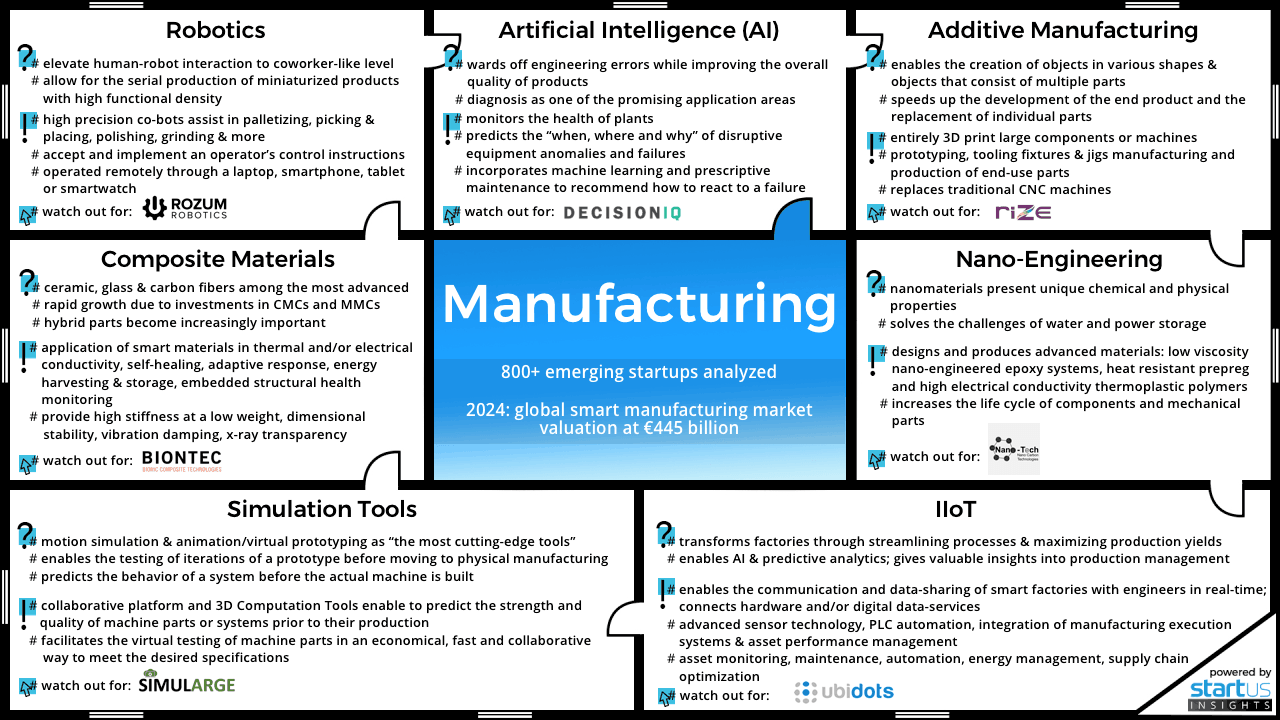
Oracle Supply Chain Management provides a complete solution to help organizations adapt quickly to changing conditions, build resilient network, and improve forecast accuracy. Oracle SCM allows flexible supply chain planning. It provides end-to-end visibility across the entire supply chain. This improves collaboration while minimizing costs. With Oracle Fusion Cloud SCM, you can use this solution to optimize your business processes and collaborate more effectively with your suppliers. Oracle SCM can help achieve these goals by reducing disruptions, reducing cost, and improving forecast accuracy.
Interface that is user-friendly
Many of the improvements to Oracle SCM are related the user-friendly design. This new release makes the system simpler and more user-friendly. An automated product-based analyzer script gives recommendations, solutions, early warnings and provides assistance. The Oracle Inbound Transactions Analyzer is a great example of this. It is designed to identify issues with inbound transactions and provides solutions for each issue. Moreover, it is highly customizable.
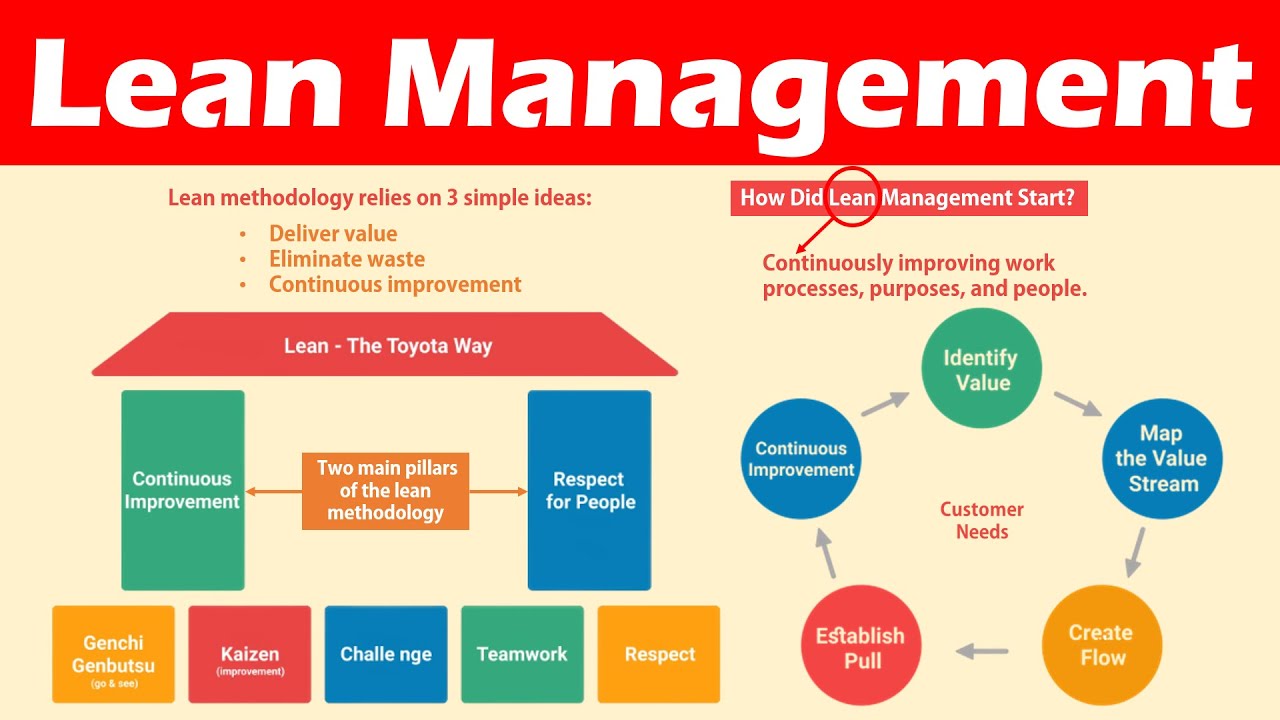
Cost management
With Oracle SCM, cost management policies and decisions can be defined at the item level. Cost profiles can be created by product or manufacturing process, and not just rely on one costing methodology. For example, manufacturing items can be driven by a standard cost per unit, while repairs items will use the actual costing methodology. The software supports both open and closed periods. It supports cost simulation, copying and other capabilities.
Decision support
Oracle SCM Decision Support is the use advanced analytics to improve management processes. Management can make the right decision based on information and data by using a range of business intelligence tool. Oracle Strategic Enterprise Management apps are designed to assist many companies in their strategic management strategies. This technology allows executives to manage their costs and track their progress against a plan. Additionally, they can measure and compensate employees based on performance. These integrated applications offer enterprise-wide solutions and can complement Oracle ERP systems.
Compliance with regulations
Organizations need to be able to effectively manage the increasing number of regulations and laws. Oracle has the answer. With Oracle SCM regulatory compliance solutions, organizations can more easily meet their legal and regulatory compliance needs. Organizations of all sizes can deploy the Oracle Cloud Platform with flexible options. Oracle provides a variety of customizable, configurable products that help customers meet regulatory compliance requirements and stay compliant.
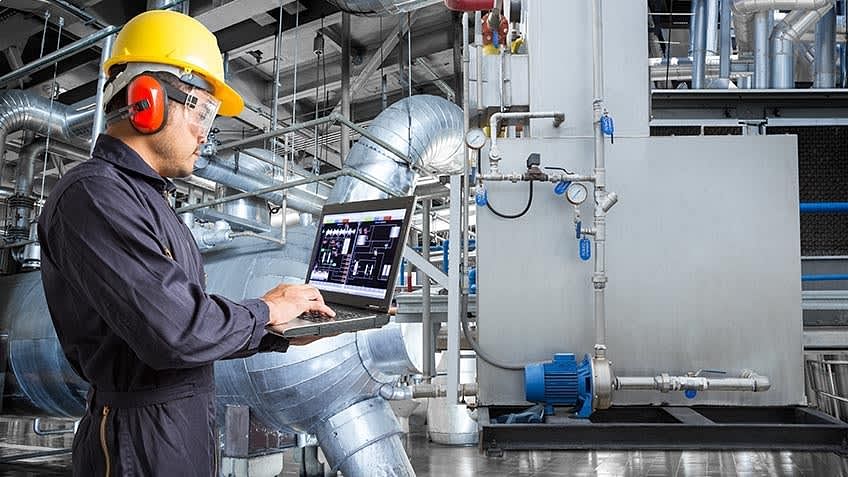
Flexible solution
Intellinum Inc. is a leader in supply chain mobility solutions and has developed Flexi LogiPro. This flexible solution allows Oracle SCM to be integrated with Oracle WMS Cloud. The flexible mobile solution provides a customizable, barcode enabled user interface for mobile devices. It integrates with the backend system in real time and supports Oracle SCM and WMS Cloud. It is available both for cloud and on-premise deployments. This allows companies to customize mobile apps for their unique needs.
FAQ
What are the four types of manufacturing?
Manufacturing is the process of transforming raw materials into useful products using machines and processes. Manufacturing can include many activities such as designing and building, testing, packaging shipping, selling, servicing, and other related activities.
How can manufacturing efficiency improved?
First, we need to identify which factors are most critical in affecting production times. We then need to figure out how to improve these variables. If you don’t know how to start, look at which factors have the greatest impact upon production time. Once you have identified the factors, then try to find solutions.
What skills is required for a production planner?
Being a production planner is not easy. You need to be organized and flexible. Also, you must be able and willing to communicate with clients and coworkers.
What are the responsibilities of a manufacturing manager
A manufacturing manager must make sure that all manufacturing processes run smoothly and effectively. They should be alert for any potential problems in the company and react accordingly.
They should also be able and comfortable communicating with other departments like sales and marketing.
They should be informed about industry trends and be able make use of this information to improve their productivity and efficiency.
How does manufacturing avoid bottlenecks in production?
You can avoid bottlenecks in production by making sure that everything runs smoothly throughout the production cycle, from the moment you receive an order to the moment the product is shipped.
This includes planning for capacity requirements as well as quality control measures.
This can be done by using continuous improvement techniques, such as Six Sigma.
Six Sigma management is a system that improves quality and reduces waste within your organization.
It's all about eliminating variation and creating consistency in work.
Statistics
- Job #1 is delivering the ordered product according to specifications: color, size, brand, and quantity. (netsuite.com)
- [54][55] These are the top 50 countries by the total value of manufacturing output in US dollars for its noted year according to World Bank.[56] (en.wikipedia.org)
- (2:04) MTO is a production technique wherein products are customized according to customer specifications, and production only starts after an order is received. (oracle.com)
- In 2021, an estimated 12.1 million Americans work in the manufacturing sector.6 (investopedia.com)
- You can multiply the result by 100 to get the total percent of monthly overhead. (investopedia.com)
External Links
How To
How to use the Just In-Time Production Method
Just-intime (JIT), which is a method to minimize costs and maximize efficiency in business process, is one way. It allows you to get the right amount resources at the right time. This means that only what you use is charged to your account. Frederick Taylor, a 1900s foreman, first coined the term. He observed how workers were paid overtime if there were delays in their work. He decided that workers would be more productive if they had enough time to complete their work before they started to work.
JIT is a way to plan ahead and make sure you don't waste any money. Look at your entire project, from start to end. Make sure you have enough resources in place to deal with any unexpected problems. You will have the resources and people to solve any problems you anticipate. This will prevent you from spending extra money on unnecessary things.
There are many JIT methods.
-
Demand-driven JIT: You order the parts and materials you need for your project every other day. This will allow for you to track the material that you have left after using it. You'll also be able to estimate how long it will take to produce more.
-
Inventory-based: This type allows you to stock the materials needed for your projects ahead of time. This allows you predict the amount you can expect to sell.
-
Project-driven: This is an approach where you set aside enough funds to cover the cost of your project. If you know the amount you require, you can buy the materials you need.
-
Resource-based: This is the most common form of JIT. This is where you assign resources based upon demand. You might assign more people to help with orders if there are many. If there aren't many orders, you will assign fewer people.
-
Cost-based : This is similar in concept to resource-based. But here, you aren't concerned about how many people your company has but how much each individual costs.
-
Price-based: This approach is very similar to the cost-based method except that you don't look at individual workers costs but the total cost of the company.
-
Material-based is an alternative to cost-based. Instead of looking at the total cost in the company, this method focuses on the average amount of raw materials that you consume.
-
Time-based JIT is another form of resource-based JIT. Instead of focusing solely on the amount each employee costs, focus on how long it takes for the project to be completed.
-
Quality-based JIT: This is another variation of resource based JIT. Instead of worrying about the costs of each employee or how long it takes for something to be made, you should think about how quality your product is.
-
Value-based JIT: This is the latest form of JIT. In this instance, you are not concerned about the product's performance or meeting customer expectations. Instead, your focus is on the value you bring to the market.
-
Stock-based: This inventory-based approach focuses on how many items are being produced at any one time. It's used when you want to maximize production while minimizing inventory.
-
Just-in-time (JIT) planning: This is a combination of JIT and supply chain management. It is the process of scheduling components' delivery as soon as they have been ordered. It reduces lead times and improves throughput.