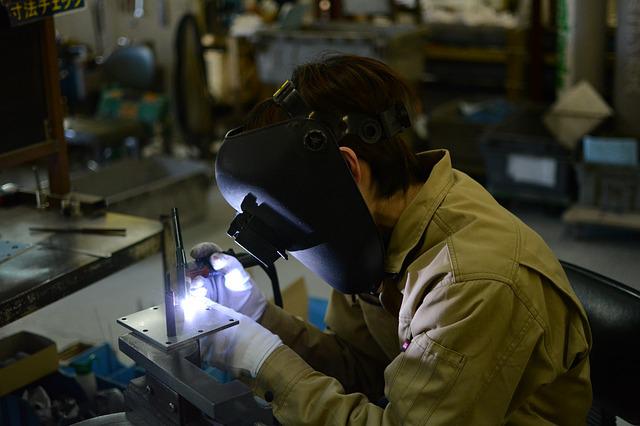
Watts didn't know he wanted to be a supply-chain major when he graduated. Jack Jensen was able convince Watts to join the Moore School supply chain management program when he told him he would get to work on a capstone project.
The capstone project, one of the more prestigious courses in undergraduate business school curriculum, lets students dig deep into supply chain problems on real-world projects for companies and nonprofits. Jensen claims that Moore School students have worked with more 150 companies to identify savings totaling $175 million in the last 8 years.
Students work with advisors from the faculty and other organizations to analyse real-world supply chains using tools such as Lean Manufacturing or Six Sigma. They learn how to prepare, transform, and organize data, create models, and evaluate the results.
Students complete a capstone course project after completing their studies. They present the problem and its significance for theory and business, the background of the project, the research, the method and the results.
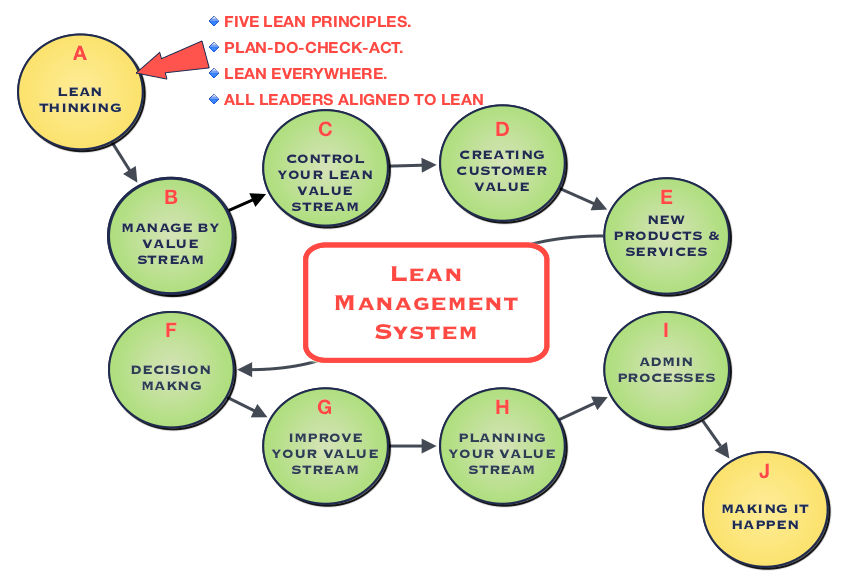
The capstone project provides a unique opportunity to put into practice the knowledge and skills you have gained throughout your degree. It is also a way to show your dedication to your education.
As a consequence, many schools give their students the option to complete a final project as part graduation requirements. These projects are often very difficult, and the students need to put in a lot of effort and time to finish them.
The project could be carried out over a course of one semester or more. It is recommended that you spend between 100-120 hrs on the project.
Towson Place Apartment is a student housing community located just a short walk from campus that offers studios, one- and two-bedroom apartments. Professionally managed by Capstone Management, residents enjoy a variety of amenities designed to meet their needs.
Millennium Hall is a three-building community of 400 beds whose design was developed in partnership with Towson University and delivered in 2001. The building is home to both undergraduates and graduates. The complex consists of studios as well one and two bedroom units. There is also a central mailbox and a laundry facility.
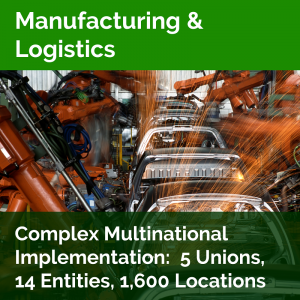
MEDCO is the owner of Paca, Tubman and Millennium Hall. TU leases these residences. MEDCO hires Capstone Properties Inc to manage day-to-day operations.
Several families claim they are being held captive by their lease agreement as TU switches to distance-learning. The families claim that MEDCO has refused to refund their rents and release them from their lease agreements, despite following guidelines established by TU Housing and Residence Life, the University of Maryland Campus Living Services and the Center for Disease Control.
The lawsuit was filed in March 2018, and it has not been resolved as of yet. Lucchi's case will be pursued further after he has received responses and advice from MEDCO's lawyers.
FAQ
What is the importance of logistics in manufacturing?
Logistics is an integral part of every business. They enable you to achieve outstanding results by helping manage product flow from raw materials through to finished goods.
Logistics play an important role in reducing costs as well as increasing efficiency.
What does it take to run a logistics business?
It takes a lot of skills and knowledge to run a successful logistics business. Good communication skills are essential to effectively communicate with your suppliers and clients. You must be able analyze data and draw out conclusions. You must be able to work well under pressure and handle stressful situations. To improve efficiency, you must be innovative and creative. You will need strong leadership skills to motivate and direct your team members towards achieving their organizational goals.
It is also important to be efficient and well organized in order meet deadlines.
Is automation necessary in manufacturing?
Not only is automation important for manufacturers, but it's also vital for service providers. They can provide services more quickly and efficiently thanks to automation. It helps them to lower costs by reducing human errors, and improving productivity.
What types of jobs can you find in logistics
Logistics can offer many different jobs. Some of them are:
-
Warehouse workers - They load and unload trucks and pallets.
-
Transportation drivers: They drive trucks and trailers and deliver goods and make pick-ups.
-
Freight handlers - They sort and pack freight in warehouses.
-
Inventory managers - These are responsible for overseeing the stock of goods in warehouses.
-
Sales representatives: They sell products to customers.
-
Logistics coordinators - They organize and plan logistics operations.
-
Purchasing agents: They are responsible for purchasing goods and services to support company operations.
-
Customer service representatives - They answer calls and emails from customers.
-
Ship clerks - They issue bills and process shipping orders.
-
Order fillers - They fill orders based on what is ordered and shipped.
-
Quality control inspectors - They check incoming and outgoing products for defects.
-
Others - There are many types of jobs in logistics such as transport supervisors and cargo specialists.
What is meant by manufacturing industries?
Manufacturing Industries are companies that manufacture products. Consumers are those who purchase these products. These companies employ many processes to achieve this purpose, such as production and distribution, retailing, management and so on. They create goods from raw materials, using machines and various other equipment. This includes all types manufactured goods such as clothing, building materials, furniture, electronics, tools and machinery.
How can I find out more about manufacturing?
You can learn the most about manufacturing by getting involved in it. But if that is not possible you can always read books and watch educational videos.
Statistics
- In 2021, an estimated 12.1 million Americans work in the manufacturing sector.6 (investopedia.com)
- According to the United Nations Industrial Development Organization (UNIDO), China is the top manufacturer worldwide by 2019 output, producing 28.7% of the total global manufacturing output, followed by the United States, Japan, Germany, and India.[52][53] (en.wikipedia.org)
- Many factories witnessed a 30% increase in output due to the shift to electric motors. (en.wikipedia.org)
- You can multiply the result by 100 to get the total percent of monthly overhead. (investopedia.com)
- It's estimated that 10.8% of the U.S. GDP in 2020 was contributed to manufacturing. (investopedia.com)
External Links
How To
How to Use Just-In-Time Production
Just-intime (JIT), which is a method to minimize costs and maximize efficiency in business process, is one way. It is a process where you get the right amount of resources at the right moment when they are needed. This means that your only pay for the resources you actually use. Frederick Taylor, a 1900s foreman, first coined the term. He saw how overtime was paid to workers for work that was delayed. He realized that workers should have enough time to complete their jobs before they begin work. This would help increase productivity.
JIT is a way to plan ahead and make sure you don't waste any money. Look at your entire project, from start to end. Make sure you have enough resources in place to deal with any unexpected problems. You will have the resources and people to solve any problems you anticipate. This way, you won't end up paying extra money for things that weren't really necessary.
There are many JIT methods.
-
Demand-driven JIT: You order the parts and materials you need for your project every other day. This will allow you to track how much material you have left over after using it. This will allow you to calculate how long it will take to make more.
-
Inventory-based : You can stock the materials you need in advance. This allows one to predict how much they will sell.
-
Project-driven: This method allows you to set aside enough funds for your project. Once you have an idea of how much material you will need, you can purchase the necessary materials.
-
Resource-based JIT : This is probably the most popular type of JIT. You allocate resources based on the demand. You might assign more people to help with orders if there are many. If you don't have many orders, you'll assign fewer people to handle the workload.
-
Cost-based: This is similar to resource-based, except that here you're not just concerned about how many people you have but how much each person costs.
-
Price-based pricing: This is similar in concept to cost-based but instead you look at how much each worker costs, it looks at the overall company's price.
-
Material-based: This is very similar to cost-based but instead of looking at total costs of the company you are concerned with how many raw materials you use on an average.
-
Time-based: This is another variation of resource-based JIT. Instead of focusing solely on the amount each employee costs, focus on how long it takes for the project to be completed.
-
Quality-based JIT: Another variation on resource-based JIT. Instead of focusing on the cost of each worker or how long it takes, think about how high quality your product is.
-
Value-based: This is one of the newest forms of JIT. In this instance, you are not concerned about the product's performance or meeting customer expectations. Instead, your focus is on the value you bring to the market.
-
Stock-based: This stock-based method focuses on the actual quantity of products being made at any given time. This method is useful when you want to increase production while decreasing inventory.
-
Just-in-time (JIT) planning: This is a combination of JIT and supply chain management. It refers to the process of scheduling the delivery of components as soon as they are ordered. It's important as it reduces leadtimes and increases throughput.