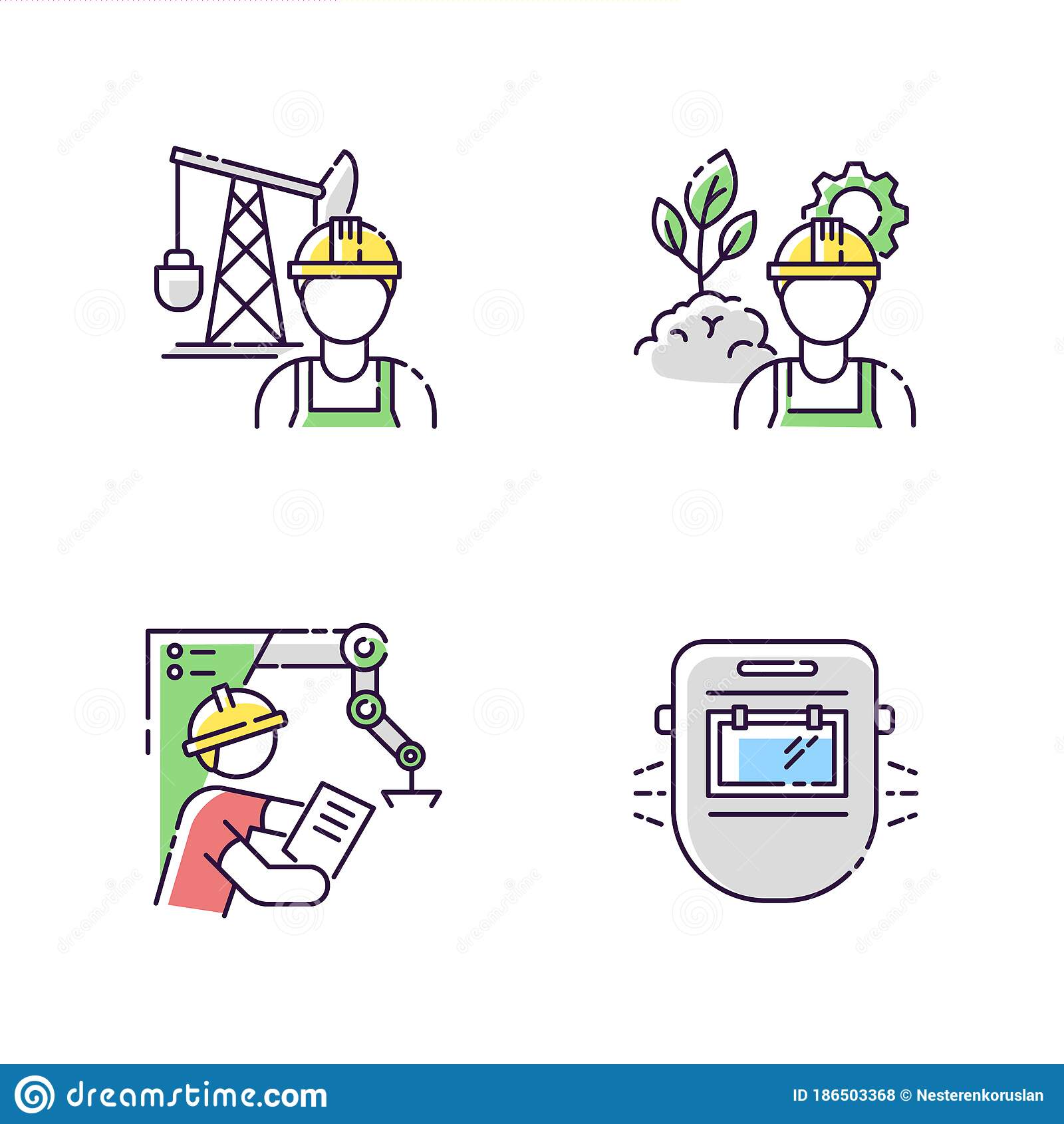
Materials engineers design and develop new materials to enable the technology of tomorrow. They work with metals ceramics plastics composites and composites in order to create materials that satisfy chemical, electronic, and mechanical requirements.
What is the role of a materials engineer?
A material engineer processes, tests, and develops the raw materials used to make a wide range of products such as aircraft wings, computer chips, biomedical devices, or golf clubs. These engineers study and evaluate the structures and properties of metals, ceramics, plastics, nanomaterials (extremely small substances), and other substances in order to create new materials that meet particular chemical, electrical, and mechanical requirements.
Materials engineers' responsibilities vary depending on the type of material they work with and the sector in which they work. They are usually responsible for budgeting, quality control and assessing production costs.
What does a materials engineer do?
A materials science engineer can work with metals as well as ceramics and composites. They also improve the durability, strength, and weight of these materials. The materials scientists can also improve existing materials by developing new ones.
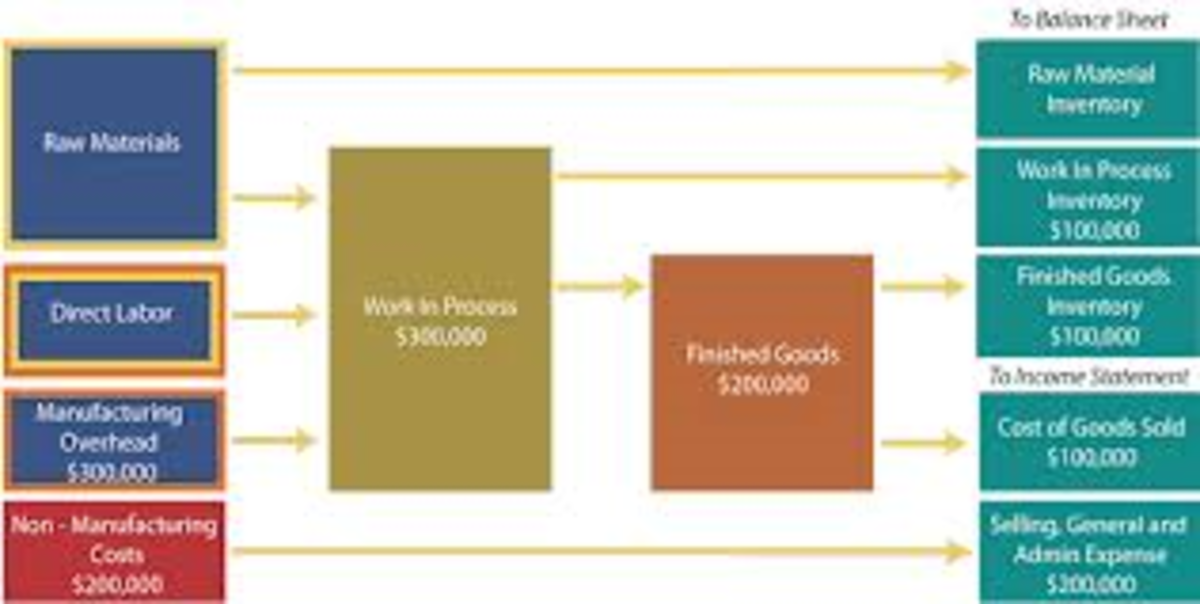
What skills does a materials scientist need?
For a career as a materials engineer you will need to have a bachelor’s degree in an engineering or materials science field. This degree must include both classroom and laboratory training with an emphasis placed on engineering principles. The program can be completed in a few short years.
After graduation you can get a job as materials engineer and you will earn around PS25,000 each year. Your salary will rise significantly as you gain experience.
How to be a materials engineer
Materials engineers have different qualifications depending on their industry. The majority of jobs require a minimum bachelor's degree, usually in materials engineering or science. This will include studies of chemistry, physics, and mathematics.
A materials science engineer's qualifications are usually a high school diploma, and a bachelor degree in an appropriate field like physics or chemistry. Most research positions at higher levels require a PhD or a Master's.
How much money can a materials engineer make?
Salary ranges for materials engineers are dependent on their level and expertise as well as the type of industry they work in. Additionally, they may receive other perks or bonuses for their efforts.
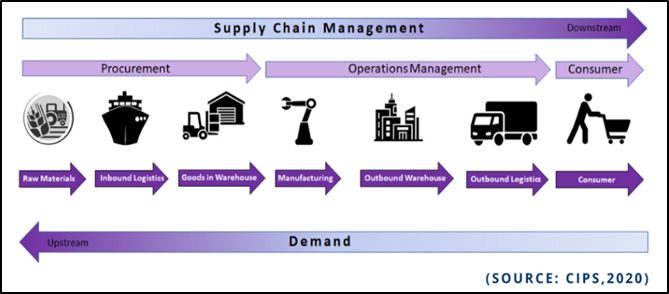
What is the career future for material engineers?
It is predicted that the future of materials engineering will be bright, and there are many opportunities available to those who choose to pursue this career. The demand for more advanced and newer materials is increasing in areas such as architecture, medicine, and communication.
Studying metallurgy or chemistry can lead to a career as a materials engineer. You will gain the knowledge necessary to start a career and possibly open more doors for you. A degree in a subject such as chemistry will help you with your research and development skills. You can gain more experience by working in an engineering firm specializing in specific fields of materials.
FAQ
What is the distinction between Production Planning or Scheduling?
Production Planning (PP), or production planning, is the process by which you determine what products are needed at any given time. This can be done by forecasting demand and identifying production capabilities.
Scheduling involves the assignment of dates and times to tasks in order to complete them within the timeframe.
How is a production manager different from a producer planner?
The primary difference between a producer planner and a manager of a project is that the manager usually plans and organizes the whole project, while a production planner is only involved in the planning stage.
How can we increase manufacturing efficiency?
The first step is to identify the most important factors affecting production time. We must then find ways that we can improve these factors. If you don’t know where to begin, consider which factors have the largest impact on production times. Once you have identified the factors, then try to find solutions.
Statistics
- In the United States, for example, manufacturing makes up 15% of the economic output. (twi-global.com)
- According to a Statista study, U.S. businesses spent $1.63 trillion on logistics in 2019, moving goods from origin to end user through various supply chain network segments. (netsuite.com)
- (2:04) MTO is a production technique wherein products are customized according to customer specifications, and production only starts after an order is received. (oracle.com)
- It's estimated that 10.8% of the U.S. GDP in 2020 was contributed to manufacturing. (investopedia.com)
- In 2021, an estimated 12.1 million Americans work in the manufacturing sector.6 (investopedia.com)
External Links
How To
How to use lean manufacturing in the production of goods
Lean manufacturing is a management style that aims to increase efficiency and reduce waste through continuous improvement. It was developed in Japan during the 1970s and 1980s by Taiichi Ohno, who received the Toyota Production System (TPS) award from TPS founder Kanji Toyoda. Michael L. Watkins published the book "The Machine That Changed the World", which was the first to be published about lean manufacturing.
Lean manufacturing, often described as a set and practice of principles, is aimed at improving the quality, speed, cost, and efficiency of products, services, and other activities. It is about eliminating defects and waste from all stages of the value stream. Lean manufacturing is also known as just in time (JIT), zero defect total productive maintenance(TPM), and five-star (S). Lean manufacturing is about eliminating activities that do not add value, such as inspection, rework, and waiting.
Lean manufacturing is a way for companies to achieve their goals faster, improve product quality, and lower costs. Lean manufacturing is considered one of the most effective ways to manage the entire value chain, including suppliers, customers, distributors, retailers, and employees. Many industries worldwide use lean manufacturing. For example, Toyota's philosophy underpins its success in automobiles, electronics, appliances, healthcare, chemical engineering, aerospace, paper, food, etc.
Lean manufacturing includes five basic principles:
-
Define Value - Identify the value your business adds to society and what makes you different from competitors.
-
Reduce Waste – Eliminate all activities that don't add value throughout the supply chain.
-
Create Flow: Ensure that the work process flows without interruptions.
-
Standardize & Simplify - Make processes as consistent and repeatable as possible.
-
Build relationships - Develop and maintain personal relationships with both your internal and external stakeholders.
Lean manufacturing, although not new, has seen renewed interest in the economic sector since 2008. Many businesses are now using lean manufacturing to improve their competitiveness. Some economists even believe that lean manufacturing can be a key factor in economic recovery.
Lean manufacturing, which has many benefits, is now a standard practice in the automotive industry. These include higher customer satisfaction levels, reduced inventory levels as well as lower operating costs.
Any aspect of an enterprise can benefit from Lean manufacturing. This is because it ensures efficiency and effectiveness in all stages of the value chain.
There are three main types in lean manufacturing
-
Just-in-Time Manufacturing (JIT): This type of lean manufacturing is commonly referred to as "pull systems." JIT means that components are assembled at the time of use and not manufactured in advance. This approach aims to reduce lead times, increase the availability of parts, and reduce inventory.
-
Zero Defects Manufacturing: ZDM ensures that no defective units leave the manufacturing plant. If a part needs to be fixed during the assembly line, it should be repaired rather than scrapped. This applies to finished products, which may need minor repairs before they are shipped.
-
Continuous Improvement (CI), also known as Continuous Improvement, aims at improving the efficiency of operations through continuous identification and improvement to minimize or eliminate waste. Continuous Improvement involves continuous improvement of processes.