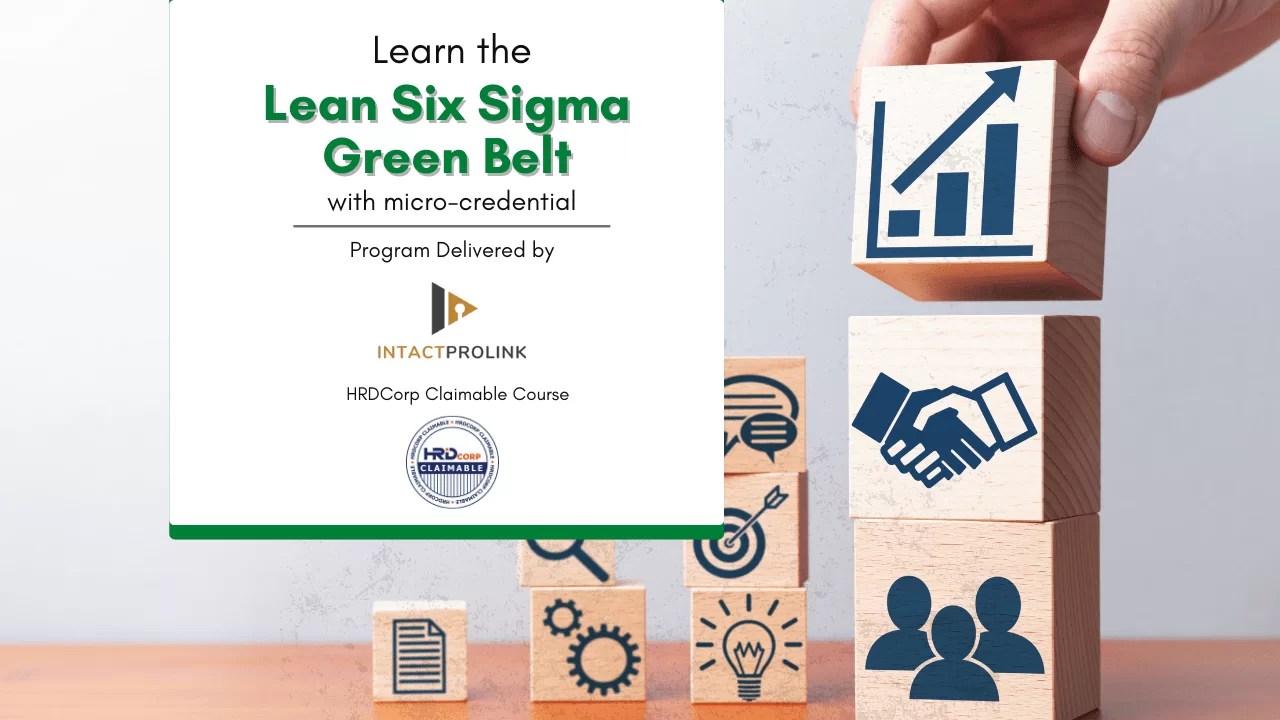
Strategic supply chain management requires the ability of a company to adapt to market requirements and remain competitive. The right strategy must be considered from many angles. These factors include competitive positioning as well cost-effectiveness and customer service. These factors should not be overlooked. The company should also be ready to invest in manufacturing infrastructure to allow it to adapt to changing markets.
Competitive positioning
It is critical for a brand or company to have a competitive advantage in a given market. This requires paying attention to customer preferences, needs, and current trends. Competitive positioning is a way for a brand to stand out from its competitors and increase its sales. It also helps brands solve customers' problems which increases their value.
Market research is key to creating a strong positioning strategy. The first step in estimating the market size is to determine the opportunity. This can easily be accomplished using data collected from various sources like industry reports, data on the external market and personal experience in this market. This information helps determine the total potential customers and sales. It helps you to understand the market's structure, growth, and stability.
Cost-effectiveness
A strategic supply chain can help manufacturers and retailers be more competitive. It allows firms to get a complete view of their supply chains, and can also help them to create data-driven demand forecasts. It should ultimately help companies calculate their investment costs and to explore different "what-if” scenarios.
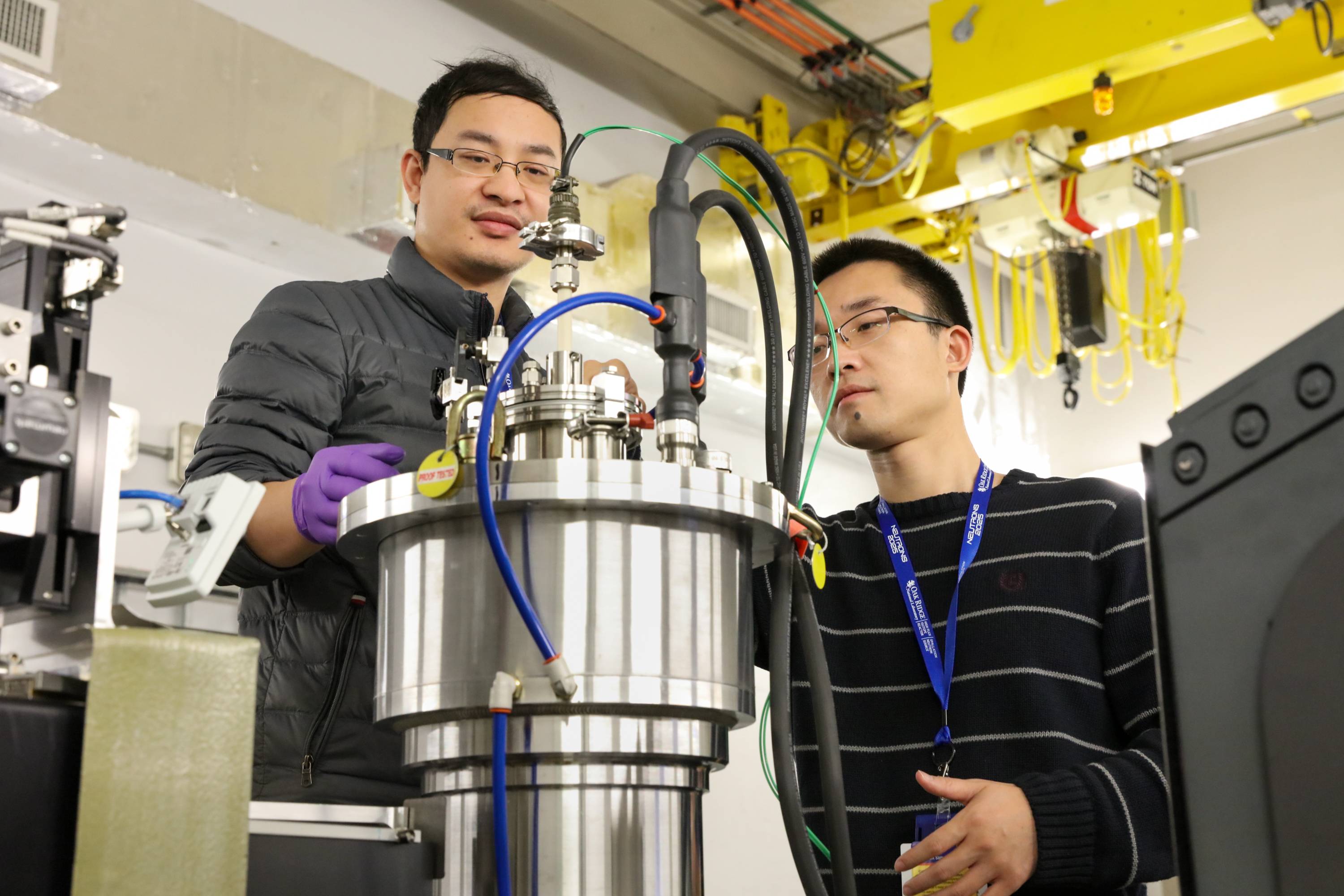
It can help businesses make better decisions and increase their ROI. As such, it is an essential tool in today's data-driven economy. It allows decision-makers to identify and evaluate opportunities, and will allow them to balance cost and benefit and prosper in the global market.
Customer service
Maximizing customer service is a key aspect of strategic supply chains management. This aspect is vital to the success of your business. You will be outsold by your competitors if you don't have it. Only a very small percentage of companies reach the top in satisfying customers' needs. Recent studies have shown that customers are dissatisfied with their service experience and the concept of customer service is often misunderstood and poorly defined.
Customers are satisfied when they receive excellent customer service. These elements include customer satisfaction, price, and product quality. Customer service is multifaceted and requires planning during both the transactional and pretransaction phases.
Manufacturing infrastructure
Strategic supply chain management requires the infrastructure of manufacturing. It ensures the timely availability of domestic industrial resources. This infrastructure includes the products and human resources that make up a company's supply chain. This infrastructure also supports the use of on-hand and vendor-managed inventory. This infrastructure also ensures sufficient manufacturing capacity.
Numerous studies have shown significant savings from improving manufacturing infrastructure. Supply chains can be made more efficient by improving logistics, material sourcing, manufacturing capabilities, and other aspects. However, many companies don't understand that supply chains are more than just operational processes.
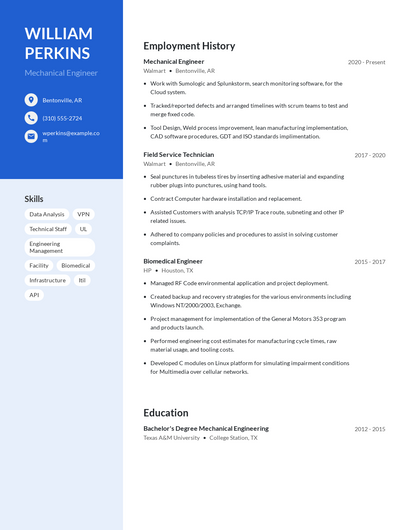
Technology
It is becoming increasingly clear that technology is a crucial part of a business's success. In an uncertain business environment, a more agile and resilient supply chain is imperative. Technology-enabled suppliers can reduce costs up to 20%, improve EBITDA as high as 10%, and improve customer services by up 30%. These innovative supply chain management approaches are at the core of many new business models.
Traditional supply-chain technology adoption required significant changes in an organization and multi-year, multimillion dollar investments. Companies can now experiment with new strategies in a cost-effective, fast-paced setting thanks to three new technologies. These technologies are able to help companies test new ideas and improve processes. They also allow them to make rapid impacts. These technologies allow companies to reduce risks by implementing them in smaller and more specific areas.
FAQ
How can overproduction in manufacturing be reduced?
The key to reducing overproduction lies in developing better ways to manage inventory. This would decrease the time that is spent on inefficient activities like purchasing, storing, or maintaining excess stock. By doing this, we could free up resources for other productive tasks.
Kanban systems are one way to achieve this. A Kanban Board is a visual display that tracks work progress. In a Kanban system, work items move through a sequence of states until they reach their final destination. Each state has a different priority level.
If work is moving from one stage to the other, then the current task can be completed and moved on to the next. It is possible to keep a task in the beginning stages until it gets to the end.
This allows for work to continue moving forward, while also ensuring that there is no work left behind. A Kanban board allows managers to monitor how much work is being completed at any given moment. This data allows them adjust their workflow based upon real-time data.
Lean manufacturing is another option to control inventory levels. Lean manufacturing is about eliminating waste from all stages of the production process. Anything that doesn't add value to the product is considered waste. The following are examples of common waste types:
-
Overproduction
-
Inventory
-
Unnecessary packaging
-
Exceed materials
By implementing these ideas, manufacturers can improve efficiency and cut costs.
What's the difference between Production Planning & Scheduling?
Production Planning (PP), is the process of deciding what production needs to take place at any given time. This can be done by forecasting demand and identifying production capabilities.
Scheduling refers to the process of allocating specific dates to tasks in order that they can be completed within a specified timeframe.
What skills do production planners need?
A production planner must be organized, flexible, and able multitask to succeed. Also, you must be able and willing to communicate with clients and coworkers.
How can manufacturing avoid production bottlenecks
The key to avoiding bottlenecks in production is to keep all processes running smoothly throughout the entire production cycle, from the time you receive an order until the time when the product ships.
This includes both quality control and capacity planning.
Continuous improvement techniques like Six Sigma are the best way to achieve this.
Six Sigma can be used to improve the quality and decrease waste in all areas of your company.
It focuses on eliminating variation and creating consistency in your work.
What is the best way to learn about manufacturing?
Hands-on experience is the best way to learn more about manufacturing. You can read books, or watch instructional videos if you don't have the opportunity to do so.
What are the products and services of logistics?
Logistics is the process of moving goods from one point to another.
They cover all aspects of transportation, such as packing, loading, transporting and unloading.
Logisticians make sure that the right product arrives at the right place at the correct time and in safe conditions. They provide information on demand forecasts as well stock levels, production schedules and availability of raw material.
They keep track and monitor the transit of shipments, maintain quality standards, order replenishment and inventories, coordinate with suppliers, vendors, and provide support for sales and marketing.
Statistics
- In the United States, for example, manufacturing makes up 15% of the economic output. (twi-global.com)
- According to the United Nations Industrial Development Organization (UNIDO), China is the top manufacturer worldwide by 2019 output, producing 28.7% of the total global manufacturing output, followed by the United States, Japan, Germany, and India.[52][53] (en.wikipedia.org)
- You can multiply the result by 100 to get the total percent of monthly overhead. (investopedia.com)
- Many factories witnessed a 30% increase in output due to the shift to electric motors. (en.wikipedia.org)
- In 2021, an estimated 12.1 million Americans work in the manufacturing sector.6 (investopedia.com)
External Links
How To
Six Sigma in Manufacturing
Six Sigma can be described as "the use of statistical process control (SPC), techniques to achieve continuous improvement." Motorola's Quality Improvement Department developed it at their Tokyo plant in Japan in 1986. Six Sigma's core idea is to improve the quality of processes by standardizing and eliminating defects. Since there are no perfect products, or services, this approach has been adopted by many companies over the years. Six Sigma aims to reduce variation in the production's mean value. If you take a sample and compare it with the average, you will be able to determine how much of the production process is different from the norm. If this deviation is too big, you know something needs fixing.
Understanding the nature of variability in your business is the first step to Six Sigma. Once you have a good understanding of the basics, you can identify potential sources of variation. This will allow you to decide if these variations are random and systematic. Random variations are caused by human errors. Systematic variations can be caused by outside factors. These are, for instance, random variations that occur when widgets are made and some fall off the production line. It would be considered a systematic problem if every widget that you build falls apart at the same location each time.
Once you identify the problem areas, it is time to create solutions. This could mean changing your approach or redesigning the entire process. After implementing the new changes, you should test them again to see if they worked. If they didn't work, then you'll need to go back to the drawing board and come up with another plan.