklin Park Conservatory. This is not to mention the plethora of theatres and casinos. The city also has one of the best public transportation systems in America.
FAQ
Is automation important for manufacturing?
Automating is not just important for manufacturers, but also for service providers. It allows them provide faster and more efficient services. It helps them to lower costs by reducing human errors, and improving productivity.
What are the 7 R's of logistics?
The 7R's of Logistics is an acronym for the seven basic principles of logistics management. It was developed and published by the International Association of Business Logisticians in 2004 as part of the "Seven Principles of Logistics Management".
The following letters form the acronym:
-
Responsible - ensure that all actions taken are within legal requirements and are not harmful to others.
-
Reliable - Have confidence in your ability to fulfill all of your commitments.
-
Be responsible - Use resources efficiently and avoid wasting them.
-
Realistic - Consider all aspects of operations, including environmental impact and cost effectiveness.
-
Respectful - Treat people fairly and equitably
-
Reliable - Find ways to save money and increase your productivity.
-
Recognizable - Provide value-added services to customers
How can manufacturing overproduction be reduced?
Better inventory management is key to reducing excess production. This would reduce the time spent on unproductive activities like purchasing, storing and maintaining excess stock. This will allow us to free up resources for more productive tasks.
You can do this by adopting a Kanban method. A Kanban board can be used to monitor work progress. A Kanban system allows work items to move through several states before reaching their final destination. Each state represents an individual priority level.
To illustrate, work can move from one stage or another when it is complete enough for it to be moved to a new stage. However, if a task is still at the beginning stages, it will remain so until it reaches the end of the process.
This allows for work to continue moving forward, while also ensuring that there is no work left behind. Managers can see how much work has been done and the status of each task at any time with a Kanban Board. This allows them the ability to adjust their workflow using real-time data.
Lean manufacturing can also be used to reduce inventory levels. Lean manufacturing focuses on eliminating waste throughout the entire production chain. Anything that doesn't add value to the product is considered waste. Here are some examples of common types.
-
Overproduction
-
Inventory
-
Unnecessary packaging
-
Exceed materials
These ideas can help manufacturers improve efficiency and reduce costs.
Statistics
- According to the United Nations Industrial Development Organization (UNIDO), China is the top manufacturer worldwide by 2019 output, producing 28.7% of the total global manufacturing output, followed by the United States, Japan, Germany, and India.[52][53] (en.wikipedia.org)
- Job #1 is delivering the ordered product according to specifications: color, size, brand, and quantity. (netsuite.com)
- (2:04) MTO is a production technique wherein products are customized according to customer specifications, and production only starts after an order is received. (oracle.com)
- Many factories witnessed a 30% increase in output due to the shift to electric motors. (en.wikipedia.org)
- According to a Statista study, U.S. businesses spent $1.63 trillion on logistics in 2019, moving goods from origin to end user through various supply chain network segments. (netsuite.com)
External Links
How To
How to Use 5S for Increasing Productivity in Manufacturing
5S stands for "Sort", "Set In Order", "Standardize", "Separate" and "Store". Toyota Motor Corporation invented the 5S strategy in 1954. It helps companies achieve higher levels of efficiency by improving their work environment.
The basic idea behind this method is to standardize production processes, so they become repeatable, measurable, and predictable. Cleaning, sorting and packing are all done daily. Workers can be more productive by knowing what to expect.
There are five steps to implementing 5S, including Sort, Set In Order, Standardize, Separate and Store. Each step involves a different action which leads to increased efficiency. You can make it easy for people to find things later by sorting them. Once you have placed items in an ordered fashion, you will put them together. After you have divided your inventory into groups you can store them in easy-to-reach containers. Finally, when you label your containers, you ensure everything is labeled correctly.
Employees need to reflect on how they do their jobs. Employees need to be able understand their motivations and discover alternative ways to do them. To implement the 5S system, employees must acquire new skills and techniques.
The 5S Method not only improves efficiency, but it also helps employees to be more productive and happier. As they begin to see improvements, they feel motivated to continue working towards the goal of achieving higher levels of efficiency.