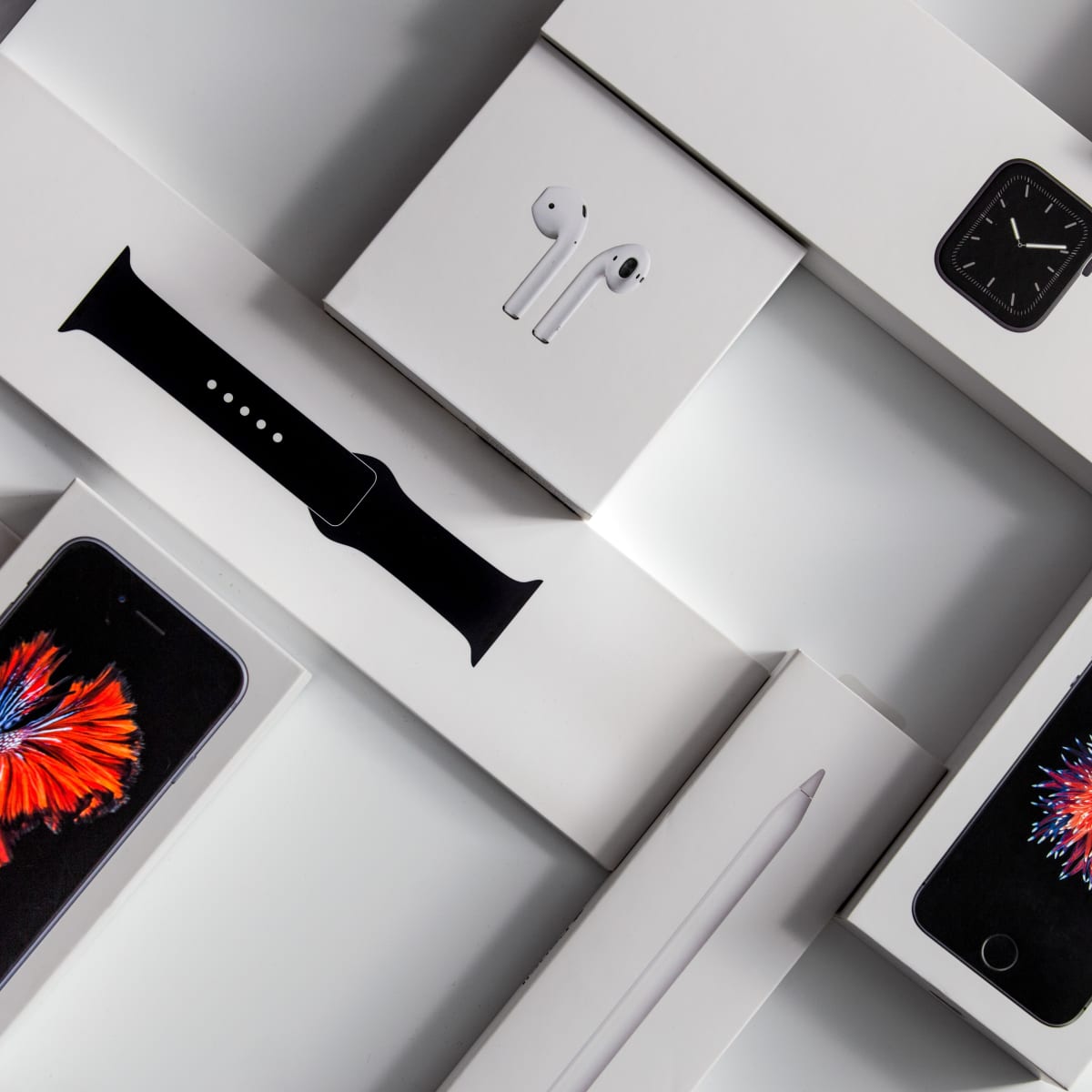
It can be daunting to enter the logistics industry. To get your first job, you might need to take extra classes or do some internships. There are many entry-level logistics jobs that can help you get in the door.
Although most positions require an associates degree, it is possible to obtain a bachelors degree. This degree will allow you to understand how the supply chain works. A degree can help you get professional certifications. You can also take online classes on specialized areas. In some cases, you can get reimbursed for the cost of your graduate program.
Entry level logistics jobs can be found in a variety of industries. For instance, you can work in aerospace manufacturing, oil and gas, or in a freight transportation arrangement. You may also have the opportunity to work in international settings, in a variety industries.
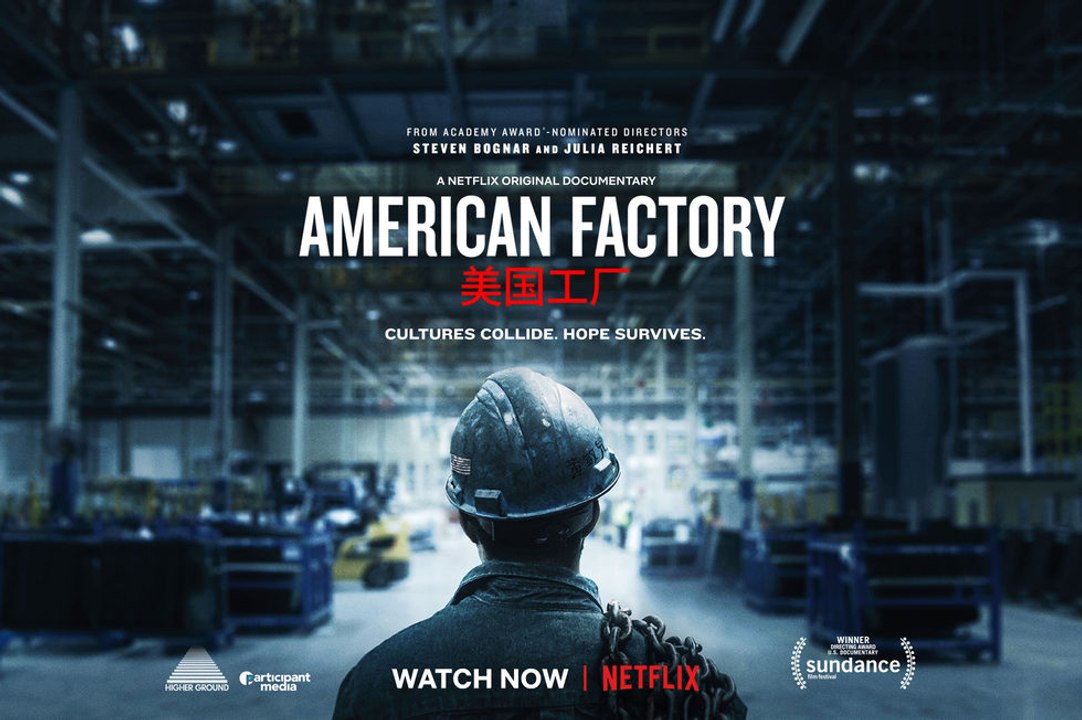
Logistics professionals use both sides of their brains to solve problems. They use their skills to create sustainable supply chains. They have the ability to influence both executive and operational decision-making. This job can be difficult, but rewarding. The logistics industry is growing rapidly in a booming economy.
Strong leadership and management skills are essential for logistics workers. They must be able speak clearly and communicate effectively. They must also be able to use specialized software systems. They may also be responsible to find storage space near shipping ports. They may also be responsible to make sure that the goods are cleared at customs.
Logistics is continuously evolving. The industry is constantly changing with new technologies and business models. Understanding these changes is important. A bachelor's degree can help you become a skilled logistics professional. A bachelor's degree can help you build a professional community. You can also attend industry conferences and seminars. An accredited institution can also award your degree.
Many administrative jobs require strong communication skills and analytical abilities. Some of these roles could be internal to the company. Others may involve customers or suppliers.
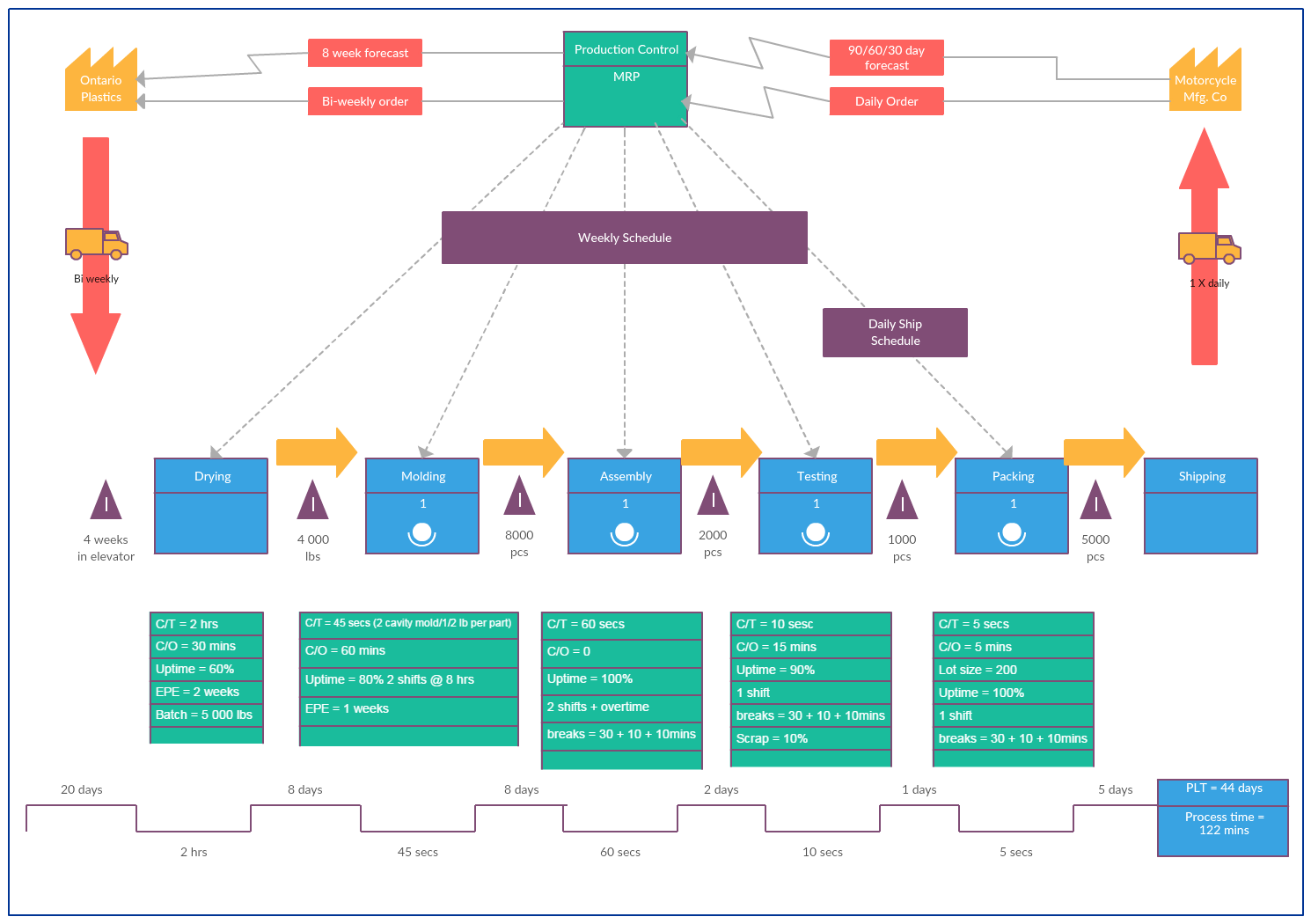
A membership in an industry association is a great way to get started in logistics. These associations provide information about professional certifications as well as industry news and job listings. They may also be able to help you find a mentor. Some organizations even offer graduate fellowships.
Many countries also offer vocational certifications that do not require prior logistics experience. These certifications can be especially valuable to companies that own their own transport fleets. A Certificate of Professional Competence (Road Transport Operations) can also be obtained. This certificate is highly valued by companies with in-house fleets.
Entry-level jobs in logistics are available all across the country. There are also a variety of online resources for job hunters. You can also draw on your network of friends and family for help.
FAQ
How can manufacturing reduce production bottlenecks?
Production bottlenecks can be avoided by ensuring that processes are running smoothly during the entire production process, starting with the receipt of an order and ending when the product ships.
This includes planning for both capacity requirements and quality control measures.
Continuous improvement techniques such Six Sigma can help you achieve this.
Six Sigma management is a system that improves quality and reduces waste within your organization.
It emphasizes consistency and eliminating variance in your work.
What does warehouse mean?
Warehouses and storage facilities are where goods are kept before being sold. It can be an indoor space or an outdoor area. In some cases, it may be a combination of both.
What does the term manufacturing industries mean?
Manufacturing Industries is a group of businesses that produce goods for sale. Consumers are the people who purchase these products. To accomplish this goal, these companies employ a range of processes including distribution, sales, management, and production. They create goods from raw materials, using machines and various other equipment. This includes all types manufactured goods such as clothing, building materials, furniture, electronics, tools and machinery.
Statistics
- In the United States, for example, manufacturing makes up 15% of the economic output. (twi-global.com)
- (2:04) MTO is a production technique wherein products are customized according to customer specifications, and production only starts after an order is received. (oracle.com)
- Many factories witnessed a 30% increase in output due to the shift to electric motors. (en.wikipedia.org)
- It's estimated that 10.8% of the U.S. GDP in 2020 was contributed to manufacturing. (investopedia.com)
- You can multiply the result by 100 to get the total percent of monthly overhead. (investopedia.com)
External Links
How To
How to use the Just In-Time Production Method
Just-intime (JIT), which is a method to minimize costs and maximize efficiency in business process, is one way. It's the process of obtaining the right amount and timing of resources when you need them. This means that you only pay the amount you actually use. The term was first coined by Frederick Taylor, who developed his theory while working as a foreman in the early 1900s. Taylor observed that overtime was paid to workers if they were late in working. He decided to ensure workers have enough time to do their jobs before starting work to improve productivity.
JIT teaches you to plan ahead and prepare everything so you don’t waste time. You should also look at the entire project from start to finish and make sure that you have sufficient resources available to deal with any problems that arise during the course of your project. If you expect problems to arise, you will be able to provide the necessary equipment and personnel to address them. You won't have to pay more for unnecessary items.
There are many JIT methods.
-
Demand-driven: This type of JIT allows you to order the parts/materials required for your project on a regular basis. This will let you track the amount of material left over after you've used it. It will also allow you to predict how long it takes to produce more.
-
Inventory-based: This type allows you to stock the materials needed for your projects ahead of time. This allows for you to anticipate how much you can sell.
-
Project-driven: This means that you have enough money to pay for your project. Once you have an idea of how much material you will need, you can purchase the necessary materials.
-
Resource-based JIT: This is the most popular form of JIT. This is where you assign resources based upon demand. If you have many orders, you will assign more people to manage them. You'll have fewer orders if you have fewer.
-
Cost-based: This approach is very similar to resource-based. However, you don't just care about the number of people you have; you also need to consider how much each person will cost.
-
Price-based pricing: This is similar in concept to cost-based but instead you look at how much each worker costs, it looks at the overall company's price.
-
Material-based: This approach is similar to cost-based. However, instead of looking at the total cost for the company, you look at how much you spend on average on raw materials.
-
Time-based: This is another variation of resource-based JIT. Instead of worrying about how much each worker costs, you can focus on how long the project takes.
-
Quality-based: This is yet another variation of resource-based JIT. Instead of focusing on the cost of each worker or how long it takes, think about how high quality your product is.
-
Value-based JIT : This is the newest type of JIT. In this case, you're not concerned with how well the products perform or whether they meet customer expectations. Instead, your focus is on the value you bring to the market.
-
Stock-based: This inventory-based approach focuses on how many items are being produced at any one time. This method is useful when you want to increase production while decreasing inventory.
-
Just-in time (JIT), planning: This is a combination JIT/supply chain management. It is the process that schedules the delivery of components within a short time of their order. It's important as it reduces leadtimes and increases throughput.