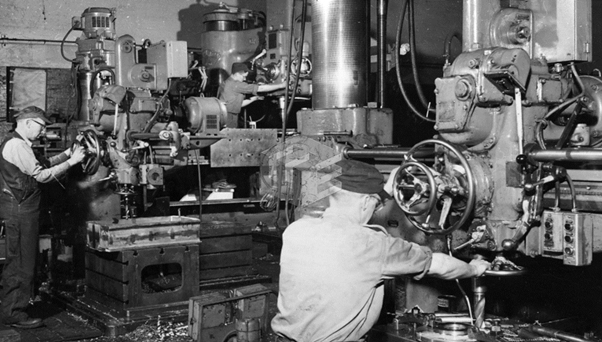
Lean services is a process that applies lean manufacturing production techniques to the service sector. This approach has been adopted by companies such as HMRC in the UK and US health care providers. Lean services are intended to reduce waste and increase customer satisfaction while reducing costs. Lean services are available to all businesses, regardless of whether they're small startups or global giants.
Lean manufacturing
Lean manufacturing refers to a process that eliminates waste. The process improves productivity, lowers operating costs and increases employee satisfaction. It can help increase profits. It can reduce the time it takes to produce a product, and increase profits. Companies can increase their customer base, and their revenue streams by using lean manufacturing services.
Lean manufacturing requires teamwork and lots of talent. It is important that everyone on the team understands the process and how it works. The team should be able adjust the practices to their specific needs. To simplify manufacturing processes is the first step towards lean manufacturing. Complex manufacturing processes can make it difficult for people to spot inefficiencies and waste. A simplified process also improves visibility and helps create a culture of continuous improvement. This will empower your employees and allow them to identify inefficiencies.
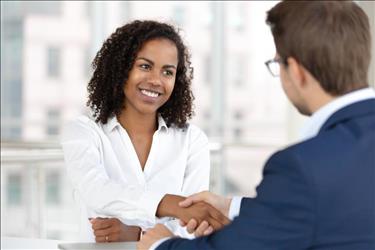
Lean manufacturing can help companies increase their efficiency by reducing lead times. MXGlobal is one company that provides lean implementation services and has successfully consulted Japanese businesses with a U.S. footprint. The firm's lean manufacturing services are aimed at helping businesses grow internationally and achieve their business goals.
Lean manufacturing services are designed to help businesses create an environment that maximizes profits. They work to reduce waste and increase productivity. There are eight types. They include wastes from overproduction, inventory, defects, and transportation. These wastes can lead to higher costs and lower customer satisfaction.
Management of Lean operations
To implement lean operations management for lean services, organizations must first determine what they are trying to achieve. As the name implies, it is a systematic approach that seeks to create value for the end customers. This is what customers expect from a product/service. Value is what drives sales. To get started, consider mapping all steps in the creation of a product or service and ask, "What adds value to the customer?"
The goal of a lean management system is to continually improve your processes. This is the most important part of lean management. This ensures your team delivers work assignments consistently in a shorter amount of time and with less effort. This method also reduces waste in production and optimizes overheads and storage costs. The four principles of lean management include continuous improvement, minimizing waste, reducing cycle time, and ensuring continuous workflows.
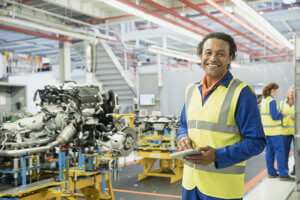
Lean operations management in lean services is focused on creating more value and utilizing fewer resources. Lean principles help to eliminate intangible wastes. However, it is difficult to identify them in a service environment. Companies can reduce waste and increase profits.
FAQ
What are the logistics products?
Logistics refers to the movement of goods from one place to another.
They include all aspects associated with transport including packaging, loading transporting, unloading storage, warehousing inventory management customer service, distribution returns and recycling.
Logisticians ensure that products reach the right destination at the right moment and under safe conditions. They provide information on demand forecasts as well stock levels, production schedules and availability of raw material.
They keep track and monitor the transit of shipments, maintain quality standards, order replenishment and inventories, coordinate with suppliers, vendors, and provide support for sales and marketing.
Why automate your warehouse
Modern warehousing has seen automation take center stage. With the rise of ecommerce, there is a greater demand for faster delivery times as well as more efficient processes.
Warehouses must adapt quickly to meet changing customer needs. Technology is essential for warehouses to be able to adapt quickly to changing needs. Automation of warehouses offers many benefits. Here are some reasons why it's worth investing in automation:
-
Increases throughput/productivity
-
Reduces errors
-
Increases accuracy
-
Safety Boosts
-
Eliminates bottlenecks
-
Companies can scale more easily
-
Increases efficiency of workers
-
Provides visibility into everything that happens in the warehouse
-
Enhances customer experience
-
Improves employee satisfaction
-
Reduces downtime and improves uptime
-
Quality products delivered on time
-
Removes human error
-
It helps ensure compliance with regulations
How can I learn about manufacturing?
Experience is the best way for you to learn about manufacturing. If that is not possible, you could always read books or view educational videos.
How can overproduction in manufacturing be reduced?
The key to reducing overproduction lies in developing better ways to manage inventory. This would reduce time spent on activities such as purchasing, stocking, and maintaining excess stock. This would allow us to use our resources for more productive tasks.
Kanban systems are one way to achieve this. A Kanban board, a visual display to show the progress of work, is called a Kanban board. A Kanban system allows work items to move through several states before reaching their final destination. Each state represents a different priority.
To illustrate, work can move from one stage or another when it is complete enough for it to be moved to a new stage. It is possible to keep a task in the beginning stages until it gets to the end.
This helps to keep work moving forward while ensuring that no work is left behind. A Kanban board allows managers to monitor how much work is being completed at any given moment. This data allows them adjust their workflow based upon real-time data.
Lean manufacturing can also be used to reduce inventory levels. Lean manufacturing works to eliminate waste throughout every stage of the production chain. Waste includes anything that does not add value to the product. Some common types of waste include:
-
Overproduction
-
Inventory
-
Packaging that is not necessary
-
Materials in excess
These ideas will help manufacturers increase efficiency and lower costs.
Why is logistics important for manufacturing?
Logistics are an essential component of any business. They enable you to achieve outstanding results by helping manage product flow from raw materials through to finished goods.
Logistics plays a significant role in reducing cost and increasing efficiency.
Statistics
- In the United States, for example, manufacturing makes up 15% of the economic output. (twi-global.com)
- (2:04) MTO is a production technique wherein products are customized according to customer specifications, and production only starts after an order is received. (oracle.com)
- You can multiply the result by 100 to get the total percent of monthly overhead. (investopedia.com)
- Job #1 is delivering the ordered product according to specifications: color, size, brand, and quantity. (netsuite.com)
- In 2021, an estimated 12.1 million Americans work in the manufacturing sector.6 (investopedia.com)
External Links
How To
How to Use 5S to Increase Productivity in Manufacturing
5S stands for "Sort", "Set In Order", "Standardize", "Separate" and "Store". Toyota Motor Corporation developed the 5S method in 1954. This methodology helps companies improve their work environment to increase efficiency.
This approach aims to standardize production procedures, making them predictable, repeatable, and easily measurable. It means tasks like cleaning, sorting or packing, labeling, and storing are done every day. These actions allow workers to perform their job more efficiently, knowing what to expect.
There are five steps to implementing 5S, including Sort, Set In Order, Standardize, Separate and Store. Each step has a different action and leads to higher efficiency. If you sort items, it makes them easier to find later. When you arrange items, you place them together. Then, after you separate your inventory into groups, you store those groups in containers that are easy to access. Make sure everything is correctly labeled when you label your containers.
Employees must be able to critically examine their work practices. Employees need to understand the reasons they do certain jobs and determine if there is a better way. In order to use the 5S system effectively, they must be able to learn new skills.
The 5S method increases efficiency and morale among employees. As they begin to see improvements, they feel motivated to continue working towards the goal of achieving higher levels of efficiency.