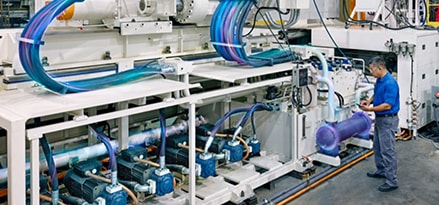
Manufacturing Extension Partnership Centers (MEPs) offer a wide range of services that help small and mid-sized manufacturers to grow and prosper. MEP Centers have been established in every state, including Puerto Rico. These centers are trusted business advisors that help solve manufacturers' challenges while identifying opportunities for expansion.
MEP centers recruit subject matter specialists who are familiar with their local industries and have experience working with small and mid-sized manufacturers. They can offer assistance in a variety of areas, such as productivity, quality, cybersecurity protection, business growth and advanced technologies. Sharon Ohman says they can also create tools SMMs use internally, or work with suppliers to develop, and that these tools are available for SMMs.
The centers are supported by federal appropriations paid one-half to each center, with the balance provided by state and local governments and/or private entities. The American Innovation and Competitiveness Act, which was passed in January 2017, adjusted the cost-share ratio for MEP Centers. This allowed them to keep more of their nonfederal funds.
Many MEP Centers are not-for-profit organizations or universities. Other MEP centers are operated by the state government or an agency within the same state as the center.
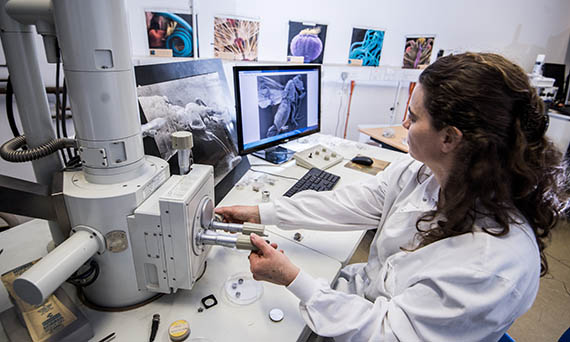
These centers could be staffed either by professionals, managers or consultants. Some centers are more technologically advanced and have laboratories or a research center.
Some centers offer consulting and training services to other businesses. For example, the Nebraska MEP provides support to manufacturers on implementing new technology.
MEP services can be delivered to a manufacturer's employees or even to the company itself. Some centers send specialists to manufacturing sites to work with the manufacturer's management team on specific goals.
During the past year, MEP centers connected with more than 3,000 manufacturers. The MEP centers were able to generate $14.4 billion of sales, $1.5 million in cost savings and $5.2 billion new client investments.
The MEP National Network includes the NIST MEP Program Office, 51 MEP Centers and an MEP Advisory Board. These partners have an important role to play in the success of the MEP system by helping to ensure that the MEP system remains effective and has the capacity to expand its reach to U.S. manufacturers in the future.
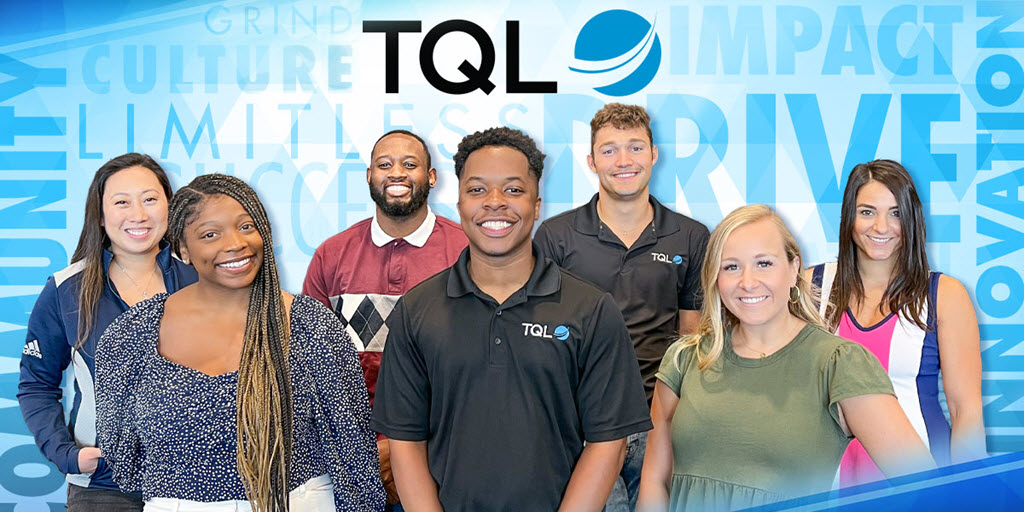
The MEP Network, through its pilots and information infrastructure services, helps MEP centers and small manufacturers to access the technical information needed to run their business. These projects will accelerate the adoption and use of electronic commerce among MEP centers, smaller manufacturers and other businesses.
The MEP National Network also forms a major part of a national strategy that aims to help small and medium manufacturers adopt technology in order to grow their businesses and achieve economic growth. MEP National Network works to connect with more than 7 000 manufacturers annually, and their work contributes to innovation, growth of the economy and creation of jobs in the United States.
FAQ
What is production planning?
Production Planning is the creation of a plan to cover all aspects, such as scheduling, budgeting. Location, crew, equipment, props and other details. This document aims to ensure that everything is planned and ready when you are ready to shoot. It should also provide information about how best to produce the best results while on set. This includes shooting schedules, locations, cast lists, crew details, and equipment requirements.
The first step in filming is to define what you want. You may have decided where to shoot or even specific locations you want to use. Once you have identified your locations and scenes it's time to begin figuring out what elements you will need for each one. If you decide you need a car and don't know what model to choose, this could be an example. You could look online for cars to see what options are available, and then narrow down your choices by selecting between different makes or models.
After you've found the perfect car, it's time to start thinking about adding extras. You might need to have people in the front seats. Maybe you need someone to move around in the back. Maybe you'd like to change the interior from black to a white color. These questions can help you decide the right look for your car. The type of shots that you are looking for is another thing to consider. Will you be filming close-ups or wide angles? Maybe the engine or steering wheel is what you are looking to film. This will allow you to determine the type of car you want.
Once you have established all the details, you can create a schedule. You can use a schedule to determine when and where you need it to be shot. Every day will have a time for you to arrive at the location, leave when you are leaving and return home when you are done. Everyone will know what they need and when. You can also make sure to book extra staff in advance if you have to hire them. It's not worth paying someone to show up if you haven't told him.
When creating your schedule, you will also need to consider the number of days you need to film. Some projects may only take a couple of days, while others could last for weeks. When creating your schedule, be aware of whether you need more shots per day. Multiple takes at the same place will result in higher costs and longer completion times. It is better to be cautious and take fewer shots than you risk losing money if you are not sure if multiple takes are necessary.
Budget setting is an important part of production planning. A realistic budget will help you work within your means. It is possible to reduce the budget at any time if you experience unexpected problems. But, don't underestimate how much money you'll spend. You'll end up with less money after paying for other things if the cost is underestimated.
Production planning is a complicated process. But once you understand how everything works together, it becomes much easier to plan future project.
Why is logistics important in manufacturing?
Logistics is an integral part of every business. They help you achieve great results by helping you manage all aspects of product flow, from raw materials to finished goods.
Logistics are also important in reducing costs and improving efficiency.
How can manufacturing prevent production bottlenecks?
To avoid production bottlenecks, ensure that all processes run smoothly from the moment you receive your order to the time the product ships.
This includes planning to meet capacity requirements and quality control.
The best way to do this is to use continuous improvement techniques such as Six Sigma.
Six Sigma is a management method that helps to improve quality and reduce waste.
It emphasizes consistency and eliminating variance in your work.
What is the job of a logistics manger?
A logistics manager ensures that all goods are delivered on time and without damage. This is done through his/her expertise and knowledge about the company's product range. He/she also needs to ensure adequate stock to meet demand.
Why automate your warehouse
Modern warehouses are increasingly dependent on automation. The rise of e-commerce has led to increased demand for faster delivery times and more efficient processes.
Warehouses must be able to quickly adapt to changing demands. Technology is essential for warehouses to be able to adapt quickly to changing needs. Automating warehouses has many benefits. Here are some reasons why it's worth investing in automation:
-
Increases throughput/productivity
-
Reduces errors
-
Improves accuracy
-
Boosts safety
-
Eliminates bottlenecks
-
Allows companies scale more easily
-
It makes workers more efficient
-
It gives visibility to everything that happens inside the warehouse
-
Enhances customer experience
-
Improves employee satisfaction
-
Reduces downtime and improves uptime
-
High quality products delivered on-time
-
Eliminates human error
-
It helps ensure compliance with regulations
Statistics
- According to the United Nations Industrial Development Organization (UNIDO), China is the top manufacturer worldwide by 2019 output, producing 28.7% of the total global manufacturing output, followed by the United States, Japan, Germany, and India.[52][53] (en.wikipedia.org)
- In 2021, an estimated 12.1 million Americans work in the manufacturing sector.6 (investopedia.com)
- Job #1 is delivering the ordered product according to specifications: color, size, brand, and quantity. (netsuite.com)
- (2:04) MTO is a production technique wherein products are customized according to customer specifications, and production only starts after an order is received. (oracle.com)
- In the United States, for example, manufacturing makes up 15% of the economic output. (twi-global.com)
External Links
How To
How to Use the 5S to Increase Productivity In Manufacturing
5S stands in for "Sort", the "Set In Order", "Standardize", or "Separate". Toyota Motor Corporation was the first to develop the 5S approach in 1954. This methodology helps companies improve their work environment to increase efficiency.
This method has the basic goal of standardizing production processes to make them repeatable. This means that tasks such as cleaning, sorting, storing, packing, and labeling are performed daily. This knowledge allows workers to be more efficient in their work because they are aware of what to expect.
Five steps are required to implement 5S: Sort, Set In Order, Standardize. Separate. Each step requires a different action, which increases efficiency. By sorting, for example, you make it easy to find the items later. When you set items in an order, you put items together. Once you have separated your inventory into groups and organized them, you will store these groups in easily accessible containers. You can also label your containers to ensure everything is properly labeled.
This requires employees to critically evaluate how they work. Employees need to understand the reasons they do certain jobs and determine if there is a better way. In order to use the 5S system effectively, they must be able to learn new skills.
In addition to increasing efficiency, the 5S method also improves morale and teamwork among employees. They feel more motivated to work towards achieving greater efficiency as they see the results.