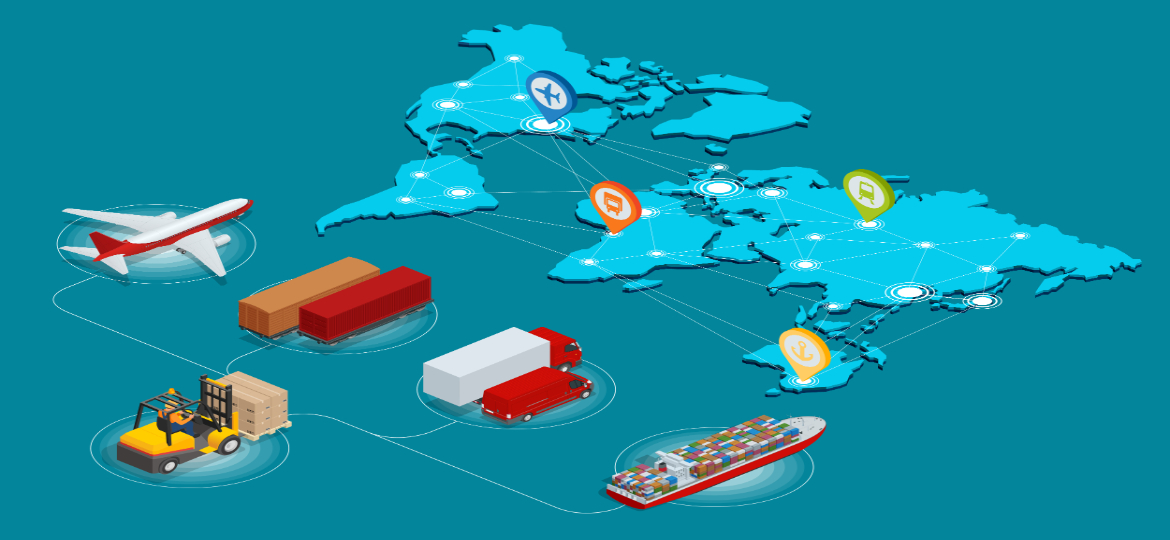
Durable goods have items that don't wear out quickly and can provide utility for a prolonged period. Unlike nondurable goods, which are usually used for a single use, these products are durable. They will provide greater or equal utility over time. For example, a durable car will continue to serve you for years.
Nondurable products can be consumed right away
In contrast to durable goods, which have a long lifespan, nondurable goods are consumed immediately. In a recession, consumers tend to avoid spending money on durable goods but continue to purchase nondurable goods. These items usually have low prices and can often be purchased with cash. Nondurable goods include meats, fruits, vegetables and dairy products. Detergent, dish soap, cosmetics are just a few examples.
Nondurable goods are generally the cheapest type of goods. They last less three years. They are also purchased relatively often, allowing consumers to buy them frequently without concern for their future value. Nondurable goods such as laundry detergent and packaged food are disposable. However, service goods are tangible and are made to meet consumer demands. The perception of a product by consumers is what drives their purchase decisions. This perception can change depending on the product's price.
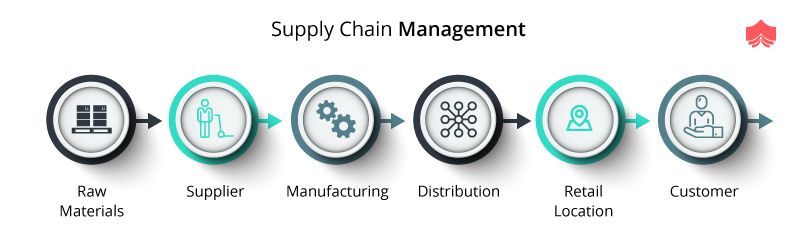
Durable goods are, in contrast, products that are expected provide a steady flow of utility over a time period. These products are also commonly known as consumer durables, and include automobiles, household furnishings, sporting goods, and jewelry. Durables are more popular during economic booms, while nondurables can be bought in periods of economic recession.
Durable goods last more that a year
Durable goods refer to tangible commodities that can last for at most one year when used as intended. They can be classified into two main categories: producer durables as well as consumer durables. Consumer durables consist of household goods, such as cars, boats and furniture. Producer durability includes machinery, appliances, and fine jewellery.
Durable goods should last for at least three years. However, they might need to be serviced or repaired. Durable goods are built so that breakage is unlikely within the first few years. If you take care of your durable goods properly, they can last for up to 20 more years.
Durable goods are often an indicator of economic growth. In order to increase employment and improve investment returns, durable goods should be sold more often. A decline in durable goods sales could indicate a decrease in economic activity. This could mean that consumers are spending their money on repairs and maintenance of their products, rather than buying new ones. The result could be a slowdown or recession in durable goods.
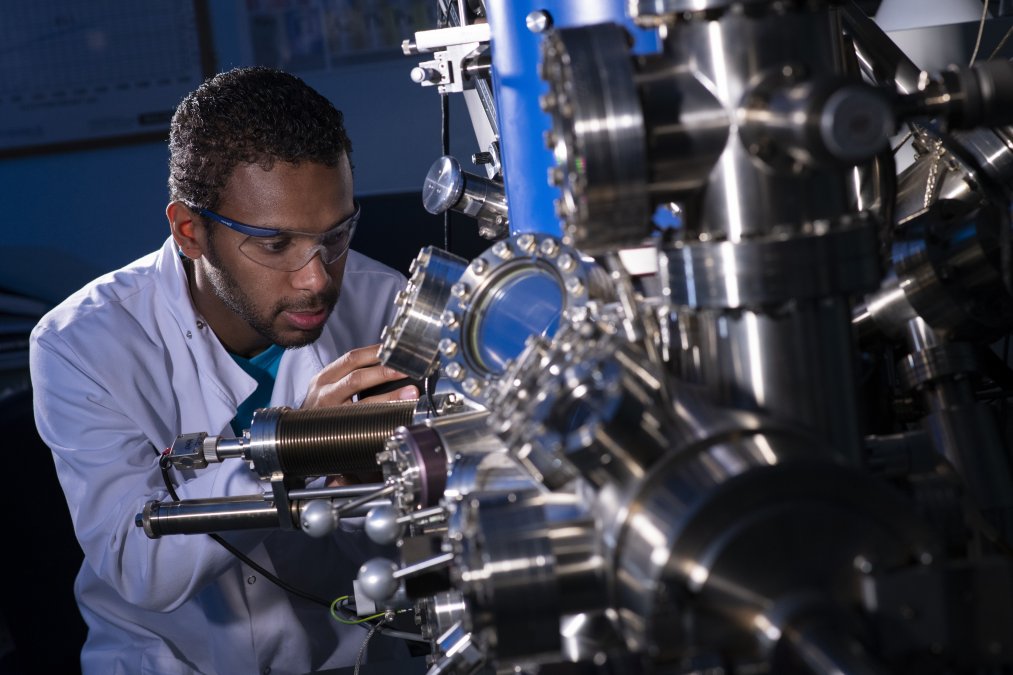
Impact of COVID-19 Pandemic on Durable Goods
COVID-19 is a pandemic that has caused widespread illness and has had an impact on consumer spending, especially on durable goods. People stopped going to the gym and stopped attending social events as a result of the disease. People also stopped hailing taxis, which led to a decrease in consumer spending. Instead, people decided to spend more time at home producing and enjoying leisure activities. This reduced consumer spending on services and restaurants.
The US economy was impacted by the COVID-19 Pandemic in a significant way. The disease not only increased the demand for durable goods but also prompted strong fiscal policies to increase household disposable income. This could account for about half of the increase in consumer durable goods spending by 2020.
The COVID-19 epidemic has affected individuals, businesses, and communities. The impact of the disease upon fast-moving goods has been well covered, but less attention has been given to the effects on durable goods. NielsenIQ BASES recently conducted a survey that revealed that nearly a third of respondents have made durables purchases in response. The disease has also affected consumers' purchasing habits because they spend more of their time at home caring for children.
FAQ
What does it mean to warehouse?
Warehouses and storage facilities are where goods are kept before being sold. It can be an outdoor or indoor area. In some cases it could be both indoors and outdoors.
What are the responsibilities of a logistic manager?
A logistics manager makes sure that all goods are delivered on-time and in good condition. This is done by using his/her experience and knowledge of the company's products. He/she also needs to ensure adequate stock to meet demand.
How does manufacturing avoid bottlenecks in production?
To avoid production bottlenecks, ensure that all processes run smoothly from the moment you receive your order to the time the product ships.
This includes planning to meet capacity requirements and quality control.
This can be done by using continuous improvement techniques, such as Six Sigma.
Six Sigma management is a system that improves quality and reduces waste within your organization.
It emphasizes consistency and eliminating variance in your work.
What are the requirements to start a logistics business?
To run a successful logistics company, you need a lot knowledge and skills. You must have good communication skills to interact effectively with your clients and suppliers. It is important to be able to analyse data and draw conclusions. You will need to be able handle pressure well and work in stressful situations. In order to innovate and create new ways to improve efficiency, creativity is essential. To motivate and guide your team towards reaching organizational goals, you must have strong leadership skills.
To meet tight deadlines, you must also be efficient and organized.
What skills are required to be a production manager?
A production planner must be organized, flexible, and able multitask to succeed. Communication skills are essential to ensure that you can communicate effectively with clients, colleagues, and customers.
Statistics
- In the United States, for example, manufacturing makes up 15% of the economic output. (twi-global.com)
- It's estimated that 10.8% of the U.S. GDP in 2020 was contributed to manufacturing. (investopedia.com)
- (2:04) MTO is a production technique wherein products are customized according to customer specifications, and production only starts after an order is received. (oracle.com)
- According to a Statista study, U.S. businesses spent $1.63 trillion on logistics in 2019, moving goods from origin to end user through various supply chain network segments. (netsuite.com)
- In 2021, an estimated 12.1 million Americans work in the manufacturing sector.6 (investopedia.com)
External Links
How To
How to use the Just-In Time Method in Production
Just-in-time (JIT) is a method that is used to reduce costs and maximize efficiency in business processes. It's a way to ensure that you get the right resources at just the right time. This means that you only pay the amount you actually use. Frederick Taylor, a 1900s foreman, first coined the term. He saw how overtime was paid to workers for work that was delayed. He then concluded that if he could ensure that workers had enough time to do their job before starting to work, this would improve productivity.
JIT is about planning ahead. You should have all the necessary resources ready to go so that you don’t waste money. Look at your entire project, from start to end. Make sure you have enough resources in place to deal with any unexpected problems. If you anticipate that there might be problems, you'll have enough people and equipment to fix them. This will prevent you from spending extra money on unnecessary things.
There are many JIT methods.
-
Demand-driven JIT: This is a JIT that allows you to regularly order the parts/materials necessary for your project. This will allow for you to track the material that you have left after using it. This will allow you to calculate how long it will take to make more.
-
Inventory-based: This type allows you to stock the materials needed for your projects ahead of time. This allows for you to anticipate how much you can sell.
-
Project-driven: This method allows you to set aside enough funds for your project. If you know the amount you require, you can buy the materials you need.
-
Resource-based JIT: This is the most popular form of JIT. You allocate resources based on the demand. For example, if there is a lot of work coming in, you will have more people assigned to them. If you don't receive many orders, then you'll assign fewer employees to handle the load.
-
Cost-based: This is a similar approach to resource-based but you are not only concerned with how many people you have, but also how much each one costs.
-
Price-based pricing: This is similar in concept to cost-based but instead you look at how much each worker costs, it looks at the overall company's price.
-
Material-based: This is quite similar to cost-based, but instead of looking at the total cost of the company, you're concerned with how much raw materials you spend on average.
-
Time-based: This is another variation of resource-based JIT. Instead of focusing only on how much each employee is costing, you should focus on how long it takes to complete your project.
-
Quality-based JIT: Another variation on resource-based JIT. Instead of thinking about the cost of each employee or the time it takes to produce something, you focus on how good your product quality.
-
Value-based JIT : This is the newest type of JIT. In this instance, you are not concerned about the product's performance or meeting customer expectations. Instead, you are focused on adding value to the marketplace.
-
Stock-based: This stock-based method focuses on the actual quantity of products being made at any given time. This method is useful when you want to increase production while decreasing inventory.
-
Just-in-time (JIT) planning: This is a combination of JIT and supply chain management. It refers to the process of scheduling the delivery of components as soon as they are ordered. It's important because it reduces lead times and increases throughput.